Environment
Wish list Budget 2013
Published
4 years agoon
By
admin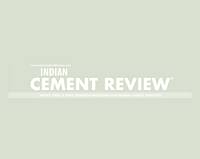
Indian Cement Industry has a total capacity of around 340 million tonne and ranks second in the world, producing quality cement that matches the world’s best and has its footprints in around 30 countries of the world through cement exports. The Working Group on Cement Industry for the XI Five Year Plan (2007-12) had set a target of cement production at 269 mnt and the capacity needed at 298 mnt at the end of the Plan i.e. 2011-12. Against this, the Cement Industry surpassed the target and created an installed capacity of over 340 mnt by the terminal year of the 11th Plan resulting in surplus capacity situation.
Though cement is the most essential infrastructure input, the tax on cement continues to be the highest among the items required for building infrastructure. The levies and taxes on cement in India are far higher compared to those in countries of the Asia Pacific Region. Average tax on cement in the Asia Pacific Region is just 11.4 per cent with the highest levy of 20 per cent being in Sri Lanka.
In this backdrop, the cement industry would like to submit the following suggestions in order to help the industry sustain a healthy growth:
1. Uniform and specific rate of excise duty
Till 28-2-2007, specific rate of excise duty was applicable on cement; and thereafter, up to 28.2.2011 different rates of Excise duty based on Retail Sale Price were levied for cement. However, in the Union Budget 2011-12 the Excise Duty Rates on cement were replaced with composite rates having a 10 per cent ad valorem and specific component of Rs 80 and Rs 160 per tonne, based on Retail Sale Price. In the Union Budget 2012-13 the excise duty on cement increased from 10 to 12 per cent ad valorem whereas specific duty was at Rs.120/- per tonne of cement. Cement has also been notified under Section 4A of the C.E. Act. Accordingly, the value for the purpose of charging duty on packaged cement is determined on the basis of the Retail Sale Price (RSP). Abatement of 30 per cent from the RSP has also been notified. The existing rates of excise duty on cement are as under:
It is clear from the above that the incidence of excise duty on cement is still on the higher side for consumers other than industrial/institutional as an additional specific rate of duty of Rs.120/- per tonne is payable by them. Also the basis of levying Excise Duty is different i.e. 12 per cent on RSP less 30 per cent of RSP (as abatement) and 12 per cent on Transaction Value for sale to industrial/institutional consumers. Thus, the current regime makes for different sets of duties per tonne of cement payable by a producer on any given day.
Excise duty rates on cement are one of the highest and next only to luxury goods such as cars. Other core industries such as coal steel attract duty at around 5 per cent. Cement is one of the core infrastructure industries and it requires large-scale investments and capacity additions in view of the expected GDP growth and projected demand for cement over the medium to long term.
It is well-known that today the industry suffers from excess of surplus capacity of cement in the country and cement market is on bearish trend. Therefore, for growth of cement industry Government may kindly reduce excise duty on cement and clinker.
To encourage cement industry and to bring it at par with other core and infrastructure industries, the excise duty rate be rationalized from 12 per cent to 6-8 per cent and a holistic view may be taken to scrap the specific rate of duty of Rs.120/- per tonne in the interest of common man’s housing needs. Also, the duty structure be simplified to be either on specific rate per MT or on advalorem basis and without relating to MRP etc.
2.Excise Duty on Coal, Lignite, Coke, Fly Ash etc.
In the Budget for the year 2011-12, 1 per cent excise duty was levied on various items including items like coal, lignite, coke, flyash etc which are important for the industry. The aforesaid duty was increased to 2 per cent (except on coal, on which 1 per cent duty continued) in the budget for the year 2012-13. As no Cenvat Credit is available for aforesaid + per cent Excise duty paid, it has increased the cost for the manufacturers. It is also worthwhile to mention that the prices of coal have increased sharply and the industry is already absorbing oClean Energy Cessö levied earlier.
It is suggested that levy of aforesaid duty may be withdrawn or Cenvat credit be made available for the duty paid.
Customs Duty on pet coke, gypsum and other inputs
Cement Industry has been subject to perennial shortages of coal, the main fuel. Approx, only 39 per cent of linked coal is received by the member cos. against their total fuel requirement for kiln under the coal linkage Scheme. This adversely impacts the Cement Industry through increased fuel cost, as the balance requirement of fuel has to be necessarily procured from open market/e-auction, import of coal and use of alternative fuel like Pet coke at a substantially higher rate than linked coal.
In the Union Budget 2012-13, steam coal was fully exempted from the basic custom duty. This provided some much-needed relief to the cement industry on import of coal. However, this relief alone cannot fully meet the fuel shortage for the cement industry. Pet coke is an important material as fuel, which is used in the cement industry. In view of the reducing availability of coal, the cement industry has been resorting to increased usage of pet coke. The indigenous availability of pet coke being short, more and more pet coke is imported to make up shortage of coal.
Gypsum is another important input. Because of the limited availability of indigenous Gypsum, the industry is depends on imports.
Pet-coke and Gypsum attract 2.5 per cent duty, if imported, while there is no import duty on cement import. This leads to an anomaly situation that "Import Duty on inputs is higher than a finished product".
Therefore, it is requested that government may kindly scrap import duty on pet coke, gypsum. Levy of customs duty on imports.
Presently, import of cement into India is freely allowed without having to pay basic customs duty. However, all the major inputs for manufacturing cement such as limestone, gypsum, pet coke, packing bags etc attract customs duty. In this situation duty-free imports cause further hardship to the Indian cement industry apart from the security concerns that are caused by import of cement from Pakistan.
Therefore, it is requested that to provide a level- playing field, basic customs duty be levied on cement imports into India.
Alternatively, Import duties on goods required for manufacture of cement be abolished and freely allowed without levy of duty.
Withdrawal of excise duty on flyash
Excise duty has been levied on fly ash, which is a waste product generated on burning of coal in the boiler of power plant vide notification no. 1/2011 – CE and 2/2011 – CE.
In this regard the decision of the Hon’ble Supreme Court in case of Union of India Vs. Ahmadabad Electricity Co. Ltd., in 2003 (158) ELT 3 (SC) has settled the issue that use of coal as fuel to produce steam resulting in fly ash as a byproduct cannot amount to manufacture.
There is no change in the process generation of fly ash viz. a waste generated on burning coal in the boiler, therefore, the above judgment still holds good & hence fly ash generation should not be treated as manufacture and no Excise Duty on fly ash be levied.
Treatment of waste heat recovery as renewable energy
Energy cost is a very substantial part of the cost of producing cement, as indeed, it is for many other industries. The prices of conventional energy resources are rising higher and higher and further, greater use of these is adversely affecting the environment. Also, various Government are imposing renewable energy obligations on the industry. Looking at all the above, the cement industry has been putting up Waste Heat Recovery plants so as to derive more energy from the same energy resource. In a way, this is akin to green energy. All of this requires further substantial capital investments.
To help the industry in its endeavor to produce more such environment-friendly energy, it is requested that such energy generation be treated as Renewable Energy Source.
Abolition of Import Duty on Tyre Chips
Cement industry is an energy-intensive industry and requires huge amounts of energy resources. However, it does not get adequate supplies of domestic coal and hence has to resort to expensive imported coal.
To meet its requirements, the industry has been developing alternative energy sources like tyre chips etc. However, tyre-chips is presently put under the "negative list" of imports, whereby the same cannot be imported into India. To increase supply of energy sources as well as for conserving the domestic energy sources it is necessary, in the National Interest, that tyre chips be allowed to be imported by removing it from the Negative list and by reducing import duty on the same to ZERO.
Classifying Cement as "Declared Goods"
Cement industry is one of the basic and core infrastructure industries. However, unlike other similar industries/goods, cement is subject to higher rates of taxation. It is requested that Cement be stipulated as "Declared Goods" under Section 14 of Central Sales Tax Act, so that it is put on an equal footing with other core sector goods like coal and steel.
Tax exemption to Certified Emission Reduction (CER) credits under Clean Development Mechanism
The Clean Development Mechanism (CDM) allows industrialised countries to meet their emission reduction commitments under the Kyoto Protocol by purchasing carbon credits from developing countries.
India does not have any carbon emission obligations under Kyoto Protocol. However, Indian enterprises are entitled to earn carbon credits.
As per proviso (ii) to Sec-28(va), any sum received as compensation, from the multilateral fund of Montreal Protocol on substances that deplete the Ozone Layer under United Nations Environment Program, in accordance with the terms of agreement entered into with the Govt. of India, is not taxable.
To motivate the corporate sector for reduction in carbon emission, receipt from CER credit should be exempted from tax.
Exemption to Cement Industry u/s 80-1A
As per provision of Sec. 80-IA(4), deduction is allowed on income derived by any enterprise carrying on the business of (i) developing, or (ii) operating and maintaining or, (iii) developing, operating and maintaining any infrastructure facility.
Since for developing infrastructure facility, cement Industry plays a major role by providing basic material i.e. cement, 80-IA benefit should also be extended to cement Industry.
It is also justifiable for the survival of cement sector which is adversely affected due to increase in cost of production and surplus of capacity as compared to demand, resulting in prices being under pressure.
Exemption to Power Plants U/S 80-IA Power is the critical infrastructure on which the socio-economic development of the country depends. The growth of the economy and its global competitiveness hinges on the availability of reliable and quality power. The demand of power in India is enormous and is growing steadily. India is the world’s sixth largest energy consumer, accounting for about 3.5 per cent of the world’s total annual energy consumption.
In view of the emphasis by Planning Commission to increase the power generation in India, it would be in line with the vision of Planning Commission to continue the exemption to power plants till the demand-supply gap gets bridged.
As per provision of Sec. 80-IA (4) (iv), profit earned by an undertaking which is set-up for generation or generation and distribution of power, if it begins to generate power up to 31st Mar-2012, is exempted.
In view of the scarcity of power & to promote the Power Plants, it is suggested to continue the exemption if the power plants are commissioned by 31st Mar-2015.
Goods & Service Tax (GST)
Central Government is seriously considering introducing GST w.e.f. 1.4.2013. In this regard, the following suggestions may kindly be considered before introduction of the new tax regime:
a) Single Rate of Tax: Central Government has made a proposal to State Government for dual rate under GST which would be brought to single rate over a period of 3 years. However, it is suggested that single rate may kindly be introduced from the first year itself, so that all disputes/litigation towards classification can be avoided from the first year itself.
b) Common Law & enforcement: The Basic purpose behind introduction of GST is simplicity and uniformity of the tax law throughout India. Though the Empowered committee of State Finance Ministers (EC) has agreed to introduce Dual GST with separate Act for SGST to be levied by each state, it may be ensured that there is uniformity in the law to be enacted by various states and process/procedures of different states are similar, as otherwise, the basic purpose behind the introduction of GST would get defeated.
In this regard, it is suggested that any change in the statute of any state, after introduction of GST, be made only with the concurrence of all states.
c) Cenvat/Input tax Credit: Input Tax Credit of tax paid is available under present Excise/Service Tax/VAT laws and the same is presumed to be continued under GST regime. However, this area attracts most of the litigation and hence the criteria/process for availing Input tax credit be simple and unambiguous. To achieve this purpose, the following suggestions are submitted:
i) Input tax credit may be made available for all the inputs and capital goods in or in relation to manufacturing and business activities.
ii) No condition be imposed for availing Input tax credit as long as it relates to the business or industrial activity.
iii) Exclusion (negative list) for availment of Input Tax Credit in respect of items used for or in relation to manufacture be abolished.
iv) 100 per cent input tax credit may be allowed on Capital Goods in the year of purchase itself and conditions like capitalisation/put to use not be imposed.
d) Common dispute resolution mechanism: To reap the full benefit of GST, it is suggested that the mechanism for dispute resolution prescribed may be common throughout all the states.
Concrete
India donates 225t of cement for Myanmar earthquake relief
Published
3 months agoon
June 17, 2025By
admin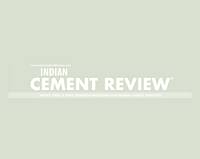
On 23 May 2025, the Indian Navy ship UMS Myitkyina arrived at Thilawa (MITT) port carrying 225 tonnes of cement provided by the Indian government to aid post-earthquake rebuilding efforts in Myanmar. As reported by the Global Light of Myanmar, a formal handover of 4500 50kg cement bags took place that afternoon. The Yangon Region authorities managed the loading of the cement onto trucks for distribution to the earthquake-affected zones.
Concrete
Reclamation of Used Oil for a Greener Future
Published
3 months agoon
June 16, 2025By
admin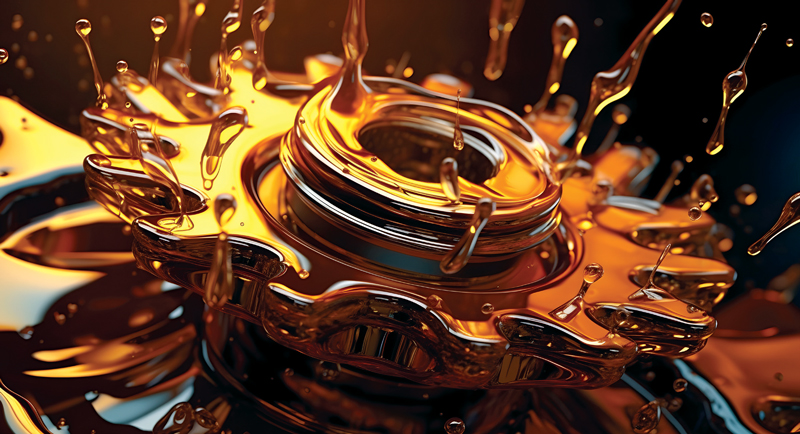
In this insightful article, KB Mathur, Founder and Director, Global Technical Services, explores how reclaiming used lubricants through advanced filtration and on-site testing can drive cost savings, enhance productivity, and support a greener industrial future. Read on to discover how oil regeneration is revolutionising sustainability in cement and core industries.
The core principle of the circular economy is to redefine the life cycle of materials and products. Unlike traditional linear models where waste from industrial production is dumped/discarded into the environment causing immense harm to the environment;the circular model seeks to keep materials literally in continuous circulation. This is achievedthrough processes cycle of reduction, regeneration, validating (testing) and reuse. Product once
validated as fit, this model ensures that products and materials are reintroduced into the production system, minimising waste. The result? Cleaner and greener manufacturing that fosters a more sustainable planet for future generations.
The current landscape of lubricants
Modern lubricants, typically derived from refined hydrocarbons, made from highly refined petroleum base stocks from crude oil. These play a critical role in maintaining the performance of machinery by reducing friction, enabling smooth operation, preventing damage and wear. However, most of these lubricants; derived from finite petroleum resources pose an environmental challenge once used and disposed of. As industries become increasingly conscious of their environmental impact, the paramount importance or focus is shifting towards reducing the carbon footprint and maximising the lifespan of lubricants; not just for environmental reasons but also to optimise operational costs.
During operations, lubricants often lose their efficacy and performance due to contamination and depletion of additives. When these oils reach their rejection limits (as they will now offer poor or bad lubrication) determined through laboratory testing, they are typically discarded contributing to environmental contamination and pollution.
But here lies an opportunity: Used lubricants can be regenerated and recharged, restoring them to their original performance level. This not only mitigates environmental pollution but also supports a circular economy by reducing waste and conserving resources.
Circular economy in lubricants
In the world of industrial machinery, lubricating oils while essential; are often misunderstood in terms of their life cycle. When oils are used in machinery, they don’t simply ‘DIE’. Instead, they become contaminated with moisture (water) and solid contaminants like dust, dirt, and wear debris. These contaminants degrade the oil’s effectiveness but do not render it completely unusable. Used lubricants can be regenerated via advanced filtration processes/systems and recharged with the use of performance enhancing additives hence restoring them. These oils are brought back to ‘As-New’ levels. This new fresher lubricating oil is formulated to carry out its specific job providing heightened lubrication and reliable performance of the assets with a view of improved machine condition. Hence, contributing to not just cost savings but leading to magnified productivity, and diminished environmental stress.
Save oil, save environment
At Global Technical Services (GTS), we specialise in the regeneration of hydraulic oils and gear oils used in plant operations. While we don’t recommend the regeneration of engine oils due to the complexity of contaminants and additives, our process ensures the continued utility of oils in other applications, offering both cost-saving and environmental benefits.
Regeneration process
Our regeneration plant employs state-of-the-art advanced contamination removal systems including fine and depth filters designed to remove dirt, wear particles, sludge, varnish, and water. Once contaminants are removed, the oil undergoes comprehensive testing to assess its physico-chemical properties and contamination levels. The test results indicate the status of the regenerated oil as compared to the fresh oil.
Depending upon the status the oil is further supplemented with high performance additives to bring it back to the desired specifications, under the guidance of an experienced lubrication technologist.
Contamination Removal ? Testing ? Additive Addition
(to be determined after testing in oil test laboratory)
The steps involved in this process are as follows:
1. Contamination removal: Using advanced filtration techniques to remove contaminants.
2. Testing: Assessing the oil’s properties to determine if it meets the required performance standards.
3. Additive addition: Based on testing results, performance-enhancing additives are added to restore the oil’s original characteristics.
On-site oil testing laboratories
The used oil from the machine passes through 5th generation fine filtration to be reclaimed as ‘New Oil’ and fit to use as per stringent industry standards.
To effectively implement circular economy principles in oil reclamation from used oil, establishing an on-site oil testing laboratory is crucial at any large plants or sites. Scientific testing methods ensure that regenerated oil meets the specifications required for optimal machine performance, making it suitable for reuse as ‘New Oil’ (within specified tolerances). Hence, it can be reused safely by reintroducing it in the machines.
The key parameters to be tested for regenerated hydraulic, gear and transmission oils (except Engine oils) include both physical and chemical characteristics of the lubricant:
- Kinematic Viscosity
- Flash Point
- Total Acid Number
- Moisture / Water Content
- Oil Cleanliness
- Elemental Analysis (Particulates, Additives and Contaminants)
- Insoluble
The presence of an on-site laboratory is essential for making quick decisions; ensuring that test reports are available within 36 to 48 hours and this prevents potential mechanical issues/ failures from arising due to poor lubrication. This symbiotic and cyclic process helps not only reduce waste and conserve oil, but also contributes in achieving cost savings and playing a big role in green economy.
Conclusion
The future of industrial operations depends on sustainability, and reclaiming used lubricating oils plays a critical role in this transformation. Through 5th Generation Filtration processes, lubricants can be regenerated and restored to their original levels, contributing to both environmental preservation and economic efficiency.
What would happen if we didn’t recycle our lubricants? Let’s review the quadruple impacts as mentioned below:
1. Oil Conservation and Environmental Impact: Used lubricating oils after usage are normally burnt or sold to a vendor which can be misused leading to pollution. Regenerating oils rather than discarding prevents unnecessary waste and reduces the environmental footprint of the industry. It helps save invaluable resources, aligning with the principles of sustainability and the circular economy. All lubricating oils (except engine oils) can be regenerated and brought to the level of ‘As New Oils’.
2. Cost Reduction Impact: By extending the life of lubricants, industries can significantly cut down on operating costs associated with frequent oil changes, leading to considerable savings over time. Lubricating oils are expensive and saving of lubricants by the process of regeneration will overall be a game changer and highly economical to the core industries.
3. Timely Decisions Impact: Having an oil testing laboratory at site is of prime importance for getting test reports within 36 to 48 hours enabling quick decisions in critical matters that may
lead to complete shutdown of the invaluable asset/equipment.
4. Green Economy Impact: Oil Regeneration is a fundamental part of the green economy. Supporting industries in their efforts to reduce waste, conserve resources, and minimise pollution is ‘The Need of Our Times’.
About the author:
KB Mathur, Founder & Director, Global Technical Services, is a seasoned mechanical engineer with 56 years of experience in India’s oil industry and industrial reliability. He pioneered ‘Total Lubrication Management’ and has been serving the mining and cement sectors since 1999.
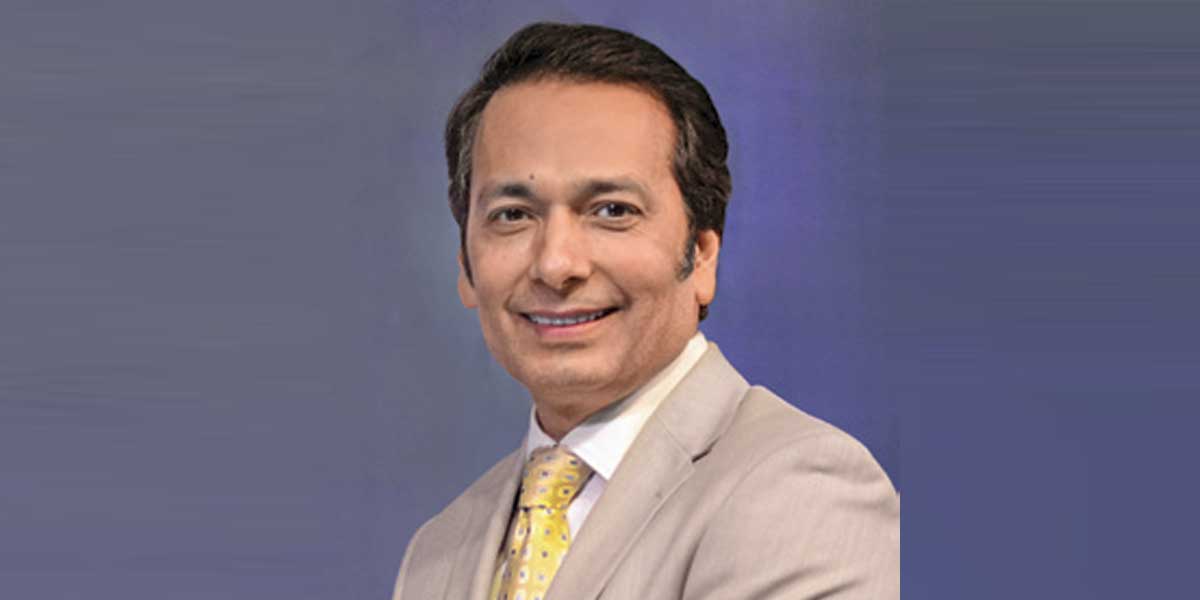
The Indian cement industry has reached a critical juncture in its sustainability journey. In a landmark move, the Ministry of Environment, Forest and Climate Change has, for the first time, announced greenhouse gas (GHG) emission intensity reduction targets for 282 entities, including 186 cement plants, under the Carbon Credit Trading Scheme, 2023. These targets, to be enforced starting FY2025-26, are aligned with India’s overarching ambition of achieving net zero emissions by 2070.
Cement manufacturing is intrinsically carbon-intensive, contributing to around 7 per cent of global GHG emissions, or approximately 3.8 billion tonnes annually. In India, the sector is responsible for 6 per cent of total emissions, underscoring its critical role in national climate mitigation strategies. This regulatory push, though long overdue, marks a significant shift towards accountability and structured decarbonisation.
However, the path to a greener cement sector is fraught with challenges—economic viability, regulatory ambiguity, and technical limitations continue to hinder the widespread adoption of sustainable alternatives. A major gap lies in the lack of a clear, India-specific definition for ‘green cement’, which is essential to establish standards and drive industry-wide transformation.
Despite these hurdles, the industry holds immense potential to emerge as a climate champion. Studies estimate that through targeted decarbonisation strategies—ranging from clinker substitution and alternative fuels to carbon capture and innovative product development—the sector could reduce emissions by 400 to 500 million metric tonnes by 2030.
Collaborations between key stakeholders and industry-wide awareness initiatives (such as Earth Day) are already fostering momentum. The responsibility now lies with producers, regulators and technology providers to fast-track innovation and investment.
The time to act is now. A sustainable cement industry is not only possible—it is imperative.