Concrete
Stepping Up Sustainability
Published
9 months agoon
By
Roshna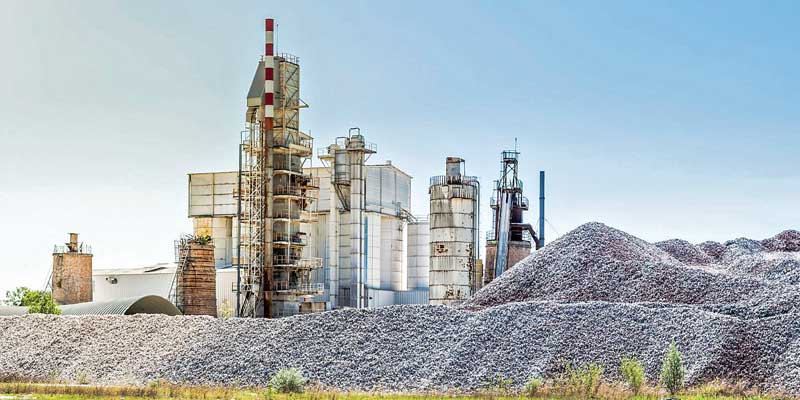
Supplementary Cementitious Materials (SCMs) offer a sustainable way to reduce cement usage, enhance concrete durability and lower the environmental impact of construction. ICR discusses integrating industrial byproducts like fly ash and slag as SCMs support resource conservation, cost savings, and long-lasting infrastructure.
The construction industry is at a pivotal juncture, facing increasing pressure to adopt sustainable practices amidst growing environmental concerns. As a major contributor to global greenhouse gas emissions, the industry recognises the urgent need for innovative solutions to minimise its ecological footprint. One such solution is the use of Supplementary Cementitious Materials (SCMs), which have emerged as vital components in the quest for sustainable concrete production. SCMs not only reduce the reliance on Portland cement—one of the most significant contributors to carbon emissions in construction—but also enhance the performance and durability of concrete.
According to a research report published by Spherical Insights & Consulting, the Global Supplementary Cementitious Materials Market Size is Expected to Grow from USD 25.40 Billion in 2023 to USD 47.70 Billion by 2033, at a CAGR of 6.50 per cent during the forecast period 2023-2033. Asia Pacific is estimated to hold the largest share of the supplementary cementitious materials market over the forecast period.
The market for supplementary cementitious materials is experiencing rapid growth, driven by factors such as rapid/fast-paced urbanisation and infrastructure development in emerging economies like China, India, Malaysia, and Singapore. Supportive policies and regulations, coupled with rising demand for durable concrete with lower penetrability, are key drivers impelling the surge in demand for supplementary cementitious materials.
Understanding SCMs
SCMs are materials that can be used to replace a portion of Portland cement in concrete. They react with calcium hydroxide to form additional cementitious compounds, thereby enhancing the concrete’s properties. SCMs include a variety of materials, such as fly ash, ground granulated blast-furnace slag (GGBS), silica fume and natural pozzolans.
- Fly ash: Fly ash is a byproduct from burning pulverised coal in electric power generating plants. It is collected from the flue gases and is commonly used in concrete due to its pozzolanic properties. Fly ash can improve workability, reduce water demand, and enhance long-term strength and durability. Its fine particles fill voids within the concrete matrix, resulting in a denser and more impermeable material.
In an authored article by Dr Supradip Das, Vice Chairman, CED 41 (BIS), for NBM&CW, he points out that compared to cement and water, the chemical reaction between fly ash and calcium hydroxide occurs at a slower pace, leading to a delayed setting time in concrete, which promotes enhanced hardening. He explains how this slower hardening, together with the varying properties of fly ash, can present substantial challenges in concrete production. In India, ash ponds currently occupy approximately 65,000 acres, and fly ash production is projected to exceed 235 million tonnes by 2024, he elaborates. - GGBS: This material is obtained by rapidly cooling molten iron slag from a blast furnace with water or steam. GGBS is known for its high strength and durability, particularly in aggressive environments where concrete is exposed to chlorides or sulphates. It not only enhances the concrete’s mechanical properties but also contributes to its resistance to corrosion and shrinkage.
- Silica fume: Silica fume is a byproduct of the production of silicon metal or ferrosilicon alloys. It is extremely fine, with a particle size much smaller than that of cement. When added to concrete, silica fume significantly increases strength, reduces permeability, and enhances durability. Its high silica content promotes additional pozzolanic reactions, leading to a denser concrete matrix.
- Natural pozzolans: Natural pozzolans, such as volcanic ash and pumice, have been used in construction for centuries. They react with calcium hydroxide in the presence of moisture to form compounds with cementitious properties. These materials are particularly valuable in regions where volcanic ash is abundant, as they are sustainable alternatives that can improve concrete’s performance.
Benefits of Using SCMs
The incorporation of SCMs into concrete mixtures offers numerous benefits that align with sustainable construction practices:
- Enhanced durability: Concrete containing SCMs exhibits improved durability characteristics, including increased resistance to sulfate attack, reduced permeability, and enhanced longevity. This durability translates into lower maintenance costs and longer service life for structures.
- Reduced carbon footprint: The use of SCMs significantly decreases the amount of Portland cement required in concrete. As cement production is responsible for approximately 8 per cent of global CO2 emissions, reducing its usage through SCMs can lead to substantial reductions in greenhouse gas emissions.
- Improved workability: SCMs like fly ash improve the workability of fresh concrete, making it easier to place and finish. This can lead to enhanced productivity on construction sites and reduced labour costs.
- Cost-effectiveness: By substituting a portion of cement with SCMs, construction projects can achieve cost savings. Fly ash and GGBS, being industrial byproducts, are often more affordable than Portland cement.
- Waste Utilisation: The use of SCMs promotes recycling and waste reduction. By utilising industrial byproducts such as fly ash and slag, the construction industry can contribute to a circular economy.
Vimal Joshi, Assistant General Manager – Quality Control, Wonder Cement, says, “SCMs like fly ash, slag and silica fume significantly enhance the durability and strength of concrete, particularly under diverse environmental conditions. Fly ash improves workability and extends the setting time, making it ideal for mass concrete projects and hot climates. The fine particles fill voids in the cement matrix, reducing permeability and enhancing resistance to sulphate and chloride attack, thus increasing durability. Slag, with its slow hydration properties, improves long-term strength and is particularly effective in reducing thermal cracking in massive concrete structures. It also enhances resistance to aggressive chemicals, making it suitable for marine environments and industrial applications.”
“Silica fume, known for its ultrafine particles, increases the density of concrete, boosting both compressive strength and durability, especially in harsh environments. By incorporating SCMs, we create concrete that is more resilient to environmental stressors, ensuring longer-lasting structures with reduced maintenance needs” he adds.
Sustainable construction
Sustainable construction practices are increasingly prioritised due to their environmental, social and economic impact. SCMs play a pivotal role in this paradigm shift. By integrating SCMs into concrete production, the construction industry can achieve:
- Reduced resource consumption: By minimising the reliance on virgin materials, SCMs contribute to the conservation of natural resources. This is particularly important in regions where natural aggregates and raw materials are scarce.
- Promotion of circular economy: The use of byproducts like fly ash and slag exemplifies a circular economy approach, where waste materials are repurposed for new applications. This not only reduces landfill waste but also promotes sustainable sourcing practices.
- Alignment with green building certifications: Many green building rating systems, such as LEED (Leadership in Energy and Environmental Design), encourage the use of SCMs. By incorporating these materials, projects can earn credits for sustainability, making them more appealing to environmentally conscious clients.
Tushar Khandhadia, General Manager – Production, Udaipur Cement Works, says, “SCMs provide an environmentally friendly alternative to traditional Portland cement by reducing the amount of clinker required to produce cement. Clinker is the main ingredient in Portland cement and is produced by heating limestone and other raw materials to high temperatures, which releases significant GHG emissions. Thus, by using SCMs, less clinker is required, thereby reducing GHG emissions, energy use and the environmental impact of cement production. Some SCMs such as fly ash and slag are by-products of other industrial processes, meaning that their use in cement production reduces waste and enhances resource efficiency. Moreover, the use of SCMs can enhance the properties of concrete, thereby increasing its durability and service life which helps to further reduce the overall embodied carbon of the structure.”
“In short, the use of SCMs contributes to reducing the carbon footprint of cement production by improving the efficiency of resource utilisation and reducing greenhouse gas (GHG) emissions during the production process. This has led to an increased demand for SCMs in the construction industry, as environmental concerns and sustainable development goals have become more prominent factors in the selection of building materials,” he adds.
Performance Characteristics of SCMs
The performance characteristics of concrete are significantly enhanced when SCMs are incorporated. Key attributes include:
- Increased Compressive Strength: Studies have demonstrated that concrete containing SCMs, particularly silica fume and GGBS, can achieve higher compressive strengths compared to conventional concrete mixtures. This is crucial for high-performance applications, such as high-rise buildings and infrastructure.
Dr SB Hegde, Professor, Jain College of Engineering and Technology, Hubli, and Visiting Professor, Pennsylvania State University, USA states, “The raw mix plays a vital role in clinker formation. A high liquid phase due to improper ratios of silica, alumina, and iron oxide can lead to excessive melting. Controlling the silica modulus (SM: 2.3-2.7) and alumina modulus (AM: 1.3-1.8) ensures a more stable clinker and reduces the risk of red river formation. If the raw mix is improperly proportioned, red river formation becomes more likely due to high fluxing compounds that melt at lower temperatures. The occurrence of red river has numerous negative impacts on both clinker quality and kiln performance.”
- Reduced permeability: SCMs improve the density of the concrete matrix, leading to reduced permeability. This characteristic is vital for structures exposed to harsh environmental conditions, as it minimises water ingress and subsequent damage.
- Altered hydration kinetics: The presence of SCMs can influence the hydration process of cement, often resulting in a slower but more sustained release of heat. This is beneficial in mass concrete applications where heat buildup can lead to cracking.
- Long-term strength development: Concrete containing SCMs typically exhibits improved long-term strength characteristics. While initial strength development may be slower, the overall strength continues to increase over time as the pozzolanic reactions progress.
Guidelines and Standards
The effective use of SCMs in concrete is governed by various guidelines and standards. In India, the Bureau of Indian Standards (BIS) has established specific specifications for the use of fly ash and GGBS in concrete.
- IS 456:2000: This Indian Standard provides general guidelines for the use of SCMs in concrete and outlines performance requirements to ensure the quality of construction materials. Adherence to these standards is crucial for maintaining the integrity and performance of concrete.
- IS 1489 (Part 1 and Part 2): These standards specifically address the use of fly ash and GGBS, providing criteria for their quality, chemical composition, and performance in concrete.
Following these guidelines ensures that SCMs contribute positively to concrete performance, supporting the construction of durable and sustainable structures.
Challenges in SCM Adoption
Despite their numerous advantages, several challenges hinder the widespread adoption of SCMs in India:
- Quality variability: The quality of SCMs can vary significantly depending on their source and production methods. This variability can lead to inconsistencies in concrete performance, necessitating rigorous quality control measures.
- Regulatory barriers: A lack of comprehensive regulations and standards for SCMs can impede their acceptance and use in construction projects. Greater clarity and uniformity in regulations would facilitate broader adoption.
- Compatibility issues: Different types of cement and SCMs may not always be compatible, leading to challenges in mix design. It is essential to conduct thorough testing to ensure that the chosen SCMs integrate well with the cement used in a specific project.
Shreesh A Khadilkar, Consultant and Advisor, and Former Director Quality and Product Development, ACC says, “Clinkers with good reactivity are observed to show 1 Day strengths in lab ground cements of 30 to 35 MPa. Higher values being observed when clinker alkali sulphates are high (especially with Petcoke as fuel), the achieved Blaine’s and quantity of nibs removed from the lab ground cement, in the fixed grinding time is also indicative of clinker grindability. Judicious raw mix optimisation with existing or alternative corrective materials (with the fuel mix used by the plant) can be attempted so as to have a clinker with improved reactivity/hydraulic potential. In a running plant the approach has to be by attempting small gradual changes to clinker composition and assessing the impact of the changes, on kiln performance and clinker quantity.”
Awareness and training: There is a need for increased awareness and training among construction professionals regarding the benefits and proper use of SCMs. Educating stakeholders can drive their acceptance and utilisation.
Successful Applications of SCMs
Several projects across India have successfully demonstrated the benefits of using SCMs, showcasing their effectiveness in enhancing concrete performance while reducing environmental impact:
- Delhi Metro Rail Corporation (DMRC): In the construction of the DMRC, high volumes of fly ash were used to produce concrete. This decision resulted in substantial cost savings, improved workability, and reduced environmental impact. The use of SCMs also contributed to the project’s overall sustainability goals.
- Narmada River Valley Project: In this project, GGBS was incorporated into the concrete mix, enhancing the durability and longevity of structures exposed to the water-saturated environment. The use of GGBS ensured that the concrete could withstand the harsh conditions prevalent in the region, reducing maintenance needs and extending the service life of the structures.
These case studies illustrate the practical benefits of using SCMs in large-scale construction projects, reinforcing their viability as sustainable alternatives.
Future Trends in SCM Use
As the Indian cement industry evolves, several trends are expected to shape the future of SCM utilisation:
Innovations in materials: Research into new SCMs, such as bio-based materials and advanced pozzolans, is on the rise. These innovations may expand the range of materials available for sustainable concrete production, providing more options for construction professionals.
Increased awareness: Growing awareness among construction professionals about the benefits of SCMs is likely to drive their adoption. Workshops, seminars, and training programs can play a crucial role in educating stakeholders about proper mix design and applications.
Government support: Policymakers can promote the use of SCMs by offering incentives for sustainable construction practices. This can include subsidies, tax breaks, or recognition for projects that utilise SCMs, encouraging broader acceptance.
Technological advancements: Advances in technology may facilitate better quality control, enabling more consistent production of SCMs and improving their integration into concrete mixtures.
Conclusion
SCMs represent a vital component in the transition toward more sustainable concrete production. By incorporating these materials, the Indian cement industry can significantly reduce its carbon footprint, enhance concrete performance, and contribute to a circular economy. While challenges remain, the benefits of SCMs far outweigh the drawbacks, making them an essential element in the future of sustainable construction. As awareness grows
and innovations emerge, SCMs are poised to play an even more significant role in shaping a greener built environment.
– Kanika Mathur
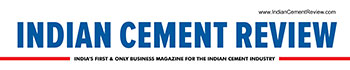
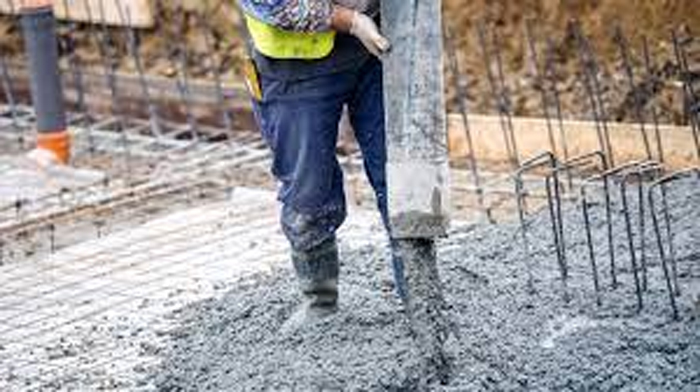
Tamil Nadu is set to host one of India’s five national carbon capture and utilisation (CCU) testbeds, aimed at reducing CO2 emissions in the cement industry as part of the country’s 2070 net-zero goal, as per a news report. The facility will be based at UltraTech Cement’s Reddipalayam plant in Ariyalur, supported by IIT Madras and BITS Pilani. Backed by the Department of Science and Technology (DST), the project will pilot an oxygen-enriched kiln capable of capturing up to two tonnes of CO2 per day for conversion into concrete products. Additional testbeds are planned in Rajasthan, Odisha, and Andhra Pradesh, involving companies like JK Cement and Dalmia Cement. Union Minister Jitendra Singh confirmed that funding approvals are underway, with full implementation expected in 2025.
Image source:https://www.heavyequipmentguide.ca/
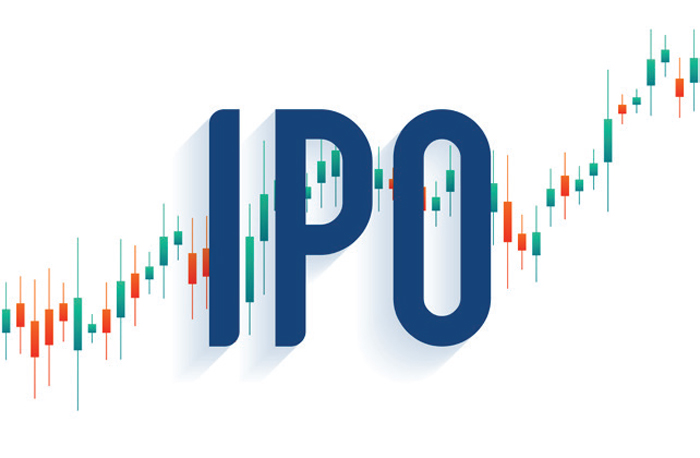
JSW Cement has set the price range for its upcoming initial public offering(IPO) at US$1.58 to US$1.67 per share, aiming to raise approximately US$409 million. As reported in the news, around US$91 million from the proceeds will be directed towards partially financing a new integrated cement plant in Nagaur, Rajasthan. Additionally, the company plans to utilise US$59.2 million to repay or prepay existing debts. The remaining capital will be allocated for general corporate purposes.
Concrete
Cement industry to gain from new infrastructure spending
Published
1 month agoon
July 24, 2025By
admin
As per a news report, Karan Adani, ACC Chair, has said that he expects the cement industry to benefit from the an anticipated US$2.2tn in new public infrastructure spending between 2025 and 2030. In a statement he said that ACC has crossed the 100Mt/yr cement capacity milestone in April 2025, propelling the company to get closer to its ambitious 140Mt/yr target by the 2028 financial year. The company’s capacity corresponds to 15 per cent of an all-India installed capacity of 686Mt/yr.
Image source:https://cementplantsupplier.com/cement-manufacturing/emerging-trends-in-cement-manufacturing-technology/