Process
ACC strives to minimise its carbon footprint by turning all its operations green
Published
4 years agoon
By
admin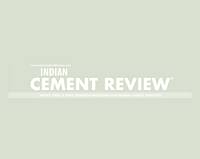
K N Rao, ACC, Director (Energy & Environment)
ACC perceives water conservation, water harvesting, energy efficiency, environment protection, CO2 reduction, optimisation of the use of natural resources and fossil fuels, preservation of biodiversity, safety as some of the most important pillars of operation, to be pursued very seriously for the survival of the business, says K N Rao ACC, Director (Energy & Environment). Excerpts from the interview.
How do you look at the sustainability issues in the cement industry?
Being one of India’s oldest and most responsible cement manufacturers, sustainability has become an integral part of ACC’s business model. The triple bottomline concept is embedded into our decision- making process to make the business more sustainable. ACC has witnessed 76 glorious years of the Indian cement industry’s journey and withstood various challenges in that time. This is a clear indicator of ACC’s sustainable business practices, which has helped it to withstand rough weather and grow strong, day by day.
Could you throw some light on the initiatives ACC has taken to reduceCO2?
Since 2006, ACC has been monitoring its CO2 emissions. Scope-I emissions from its cement manufacturing activities are monitored using the CSI-WBCSD protocol. Scope-II and III emissions are monitored using the GHG protocol.
Over and above, ACC has taken various steps for reduction of the levels of CO2emissions, such as:
- Moving from wet / semi-wet process to dry process cement manufacturing.
- Reduction of electrical and thermal energy by adopting energy-efficient technologies and products.
- Enhanced use of alternative fuels.
- Reduction of clinker factor and clinker usage in cement manufacturing.
- Enhanced use of alternative raw materials.
- Enhanced use of renewable energy.
- Pursuing waste heat recovery systems.
- Increasing renewable energy portfolio to reduce the use of fossil fuel- based electrical energy.
- Increased usage of rail networks for bulk transport of cement.
- Research on increased use of pozzolona during the manufacture of blended cements (PPC / PSC).
- Green building design.
We have been authorised to use the CDP leadership logo in recognition of our continued leadership in CDP.
How do you assess the RPO regulations’ impact?
The manufacturing process at ACC has been significantly impacted by RPO regulations. Most of the integrated plants are operating with a captive power plant to achieve energy security. In anticipation of the Renewable Purchase Obligations, ACC installed 19 MW of windmills in the states of Tamil Nadu, Rajasthan and Maharashtra to meet its RPO obligations; we have also earned renewable energy certificates in the process. While our long- term objective is to have sources of renewable energy for all plants, as a short-term measure, ACC has purchased Renewable Energy Certificates to meet RPO requirements.
What is ACC’s goal on sustainability and what are the challenges it faces?
Our major objectives are to bring down CO2 intensity considerably, become water positive and biodiversity positive, reduce the use of natural raw materials and fossil fuels and ensure no harm is done to the environment. Many challenges lie ahead of us, especially when it comes to energy. With the currency depreciation, fuel costs are spiralling, thus raising the cost of thermal power generation. Quality coal and its availability, availability of quality raw materials like limestone, continues to be a concern. What’s more, power shortages have compelled us to set up captive power plants (CPP) to fulfil our energy needs.
Then, there is the increased pressure of complying with mandatory energy regulations such as Perform, Achieve, Trade (PAT), where we must meet energy reduction targets as well as our renewable energy purchase (RPO) obligations. These provide both challenges and opportunities to make units green and self- sustainable in terms of power. Also, the continuous reduction in SEC, has, to some extent, helped mitigate the rising cost of electricity generation.
One of our units in Himachal Pradesh will be commissioning a waste heat recovery- based power generating unit of 7.5 MW capacity shortly. We are also planning similar units in other plants in a phased manner.
ACC is on track as per our stated goals. However, progress was not upto the mark in the renewable energy portfolio. This was due to recent changes in the government’s fiscal policy with respect to wind energy, and the economic crisis. ACC is trying hard to increase the renewable energy portfolio in the coming days. A lot of investment has been made in improving energy efficiency by the installation of variable speed drives (VSDs). Capacity for water conservation and harvesting is increasing day by day across all ACC plants.
Could you brief us on the initiatives on the AFR front?
The main benefit of co-processing eventually reaches the people or society, as it is instrumental in solving local waste management problems. AFR utilisation helps in regional job creation, waste collection and in pre-treatment facilities, helps in saving public funds which otherwise would have been spent on building additional incinerators; here, the infrastructure (cement kilns) is already in place.
Additionally, through initiatives like HAAT (Heap, Acquire and Transport) and the sourcing of biomass from communities, ACC has ensured that biomass (used as an alternative fuel) procurement activities are designed around the agricultural practices of the local community. Only locally available biomass residues from traditional crops which are over and above the needs of the community are procured directly from the community. This initiative goes a long way towards supporting local priorities and making a positive social and economic difference to the local community.
Co-processing ranks higher on the waste disposal hierarchy and eliminates the need for landfills and incineration. ACC undertakes waste management only after the options to Reduce- Reuse- Recycle are exhausted and avoids the evils of resource destruction by way of incineration and containment by way of landfills.
AFR utilisation also helps in saving precious raw materials and fuels, thereby reducing the environmental impact of extraction (mining or quarrying), transporting and processing of raw materials. Disposal of waste through co-processing as AFR leaves no residue since the incombustible, inorganic content of the waste materials are incorporated into the clinker matrix. AFR utilisation reduces GHG emissions, which are expelled if waste is incinerated and traditional fuels are used in the cement production process.
Through these initiatives, ACC has tried to address and provide an environmentally and socially acceptable solution for industrial hazardous and non-hazardous waste, along with municipal sorted solid waste, thus ensuring a cleaner and greener tomorrow.
How green is ACC’s operative processes?
ACC’s product portfolio has approximately 90 per cent of blended cements which comprise both Pozzolona Portland Cement (PPC) and Pozzolona Slag Cement (PSC). PPC cement absorbs fly ash (waste from thermal base power plants) and PSC absorbs slag (waste from steel cement plants) in the cement manufacturing process. Some initiatives adopted by ACC to make its operations green are listed below:
- Reduction of natural raw material used (limesstone). This leads to the reduction of CO2 emissions on account of calcinations.
- Conservation of fossil fuels.
- Absorption of industrial wastes, which otherwise pose a huge environmental problem.
- Utilisation of alternative fuels and raw materials. This not only conserves fossil fuels and natural raw materials but also leads to the reduction of CO2 emissions.
- Migrating to bulk transportation modes like using high capacity vehicles, use of railways lead to reduction in the Scope-III type of CO2emissions.
- Enhancement of renewable portfolio to reduce Scope-II CO2 emissions.
- Adoption of latest techniques during blasting process, like NONEL.
- Transportation of limestone from mines to plant through closed conveyors.
- Installation of state- of-the- art pollution control equipment to minimise emissions.
- Utilisation of waste heat to reheat incoming material.
- Closed water cooling circuit.
What do you think of the PAT scheme?
Ten plants of ACC (nine integrated plants and the Tikaria grinding unit) have been identified as DCs under PAT. Though PAT poses a significant challenge to capex investments, we see opportunities in long term growth. To make the most of it, our twin focus should be on improving efficiencies across the industry and reducing the use of thermal and electrical energy in the manufacturing process by generating and using renewable energy. Opportunities abound when it comes to energy efficiency. One can consider upgrading old plants, co-processing industrial and municipal waste in cement kilns, generating power from the waste heat in kilns, using waste from other industries like fly ash and slag in the manufacturing process. Besides this, improving the efficiency of CPP and making a paradigm shift to blended and composite cements to minimise CO2 emissions, are vital to the cement manufacturing process.
Brief us on the pollution control equipment in your plants.
ACC is continuously adopting the latest technologies in the area of air pollution control. For their cement kilns, ACC converted all the Electrostatic Precipitators (ESPs) into bag filters and consequently, reduced the usage of water for gas cooling while maintaining constant emissions irrespective of process changes. Similarly, regarding power plants, ESPs are being converted into hybrid filters. Bag filters have been installed in all the remaining areas. These initiatives have led to us achieving stack emissions of <30mg/Nm3 in most of the stacks, as against the statutory regulation of 50mg/Nm3.
In 2011, ACC set up a project at Gagal to generate power through waste heat recovery. Could you tell us something about it?
At Gagal, the WHR plant absorbs heat from its two kilns and two coolers. The expected energy generation potential from this initiative is approximately 7.5 MW.
One of ACC’s plants was recently given a Greenco rating. Will ACC be replicating the move in other plants, too?
ACC’s Thondebavi cement works is a grinding unit near Bangalore, and is the youngest family member of ACC. This plant has been awarded the Greenco Silver rating at the recently concluded Green Cementech-13th conference held at Hyderabad. The plant has made remarkable progress in the areas of energy and water conservation. Yes, ACC is aggressively pursuing the participation of other plants with this rating system.
What are the major challenges you face in making ACC completely green?
Considering the nature of the cement manufacturing process, the usage of limestone as raw material, the amount of the energy required, the amount of logistics involved, it is practically impossible to make cement manufacturing process totally green. However, ACC is trying its best to drive its operations towards a green manufacturing process by adopting various measures such as enhanced utilisation of alternative raw materials, enhanced utilisation of alternative fossil fuels, reduction of clinker factor, reduction of thermal energy both at kiln and CPP, migration towards bulk and rail transportation, enhancing the renewable energy portfolio, etc.
Where does the company see itself five years down the line?
ACC will continue to increase its efforts in the areas indicated above. This will, in turn, give benefits to the organisation such as reduction of carbon intensity, specific water consumption, specific thermal energy, specific electrical energy, improvement in environmental performance and conservation of raw materials, etc.
Energy Efficiency
Installation of variable frequency drives for both LV as well as HV drives.
Thermal imaging of kiln and pre- heaters to identify major thermal loss areas and subsequently their rectification.
Carrying out CFD studies on major process equipment.
Installation of a rota scale in the kiln coal dosing system. Creation of an energy conserving organisation .
Conducting regular energy audit for identification and implementation of energy saving opportunities.
Increasing the PRI (Production Rate Index), OEE and MTBF of all critical plant equipment.
Replacement of inefficient pumps, motors, fans and compressors with high efficiency equipment in some plants.
Replacement of pneumatic conveying with the energy- efficient mechanical conveying system.
Operational improvements like arresting of leakages, optimisation of mills, fans, compressors, interlocking of auxiliaries to avoid idle runs, improving the power factor, etc.
Green Challenges
Ever-increasing cost of fossil fuels. Unfavourable waste legislation.
Issues related to the availability of segregated waste.
Issues related to consistent quality and quantity AF availability. Trans- boundary movement of alternative fuels.
Pricing of alternative fuels. Increased demand for OPC.
Lack of standards for composite cements.
Lack of economically viable and proven technologies for utilising huge deposits of pond /dump ash.
Inadequate infrastructure to granulate all blast furnace slag generated.
Long distance between sourcing of Pozzolonic materials (for manufacturing blended cements) and cement plants and issues related to logistics. Exorbitant pricing of blending material.
Long payback and lack of financial incentives, making it difficult for aggressive exploration of the WHRS option.
Lack of robust new technologies.
Huge requirement of financial resources.
You may like
-
Double Tap to Go Green
-
15th Cement EXPO to be held in March 2025 in Hyderabad
-
14th Cement EXPO
-
Vinita Singhania receives Lifetime Achievement Award at the 7th Indian Cement Review Awards
-
Increasing Use of Supplementary Cementitious Materials
-
Indian Cement Review Touts Decarbonisation Mantra & Awards Growth
Process
Price hikes, drop in input costs help cement industry to post positive margins: Care Ratings
Published
4 years agoon
October 21, 2021By
admin
Region-wise,the southern region comprises 35% of the total cement capacity, followed by thenorthern, eastern, western and central region comprising 20%, 18%, 14% and 13%of the capacity, respectively.
The cement industry is expected to post positive margins on decent price hikes over the months, falling raw material prices and marked drop in overall production costs, said an analysis of Care Ratings.
Wholesale and retail prices of cement have increased 11.9% and 12.4%, respectively, in the current financial year. As whole prices have remained elevated in most of the markets in the months of FY20, against the corresponding period of the previous year.
Similarly, electricity and fuel cost have declined 11.9% during 9M FY20 due to drop in crude oil prices. Logistics costs, the biggest cost for cement industry, has also dropped 7.7% (selling and distribution) as the Railways extended the benefit of exemption from busy season surcharge. Moreover, the cost of raw materials, too, declined 5.1% given the price of limestone had fallen 11.3% in the same aforementioned period, the analysis said.
According to Care Ratings, though the overall sales revenue has increased only 1.3%, against 16% growth in the year-ago period, the overall expenditure has declined 3.2% which has benefited the industry largely given the moderation in sales.
Even though FY20 has been subdued in terms of production and demand, the fall in cost of production has still supported the cement industry by clocking in positive margins, the rating agency said.
Cement demand is closely linked to the overall economic growth, particularly the housing and infrastructure sector. The cement sector will be seeing a sharp growth in volumes mainly due to increasing demand from affordable housing and other government infrastructure projects like roads, metros, airports, irrigation.
The government’s newly introduced National Infrastructure Pipeline (NIP), with its target of becoming a $5-trillion economy by 2025, is a detailed road map focused on economic revival through infrastructure development.
The NIP covers a gamut of sectors; rural and urban infrastructure and entails investments of Rs.102 lakh crore to be undertaken by the central government, state governments and the private sector. Of the total projects of the NIP, 42% are under implementation while 19% are under development, 31% are at the conceptual stage and 8% are yet to be classified.
The sectors that will be of focus will be roads, railways, power (renewable and conventional), irrigation and urban infrastructure. These sectors together account for 79% of the proposed investments in six years to 2025. Given the government’s thrust on infrastructure creation, it is likely to benefit the cement industry going forward.
Similarly, the Pradhan Mantri Awaas Yojana, aimed at providing affordable housing, will be a strong driver to lift cement demand. Prices have started correcting Q4 FY20 onwards due to revival in demand of the commodity, the agency said in its analysis.
Industry’s sales revenue has grown at a CAGR of 7.3% during FY15-19 but has grown only 1.3% in the current financial year. Tepid demand throughout the country in the first half of the year has led to the contraction of sales revenue. Fall in the total expenditure of cement firms had aided in improving the operating profit and net profit margins of the industry (OPM was 15.2 during 9M FY19 and NPM was 3.1 during 9M FY19). Interest coverage ratio, too, has improved on an overall basis (ICR was 3.3 during 9M FY19).
According to Cement Manufacturers Association, India accounts for over 8% of the overall global installed capacity. Region-wise, the southern region comprises 35% of the total cement capacity, followed by the northern, eastern, western and central region comprising 20%, 18%, 14% and 13% of the capacity, respectively.
Installed capacity of domestic cement makers has increased at a CAGR of 4.9% during FY16-20. Manufacturers have been able to maintain a capacity utilisation rate above 65% in the past quinquennium. In the current financial year due to the prolonged rains in many parts of the country, the capacity utilisation rate has fallen from 70% during FY19 to 66% currently (YTD).
Source:moneycontrol.com
Process
Wonder Cement shows journey of cement with new campaign
Published
4 years agoon
October 21, 2021By
admin
The campaign also marks Wonder Cement being the first ever cement brand to enter the world of IGTV…
ETBrandEquity
Cement manufacturing company Wonder Cement, has announced the launch of a digital campaign ‘Har Raah Mein Wonder Hai’. The campaign has been designed specifically to run on platforms such as Instagram, Facebook and YouTube.
#HarRaahMeinWonderHai is a one-minute video, designed and conceptualised by its digital media partner Triature Digital Marketing and Technologies Pvt Ltd. The entire journey of the cement brand from leaving the factory, going through various weather conditions and witnessing the beauty of nature and wonders through the way until it reaches the destination i.e., to the consumer is very intriguing and the brand has tried to showcase the same with the film.
Sanjay Joshi, executive director, Wonder Cement, said, "Cement as a product poses a unique marketing challenge. Most consumers will build their homes once and therefore buy cement once in a lifetime. It is critical for a cement company to connect with their consumers emotionally. As a part of our communication strategy, it is our endeavor to reach out to a large audience of this country through digital. Wonder Cement always a pioneer in digital, with the launch of our IGTV campaign #HarRahMeinWonderHai, is the first brand in the cement category to venture into this space. Through this campaign, we have captured the emotional journey of a cement bag through its own perspective and depicted what it takes to lay the foundation of one’s dreams and turn them into reality."
The story begins with a family performing the bhoomi poojan of their new plot. It is the place where they are investing their life-long earnings; and planning to build a dream house for the family and children. The family believes in the tradition of having a ‘perfect shuruaat’ (perfect beginning) for their future dream house. The video later highlights the process of construction and in sequence it is emphasising the value of ‘Perfect Shuruaat’ through the eyes of a cement bag.
Tarun Singh Chauhan, management advisor and brand consultant, Wonder Cement, said, "Our objective with this campaign was to show that the cement produced at the Wonder Cement plant speaks for itself, its quality, trust and most of all perfection. The only way this was possible was to take the perspective of a cement bag and showing its journey of perfection from beginning till the end."
According to the company, the campaign also marks Wonder Cement being the first ever cement brand to enter the world of IGTV. No other brand in this category has created content specific to the platform.
Process
In spite of company’s optimism, demand weakness in cement is seen in the 4% y-o-y drop in sales volume. (Reuters)
Published
4 years agoon
October 21, 2021By
admin
Cost cuts and better realizations save? the ?day ?for ?UltraTech Cement, Updated: 27 Jan 2020, Vatsala Kamat from Live Mint
Lower cost of energy and logistics helped Ebitda per tonne rise by about 29% in Q3
Premiumization of acquired brands, synergistic?operations hold promise for future profit growth Topics
UltraTech Cement
India’s largest cement producer UltraTech Cement Ltd turned out a bittersweet show in the December quarter. A sharp drop in fuel costs and higher realizations helped drive profit growth. But the inherent demand weakness was evident in the sales volumes drop during the quarter.
Better realizations during the December quarter, in spite of the 4% year-on-year volume decline, minimized the pain. Net stand-alone revenue fell by 2.6% to ?9,981.8 crore.
But as pointed out earlier, lower costs on most fronts helped profitability. The chart alongside shows the sharp drop in energy costs led by lower petcoke prices, lower fuel consumption and higher use of green power. Logistics costs, too, fell due to lower railway freight charges and synergies from the acquired assets. These savings helped offset the increase in raw material costs.
The upshot: Q3 Ebitda (earnings before interest, tax, depreciation and amortization) of about ?990 per tonne was 29% higher from a year ago. The jump in profit on a per tonne basis was more or less along expected lines, given the increase in realizations. "Besides, the reduction in net debt by about ?2,000 crore is a key positive," said Binod Modi, analyst at Reliance Securities Ltd.
Graphic by Santosh Sharma/Mint
What also impressed analysts is the nimble-footed integration of the recently merged cement assets of Nathdwara and Century, which was a concern on the Street.
Kunal Shah, analyst (institutional equities) at Yes Securities (India) Ltd, said: "The company has proved its ability of asset integration. Century’s cement assets were ramped up to 79% capacity utilization in December, even as they operated Nathdwara generating an Ebitda of ?1,500 per tonne."
Looks like the demand weakness mirrored in weak sales during the quarter was masked by the deft integration and synergies derived from these acquired assets. This drove UltraTech’s stock up by 2.6% to ?4,643 after the Q3 results were declared on Friday.
Brand transition from Century to UltraTech, which is 55% complete, is likely to touch 80% by September 2020. A report by Jefferies India Pvt. Ltd highlights that the Ebitda per tonne for premium brands is about ?5-10 higher per bag than the average (A cement bag weighs 50kg). Of course, with competition increasing in the arena, it remains to be seen how brand premiumization in the cement industry will pan out. UltraTech Cement scores well among peers here.
However, there are road bumps ahead for the cement sector and for UltraTech. Falling gross domestic product growth, fiscal slippages and lower budgetary allocation to infrastructure sector are making industry houses jittery on growth. Although UltraTech’s management is confident that cement demand is looking up, sustainability and pricing power remains a worry for the near term.