Economy & Market
Innovation, customer support and cost optimisation are the keys to success
Published
4 years agoon
By
admin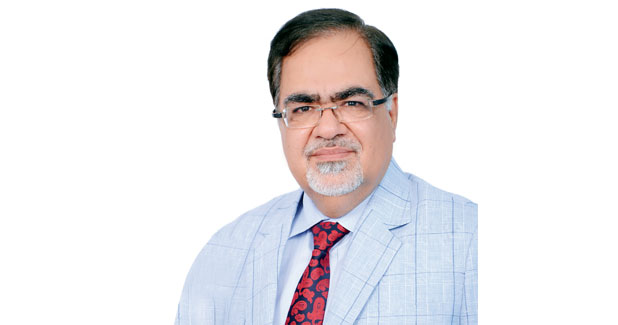
Ashok Dembla President & Managing Director, KHD Humboldt Wedag India
With over 155 years of experience in the cement industry, KHD is a global leader in cement plant technology, equipment, and services. Ashok Dembla, President & Managing Director, KHD Humboldt Wedag India speaks on the spectrum of products and aftermarket services that the company offers for the cement industry.
Give us a brief on your organisation?s Indian and worldwide operations….
The year 2016 marks KHD?s 160th anniversary. With over 160 years of experience in the cement industry, KHD Humboldt Wedag is a global leader in cement plant technology and services. The holding company KHD Humboldt Wedag International AG is based in Cologne, Germany. The group has over 750 employees worldwide with customer service centres and sales offices in growing markets like India, China, Turkey and Russia as well as in Europe and USA. Humboldt Wedag India is an important Customer Service Center which serves all of India as well as the SAARC Countries. KHD?s Indian location also provides more and more global support to other Group CSCs.
What are the core competencies of KHD? How is the flow of technology from Germany to India?
KHD Humboldt Wedag offers a wide range of products and aftermarket services for the cement industry and is the leader in energy-efficient and environmentally friendly technology for the grinding and pyro-processing sections of cement plants. In addition to our high-quality product offerings, process engineering and project management are among our core competencies. Humboldt Wedag India was established way back in year 2000. Most of the experts at the time had experience in working with Cimmco Birla Limited, which had a technical collaboration with KHD Humboldt Wedag from 1983-2000. KHD Humboldt Wedag decided to start a wholly-owned Indian subsidiary, Humboldt Wedag Pvt Ltd, which focused especially on the cement plant and machinery area in order to seamlessly continue to serve its prestigious Indian clients (after the closure of Cimmco Birla). Humboldt Wedag India has so far supplied 39 operating pyro-processing plants, 21 raw material grinding systems, 70 cement grinding systems and 22 slag grinding systems to esteemed clients like UltraTech, Dalmia Cement, Shree Cement, JSW Cement, Holcim, KCP Cement, Birla Corp, Penna Cement, and NCL, etc. Humboldt Wedag India has also supplied customers outside of India in countries like Iran, Oman, Nigeria, Jordan and Yemen.
Today Humboldt Wedag India is 285 people strong, who are capable of providing almost all cement plant technology and services. As a competence centre, our German headquarters in Cologne, Germany, provides us with process engineering support and manages the design of the Group?s core products. Critical equipment like our market-leading Roller Press also comes from Germany.
Some of the important plants supplied by Humboldt Wedag India are;
- Rajashree Cement (UTCL) – All four kiln lines, including raw material and cement grinding. The line No 4 is at present operating at 12,000 t/d;
- UTCL Raipur – Kiln No II – presently operating at 12000 t/d;
- UTCL Tadpatri, Kotputli and Aditya Cement (Line II) GCo identical kiln lines, each operating at an average output of 9,500-9,600 t/d;
- Shree Cement – All kiln lines at Ras, Raipur and one kiln line at Beawar and cement grinding units at Beawar Ras, Khushkhera and Bihar;
- JSW Cement – All cement and slag grinding units at Vijaynagar, Nandyal and kiln line at Nandyal.
Give us some idea on the technological innovations carried out by KHD-HW. KHD has been a pioneer in many technologies. To name a few:
I)First 4-stage Preheater Technology – The first plants with 300 t/d capacity and 600 t/d capacity, came in from Humboldt in Andhra Pradesh at the end of the 1960s. These plants have now been upgraded to 3-4 times of their original capacity.
II)Roller Press Technology – First plants again came from Humboldt in Diamond Cement, Rajashree Cement and Vikram Cement, in the year 1986-87, which have now been upgraded.
III)V Separator Technology – This technology came as a boon for energy savings and reliability for semi-finish grinding technology in the year 1995.
IV) Alternative Fuels – Extended PYROCLON? and KHD?s Combustion Chamber came as an excellent technology to use petcoke, city waste and other waste derived fuels.
V)5 & 6 Stage Preheater Technology – The first of these type of plants came on line in India, e.g., Diamond Cement, Vikram Cement and Rajashree Cement, in order to reduce thermal energy consumption.
VI)Latest Generation Grate Coolers – The KHD Grate Cooler got its start at Vikram Cement. Later came the PYROSTEP? Cooler and now PYROFLOOR? cooler.
In addition, there have been many innovations in burner technology, where the original KHD design has become the world standard. We also have a lot of proprietary knowledge in the area of environmentally-friendly technology. We have earned an excellent reputation in the areas of energy efficiency and reliability. In fact our buzzword for technology is Energy, Efficiency and Environment, or the 3Es.
What is your USP?
Humboldt Wedag India plants operate at thermal and electrical energy levels comparable to best in the Indian cement industry. For example, KCP Cement is operating at 45 kWh/tonne (until clinkerisation), UTCL Dharni is operating at 21 kWh/tonne in PPC grinding and JSW Cement is operating at 34 kWh/tonne for slag grinding at Blaine value of 4500. Also Dalmia Belgaum is operating at less than 10 kWh/tonne in raw material grinding. Kiln lines at Rajashree Cement and KCP Cement are operating at thermal energy consumption of 685 Kcal /kg clinker. These energy figures have set the norms in our industry.
You have been appreciated for energy efficient grinding systems coupled with roller presses. Give us some insight….
As already mentioned, our buzzword for technology is Energy, Efficiency and Environment. All KHD grinding circuits follow the 3E concept, for example: With our proven COMFLEX? grinding system, we can use the same energy-efficient configuration for raw material, cement and slag grinding. This process circuit can handle materials with high moisture content, especially in case of slag and raw materials, without the problem of clogging of vent ducts and bucket elevators. Due to its flexibility, customers can also determine exactly the type of cement they want to grind, even in the area of high-blaine cements. In terms of the 3E concept, the advantages are; Energy: The COMFLEX? grinding system consumes less energy compared to other process circuits. The same system works for raw material, clinker and slag grinding. More and more customers are also beginning to use this roller press-based system in the finish-grinding mode and are achieving excellent results with the same quality of cement. However, they consume far less specific power compared to other technologies available at present.
Efficiency: It is proven that our roller press gives more efficiency than other grinding systems. Under normal operation conditions, our studded roller surfaces are maintenance free for a number of years. This gives customers increased reliability and availability in comparison with other grinding systems.
Environment: COMFLEX? grinding plants offer a dust-free circuit with no belt conveyers and a very effective de-dusting concept.
With the cement industry not doing so well right now, many jobs are in cold storage; when do you think the situation will improve?
With an installed capacity of around 400 million tonnes and annual production of 270 million tonnes in 2015-2016, the industry is running at less than 70 per cent utilisation. Future investment plans and policies of the Indian government indicate a continued increase in Indian cement demand. The cement industry is expected to grow at 6-7 per cent in 2016-2017 compared to 1.5-2 per cent last year. To meet government plans on the development of new highways, Smart Cities, affordable housing and other infrastructure, the projected demand for cement in 2019-2020 will exceed 400 million tonnes.
The Indian demand for cement is expected to continue its fast-paced growth and attain an installed capacity of 850 million tonnes per annum by 2030 and 1350 million tonnes by 2050. The industry has made tremendous strides in technology in recent years.
A vast number of jobs being generated today are for incremental improvements in the existing system or retrofitting. What are the limitations of such jobs?
To increase existing production capacity and improve operational efficiency in terms of energy conservation, Humboldt Wedag India offers many solutions like;
- Modification/upgradation of preheater cyclones to improve dust collection efficiency and to reduce pressure steps.
- PYROBOX? for solid fuel (coal/petcoke) firing in calciner.
- Static inlet for clinker cooler and grate plate replacements.
- High-efficiency dynamic classifier for raw meal, cement and slag.
- PYROJET? burner installation for low primary air and low NOx.
- Kiln services, like kiln ovality monitoring and correction, bending stress analysis etc.
- Installation of high-efficiency separators.
- Installation of market-leading roller press technology to increase grinding capacity and reduced power consumption.
Give us some information on Continuous Emission Monitoring System (CEMS) for the cement industry. Where is the Indian cement industry on this subject, compared to other countries in the South-East Asia region and China?
The exit gases from cement kilns are de-dusted in filters or electrostatic precipitators and the dust is normally returned to the process. At present norms exist for dust, TOC, HCl, HF, SOx, NOx Hg, heavy metals and dioxin in India, which are comparable or better as compared to China, Indonesia and the Philippines. The table below shows the comparison; In India, the CEMS system started approximately five-seven years ago for monitoring particulate emissions and subsequently NOx. Policy guidelines were also formulated and released on 10th May 2016 for emission control by the Ministry of Environment. A brief status as compared to China, Indonesia and the Philippines is as follows;
Do you think that the Indian cement industry is ready for continuous monitoring of emissions? What about the old plants?
As mentioned, the Indian government (Ministry of Environment, Forests and Climate Change) released a new notification on 10th May 2016 for control of emissions released from the cement industry. The Indian government is constantly working on policy development and sharing its updates on various platforms during international seminars like the NCB and CII. The momentum indicates that India is ready for continuous monitoring of emissions.
To protect the environment, the emission norms are to be followed for all cement plants in India and continuous emission monitoring systems (CEMS) are to be installed. However, some cement manufactures in India have not yet installed CEMS systems in their cement plants. Cement manufactures, suppliers, consultants and the government need to work together to achieve this objective, i.e., emission control. From the above, it is evident that India has a long way to go in the implementation of CEMS for the cement industry.
What have been your offerings for increasing TSR in the use of alternate fuels?
KHD Humboldt Wedag has expertise in using alternative fuels either in the calciner or in the kiln. We also supply our award-winning combustion chamber for dry municipal waste and other difficult fuels that can be used in our pyro-processing system. In fact, Humboldt Wedag India supplied Vikram Cement a handling and firing system in order to use Jaipur?s city waste. We also delivered a similar system to Jaypee Cement to use Chandigarh?s waste. Among others, UTCL is using a KHD-supplied conveying and firing system for rice husk, shredded tyres, coconut waste and other agricultural wastes.
The Indian cement industry has a huge potential to use alternative fuels in the manufacture of cement and Humboldt Wedag India has the know-how and expertise to help customers with their very individual needs and requirements.
Give us more details about your other businesses….
KHD Humboldt Wedag focuses on cement plants and the related equipment. However, our roller press offers a number of advantages in mineral processing. The KHD Group has provided WEIR Minerals with an exclusive license to sell and manufacture KHD Roller Press Technology. We also cooperate with WEIR on a number of interesting projects, where KHD separator technology is required. With over 10,000 employees, WEIR Minerals has a strong footprint in the global mining industry.
Customer centricity is becoming a focal point for the capital equipment Industry. What is your take on this with specific reference to your India operations?
At KHD Humboldt Wedag, customers always come first. We have Customer Service Centers (CSCs) in India, China, USA and Russia. Our head office in Cologne serves cement operators in Europe, Middle East and Africa. The entire group places an enormous value on customer relationships. We see our customers as partners. They are the ones who give us the first feedback regarding improvements required in our technology and also provide us a platform for testing our innovations. KHD Humboldt Wedag has also implemented the account management concept in various CSCs with the objective of bringing our customers close to various stakeholders in the company. This helps in understanding customer requirements and we align our activities accordingly. Recently we held a customer meet in Goa, where we met and interacted with 88 customers from all over India for two days. The teamwork and feedback that we experienced was nothing short of excellent.
As a key stakeholder, what is your message to the industry?
With the unlimited growth potential in India, it becomes vital that we keep in mind that the natural resources we are using are depleting and to some extent they are nonrenewable too. Effective utilisation of these resources is the key to our sustainability. So it becomes important to look out for the other alternatives to be used as raw material and additives. In parallel, increased use of blended cement also leads to the concepts of co-utilisation. Of course, everything comes with a price, but advancement and success lie in the technological innovations which are effective and cost competitive also. Continual development based on the need from the industry is the direction in which we as cement technology suppliers have to think ahead.
Ashok Dembla is the President & Managing Director of Humboldt Wedag India. He has 35 years of experience in the cement industry and has held senior management positions at Cimmco Birla Limited, Gebr Pfeiffer India, Jaypee Cement and the Beumer Group in India. As Head of Projects at Jaypee Cement, he was responsible for growing capacity from 7 million tonnes to 32 million tonnes. As the Founding-President of KHD?s Indian operations, Dembla was also instrumental in bringing Humboldt Wedag India from five employees in 2001 to its current size of over 280 employees and a market-leading position. With a Bachelor?s Degree in Chemical Engineering from Punjab University, Chandigarh, as well as a Diploma in Management from the All India Management Association, Ashok Dembla has also published more than 40 technical papers in cement magazines on various aspects of cement technology, operating norms, developmental areas, including papers on grinding and pyro-technology.
You may like
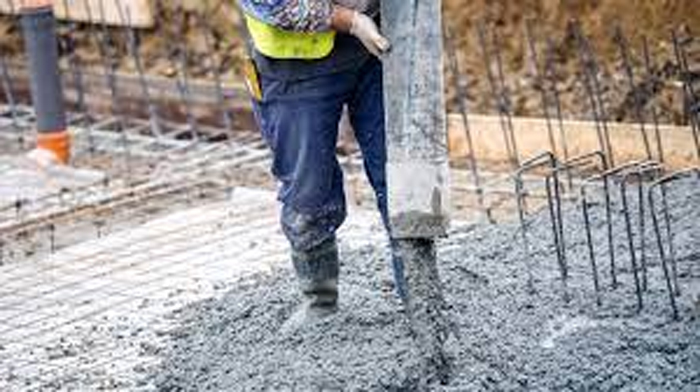
Tamil Nadu is set to host one of India’s five national carbon capture and utilisation (CCU) testbeds, aimed at reducing CO2 emissions in the cement industry as part of the country’s 2070 net-zero goal, as per a news report. The facility will be based at UltraTech Cement’s Reddipalayam plant in Ariyalur, supported by IIT Madras and BITS Pilani. Backed by the Department of Science and Technology (DST), the project will pilot an oxygen-enriched kiln capable of capturing up to two tonnes of CO2 per day for conversion into concrete products. Additional testbeds are planned in Rajasthan, Odisha, and Andhra Pradesh, involving companies like JK Cement and Dalmia Cement. Union Minister Jitendra Singh confirmed that funding approvals are underway, with full implementation expected in 2025.
Image source:https://www.heavyequipmentguide.ca/
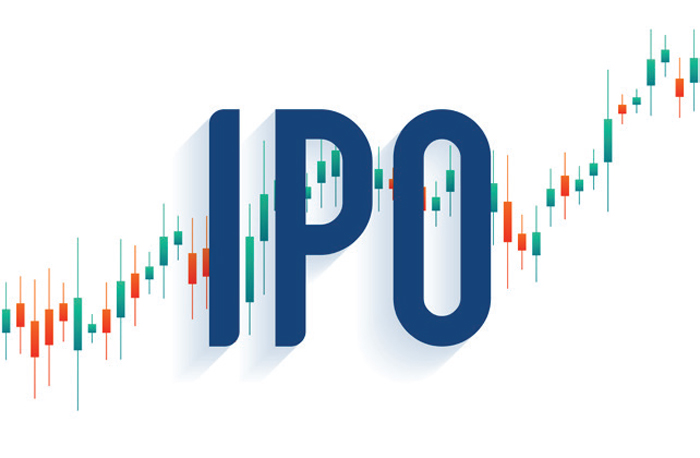
JSW Cement has set the price range for its upcoming initial public offering(IPO) at US$1.58 to US$1.67 per share, aiming to raise approximately US$409 million. As reported in the news, around US$91 million from the proceeds will be directed towards partially financing a new integrated cement plant in Nagaur, Rajasthan. Additionally, the company plans to utilise US$59.2 million to repay or prepay existing debts. The remaining capital will be allocated for general corporate purposes.
Concrete
Cement industry to gain from new infrastructure spending
Published
1 month agoon
July 24, 2025By
admin
As per a news report, Karan Adani, ACC Chair, has said that he expects the cement industry to benefit from the an anticipated US$2.2tn in new public infrastructure spending between 2025 and 2030. In a statement he said that ACC has crossed the 100Mt/yr cement capacity milestone in April 2025, propelling the company to get closer to its ambitious 140Mt/yr target by the 2028 financial year. The company’s capacity corresponds to 15 per cent of an all-India installed capacity of 686Mt/yr.
Image source:https://cementplantsupplier.com/cement-manufacturing/emerging-trends-in-cement-manufacturing-technology/