Concrete
IGNITING PROGRESS
Published
2 years agoon
By
admin
Converting raw materials into clinker through high-temperature kiln processes, pyroprocessing is a critical stage in cement manufacturing. ICR delves into the efficiency improvements that include advanced control systems, technological upgrades, and the integration of alternative fuels, such as biomass, which are making pyroprocessing a more productive process.
Pyroprocessing is a crucial stage in the cement manufacturing process, specifically responsible for the transformation of raw materials into clinker, the key ingredient in cement production. This high-temperature process occurs in the kiln, where raw materials, such as limestone, clay, and silica, undergo a series of complex chemical and physical transformations.
The first stage involves the preheating of the raw materials, where they are dried and preheated by the hot gases from the kiln. Subsequently, the materials enter the calcination zone, where intense heat causes chemical reactions, converting limestone (calcium carbonate) into lime (calcium oxide) and releasing carbon dioxide. The resulting clinker nodules are then cooled in the cooling zone.
Pyroprocessing is energy-intensive, with temperatures reaching around 1450 oC, and it plays a pivotal role in ensuring the formation of high-quality clinker, which, when mixed with gypsum, becomes cement. The control and optimisation of pyroprocessing parameters are critical for achieving the desired cement properties and maintaining sustainability in the cement manufacturing industry.
EFFICIENCY IN PYROPROCESSING
Efficiency gains in productivity, energy conservation, and cost-effectiveness within the pyroprocessing phase of cement plants can be attained through a multifaceted approach. Employing advanced process control systems ensures real-time monitoring and regulation of crucial parameters, thereby optimising conditions for pyroprocessing and diminishing energy consumption.
Amarkant Pandey, Deputy General Manager (Process), Prism Johnson (Cement Division), Satna, in his case study, outlines that to optimise efficiency, the capacity enhancement projects must incorporate state-of-the-art technologies and process improvements. For example, kiln feed transport bucket elevators have been upgraded 352.BE250 and BE340 were upgraded (to 723 tph) to increase kiln tonnage, kiln feed rotary valves, ID Fan motors and VFDs have been changed, cooler has been upgraded from SF 5×6 to SF-CB 5×7 (177 to 206 m2 grate area) and more. These advancements aim to reduce energy consumption, enhance product quality, and ensure sustainable production practices.
The integration of alternative fuels, such as biomass and waste-derived sources, offers a dual benefit by reducing dependence on conventional energy while addressing environmental concerns. Waste heat recovery systems play a pivotal role in capturing and utilising excess heat generated during pyroprocessing, transforming it into additional energy to enhance overall efficiency. Analysing and optimising the composition of raw materials and fuels through advanced technologies aids in maintaining a stable and efficient pyroprocessing operation, minimising variability and energy use.
AK Dembla, President and Managing Director, and Deepti Varshney, Deputy General Manager, Humboldt Wedag India, in their article KHD Technology and Efficient Processes – A Better Tomorrow, state, “Indian Cement Industry has lot of potential to utilise alternate fuels in cement manufacturing with benefits in terms of conservation of natural resources and prevention of environmental hazards including mitigation of Greenhouse Gas Emission, hence serving the goal of sustainable growth and development in India. Industrial and mineral wastes from mineral processing industries, such as chemicals, metallurgy, petrochemical, power, paper and pulp accounts for more than 200MT out of which more than 6MT are hazardous and can be used alternatively in cement kilns. Today, many cement plants are exploring to collect all the municipal waste of the area, process it and use it as an alternate fuel. Keeping in view all these, long ago KHD has rolled down equipment to use alternate fuels
of varying degrees and one such example is the combustion chamber.”
According to PC Jain, Head – Grinding Units, Wonder Cement, “Pyroprocessing, being a crucial part of cement manufacturing, holds significant potential for energy and cost efficiency improvements. At Wonder Cement, we prioritise sustainable practices and innovation in our pyroprocessing methods. Here are some steps that cement manufacturers can take to enhance energy and cost efficiency in pyroprocessing:
• Utilisation of alternative fuels: Incorporating alternative fuels like biomass, refuse-derived fuels (RDF), and other waste materials in the pyroprocessing stage can significantly reduce energy consumption and costs. This approach not only aids in minimising reliance on traditional fossil fuels but also contributes to waste management and environmental sustainability.
• Optimised kiln operation: Implementing advanced technologies and process optimisation techniques such as using preheaters, calciners, and efficient kiln designs can enhance heat transfer, reduce fuel consumption and improve overall thermal efficiency. This optimisation ensures maximum output with minimal energy input.
• Waste heat recovery systems: Installing waste heat recovery systems enables the capture and utilisation of excess heat generated during pyroprocessing. This reclaimed heat can be utilised for various purposes within the manufacturing plant, such as preheating raw materials or generating electricity, thereby reducing energy costs and improving overall efficiency.
• Continuous research and development: Investing in research and development to explore innovative technologies and materials for pyroprocessing is crucial. Constant innovation can lead to the development of more efficient and environmentally friendly processes, further reducing energy consumption and costs.
• Employee training and awareness: Educating and involving employees in energy-saving
initiatives and best practices can significantly contribute to optimising pyroprocessing operations. Engaged and informed personnel often bring forward valuable ideas and suggestions for improving efficiency.”
“We are committed to leveraging these strategies and continually exploring new avenues to enhance the energy and cost efficiency of our pyroprocessing operations. By prioritising sustainability and innovation, we aim to set new benchmarks in the cement manufacturing industry while reducing our environmental footprint,” he adds.
Optimisation of clinker cooling systems, investment in energy-efficient kiln technologies, and the integration of preheating systems contribute further to enhancing the thermal efficiency of the pyroprocessing stage. Regular maintenance practices and equipment upgrades, as well as the adoption of data analytics and digitalisation tools, facilitate the identification of areas for improvement and prediction of potential issues.
Keyur Shah, Business Manager, SB Engineers, says “Cement pyroprocessing is one of the hottest industrial processes and requires a huge amount of energy. It is also one the biggest consumers of fossil fuel which contributes to environmental pollutants. Improving energy efficiency and reducing pollutants are currently major goals of the cement industry. Therefore, monitoring of thermal and pollutant data becomes absolutely vital.”
“Traditionally, kiln, which is the consumer of approximately 40 per cent of fossil fuel of a cement plant, is monitored by a single point burning zone pyrometer, which does not give any useful data to achieve aforesaid goals. Using the latest technology of thermal imaging for the monitoring of the kiln burning zone and connected processes of clinker cooler offers required holistic monitoring as well provides required data for control and improvements. Similarly, measurement of flow of hot gases taped from kiln and cooler, offers vital data for consumption of energy and regeneration. All this data can be and will be required to be used for achieving goals using machine learning and artificial intelligence ( AI and ML),” he adds.
Employee training programs ensure a knowledgeable workforce, well-versed in the latest technologies and best practices, contributing to the successful implementation of energy-saving initiatives. By embracing these strategies, cement plants can realise substantial improvements in productivity, energy efficiency, and cost-effectiveness during the pyroprocessing stage of cement manufacturing.
USE OF ALTERNATIVE FUELS AND RAW MATERIALS
Cement manufacturers are increasingly embracing the use of alternative fuels and raw materials in the pyroprocessing stage as part of their efforts to enhance sustainability, reduce environmental impact, and optimise production processes.
They are incorporating alternative fuels, such as biomass, municipal solid waste, and industrial by-products, into their kiln systems. This reduces dependence on traditional fossil fuels and contributes to lower greenhouse gas emissions. Advanced combustion technologies and equipment modifications are often necessary to accommodate these alternative fuels.
According to A Review on Pyroprocessing Techniques for Selected Wastes Used for Blended Cement Production Applications (Hindawi, August 2020), pyroprocessing is an important stage in cement manufacturing. In this process, materials are subjected to high temperatures so as to cause a chemical or physical change. Its control improves efficiency in energy utilisation and hence enhances production for good quality assurance.
Kilns used in cement manufacturing are complex in nature. They have longer time constants, and raw materials used have variable properties. They are therefore difficult to control. Additionally, the inclusion of various alternative fuels in burning makes the process more complex as the fuel characteristics remain inconsistent throughout the kiln operation. Fuel intensity standards for kilns using fuel oil are very high, ranging from 2.9?GJ to 7.5?GJ/tonne of clinker produced. Grinding of clinker consumes power in the range of 2.5?kWh/tonne of clinker produced. These and other pyroprocessing parameters make cement production costly.
The pyroprocessing process in kilns and the grinding technologies therefore must be optimised for best processing. This paper discusses the cement manufacturing and grinding processes. The traditional kiln technologies and the current and emerging technologies together with general fuel and energy requirements of cement manufacturing have been discussed. From the discussion, it has been established that the cement manufacturing and grinding technologies are capital-intensive investments.
The kiln processes are advanced and use both electricity and natural fuels which are expensive and limited factors of production. The raw materials used in cement manufacturing are also limited and sometimes rare. The calcination of the raw materials requires external energy input which has contributed to the high cost of cement especially to low-income populations in the developing countries. Self-calcining materials, in which the pozzolanic materials burn on their own, are potential pozzolanic materials with great potential to lower the cost of cement production. Such materials, as shown from the previous research study, are rice husks, broken bricks, spent bleaching earth, and lime sludge. There is a need, therefore, for research to look into ways of making cement using kiln processes that would use this property. This will be cost-effective if successful. It can be done at micro- and small-scale enterprises.
Cement manufacturers, across the globe are proactively addressing regulatory challenges associated with the use of alternative fuels and raw materials. Compliance with emission standards, environmental regulations, and safety protocols is crucial. Engaging with regulatory authorities and adopting best practices help ensure a smooth transition to alternative inputs. They are also investing in advanced technologies and equipment designed to handle alternative fuels and raw materials efficiently. This includes state-of-the-art kiln designs, preheating and precalcination systems, and clinker cooling technologies that can accommodate the unique characteristics of alternative inputs.
CEMBUREAU, in its report A New Momentum for Standardisation, October 2023, states that the organisation is in line with the European Commission in that the cement standardisation activities must support the green transition. One of the levers identified in CEMBUREAU Roadmap to reduce the cement carbon footprint is to replace part of the clinker by cement constituents other than clinker. Low-clinker cements are possible in the existing cement standards and are already available on the market, but they face hurdles and scalability issues (due to the limited availability of clinker substitutes) as well as technical limitations as not all cement types are adapted to ensure durability for all exposure classes.
CEMBUREAU has been calling for a well-functioning standardisation process. Unfortunately, the Mandate M/114 concerning the standardisation work for cement is no longer up to date and the Commission has not been able to revise it in the last 8 years. As a result, the EU cement industry supported the work of CEN/TC 51 ‘Cement and building limes’ to shift through a non-harmonised route to speed up the way to have the new standards EN 197-5 (Portland-composite cement CEM II/C-M and Composite cement CEM VI) and EN 197-6 (Cement with recycled building materials) available for the placement of new low-carbon cements in the market.
TECHNOLOGY FOR PROCESS OPTIMISATION
Technology plays a pivotal role in advancing pyroprocessing within the cement manufacturing sector, offering significant improvements in process efficiency, energy utilisation, and overall operational excellence. State-of-the-art process control systems, equipped with real-time data monitoring capabilities, ensure the precise regulation of key parameters during pyroprocessing. These systems contribute to consistent clinker quality, reduced energy consumption and overall process optimisation.
Arpan DilipKumar Parekh, Technical Head – Vice-President, JK Cement, says, “Technology plays a crucial role in pyroprocessing within the cement manufacturing industry. Advancements in technology have led to improvements in efficiency, energy conservation, environmental sustainability, and overall process control. Modern technology allows for the design and optimisation of kilns to enhance heat transfer, minimise heat losses, and improve overall energy efficiency. Computational fluid dynamics (CFD) simulations and modelling are employed to optimise the design of kiln systems.”
“Advanced control systems, such as distributed control systems (DCS) and programmable logic controllers (PLC), enable precise control and automation of the pyroprocessing parameters. This includes temperature control, fuel and air ratios, and material feed rates. High-tech sensors and instrumentation are used to monitor various aspects of the pyroprocessing stage, including temperature profiles, gas compositions, and pressure conditions. This real-time data is crucial for process optimisation and control,” he adds.
Advanced combustion technologies facilitate the effective use of alternative fuels, ensuring proper combustion while maintaining the requisite high temperatures for clinker formation. Waste heat recovery systems, incorporating technologies such as heat exchangers and organic Rankine cycle (ORC) units, harness excess heat generated during pyroprocessing, converting it into additional power and bolstering overall energy efficiency.
Innovations in kiln design, utilisation of high-performance refractory materials, and adoption of data analytics and digitalisation tools further contribute to the optimisation of pyroprocessing parameters. By incorporating these technological advancements, cement manufacturers can not only improve energy efficiency but also reduce environmental impact, ultimately enhancing the overall sustainability of the pyroprocessing stage in cement production.
CONCLUSION
Cement manufacturers can achieve sustainability in pyroprocessing by adopting a comprehensive and integrated approach that encompasses environmental, social, and economic considerations. One key strategy involves the incorporation of alternative fuels and raw materials, such as biomass and waste-derived sources, to reduce dependence on traditional fossil fuels and divert waste from landfills. Enhancing energy efficiency through advanced technologies, waste heat recovery systems, and optimised kiln designs contributes to minimising overall energy consumption during pyroprocessing.
Emission reduction technologies, including dust collectors and electrostatic precipitators, help mitigate the environmental impact by controlling particulate matter and other emissions. Exploring the use of clinker substitutes, like fly ash and slag, as well as blended cements, reduces the carbon footprint of cement production.
Additionally, investigating the feasibility of carbon capture and storage technologies addresses greenhouse gas emissions. Life cycle assessments provide a holistic view of the environmental impact of the entire cement production process, guiding decision-making and identifying areas for improvement. Water conservation measures, occupational health and safety practices, community engagement, and adherence to sustainability standards and certifications further contribute to a more sustainable pyroprocessing stage. These strategies collectively align with global initiatives to promote environmentally responsible industrial practices.
- –Kanika Mathur
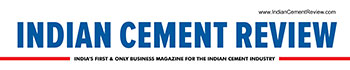
You may like
-
Unattended issues become risks
-
Wonder Cement commissions fifth production line at Nimbahera
-
How Upgrades Can Deliver Energy Savings Across the Cement Process
-
How Upgrades Can Deliver Energy Savings Across the Cement Process
-
We consistently push the boundaries of technology
-
The Science and Application of Grinding Aids
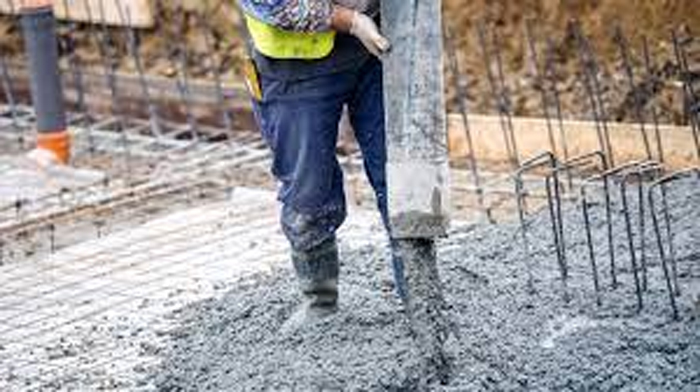
Tamil Nadu is set to host one of India’s five national carbon capture and utilisation (CCU) testbeds, aimed at reducing CO2 emissions in the cement industry as part of the country’s 2070 net-zero goal, as per a news report. The facility will be based at UltraTech Cement’s Reddipalayam plant in Ariyalur, supported by IIT Madras and BITS Pilani. Backed by the Department of Science and Technology (DST), the project will pilot an oxygen-enriched kiln capable of capturing up to two tonnes of CO2 per day for conversion into concrete products. Additional testbeds are planned in Rajasthan, Odisha, and Andhra Pradesh, involving companies like JK Cement and Dalmia Cement. Union Minister Jitendra Singh confirmed that funding approvals are underway, with full implementation expected in 2025.
Image source:https://www.heavyequipmentguide.ca/
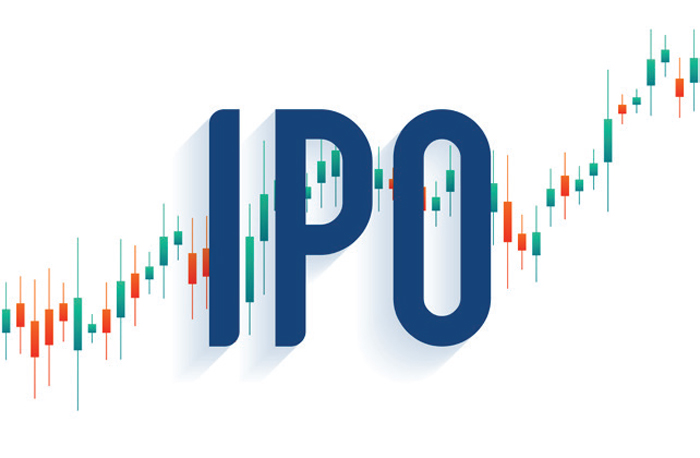
JSW Cement has set the price range for its upcoming initial public offering(IPO) at US$1.58 to US$1.67 per share, aiming to raise approximately US$409 million. As reported in the news, around US$91 million from the proceeds will be directed towards partially financing a new integrated cement plant in Nagaur, Rajasthan. Additionally, the company plans to utilise US$59.2 million to repay or prepay existing debts. The remaining capital will be allocated for general corporate purposes.
Concrete
Cement industry to gain from new infrastructure spending
Published
3 weeks agoon
July 24, 2025By
admin
As per a news report, Karan Adani, ACC Chair, has said that he expects the cement industry to benefit from the an anticipated US$2.2tn in new public infrastructure spending between 2025 and 2030. In a statement he said that ACC has crossed the 100Mt/yr cement capacity milestone in April 2025, propelling the company to get closer to its ambitious 140Mt/yr target by the 2028 financial year. The company’s capacity corresponds to 15 per cent of an all-India installed capacity of 686Mt/yr.
Image source:https://cementplantsupplier.com/cement-manufacturing/emerging-trends-in-cement-manufacturing-technology/