Concrete
Driving Efficiency
Published
2 years agoon
By
admin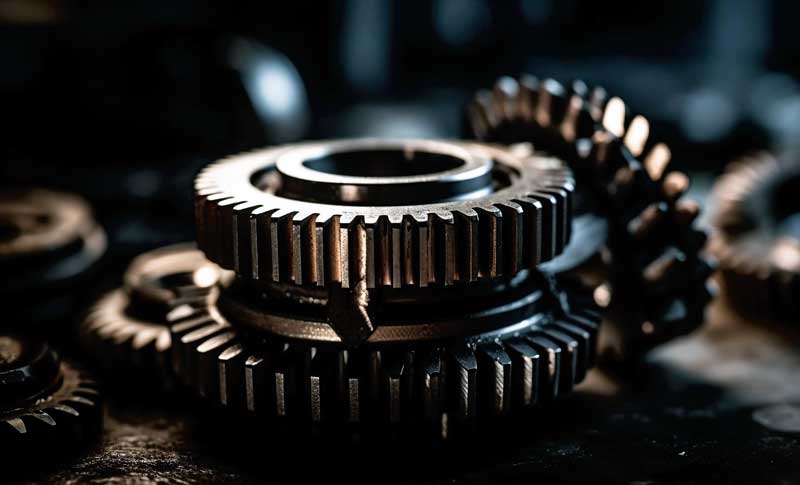
Advancements in technology are positively helping innovation in machine management at cement plants, thereby enhancing efficiency, resulting in cost savings. ICR delves into the latest updates in gears, drives and motors, which are key components for smooth functioning of equipment in cement manufacturing.
Gears, drives, and motors are essential components that play vital roles in the operations of a cement plant in India. Gears, with their toothed structure, are employed in various critical applications throughout the plant. One significant application is in the rotation of the cement kiln. The kiln is a large, cylindrical structure where raw materials are heated to high temperatures to produce clinker. Gears enable the smooth and controlled rotation of the kiln, ensuring the efficient and consistent processing of materials. Additionally, gears are utilised in cement mills, which are responsible for grinding the raw materials or clinker into a fine powder. By driving the rotation of the mill, gears facilitate the grinding process, enabling the materials to be finely ground and transformed into cement.
Gears are also integral to the functioning of conveyors and elevators within the plant. These systems are responsible for the movement of raw materials, clinker, and finished cement from one area to another. Gears assist in driving these mechanisms, ensuring the smooth and reliable transportation of materials throughout the plant.
Drives are responsible for providing the necessary power to operate various equipment within the cement plant. Motor drives are commonly used and are essential in controlling the speed and torque of electric motors. They enable precise control over equipment such as kilns, mills, crushers, and conveyors, ensuring optimal performance and efficiency in their operations. In addition to motor drives, hydraulic drives and pneumatic drives are employed in specific applications. Hydraulic drives utilise fluid power to generate motion and force, typically employed in heavy-duty machinery like crushers and clinker cooler systems. Pneumatic drives, on the other hand, utilise compressed air to provide motion and power and can be found
in systems such as air compressors and pneumatic conveyors.

Motors serve as the primary power sources for the various equipment in a cement plant. Electric motors are extensively used, driving fans, blowers, pumps, crushers, mills, and kilns. They convert electrical energy into mechanical energy, enabling the machinery to perform their intended functions efficiently. In larger-scale cement plants, high voltage motors are utilised to handle the higher power requirements. These motors are designed to operate at higher voltages and can effectively drive heavy machinery within the plant. Induction motors are also commonly employed due to their reliability and robustness, offering good performance and energy efficiency in various applications throughout the cement plant.
Collectively, gears, drives, and motors are integral components that ensure the smooth and efficient operation of a cement plant in India. They facilitate critical processes involved in cement production, such as raw material grinding, kiln rotation, and material transportation. By providing reliable power, precise control, and optimal performance, these components contribute significantly to the overall functionality and productivity of the cement plant.
“The manufacturing of cement involves an elaborate process, starting from the mining of necessary mineral resources to the processing of these minerals to obtain the final products with desired physical and chemical properties. In this process, rotary drive systems play a crucial role in powering heavy-duty critical equipment that operates under harsh conditions and heavy loads. These systems are utilised for various applications such as crushing, grinding, melting, mixing and conveying,” says Krishnaraj Sreedharan, Head of Customer Service, Flender Drives.
ACHIEVING EFFICIENCY WITH ACCURACY
Gears, drives, and motors play a crucial role in helping cement plants achieve efficiency in cement production, reduce costs, and save electricity and fuel. These components contribute to the overall optimisation of various processes, leading to improved performance and sustainability in the industry.
One significant aspect of gears, drives, and motors is their ability to provide enhanced process control. With precise control over speed, torque and operation, these components enable cement plants to enhance process parameters. For example, in the case of kilns and mills, the rotation speed can be adjusted to maintain optimal conditions for efficient and consistent cement production. This level of control minimises waste, reduces energy consumption, and enhances overall production efficiency.
Energy optimisation is another area where gears, drives, and motors play a vital role. Modern motor drives offer features such as variable speed control, allowing operators to match motor speeds to the load demand. By adjusting the motor speed according to the process requirements, energy consumption can be significantly reduced. This capability is particularly beneficial for equipment such as fans, blowers, and pumps, which consume a significant amount of energy in cement plants.
These components also contribute to improved equipment reliability. High-quality gears and drives help minimise the risk of unexpected failures and breakdowns. Furthermore, motors with efficient designs and robust construction can operate reliably under challenging conditions, reducing the need for frequent repairs and replacements. This leads to reduced downtime and maintenance costs, enhancing overall cost efficiency.
Gears, drives, and motors also contribute to fuel efficiency in cement plants. By optimising the operation of grinding mills, these components ensure effective pulverisation of raw materials or clinker while minimising energy consumption. Additionally, precise control over kiln rotation allows for better heat transfer, ensuring efficient fuel utilisation during the clinker production process. The result is reduced fuel consumption, leading to cost savings and lower environmental impact.
Another advantage of integrating gears, drives, and motors is the potential for process automation. By leveraging advanced control systems, these components enable real-time monitoring, data analysis, and decision-making based on process variables. Automation facilitates optimised equipment operation, energy management, and production scheduling. By automating repetitive tasks and optimising processes, cement plants can achieve higher efficiency, reduce human errors, and save both electricity and fuel.
Furthermore, gears, drives, and motors provide valuable data on their operating conditions, allowing for predictive maintenance planning. Through condition monitoring and sensor technology, these components can detect potential issues and provide insights on temperature, vibration, and other relevant parameters. This data enables proactive maintenance planning, minimising unplanned downtime and optimising maintenance costs.

MAINTENANCE OF GEARS, DRIVES AND MOTORS
To increase the lifetime and optimise the performance of gears, drives, and motors in cement plants, several maintenance practices can be implemented. Regular inspections should be conducted to visually assess the condition of these components and monitor temperature, vibration, and noise levels. This helps identify any signs of wear, misalignment, or damage early on.
Proper lubrication is crucial for the smooth operation of gears, drives, and motors. Following manufacturer recommendations for the type of lubricant, quantity, and frequency of lubrication is essential. Regularly checking lubrication levels and performing timely lubrication prevents excessive friction, wear and overheating.
Ensuring proper alignment of gears, drives, and motors is vital to avoid excessive loads and uneven wear. Precision alignment tools and techniques should be utilised to align shafts, couplings, and belts accurately. Dynamic balancing of rotating components should also be carried out to minimise vibrations, which can lead to premature failure and reduced lifespan.
Maintaining cleanliness around gears, drives, and motors is crucial to prevent the accumulation of dust, debris, and contaminants. Regular cleaning and removal of any buildup help maintain optimal performance and reduce the risk of overheating or component failure. Implementing dust prevention measures in the plant can minimise the ingress of dust into critical equipment.
Monitoring the temperature of gears, drives, and motors is important to detect abnormal heating patterns. Excessive heat can indicate issues such as inadequate lubrication, misalignment, or overloading. Temperature sensors and monitoring systems should be installed to identify and address temperature anomalies promptly.
Performing regular vibration analysis on gears, drives, and motors can help identify potential faults or imbalances. Vibration monitoring systems detect abnormal vibration patterns, indicating misalignment, worn components, or impending failures. Analysing vibration data enables maintenance personnel to schedule corrective actions and prevent major breakdowns.
Providing adequate training and expertise to maintenance personnel is crucial. They should be trained in inspecting, maintaining, and troubleshooting gears, drives, and motors. Continuous professional development programs and access to technical resources enhance their knowledge and skills, facilitating effective maintenance practices.
Developing a proactive replacement strategy based on the anticipated lifespan of gears, drives, and motors is important. Monitoring their performance and condition regularly enables scheduling replacements before they reach the end of their operational life. This approach prevents unexpected failures and minimises costly downtime.
Maintaining detailed records of maintenance activities, inspections, repairs, and component history is essential. This documentation provides valuable insights into the performance, maintenance requirements, and lifespan of gears, drives, and motors. It helps identify recurring issues, analyse trends, and make informed decisions regarding maintenance and replacement strategies.
By implementing these maintenance practices, cement plants can extend the lifetime of gears, drives, and motors. Regular inspections, proper lubrication, alignment, cleaning, temperature monitoring, vibration analysis, training, proactive replacements and comprehensive record-keeping contribute to their optimal performance, reliability and longevity.
IMPACT OF TECHNOLOGY ON MOTOR WORKINGS
Gears, drives and motors manufacturers are embracing digitalisation and leveraging technology to enhance their products and provide better solutions to customers. One significant area of advancement is in digital design and simulation. Manufacturers are utilising advanced computer-aided design (CAD) software and simulation tools to create highly optimised gears, drives, and motors. These tools allow for precise modeling and analysis, enabling manufacturers to test various configurations, evaluate performance, and identify potential issues before physical prototypes are produced. This digital design process significantly improves efficiency, reduces development time and enhances product quality.
Another key aspect of digitalisation is performance monitoring and analytics. By integrating sensors and monitoring systems into gears, drives, and motors, manufacturers can collect real-time data on operating conditions, performance parameters, and health status. This data is then processed and analysed using data analytics techniques, enabling predictive maintenance, performance optimisation, and early fault detection. Manufacturers can provide smarter products that offer valuable insights to customers, leading to increased reliability, reduced downtime and improved operations.
Connectivity and remote monitoring capabilities are also being incorporated into gears, drives, and motors. By integrating with Industrial Internet of Things (IIoT) platforms, manufacturers enable remote diagnostics, condition monitoring, and performance optimisation. Customers can access real-time data, receive alerts, and remotely manage their equipment, resulting in improved efficiency, reduced maintenance costs, and enhanced productivity. This connectivity enhances the overall functionality and value of the products.
“The cement industry has also been emphasising on digitalisation and ABB has been a front runner in developing ways and means to do things better. We now have the option of getting every drive functioning in an industry connected remotely to our remote monitoring centres, which enable 24×7 watch on the critical performance parameters of the drives and proactively advise the plant engineers for taking preventive actions if any negative trend is shown on any critical parameters,” says Anoop Anand, Motion System Drives Division President, ABB India.
“The challenge has always been that it was not economically viable to extend monitoring to a much greater scope of equipment across a plant. That has now changed with the introduction of a new generation of wireless smart sensors for motors. The availability of cloud computing, data analytics, and mobile data transmission, has paved the way for the arrival of low-cost, IoT-based wireless sensors. With no hard wiring requirements, they allow for permanent monitoring at a fraction of the cost of traditional condition monitoring systems,” he adds.
Digitalisation is also being used to improve energy efficiency and sustainability. Manufacturers develop intelligent control algorithms and energy management systems that enhance the operation of gears, drives, and motors, thereby reducing energy consumption and environmental impact. Digital technologies enable the integration of renewable energy sources and energy recovery systems, further enhancing the sustainability of these products and supporting the industry’s efforts towards a greener future.
“We believe in offering efficient and futuristic technology to customers. Globally, we have stopped offering IE1 and IE2 class motors and offer more energy efficient IE3 and IE4 motors and soon IE5 efficiency motors will be available in a complete product range. As the world is adapting to Industry 4.0, hence, we have made our products suitable for new edge technology and we can get all kinds of data like temperature, speed, vibration, bearing life etc., from our product, process through our drives and store on the cloud for periodic analysis sitting at remote locations. This will be useful for the maintenance team to keep their machinery operative and avert breakdowns with proper and accurate feedback in advance,” says Amit Deokule, Director- Sales & Marketing, Nord.
Manufacturers are also developing collaborative platforms and digital services to enhance customer engagement and support. These platforms provide access to technical documentation, manuals, and online support, facilitating efficient communication between manufacturers and customers. Digital services such as remote technical assistance, spare parts ordering and performance optimisation consulting further enhance customer support and provide value-added services.
By embracing digitalisation and leveraging technology, gears, drives, and motors manufacturers are advancing product design, performance monitoring, connectivity, energy efficiency and customer support. These innovations result in more intelligent, reliable, and sustainable products that meet the evolving needs of customers in various industries. The integration of digitalisation and technology is transforming the industry and paving the way for more efficient and innovative solutions in the future.
CONCLUSION
Gears, drives, and motors play crucial roles in cement plants in India. They facilitate the movement and control of heavy machinery, such as crushers, kilns and mills, enabling efficient cement production. By using advanced technology and digitalisation, manufacturers are enhancing the design, performance and sustainability of these components.
Digital design and simulation improve their functionality, while performance monitoring and analytics enable predictive maintenance and fault detection. Connectivity and remote monitoring capabilities allow for real-time data access and control, leading to improved efficiency and reduced downtime.
Energy efficiency and sustainability are prioritised through intelligent control algorithms and the integration of renewable energy sources. Augmented reality and virtual reality support product design, training, and maintenance. Collaborative platforms and digital services enhance customer support and engagement. Overall, the integration of digitalisation and technology in gears, drives and motors drives innovation, improves efficiency and delivers smarter and more sustainable solutions for the cement industry.
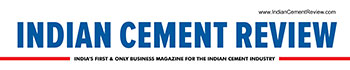
Concrete
Star Cement launches ‘Star Smart Building Solutions’
Published
4 weeks agoon
June 17, 2025By
admin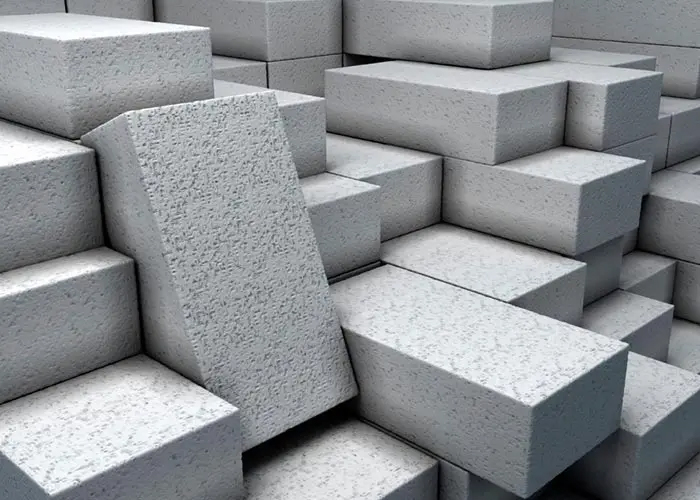
Star Cement has launched ‘Star Smart Building Solutions,’ a new initiative aimed at promoting sustainable construction practices, as per a recent news report. This venture introduces a range of eco-friendly products, including tile adhesives, tile cleaners and grouts, designed to enhance durability and reduce environmental impact. The company plans to expand this portfolio with additional value-added products in the near future. By focusing on sustainable materials and innovative building solutions, Star Cement aims to contribute to environmentally responsible construction and meet the evolving needs of modern infrastructure development.
Image source:https://www.starcement.co.in/
Concrete
Nuvoco Vistas reports record quarterly EBITDA
Published
4 weeks agoon
June 17, 2025By
admin
Nuvoco Vistas reported its highest-ever quarterly consolidated EBITDA of Rs.556 crore in Q4 FY25, with annual EBITDA at Rs.1,391 crore. Cement sales reached 19.4 MMT in FY25, with Q4 contributing 5.7 MMT. Revenue rose 4 per cent YoY to Rs.3,042 crore in Q4. Net debt reduced by Rs.390 crore to Rs.3,640 crore. The company received NCLT approval for acquiring Vadraj Cement, targeting 31 MMTPA capacity by FY27. Key marketing initiatives, expanding RMX and MBM businesses, and a focus on sustainability (457 kg CO2/tonne) drove performance. Nuvoco remains focused on premiumisation, operational efficiency, and market expansion.
Image source:nuvoco.com
Concrete
UltraTech Cement increases capacity by 1.4Mt/yr
Published
4 weeks agoon
June 17, 2025By
admin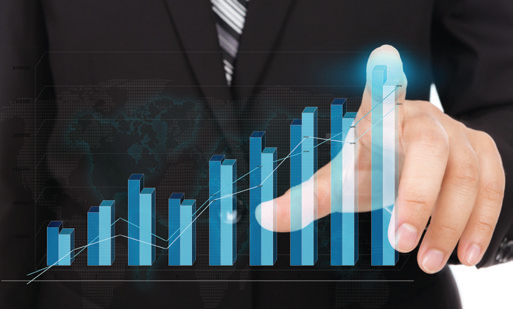
UltraTech Cement has expanded its production capacity by 1.4 million tonnes per annum (Mt/yr) through a combination of debottlenecking efforts and operational efficiency upgrades across several of its plants. The enhancements include an addition of 0.6Mt/yr in grinding capacity at the Nagpur facility in Maharashtra and a combined 0.8Mt/yr at the Panipat and Jhajjar units in Haryana. With these upgrades, the company’s total domestic grey cement capacity has risen to 184.8Mt/yr, while its global capacity now stands at 190.2Mt/yr.

Hindalco Buys US Speciality Alumina Firm for $125 Million

Star Cement launches ‘Star Smart Building Solutions’

Nuvoco Vistas reports record quarterly EBITDA

UltraTech Cement increases capacity by 1.4Mt/yr

Shree Cement reports 2025 financial year results

Hindalco Buys US Speciality Alumina Firm for $125 Million

Star Cement launches ‘Star Smart Building Solutions’

Nuvoco Vistas reports record quarterly EBITDA

UltraTech Cement increases capacity by 1.4Mt/yr
