Concrete
Strength of a refractory material changes with temperature
Published
2 years agoon
By
admin
Tushar Khandhadia, General Manager – Production, Udaipur Cement Works Limited, takes us through the workings of refractories at a cement plant while giving important inputs about their maintenance.
Tell us about the types of refractoriesused in your organisation and their respective purposes.
In our organisation, various types of refractories are utilised to withstand the extreme conditions present in the production of cement. These refractories are chosen based on their properties and suitability for specific areas within the cement manufacturing process. Here are common types of refractories used in our plant and their respective purposes:
Alumina refractories: Alumina refractories, typically made from alumina (Al2O3), are used in the kiln and cooler areas of the cement plant due to their high refractoriness and resistance to alkalis and abrasion.
Magnesia (magnesite) refractories: Magnesia refractories, made from magnesite (MgO), are used in the burning zone of the rotary kiln where temperatures are extremely high. They exhibit excellent resistance to alkaline materials present in the cement process.
Silica refractories: Silica refractories, composed primarily of silica (SiO2), are utilised in the lower temperature zones of the cement kiln and preheater. They provide good resistance to acidic materials and thermal shock.
Basic refractories (such as magnesia-chrome and magnesia-spinel): Basic refractories containing magnesia or chrome are employed in cement plant areas where the conditions are more basic (alkaline). They are used in high-temperature zones and exhibit resistance to alkaline materials.
Chrome-magnesia refractories: Chrome-magnesia refractories, combining chrome and magnesia, are utilised in areas exposed to higher temperatures and wear, such as cement kiln burners and coolers.
Insulating refractories (lightweight insulating bricks, ceramic fibres): Insulating refractories are used to reduce heat loss and improve energy efficiency in cement plant applications. They are employed in areas like the preheater and cooler to minimise thermal conductivity and conserve energy.
High-alumina refractories: High-alumina refractories, containing high levels of alumina, are used in areas where both high refractoriness and resistance to abrasive materials are needed, such as the transition zone of the cement kiln.
What are the key materials used in building a refractory lining to the kiln?
The key materials used during the refractory lining in a kiln include:
Alumina bricks – purpose: Alumina bricks, made of alumina (aluminum oxide), are crucial for high-temperature resistance in critical areas of the kiln, providing durability and thermal stability.
Basic bricks – purpose: Basic bricks, typically made from materials like magnesia or dolomite, are resistant to alkaline conditions. They are used in high-temperature zones of the kiln.
Key bricks – purpose: Key bricks are special bricks used to secure the refractory lining with closing each ring, providing stability and structural integrity to the overall refractory structure within the kiln.
Ceramic fibbers – purpose: Ceramic fibres, made from alumina-silicate or other compositions, serve as effective insulation in the refractory lining. They reduce heat loss and improve energy efficiency in the kiln.
Sodium silicate and mortar solution – purpose: Used as a binder or for coating refractory materials to enhance their properties and adhesion, improving the integrity and longevity of the refractory lining. The physical and chemical properties of mortars must be matched to the type of brick being installed.
Shim – purpose: Shims are thin, flat pieces of material used to fill small gaps or adjust the alignment of refractory bricks, ensuring a snug fit and proper construction of the refractory lining.
What are the key properties of a refractory that support the cement making process?
The key properties of a refractory that support the cement making process are:
- High refractoriness
- Chemical inertness and resistance
- Thermal shock resistance
- Abrasion and erosion resistance
- Porosity and permeability
- Mechanical strength and load-bearing capacity
- Resistance to alkali and alkali vapours
- Chemical composition and raw materials selection
Tell us more about the porosity and permeability of the refractory.
The porosity and permeability of refractories are important properties that influence their performance in high-temperature applications such as furnaces, kilns and other thermal processing equipment.
- Porosity in refractories refers to the volume percentage of voids or pores within the material. It affects the refractory’s ability to retain and release gases, liquids and thermal conductivity. Low porosity is generally desirable in refractories as it leads to better thermal and chemical resistance. High porosity can result in reduced strength and thermal conductivity.
- Permeability is the ability of a refractory material to allow the flow of gases or liquids through its pores or interconnected voids. It is influenced by the porosity and the connectivity of the pores within the material. Permeability is an essential property for refractories used in applications where gases or liquids need to flow through the refractory material, such as cement kiln.
The specific values of porosity and permeability for refractories can vary widely depending on the type of refractory material, its composition, manufacturing process, and intended application. Refractories can range from low-porosity dense materials to highly porous insulating materials, each designed for specific use cases.
What is the maximum temperature that a refractory can withhold? How does its strength differ from ambient temperature to high temperature?
Name of the spinel group mineral Composition Melting point. (oC)
Spinel MgAl2O4 (MgO. Al2O3) 2135
Hercynite FeAl2O4 (FeO. Al2O3) 1780
Picro-chromite MgCr2O4 (MgO. Cr2O3) 2350
Chromite FeCr2O4 (FeO. Cr2O3) 2075
Magnetite Fe3O4 (FeO.Fe2O3) 1591
- silica bricks: 1400-1500°C
- fireclay bricks: 1100-1400°C
- high-alumina bricks: 1400-1700°C
- magnesia/ doloma bricks: 1500-1800°C
The maximum temperature that a refractory can withstand is known as its refractoriness. Refractories are generally categorised into three main types based on their refractoriness:
- Fireclay refractories: These have a refractoriness of around 1600oC to 1800oC.
- High alumina refractories: They have a refractoriness ranging from about 1750oC to 1900oC.
- Basic refractories: Spinel, Hercynite, Chromite etc. They have a refractoriness ranging from about 1750oC to 2100oC.
- Silica refractories: Silica refractories have a refractoriness of approximately 1800oC to 1950oC
Strength of a refractory material changes with temperature. At ambient or room temperature, refractories generally have their highest mechanical strength. As the temperature increases, the strength of the refractory typically decreases due to thermal expansion, softening and possible chemical reactions. The rate and extent of this strength reduction vary based on the type of refractory and its composition.
Tell us about the installation and operating process of refractories in the kiln.
Here’s an overview of the installation and operating process of refractories in a cement kiln:
Installation of refractories
- Preparation and inspection: Before installation, inspect the kiln’s interior to assess the condition of the existing refractory lining and identify any areas requiring repair or replacement. After selection of area clean the kiln shell area properly for fixing of bricks lining.
- Material selection: Choose appropriate refractory materials based on the specific zone of the kiln (e.g., calcination, upper transition, burning zone, lower transition and cooling). Different
- zones have varying temperature and chemical exposure requirements.
- Laying the refractory bricks: Use skilled masons or technicians to install the refractories according to the design specifications. Refractory materials are laid in specific patterns to create the desired lining by using brick lining machine or kiln jack. Using of mortar are optional depend on past experience and kiln shell condition
- Sim fastening and inspection: To tighten each ring of bricks lining use sim fastening specially in alumina bricks lining, tab each line with wooden or rubber hammer for checking tightness of ring if it is found loose reapply sim.
- Drying and curing: Allow the refractory lining to dry and cure according to the manufacturer’s guidelines. Controlled heating and drying help to prevent cracking and ensure proper bonding.
Operating Process
• Start-up and warm-up: Gradually heat up the kiln to the desired operating temperature to avoid thermal shock to the refractories. The start-up process involves slowly increasing the temperature over few hours or days for drying out the refractories and ring tighten after expansion of the bricks.
• Monitoring and Control: Use advanced monitoring (shell scanner) systems to measure and controls the temperature and other critical parameters. Monitoring helps optimise the firing process and prevent damage to the refractory lining.
• Refractory maintenance: Regularly inspect the refractory lining through shell temperature for signs of wear, erosion, cracks or hot spots. Start a proactive maintenance programme to repair or replace damaged refractory sections promptly.
• Refractory repair and replacement: When necessary, schedule shut-downs for refractory repair or replacement. Use skilled personnel to execute repairs and ensure the new refractories are properly anchored and cured before restarting the kiln.
• Cool-down: After the cement production process or maintenance activities, gradually cool down the kiln to avoid thermal stress on the refractories. Controlled cooling is essential for prolonging the refractory life.
• Quality Control: Regularly assess the performance of the refractories, analyse their wear patterns, and gather data to optimise the refractory selection for future installations.
Efficient installation and careful operation of refractories in a cement kiln are vital for achieving optimal productivity, reducing downtime and extending the service life of the refractory lining. Properly maintained and installed refractories contribute to cost-effective and sustainable cement production.
What are the standards set for refractories in a cement kiln?
There are two standard shapes used in kiln for straight portion, viz. ISO shape and VDZ shape. ISO (International Organisation for Standardisation) is as per international standard and VDZ (Verein Deutsche Zementwerke) is German standard. In case of ISO brick, cold face thickness is fixed, i.e., 103 mm and in case of VDZ shape it is less than 80 mm. The average thickness for VDZ shape is fixed for all shape, i.e., 71.5 mm, that means weight for both combination shape used during lining will be same. But in case of ISO shape weight of the two types of bricks used in combination are different.
VDZ shape is prefixed with B, whereas ISO series bricks are prefixed with 3K. The last two digit represents the height of the brick or thickness of the lining in cm. e.g., B 322 means it is VDZ series brick (as B is prefix) and is having lining thickness 22 cm.
In case of basic bricks, VDZ shape is used in most of the kilns except for large kiln diameter like 6 M, where ISO shape is used for basic brick also. In case of alumina bricks, ISO shape is used in most of the kilns. However, up to 5 M dia kiln it is better to use VDZ shape for the entire length because of the following advantages:
- Better contact / arch effect with kiln shell for VDZ shape.
- Weight of VDZ shape brick is lower, hence easier to handle.
- Average thickness of VDZ shape is ~20 – 25 mm lower than ISO shape.
- Uniform compactness is achieved during green pressing of VDZ shape.
- Uniform burning condition in case of VDZ shape during manufacturing.
- Easier to install and minimum handing damage in case of VDZ shape.
The thickness of the lining is typical function of the kiln diameter. Recommended thickness of brick linings according to the shell diameter of rotary furnaces:
Kiln diameter Refractory thickness
up to 3.6 m 180 mm
3.6 to 4.2 m 200 mm
4.2 to 5.2 m 220 mm
Above 5.2 m 250 mm
The above table indicates the length of different zone and kiln environment at corresponding area.
• Discharge zone: This is also known as cooling zone. The length of discharge zone depends on the position of burner pipe tip. Generally, it is 0 -1 times of kiln diameter i.e., for 4-meter dia. kiln, the length of this zone would be approximately 4 m. There will not be coating in this area. The brick used for this area should have high abrasion resistance. High alumina brick or spinel bonded magnesia brick is suitable for this area.
• Lower transition zone: The area in between cooling and burning zone is called lower transition zone. The length varies from 1 – 2 times of kiln diameter. In this zone the coating formation on brick is unstable. Hence the brick used in this zone should have high resistance against spalling, abrasion, and chemical corrosion. Spinel bonded or hercynite bonded magnesia brick can be considered suitable for this zone. In case of very severe kiln condition (high redox condition and high chemical corrosion) zirconia-based magnesia brick may be considered.
• Burning zone: The most important area of kiln where stable coating is observed is called burning or sintering zone. The length of this zone varies from three times the kiln diameter up to five times the kiln diameter. The refractory used for this area should have high temperature resistance and high chemical corrosion resistance. In low the alkali environment mag-chrome brick is apt, but in high alkali environment hercynite bonded or spinel bonded magnesia brick is suitable.
• Upper transition zone: The area in between burning and calcining zone, where unstable coating is formed, is denoted as upper transition zone. The length of this zone can be 2-3 times of kiln diameter. Due to instability of coating in this zone, bricks having high thermal shock resistance should be used. Hercynite bonded or spinel bonded magnesia bricks are suitable.
• Calcining zone: The area between upper transition and kiln inlet is named as calcining zone. When the calcined raw meal enters the kiln, it is usually calcined up to 92-96 per cent. Rest of the calcination of kiln feed takes place in this area. The length of this zone is 7-8 times of kiln diameter. Generally, no coating is found in this area. The brick used for this area should have high spalling resistance and resistance against alkali sulfates and chlorides. Clog shape high alumina brick having 60 and 50 per cent alumina is suitable for this area.
While using high alkali loading in kiln, phosphate bonded alkali resistant bricks are
also recommended.
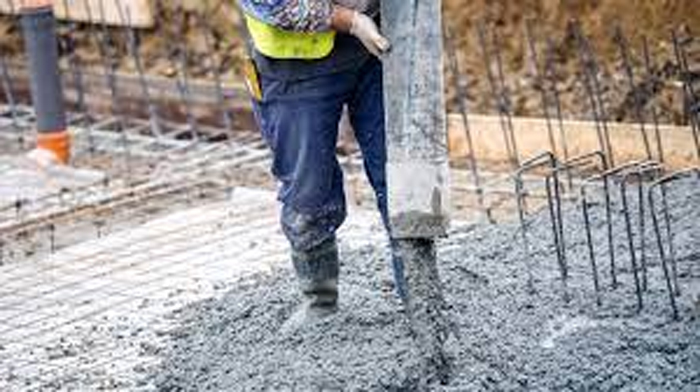
Tamil Nadu is set to host one of India’s five national carbon capture and utilisation (CCU) testbeds, aimed at reducing CO2 emissions in the cement industry as part of the country’s 2070 net-zero goal, as per a news report. The facility will be based at UltraTech Cement’s Reddipalayam plant in Ariyalur, supported by IIT Madras and BITS Pilani. Backed by the Department of Science and Technology (DST), the project will pilot an oxygen-enriched kiln capable of capturing up to two tonnes of CO2 per day for conversion into concrete products. Additional testbeds are planned in Rajasthan, Odisha, and Andhra Pradesh, involving companies like JK Cement and Dalmia Cement. Union Minister Jitendra Singh confirmed that funding approvals are underway, with full implementation expected in 2025.
Image source:https://www.heavyequipmentguide.ca/
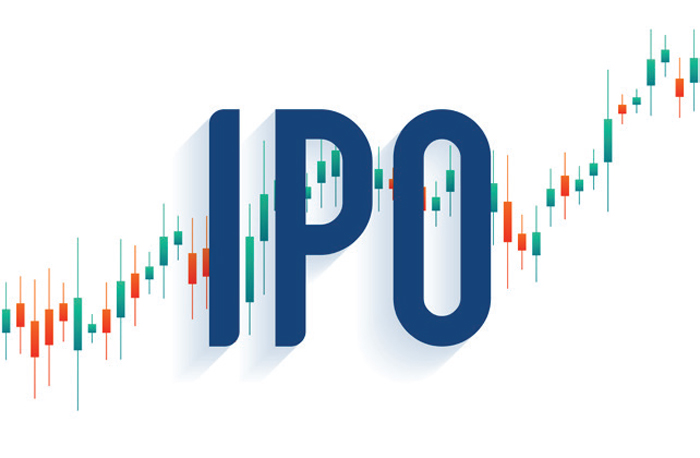
JSW Cement has set the price range for its upcoming initial public offering(IPO) at US$1.58 to US$1.67 per share, aiming to raise approximately US$409 million. As reported in the news, around US$91 million from the proceeds will be directed towards partially financing a new integrated cement plant in Nagaur, Rajasthan. Additionally, the company plans to utilise US$59.2 million to repay or prepay existing debts. The remaining capital will be allocated for general corporate purposes.
Concrete
Cement industry to gain from new infrastructure spending
Published
3 weeks agoon
July 24, 2025By
admin
As per a news report, Karan Adani, ACC Chair, has said that he expects the cement industry to benefit from the an anticipated US$2.2tn in new public infrastructure spending between 2025 and 2030. In a statement he said that ACC has crossed the 100Mt/yr cement capacity milestone in April 2025, propelling the company to get closer to its ambitious 140Mt/yr target by the 2028 financial year. The company’s capacity corresponds to 15 per cent of an all-India installed capacity of 686Mt/yr.
Image source:https://cementplantsupplier.com/cement-manufacturing/emerging-trends-in-cement-manufacturing-technology/