Concrete
Cement grinding capacity expansion
Published
4 years agoon
By
admin
Split location of a plant is an accepted concept. It is an easy route to add capacities where market exists. Shreekant Datar, who has wide experience of handling projects in multinational companies, shares details of one such case.
ABC Cement is a 10-year old cement manufacturing company. The plant started with a clinkering capacity of 1 MTPA, i.e., around 3,000 MT per day. Over the years, as the demand for cement grew, the plant has undertaken upgradation work in phases every year, and after all debottlenecking, the plant has stabilised with a clinker production capacity of 4,000 MT per day. This amounts to an excess clinker availability of 1,000 MT per day. All other plant capacities have reached their peak levels and finding a proper time for maintenance of equipment to ensure availability, has become a problem for the management. The management is forced to curtail the production to avoid overproduction of clinker as storage is a big limitation. The top management team has been mulling over an idea of investing some capital to enhance the capacities as market is growing at 8 to 10 per cent per annum. The management also thinks that this expansion will help in:
-
retaining their market share as other players in the region are trying to take a slice of market, and
-
maintaining cost effectiveness and competitiveness.
The existing cement plant has no space for expansion and management has thought to put up a plant away from clinkering unit. Questions that arose was, ??here do we put up this unit?? Since it required a thorough study before taking any further decision and a project team was made and they were given the task of formulating this plant project. The team consisted of personnel from technical, financial, legal and marketing department. The technical person heading it was the most senior and had back up experience of installing a project.
How did the project team work?
They prepared a project charter which was somewhat like this:
-
Objective: To enhance cement grinding capacity and liquidate 1000 MT of excess clinker
-
Project steps
-
Find a suitable location
-
List down all the necessary statutory requirements of government to be filled in.
Hire a consultant to understand and arrive at the overall requirements of project like technology selection, working out area requirements, capital cost involved, operating costs, logistics cost and finally the financial feasibility
Two teams were formed in which one worked on technical proposal and second on the location and market perspective.
Main equipment
Technical concept
The proposed plant should be a grinding unit with packing facility. It should be for making blended cement like fly ash based PPC or slag-based cement. Clinker to be handled by road by trucks. The cement despatch to be handled by road. The control systems shall be PLC/DCS based and remote control, with lowest manpower is possible.
The technology available for grinding is:
-
Closed circuit ball mill system
-
A vertical roller mill system
-
A combined roller press and ball mill system
Required capacity is 1,550 TPD or 5.11 LTPA. (0.5 million TPA). After a lot of deliberation with consultant and internal team, it was decided to adopt a 75 TPH roll press + ball mill system technology. The advantages seen with this were a good and consistent surface (Blaine) generation, which the market valued and flexibility to use either fly ash or other additives in future.
Plant layout: In line process equipment and storage with provision for similar second line
Total plant area required: About 20 acres
Overall timeframe for project
1. Land procurement ??six months
2. Statutory approvals ??10 months after land procurement
3. Engineering ??three months after statutory approval
4. Procurement and delivery ??eight months after first critical order
5. Detailed engineering and construction ??eight months after two months of critical equipment ordering
6. Commissioning ??one month
Total ??30 months from start of land procurement. It was noted that this can be shortened by about six months if land procurement is expedited and some engineering work is done before necessary statutory clearances are obtained.
Location finalisation
To begin with, a brainstorming was carried out and it was zeroed on following characteristics:
1) The location should be close to our market place
2) The location should be within 500 km distance from main plant
3) Should have land availability at a reasonable price
4) Should have infrastructure like roads, railway, electricity source, water source, a reasonably big town for housing the operating personnel
5) Availability of trucks for final product transfer
6) The location should be close to an additives source
Considering the above factors, a land parcel of 22 acres was available close to a power plant and clinkering unit. This was a private agricultural land.
Land procurement
The land team verified following land characteristics
1. There are no man settlements or natural waterbodies with in arial radius of 2.0 km
2. The nearest highway is within 5 km of location
3. The railway station is with in 10 km
4. Airport is within 100 km
5. Electrical substation for power sourcing is within 5 km range
6. Water source(borewell) is available in the finalised land
7. An inhabitable township is within 30 to 50 km radius. This would help in housing the families of staff working in the area.
8. The political situation and people?? attitude towards Industry was assessed
9. The land parcels have no encumbrances and are free of any litigation. All the documents of the land lineage for 20 years were checked. Wherever mutations were pending they were done quickly with the help of Gram Panchayat and Tehsil office.
The team did a wonderful job of developing good relationship with influential and in power people and manged to procure land with reasonable price and applied for conversion of agricultural land to non-agricultural category with local district authorities. After winning confidence of local Gram Panchayat officials and the influential persons in the area, NA was obtained with in six months, i.e. a saving of four months in execution time.
Statutory clearances
The following were essential ones for starting the project
1. Register project with the district Industrial Development Corporation
2. Apply for environmental clearance from MOEF (essential for clinker grinding)
3. Engage environmental consultants to establish the TOR and furnish for EC
4. Meetings were held with the concerned officials and EC was obtained six months period
5. Application was made to State pollution control board and consent to establish a plant was obtained in three months. Hence a saving of one more month in execution.
6. Application was made to Electricity Board for getting power connection. All clearances were available and the liaison team developed good relationships. The board agreed to provide connection with in six months. They also agreed to provide construction power from a nearby agricultural line.
7. Other local clearances like those from Gram Panchayat were obtained along with above activities.
8. Further clearances necessary like factories inspectorate, electrical inspectorate, town planning, etc. were listed, scheduled and completed very religiously
Procurement and Engineering
Tenders were prepared with the help of engineering consultants and floated to prospective vendors in a month after obtaining the consent to establish with efforts by engineering team. Important conditions in the tender were:
-
The battery limits for supply, engineering deliverable were very critically set to ensure that there are no grey areas and miss outs
-
The core equipment load data and GA drawings will be furnished within two months
-
Complete system engineering and layout with in battery limit to be done by suppliers
-
The engineering data furnishing and deliveries were fully aligned with project execution requirements and payment terms were purely based on these outputs.
-
Separate tender committee was formed under existing purchase department and equipment ordering was done quickly in three months??time from getting the Consent to Establish from pollution control board.
-
In due course, contracts were made and agencies for execution of civil, mechanical and E&I work were released after some engineering outputs were received.
Project management
-
A core team of six persons (project manager, planner, process engineering, mechanical engineering, drawing and design and E&I engineering)
-
Review of drawings was made by sitting together by above team as a conference and a quick review and progress of drawings was made possible.
-
Whole project execution plan was made using project planning software like MS project and monitored closely by above team. Alarms were incorporated in way of Flags and milestones. This would act as an early warning system for both time and cost matters.
-
Regular visits were undertaken to debottleneck and expedite consultant?? drawing output.
-
The floor areas of multi-storeyed building were critically examined and areas were optimised, which lead to a saving 5 per cent cost of such buildings in normal course
-
All statutory requirements of factories Inspectorate with respect to safety,
Site management
-
A team of dedicated engineers with experience in construction work as well as operation was made and placed at site under an able project leader who had a record of executing five such projects
-
The team made following arrangements before moving to site:
1. Locate a good hotel and make arrangements for stay
2. A local conveyance agency engaged for necessary vehicles
3. Doctors were identified
4. Good houses were identified for staff to stay
5. A bachelor?? accommodation with mess was tied up to begin with
6. Container offices were arranged for site work
7. Genset agency was hired for site power
8. Internet facility was tied up with a service provider
-
The team made SOP?? for ensuring timely and correct inputs to contractor?? to ensure deliverance of a good quality in defined time limits based on their past experience and following are some of the important matters they incorporated.
1. Strict discipline to be followed to ensure only latest drawing is issued and used at site by exercising control to withdraw old drawings and stamp them as superseded. Give a regular communication to contractors and engineers as soon as a new version has been received. In some projects new drawings have been issued after construction was done which lead to serious re-working.
2. The area cleaning and grading was done based on the contour survey to optimise excavation and fillings. The plant lay out was suitably adjusted to ensure water flow out in natural slope direction. Slightly hilly area was not erased but some structures requiring elevation, like in case of clinker unloading tippler was placed there. Plant roads were laid and worked up to WBM level to ensure easy movement of vehicles during execution of project. Temporary drains were created to ensure no water logging during rains. Cross over pipes were laid in pre-defined way to ensure passage of cables during the construction.
3. The foundation designs were reviewed and corrected, based on the strata actually observed during excavations. This helped in reducing depths of certain structures like clinker silos
4. Areas for storage of equipment, steel fabrication, contractor?? office were so planned and established so that there is least interference in peak project period. It also helped in keeping project site neat and clean.
5. Discipline was inculcated to remove dirt and scrap on daily/weekly basis
6. Labour colonies were constructed using ready made structures and allocated to contractors for their labour housing just outside the plant area. Water and electricity arrangements were made but limits on consumption were laid and recovery made from contractors. This helped in reducing labour turnover in holidays and keep them in a healthy spirit.
7. Strict adherence to QAP?? for all construction activities and front release for next work was done very religiously to ensure smooth continuity and reduce re-working and time loss to minimum.
8. Payments were done to contractor on the bases of % work completed against plan and not only on random quantities presented. This was based on microplanning on weekly basis with contractors and regular monitoring to keep the project on course as desired.
9. Monthly meetings with contractor?? project head from their main offices were held at site and problems were troubleshot to achieve the rate of progress and be on the defined time course.
Commissioning
-
The operations team was inducted about four months before the commissioning so that hey get familiarised with the plan, documentation and also were encouraged to come out with suggestion for convenience and unhindered operability.
-
The pre-commissioning checklists were prepared by the commissioning team and religiously implemented to ensure a plant run at: ONE GO
-
After the team worked so hard and dedication the plant got commissioned and went on production stream with in four weeks of commissioning. Least problems were faced due strict quality adherence at each stage and extensive pre-commissioning checks.
-
In this period, consent to operate was applied for with Pollution Control Board and same was obtained in time to declare commercial production.
Hence it can be concluded that with a great team, planning and dedication, it was possible to complete half a MTPA capcity cement grinding unit in 26 months from the idea was frozen by top management team. Some of the points enumerated above may be of use to some one planning a project and I am sure; it can be improved further. There is always a scope for improvement.
Shreekant Datar
ABOUT THE AUTHOR:
Shreekant Datar is a mechanical engineer with 37 years experience in the cement industry. Out of which, he has 20 plus years experience in projects with organisations like ACC, UltraTech Cement and Indiabulls. He has international exposure of projects in Nigeria in the capacity as project management consultant. Presently, he is a freelance consultant on cement projects. He can be reached at: datarsv12@gmail.com.
You may like
-
Branding Concrete with Virtual and Augmented Reality
-
LafargeHolcim launches industrial automation plan
-
Ambuja Cement scouts for buys in RMX to fuel growth
-
Construction sector shows degrowth for the past 3 years
-
China´s ministry investigates excessive cement capacity in north-east China
-
Vincent Leboucher is new president of HGH Group
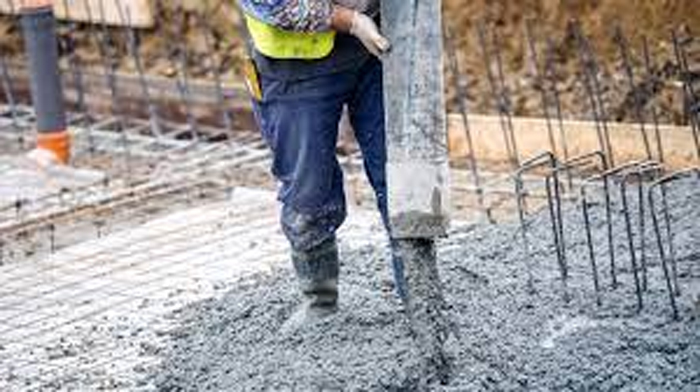
Tamil Nadu is set to host one of India’s five national carbon capture and utilisation (CCU) testbeds, aimed at reducing CO2 emissions in the cement industry as part of the country’s 2070 net-zero goal, as per a news report. The facility will be based at UltraTech Cement’s Reddipalayam plant in Ariyalur, supported by IIT Madras and BITS Pilani. Backed by the Department of Science and Technology (DST), the project will pilot an oxygen-enriched kiln capable of capturing up to two tonnes of CO2 per day for conversion into concrete products. Additional testbeds are planned in Rajasthan, Odisha, and Andhra Pradesh, involving companies like JK Cement and Dalmia Cement. Union Minister Jitendra Singh confirmed that funding approvals are underway, with full implementation expected in 2025.
Image source:https://www.heavyequipmentguide.ca/
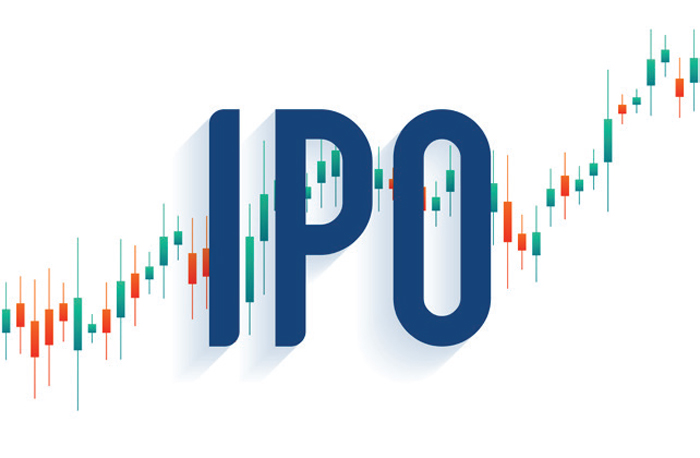
JSW Cement has set the price range for its upcoming initial public offering(IPO) at US$1.58 to US$1.67 per share, aiming to raise approximately US$409 million. As reported in the news, around US$91 million from the proceeds will be directed towards partially financing a new integrated cement plant in Nagaur, Rajasthan. Additionally, the company plans to utilise US$59.2 million to repay or prepay existing debts. The remaining capital will be allocated for general corporate purposes.
Concrete
Cement industry to gain from new infrastructure spending
Published
1 month agoon
July 24, 2025By
admin
As per a news report, Karan Adani, ACC Chair, has said that he expects the cement industry to benefit from the an anticipated US$2.2tn in new public infrastructure spending between 2025 and 2030. In a statement he said that ACC has crossed the 100Mt/yr cement capacity milestone in April 2025, propelling the company to get closer to its ambitious 140Mt/yr target by the 2028 financial year. The company’s capacity corresponds to 15 per cent of an all-India installed capacity of 686Mt/yr.
Image source:https://cementplantsupplier.com/cement-manufacturing/emerging-trends-in-cement-manufacturing-technology/