Technology
Environmentally Sustainable Mining Practices In India
Published
6 years agoon
By
admin
Sustainability has assumed considerable importance in developed countries which are extensively involved in mining practices, like Australia, Canada, USA, South Africa and Papua New Guinea etc. They take comprehensive view of sustainable development in mining which includes important dimensions such as local stakeholder engagement, socio-economic development in mining project areas and transparency in communication with the stakeholders, along with environment. These developed nations undertake mining activities with all compliances to regulatory requirements and environmental laws leads to lessen the impact of mining and strictly implement it. These compliances include provisions for mine closure and associated reclamation and rehabilitation of mined land.
In India, major mining companies have taken steps for socio-economic development projects in their mining areas. The Indian mineral industry comprises of large and small mines that are covered under public, private and informal sectors, covering most minerals being extracted. The public sector continues to play a dominant role in production of various major minerals (like coal, lignite, petroleum, iron and steel, bauxite and aluminium) where as a large number of small mines (including quarries for extracting minor minerals) operated by private players in most states. These present difficult challenges for sustainable development as their financial, technical and managerial limitations restrict their ability to take effective corrective measures against the negative impacts of mining.
Major mining companies uses advanced technology, adopt comprehensive environment protection measures, sensitise their personnel on sustainability issues and progressively try to improve their environmental performance. There are other large, medium and even small companies whose environment obligation consists in strictly conforming to the prescribed legal provisions. Major threats for adopting sustainable mining practices are illegal workings, where legal compliances are not observed to the fullest extent. It is reported that the illegal mining of sand is largely responsible for the environmental degradation especially the river beds of all major rivers including Ganga and Jamuna. There are only little checks for controlling illegal and rampant mining, whereas the political interference has turned the situation grim. Even legal mines flout norms and damage the environment considerably.
Concerns for environmentally sustainable mining
Today, the sustainable mining is the key to the security of raw materials and energy for many countries in the world. The sustainable development of mining of mineral resources is a major concern for today’s global world, addressed to mining companies, people of science associated with mining and many other institutions and organisations. Public awareness that the mineral resources are non-renewable assets, is, unfortunately, small and therefore improvements or changes to the situation in this area is another key concerns, it should be followed by concrete actions.
Modern mining, which is considered for negatively affecting the environment, and also causes discomfort for people living in mining areas or their immediate surroundings, must have the public acceptance for its activities. Thus, the real concern about the environment is becoming an important factor for obtaining such public acceptance. Mining in the twenty-first century, while striving for sustainable development, must provide employees with a safe working environment, therefore the problems regarding safety, due to its complexity, is a major challenge for mine operators. The trend of increasing the depth of mines, observed in the world, means that work safety is, and will continue to be a key area of concern for the sustainable development of the mining industry.
The complexity of the problems for the sustainable development of mining and the resulting diversity on a global scale point at the need for the continuous exchange of experience in the field of knowledge, methods, technologies and other solutions. They should provide a sustainable and socially acceptable development and continued operation of mining, invariably needed by people, to provide necessary mineral resources.
Objectives and Effects of sustainable mining practices –
There are several objectives of sustainable mining practices, which are interrelated and success will involve the issues most frequently linked to another. They can be summarised as follows:
Implementation of Sustainable Mining Practices –
Two major methods of implementing sustainable mining practices are – 1) Good governance from Global, Central & State Government bodies resulting in effective laws and regulations for implementation –
Every now and then, the various Government bodies, judiciary systems of India has shown their concerns over bad mining practices and not following sustainable approach. Also efforts are being made by them to implement these mining practices for betterment for eco-system.
At global level, the heads of 193 UN member states prepared a set of 17 Sustainable Development Goals (SDGs), which is for global development framework available for the society and generations. Mining companies have the potential to become leading partners in achieving the SDGs. Through their direct operations, mining companies can generate profits, employment, and economic growth in low-income countries. And through partnerships with government and civil society, they can ensure that benefits of mining extend beyond the life of the mine itself, so that the mining industry has a positive impact on the natural environment, climate change, and social capital.
At the same time, mining companies will be called on to extract with responsibility, produce with less waste, use safer processes, incorporate new sustainable technologies, promote the improved wellbeing of local communities, curb emissions, and improve environmental stewardship. Mining companies committed to the SDGs will benefit from improved relationships with governments and communities and better access to financial resources; those that fail to engage meaningfully with the SDGs will put their operations at risk in the short and long term.
Based on interviews with over 60 global experts from industry, civil society, governments, academia, and financial institutions, the report identifies where sustainable mining practices can enhance the positive impacts it has and mitigate the negative impacts across the 17 SDGs (see figure below).
A Planning Commission report from 2012 titled "Sustainable Development, Emerging issues in India’s mineral sector" observed that in the mineral-rich states of Odisha, Goa, Karnataka and Jharkhand, mining has brought about economic development. At the same time, it has caused significant environmental damages and negatively impacted communities in project areas. To that extent the mining and environmental laws and regulations have not been very effective.
As per the report published by NITI Ayog in 2017 on "Socio Economic Impact Study of Mining and Mining Polices on the Livelihoods of Local Population" has mentioned that mining is considered as one of the necessary evils of the modern world, which provides the materials required to sustain quality of life. While improving the quality of life and giving an impetus to economic development, it has also brought in its wake, a notable impact on the environment as well as socio-economic conditions of local people (Vagholikar and Moghe, 2003).The proposed mining areas and activities have been severely criticized by environmentalists and social activists, on the subjects of potential loss of forests and displacement of villages as the mines increase in number and size of operations. Insufficient attention to managing impacts on the environment and the socio-economic fabric observed in the past, has reflected adversely on public support for reform and private investment needed for accelerating growth in the state.
The most important environmental requirement for a mining project is a comprehensive environment assessment (EIA) programme, which was started in 1994. However, laws and regulatory instruments work unsatisfactorily due to weak enforcement and inadequate coordination among government agencies. Although mining companies tend to meet the legal requirement of preparing a mine closure plan, the implementation falls short. Local communities are not consulted in the preparation and implementation of mine closure plans.
The New Mineral Policy, 2019 has also been focused on main theme of mining being environmentally sustainable, we are going to explore those very efforts, which will answer the very question, and could mining activities ever become environmentally sustainable for both environment and our health?
The answer is, it very much possible to make mining more environmentally sustainable, there are few practices being followed across international mines, which can be implemented at Indian Mines to minimise environment pollution. All we have to do is to develop and integrate these practices that reduce environmental effects resulting from mining operations. Sustainable mining practices is basically mining practices that meets the present demand without compromising the future generation’s needs. In the process, the advent of new mining methods, tools, regulation and legislation, significant efforts are helpful to make mining more environmentally friendly.
2) Self-regulating mining enterprises which are economically viable, financially profitable and technically efficient i.e. innovative mining practices and use of technologies –
There are prime responsibility of mining companies towards the implementation of the principles of sustainability for mining. It has applications for all stages of the mine life cycle, i.e., starting from exploration, mine planning, development, mineral extraction to mine closure, post-closure reclamation and rehabilitation. These principles include elements such as intra and inter-generational equity, the precautionary principle, scientific mining, management of environmental and socio-economic impacts, creation of substitute capital in the form of social and physical infrastructure and most importantly stakeholder engagement..
In some cases, mining operations have been executed without concerning for the "carrying capacity"of the environment and other infrastructural limitations of the surroundings of the mine site. This has put unavoidable pressure on the environment and caused inconvenience to the people living alongside mining areas. Illegal mining in many cases has similar effect while additionally causing loss of public revenues. The mineral extraction and processing release several toxic materials, contaminating the soil and water which leads to deforestation and ground water degradation. Mineral extraction has also disproportionately affected health of forest ecosystems and the surrounding environment and furthermore the tribes as well as the forest dwelling populations are also adversely affected. However, the mining and mineral sectors are perceived to have failed to alleviate poverty for these vulnerable populations around the forest areas. Thus, the impacts of mining and mines upon natural ecosystems, biodiversity and tribal livelihoods have become a key environmental concern and source of conflict and socioeconomic tension.
Most of work done by mining industry to protect environment and address social concerns has not been received due attention of the Government, media and society. In spite of the fact that, their efforts of sustainable mining practices and operations, few NGOs and environmental protection agencies tries to malign all efforts based on stray incidents. With increasing stringent guidelines by the Governments to regulate mining and its impact, the mining industry has been relentlessly striving for not only achieving expectation of regulatory agencies, but also to exceed these and set international benchmarks. Mining companies are striving hard to contribute towards sustainable development of the country
To make mining environmentally friendly, few steps are suggested below, they are in regular discussion on various forums around the world. In India, mining companies can adopt these steps to achieve the goals of New Mineral Policy: –
Reclaimingof Materials used in worked out Mines and properly closing of the area-
This step involves usage of material from the old worked out mines, which affects the environment in a variety of ways, especially in its natural decaying, rotting and eroding processes, withal it can also lead to illegal or unregulated mining activity. This specially occurs in underground mines where support systems, cables, pipes etc, are left out with significant amount of ore, it decays and pollutes environment in a serious way. However, when these areas are adequately excavated, mining companies would find some materials that could be reused productively. In Opencast also, several waste materials like cables, pipes, etc, are left as is post mining and it is buried in mine overburden materials.
Every mining company has to research on these unused resources and materials throughout the mining process, to try and conserve its current "non-renewable" materials. Each company can form small decommissioning groups which study systems and the complete mining processing facilities and plants; this process will allow the pipelines to be drained, equipment and parts of the mine to be cleaned and sold off, the buildings can be repurposed or demolished, warehouse materials recovered and wasted disposed of. These groups then clean and sell off any remaining operational equipment and provided they are still structurally sound, repurpose the premises.
The main objective in reclaiming process is to return the site and the land which surrounds it back to reusable standards, ensuring that any landforms and structures are stable, and the watercourses need to be evaluated in order to regain water quality within the affected area.
This step needs the effective supervision during the process of mining and closure, its successful impacts on the environment could well be diluted through the re-use of materials that would have previously been left to decay.
Closing illegal and unregulated mines
In India, we find several illegal and unregulated mine which is operational. The New Mineral Policy 2019 has tried to curb these types of illegal mine workings. In context with enforcing regulations and maintaining steadfast legislation regarding the behaviour and processes of the mines,strict and swift closing of illegal or unregulated mining activity will set an environmental precedent within the industry.
For example, before 2010, most mines in China were completely unregulated which were affecting surrounding areas gravely. Details are mentioned in coming pages of this article, where effective steps taken by Chinese Government has helped in reducing the damage and provide a sustainable mining areas. Effective closing and reclamation of old mined out areas will significantly help in sustainable mining practices in and around the mineralised belts.
Accurate measurements and declaration of waste mining which creates pollution –
Mining companies always try to save face when it comes to the environmental conservation and try to hide the facts of actual pollution and maintain secrecy in reporting the toxic mining wastes produced by mining operations. These companies usually keep the public in the dark giving an accurate report of what’s being dumped into the environment and the various by not pollutants created by them.
New mineral Policy instructs to frame rules to recognise the actual pollution generated by mining companies; accordingly, a suitable step shall be taken to panelise these companies or to reduce pollution as much as possible, with suitable remedial measures to be suggested. Of course, strict penalties for violating companies have to be decided by State and Central Governments.
Use reusable waste to build and reuse/recycle of material –
At present ubiquitous, mining companies are discovering efficient ways to capitalize wholly on materials in order to provide sustainable goods and services. On the other hand, the society at large, wants to utilise less wood, metal, stone, plastic and other materials by adopting efficient practices.
One simple way is to start using reusable materials effectively while building new constructions and infrastructure affecting the surrounding environment of any mining. Recycling the metals from accumulated scrap and waste in landfills may be in some cases more economical than to mine ore deposits. For example, in 2008, the world steel industry produced over 1.3 billion tonnes of steel. It used 1.48 billion tons of raw materials, or 470 million tonnes less than, would have been needed to make the same volume of steel in the 1970s. Concerning aluminium, it is estimated that since 1880, approximately 900 million tons of aluminium were produced of which nearly 75% is still in use today. The demand for aluminium continues to skyrocket and recycling aluminium saves more than 90% of the energy required to producing new metal, thus rendering recycling very attractive. This scales down the amount of wasteful use on public and private level. Accordingly, mining companies can start use of durable goods that can be easily re-usable, re-manufactured, or recycled, undertaking environmentally sustainable practices will reduce its inimical impact. There are success stories in these re-usable material applications.
This creative and increasing trend of scrap mining, or utilizing ever-reusable resource for other mining initiatives, saves from the environmental hazards. It is necessary to find out each and every detail of each piece which is being used and generated in a mining site, which will help the mining industry to take suitable steps towards re-use, for becoming a more sustainable industry. For similar examples, we can use recycling of copper waste, which takes seven times less energy than processing of copper ore, and recycling steel which uses three-and-a-half times less energy than processing of iron ore. These small steps will help us immensely in determining not only the longevity of a sustainable mining practices and also have its positive environmental impact.
This article has been reproduced from CEMENT, ENERGY AND ENVIRONMENT, a Bi-Annual journal of Cement Manufacturers Association of India in its July-Dec’2019 Issue. Part II of the same will be published in the next month.
About the author – "Author BHANU PRAKASH BHATNAGAR is B.E. Mining Engg. (Gold Medal), FCC, MBA, working as Head Mining, Adani Cementation Ltd, Ahmedabad. He is having more than 27 years" experience in Overall Mine management including Acquisition of mineral resources through Auction Process, New Mine Development, Production Planning, Mine Operations and Quality Management for Large Opencast Limestone Mines. He had previously worked with cement companies like ACC-Holcim, Reliance Cement Ltd and overseas mining experience."
Part I
Come up with better regulations and legislation
As observed by the Honourable Supreme Court in its judgement on mining in 2017, the present mining legislation that we have today is far from being effective or productive. Mining continues to affect the environment because companies never cease to take advantage and continue polluting environment by waste discharges. Regulation obviously differs from country to country, with some countries more advanced in terms of their legislation than others. However, the need for improvement is always there in this industry, which inevitably causes some environmental damage.
We have to learn a lot from other countries like, for example In Canada, where mines like the Island Copper Mine on Vancouver Island stands as a highly regulated mine site that is operational from 1971 to 1995 when it was closed for resource depletion.
It was forced by regulatory agencies and control of the government that a detailed mine closure plan was developed to comfortably close the mine in order to protect the few resources which remained, and the Mine enacted the contaminated sites regulation process which was awarded the Certificate of Conditional Compliance.
This step involves the effective framing of the mineral policy and as we found that the new Mineral Policy 2019 advocates for the stringent laws for environmentally sustainable mining practices.
Effective implementation of this policy will not only protect environmental and public health, but also improve the lifespan of the mining industry and provide sustainable mining. The new Mineral Policy elaborates that extraction of mineral impacts other natural resources like land, water, air and forest. It is necessary to take a comprehensive view to facilitate the choice or order of land use keeping in view of the needs of development as well as needs of protecting the forests, environment and ecology and to conserve biodiversity of areas to be mined.
Responsible and Regulated mining near surrounding habitations of Silver Mine at Peru.
The New Mineral Policy has also emphasised on the effective Mine Closure where once the resources in mine are completely exhausted there is need for scientific mine closure which will not only restore ecology and regenerate bio-diversity but also take into account the socio-economic aspects of such closure. Government has a role in ensuring that post production mine decommissioning and land reclamation are an integral part of mine development process. Consistent approaches are adopted for efficient and effective mine reclamation and rehabilitation.
Investing in Research and Development of Environmentally sustainable Mining Technology –
Mining industry is always in need of proper research and development in order to make sure the industry is ready for today’s ever-changing commitment to sustainability and turning the world into a more "environmentally sustainable" place.
New Mineral Policy has emphasised on "Scientific Methods of Mining" which state that the mine development and mineral conservation, as governed by the Rules and Regulations, will be on sound scientific basis, with the regulatory agencies like IBM and State Directorates, closely interacting with R&D organisation and scientific and professional bodies. This is to ensure the proper mining practices being followed by mining companies. Policy advocates for R&D effort shall be made to improve efficiency in process, operation and also the recovery of by-products and reduction in specification and consumption norms. R&D efforts shall be directed to find new and alternative uses for minerals whose traditional demand is on the wane.
In this regard, as per the latest News published by NCCBM (NCB News, Sept 2019), the NCCBM has achieved great success with recent research and development with Investigation of standardization of new clinker for blended cement. The objective of the study was to investigate effects of high MgO clinker on performance characteristics of resultant OPC, PPC and PSC. The project was undertaken on accelerated mode and the report to be submitted to BIS is under preparation. The main agenda was to promote utilization of low-grade limestone containing higher MgO with good result. This will certainly result in increase of mine life.
Reduce resources inputs for effective mining practices –
The mining industry consumes large amount of water and land in their operations. One solution to becoming more environmentally sustainable is to reduce the input of the mine. By diverting surface water and pumping groundwater, mines can reduce both the quantity and quality of water available downstream for aquatic ecosystems and other use.
With regard to energy, a mining company can look into alternative energy sources such as solar or wind power. By reducing the energy usage, a mine can reduce greenhouse gases and extend the life of fossil fuel reserves. Mining companies will also be able to reduce the cost to produce the product and thus reduce the cost of the commodity itself. The New Mineral policy advocates for minimising the inputs for mining processes.
Improving the efficiency of mining processes –
This step is very much in discussion globally for closely monitoring the standard mining supply chain, mining industry/companies will be forced to confront ways in which a company can improve its efficiency where its lacking in terms of sustainability and green mining initiatives, improving the efficiency of this process can help trim down environmental impact. This also allows companies to regulate processes which may be inadequate in terms of environmental friendliness.
This needs a proper supervision of the mining and ancillary process that will allow mining companies to change elements/activities that are inefficient or that use too many natural resources. Conducting a material flows analysis will effectively track the physical flows of natural resources through extraction, production, fabrication, use, recycling and final disposal. This will develop new ways of thinking, new metrics, business process re-engineering and new management/supervisory tools that will help cushion the transition into more efficient and less environmental toxic patterns of resource used in modern societies. This process change will allow supervisors to develop new processes that are more efficient and sustainable than previous ones. Across the world, organizations like The World Resources Institute (WRI) are currently conducting research on most frequently used resources and materials, in order to better understand how the industry can conserve its non-renewable materials. The WRI has been working towards developing a database, and can now indicate the flow of materials through industrial economies. Material flows analyses, as mentioned above, will track the physical flows of natural resources in every step of mining process, accounting for both the gains and losses occurring throughout the supply chain.
The New Mineral policy mentions that the use of equipment and machinery which will improve the efficiency, productivity and economics of mining operations as well as mineral beneficiation process, safety, health of persons working in mines/beneficiation plant and surrounding area shall be encouraged.
Re-evaluating Cut-off Grades
A Raw mill cut-off grade is the level set that is considered to be the lowest quality of already mined ore which is economically feasible to continue processing. Different materials have different properties that determine a feasible cut-off grade. Often these grades are set at over-conservative levels. The easiest way to improve efficiency in mining and to reduce waste products is to decrease the mill cut-off grade of the mine. Re-evaluating these grades at each mine will significantly reduce waste.
A lower mill cut-off grade may decrease the quality of the material, but certain final uses of the material do not need a very pure compound. Cut-off grades will be determined on a mine-by-mine basis by looking at the precedents for the material in question and taking the future use of the material into consideration.
For example, the above mentioned recent R&D study done by NCCBM, has very encouraging results in terms of re-evaluating the MgO (Magnesia) content in Limestone for Clinker manufacturing, which earlier assumed to be less than 3.5%. Three types of high MgO clinker samples were obtained and designated as Clinker-1 (MgO~6.2%), Clinker-2 (MgO~6.8%) and Clinker-3 (MgO~7.5%).
PPC & PSC got succeeded in Clinker-1 & Clinker-2 in all respect, while testing with OPC autoclave expansion was observed. The performance results obtained so far are quite encouraging which will pave the way for utilization of low grade limestone containing high MgO, increased mine life (~15 years) besides improved sustainability during cement manufacture. This will also add to the utilisation of waste material of mine, thus leading to sustainable mining practices.
Replenishing the environment
A seemingly simple step, but it is rarely prioritized, replenishing mine sites and mine environment is one of the key factors to not only earning respect and cooperation of those living surrounding the mine site, but it will also ultimately protect the mine’s impact on the environment. Mining companies sometimes overlook the importance of replenishing the environment. This simple act can go a long way towards increasing the environmental sustainability of mining.
It has simple solutions like replenishing native soils and grasses, cleaning excess waste, proper waste removal, site inspections, replanting trees and natural forestry. By restoring the environment around the mine, the mining companies are contributing to positive environmental change, rather than making the environment more difficult to live in. The entire mine reclamation process should combine removal of hazardous materials, reshaping land, restoring topsoil, and planting native grasses, trees or ground cover natural to the site.
The New Mineral Policy emphasized that all mining shall be undertaken within the parameters of a comprehensive Sustainable Development Framework which will ensure that environmental, economic and social considerations are integrated effectively in all decisions of mines and mineral issues. The Guiding principal shall be that a miner shall leave the mining area in an ecological shape which is as good as it was before the commencement of mining or better with least impact on flora and fauna of the area.
Improving environmental performance
It is well known fact that mining activity impacts the environment in unnatural ways, which not only disrupts its natural decaying process, but also does more damage long-term than natural erosion processes. With exorbitant numbers of materials excavated and used daily, it is important to see that this destruction is actually going towards productive use.
This step is basically emphasised on adopting new measures useful in mitigating these environmental impacts. Let’s push for a systematic framework that will help us monitor the environmental performance.
We have to adopt practice of systematically examining environmental impacts and adopting measures to mitigate these impacts, it is possible to make mining less destructive to the environment. Incremental efficiency gains will not do the job.
Instead, an imaginative remaking of the industrial world-one that aligns economies with the natural environment that supports them is the sustainable way forward. The New Mineral Policy has given thrust on the Sustainable Development
Economy & Market
Hindalco Buys US Speciality Alumina Firm for $125 Million
Published
2 months agoon
June 25, 2025By
admin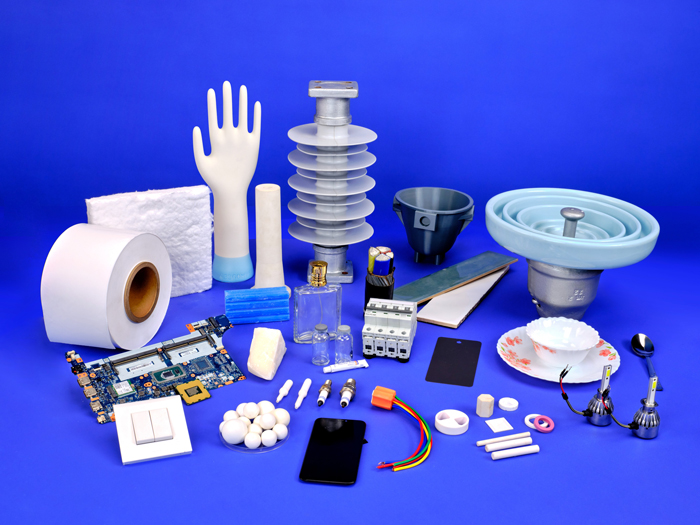
This strategic acquisition marks a significant investment in speciality alumina, a key step by Aditya Birla Group’s metals flagship towards becoming future-ready by scaling its high-value, technology-led materials portfolio.
Hindalco Industries, the world’s largest aluminium company by revenue and the metals flagship of the $28 billion Aditya Birla Group, has announced the acquisition of a 100 per cent equity stake in US-based AluChem Companies—a prominent manufacturer of speciality alumina—for an enterprise value of $125 million. The transaction will be executed through Aditya Holdings, a wholly owned subsidiary.
This acquisition represents a pivotal investment in speciality alumina and advances Hindalco’s strategy to expand its high-value, technology-led materials portfolio.
Hindalco’s speciality alumina business, a key pillar of its value-added strategy, has delivered consistent double-digit growth in recent years. It has emerged as a high-growth, high-margin vertical within the company’s portfolio. As speciality alumina finds expanding applications across electric mobility, semiconductors, and precision ceramics, the deal positions Hindalco further up the innovation curve, enabling next-generation alumina solutions and value-accretive growth.
Kumar Mangalam Birla, Chairman of Aditya Birla Group, called the acquisition an important step in their global strategy to build a leadership position in value-added, high-tech materials.
“Our strategic foray into the speciality alumina space will not only accelerate the development of future-ready, sustainable solutions but also open new pathways to pursue high-impact growth opportunities. By integrating advanced technologies into our value chain, we are reinforcing our commitment to self-reliance, import substitution, and building scale in innovation-led businesses.”
Ronald P Zapletal, Founder, AluChem Companies, said the partnership with Hindalco would provide AluChem the ability and capital to scale up faster and build scale in North America.
“AluChem will benefit from their world-class sustainability and safety standards and practices, access to integrated operations and a consistent, reliable raw material supply chain. Their ability to leverage R&D capabilities and a talented workforce adds tremendous value to our innovation pipeline, helping drive market expansion beyond North America.”
An Eye on the Future
The global speciality alumina market is projected to grow significantly, with rising demand for tailored solutions in sectors such as ceramics, electronics, aerospace, and medical applications. Hindalco currently operates 500,000 tonnes of speciality alumina capacity and aims to scale this up to 1 million tonnes by FY2030.
Commenting on the development, Satish Pai, Managing Director, Hindalco Industries, said the deal reinforced their commitment to innovation and global expansion.
“As alumina gains increasing relevance in critical and clean-tech sectors, AluChem’s advanced chemistry capabilities will significantly enhance our ability to serve these fast-evolving markets. Importantly, it deepens our high-value-added portfolio with differentiated products that drive profitability and strengthen our global competitiveness.”
AluChem adds a strong North American presence to Hindalco’s portfolio, with an annual capacity of 60,000 tonnes across three advanced manufacturing facilities in Ohio and Arkansas. The company is a long-standing supplier of ultra-low soda calcined and tabular alumina, materials prized for their thermal and mechanical stability and widely used in precision engineering and high-performance refractories.
Saurabh Khedekar, CEO of the Alumina Business at Hindalco Industries, said the acquisition unlocked immediate synergies, including market access and portfolio diversification.
“Hindalco plans to work with AluChem’s high performance technology solutions and scale up production of ultra-low soda alumina products to drive a larger global market share.”
The transaction is expected to close in the upcoming quarter, subject to customary closing conditions and regulatory approvals.

As India’s cement industry heads for unprecedented growth, the importance of smart, sustainable and strategic lubrication is gaining ground. From reducing downtime and enhancing energy efficiency to enabling predictive maintenance, lubricants are transforming plant performance. ICR explores how advanced lubrication solutions are becoming critical enablers of reliability, resilience and environmental stewardship in the cement sector.
The Indian cement industry, a cornerstone of the nation’s infrastructure development, is experiencing significant growth. In 2023, India’s cement production reached 374.55 million tonnes, marking a 6.83 per cent year-on-year growth. Projections indicate that the market size will expand from 3.96 billion tonnes in 2023 to 5.99 billion tonnes by 2032, reflecting a compound annual growth rate (CAGR) of 4.7 per cent during 2024-32. This expansion underscores the increasing demand for efficient and sustainable operations within the sector.
In cement manufacturing, equipment such as kilns, crushers, vertical mills, ball mills, conveyors and fans operate under extreme temperatures, heavy loads and high dust exposure. These demanding conditions make proper lubrication not just essential, but mission-critical. Selecting the right type of lubricant and maintaining an effective lubrication regime can drastically improve machine uptime, reduce maintenance costs, and enhance plant safety. In many cases, lubricant-related failures account for a significant proportion of unplanned downtime, underscoring the value of a well-structured lubrication strategy.
The Indian cement sector is also undergoing a technological transformation, with increasing emphasis on automation, predictive maintenance and energy efficiency. In this evolving landscape, lubricants are no longer just consumables—they are enablers of performance, longevity and sustainability. With the growing availability of advanced lubricants and condition-monitoring technologies, Indian cement plants have the opportunity to optimise their lubrication practices in line with global standards. Additionally, tightening environmental regulations and sustainability goals are driving the shift toward eco-friendly lubricants and responsible usage practices, making lubrication management a key factor in both operational and environmental performance.
As the industry moves forward, there is a growing realisation that lubrication excellence can be a competitive differentiator. This article explores the critical role of lubricants in cement manufacturing, the latest technological advancements, the environmental considerations shaping lubricant use, and the challenges and opportunities for cement producers in India aiming to maximise equipment reliability and operational efficiency.
The role of lubricants in cement manufacturing
Cement manufacturing involves heavy-duty machinery operating under extreme conditions—high temperatures, heavy loads and continuous operations. Lubricants are essential in minimising friction, reducing wear and tear, and preventing equipment failures. Proper lubrication ensures that components such as kilns, crushers and grinding mills function optimally, thereby reducing downtime and maintenance costs.
Moreover, the integration of advanced lubrication technologies has enabled predictive maintenance strategies. By monitoring lubricant conditions, operators can anticipate equipment issues before they escalate, allowing for timely interventions and uninterrupted production cycles.
“Lubricants play a crucial role in enhancing the efficiency and reliability of cement plant operations. High-performance lubricants reduce friction and wear in critical machinery such as crushers, kilns, mills, and conveyors, ensuring smoother operation and extending equipment life. By minimising mechanical breakdowns and unplanned downtime, they contribute to consistent production and lower maintenance costs. Additionally, specialised lubricants designed to withstand high temperatures, heavy loads, and dusty environments help maintain optimal performance under demanding conditions. Proper lubrication also improves energy efficiency by reducing power loss due to friction. In essence, the right lubrication strategy not only enhances equipment reliability and operational uptime but also supports overall cost-effectiveness and productivity in cement manufacturing,” says Hiten Ved, Sales Head, Royal Petro Specialities.
In addition to enhancing equipment longevity, lubricants are pivotal in ensuring uninterrupted production cycles. Cement manufacturing is a 24/7 operation, and any unexpected downtime due to mechanical failure can lead to significant financial losses. Lubricants with high thermal stability and oxidation resistance prevent the breakdown of oil films under intense heat, especially in applications like rotary kilns, vertical roller mills and clinker coolers. By reducing the likelihood of equipment seizures or breakdowns, these lubricants act as silent enablers of plant reliability and uptime.
Gaurav Mathur, Director and Chief Executive Officer, Global Technical Services, says, “Wall paintings in tombs show workers using water to move statues, indicating early recognition of lubrication. By 1400 BC, animal fat was used to lubricate chariot axles, ever since then mankind has been relentlessly working to improvise the efficiency of lubricants. Tribological advancements have propelled industrialisation in the world. Machines working in demanding environment need better performance, however merely just better lubricant that is made from highly refined base oils is not good enough. Mineral and synthetic base oils and advanced additives chemistry have given birth to advanced lubricants. These lubricants have better performance characteristics and longer service life.”
“However, the way lubrication is done is more critical and if lubrication is not performed in a proper way, highest performing lubricants would also under perform compared to the lowest specification product. Total Lubrication Management has to be implemented for better machine reliability, equipment availability and lower down time. Implementation of TLM has paid rich dividends in the industry. Pillars of TLM being, contamination free lubrication, regular testing of lubricants to access the lubricant and machine condition and regeneration of lubricants,” he adds.
Lubricants contribute directly to energy efficiency. Friction losses within rotating equipment can account for up to 30 per cent of the total energy consumption in certain plant areas. Advanced synthetic lubricants, with low traction coefficients and superior film strength, reduce this internal resistance, thus improving mechanical efficiency and lowering the plant’s overall energy footprint. As Indian cement plants pursue energy benchmarking and ISO 50001 certifications, the use of high-performance lubricants becomes an integral strategy in achieving energy conservation goals.
“The cement industry has many lubrication points that require NLGI Grade 2 grease that can be used in high temperature applications. These may include bearings on vibrating screens and roller mills; rotating joints on grinding units; and various shafts, pivots, and metal to metal contact points found throughout the plant. CorrLube™ VpCI® Lithium EP Grease has a dropping point of 360 °F (182 °C), allowing it to be used in a broad range of temperatures. For areas that need a slightly harder grease of NLGI Grade 3, EcoLine® Biobased Grease offers a
similar dropping point of 365 °F (185 °C), explain Julie Holmquist, Marketing Content Writer,
Cortec Corporation.
Market dynamics: growth and trends
The Indian industrial lubricants market was valued at $13.05 billion in 2024 and is projected to reach $ 20.72 billion by 2033, growing at a CAGR of 4.12 per cent. This growth is driven by the expanding industrial sector, increased mechanisation, and the adoption of advanced machinery requiring specialised lubricants.
In the cement sector specifically, the demand for high-performance lubricants is rising. The lubricants for cement market are estimated to be $ 2.5 billion in 2024 and is expected to reach $ 3.9 billion by 2033, at a CAGR of 5.3 per cent from 2026 to 2033. This surge is attributed to the need for lubricants that can withstand harsh operating conditions and enhance equipment reliability.
Advancements in lubrication technology
Recent years have witnessed significant advancements in lubrication technology tailored for the cement industry. Synthetic lubricants, known for their superior thermal stability and longer service life, are increasingly being adopted. These lubricants perform effectively under extreme temperatures and heavy loads, common in cement manufacturing processes.
Additionally, the development of bio-based lubricants offers environmentally friendly alternatives without compromising performance. These lubricants, derived from renewable sources, reduce the environmental footprint and align with global sustainability goals. Their biodegradability and low toxicity make them suitable for applications where environmental considerations are paramount.
Smart lubrication systems are another breakthrough in the cement industry. These systems use IoT-enabled sensors and controllers to monitor lubricant condition in real time—tracking parameters such as viscosity, temperature, contamination levels and usage. This data is integrated into plant maintenance software to automate lubricant replenishment and alert operators to potential failures. Predictive lubrication ensures that each component receives the right amount of lubricant at the right time, minimising waste, reducing manual intervention, and extending machinery life.
“Many VpCI® products can be applied to surfaces with minimal pre-cleaning, and the protective VpCI® layer typically does not need to be removed before equipment is put back into service. VpCI® ‘s save significant labor, time, and associated costs compared to methods that require extensive surface preparation (e.g., sandblasting) and post-application cleaning or degreasing. This allows for faster startup after maintenance,” elaborates Ana Juraga, Content Writer, Cortec Corporation.
Furthermore, Original Equipment Manufacturers (OEMs) and lubricant suppliers are collaborating to develop application-specific lubricants tailored to the unique operating conditions of cement manufacturing units. For example, gear oils designed for high-load kilns or open gear systems now come with superior Extreme Pressure (EP) additives and anti-wear properties to cope with shock loading and variable speed operations. These co-developed solutions not only enhance mechanical reliability but also ensure compatibility with diverse materials used in modern cement equipment, ensuring peak performance in both greenfield and brownfield plants.
Sustainability and environmental considerations
The cement industry is under increasing pressure to reduce its environmental impact. Lubricants contribute to this goal by enhancing energy efficiency and reducing emissions. High-quality lubricants decrease friction, leading to lower energy consumption and, consequently, reduced greenhouse gas emissions.
Furthermore, the use of long-life lubricants minimises the frequency of oil changes, thereby reducing waste generation and disposal issues. The shift towards bio-based and recyclable lubricants also supports circular economy principles, promoting resource efficiency and environmental stewardship.
A report by Klüber Lubrication India suggests that sustainability continues to be a key focus for industries, the Securities and Exchange Board of India (SEBI) has mandated Business Responsibility and Sustainability Reporting (BRSR) for the top 1,000 listed companies. This framework requires organisations to disclose their environmental, social and governance (ESG) initiatives, including energy conservation, emission reductions and resource optimisation. Beyond compliance, BRSR reporting allows companies to showcase their sustainability leadership and build investor confidence. Organisations that proactively address sustainability challenges are better positioned to attract long-term investors, secure financing, and maintain a competitive advantage in an evolving regulatory landscape.
The report also states that their high-performance synthetic lubricants play a crucial role in helping cement manufacturers meet these regulatory requirements by enhancing energy efficiency and reducing CO2 emissions in critical machinery such as vertical roller mills (VRMs) and main gearboxes. By adopting our energy-efficient solutions, companies can strengthen their BRSR compliance while achieving tangible operational benefits.
An emerging trend in the lubricant industry is the formulation of biodegradable lubricants specifically tailored for heavy industries like cement manufacturing. These eco-friendly alternatives are made from renewable base stocks and are designed to degrade naturally without leaving behind harmful residues. In environmentally sensitive zones or operations with high spill risk, such as open gear applications or hydraulic systems exposed to the elements, biodegradable lubricants offer a sustainable solution that aligns with stricter environmental regulations and the growing emphasis on corporate social responsibility (CSR) in India’s industrial sector.
KB Mathur, Founder and Director, Global Technical Services, says, “In the world of industrial machinery, lubricating oils while essential; are often misunderstood in terms of their life cycle. When oils are used in machinery, they don’t simply ‘DIE’. Instead, they become contaminated with moisture (water) and solid contaminants like dust, dirt and wear debris. These contaminants degrade the oil’s effectiveness but do not render it completely unusable. Used lubricants can be regenerated via advanced filtration processes/systems and recharged with the use of performance enhancing additives hence restoring them. These oils are brought back to ‘As-New’ levels. This new fresher lubricating oil is formulated to carry out its specific job providing heightened lubrication and reliable performance of the assets with a view of improved machine condition. Hence, contributing to not just cost savings but leading to magnified productivity, and diminished environmental stress.”
Lubricant manufacturers are increasingly focusing on circular economy principles, offering oil analysis, filtration and recycling services that extend lubricant life and minimise waste. Used oil regeneration programs not only reduce disposal costs but also help cement plants meet regulatory norms under the Hazardous Waste Management Rules of India. This closed-loop approach not only lowers the environmental burden but also enhances economic efficiency—making sustainability a dual benefit for operational and ecological performance. As cement companies work towards science-based targets and carbon neutrality, lubricant selection and management play a more strategic role in meeting these broader sustainability commitments.
Challenges and opportunities
Despite the benefits, the adoption of advanced lubricants in the Indian cement industry faces challenges. These include the higher initial costs of synthetic and bio-based lubricants and a lack of awareness about their long-term benefits. Additionally, the integration of lubrication management systems requires investment in training and infrastructure.
However, these challenges present opportunities for innovation and collaboration. Manufacturers
can work closely with lubricant suppliers to develop customised solutions that meet specific operational needs. Moreover, government incentives and regulatory frameworks promoting sustainable practices can accelerate the adoption of advanced lubrication technologies.
Another key challenge is the limited awareness and technical training available at the plant level regarding proper lubrication practices. Many maintenance teams still rely on outdated methods such as manual greasing or fixed-interval lubrication schedules, which often lead to over-lubrication, under-lubrication or lubricant contamination. This results in premature equipment wear and higher operating costs. There is a growing need for skill development programmes and collaboration with lubricant suppliers to train technicians on best practices, condition-based monitoring, and the use of smart lubrication systems.
“Oil in the machine is like blood in the human body. There is no rotating machine that works without lubricants (liquid, semi liquid or solid). Based on the machine component, type of lubricant is used to minimise the mechanical changes in the machine. Lubricant being the product that separates two or more materials under movement. With modern machines being more and more sophisticated and tolerances being finer than before, cleanliness of Lubricants is critical, would the source of contamination be internal wear or external contamination. These contaminations rupture and compromises lubricant film, contamination particles when come in-between the fine tolerances, become cause of catastrophic failure,” expounds Gaurav Mathur.
At the same time, the industry is witnessing an opportunity to leverage digitalisation in lubrication management. Advanced lubrication tracking tools, coupled with ERP and maintenance software, can now offer real-time visibility into lubricant consumption, scheduling and health diagnostics. Integration of AI-powered analytics helps predict equipment failure based on lubricant data, enabling a shift from reactive to predictive maintenance. For Indian cement manufacturers aiming to digitise plant operations as part of Industry 4.0, lubrication is an ideal entry point that delivers immediate ROI and long-term gains in efficiency, asset life and sustainability.
Conclusion
As the Indian cement industry continues its trajectory of growth, the role of high-performance lubricants in ensuring operational reliability, energy efficiency and cost savings cannot be overstated. From kilns and crushers to ball mills and gearboxes, modern lubrication solutions are critical in
reducing downtime and maximising equipment lifespan. With rising demand and increased production pressures, cement plants must adopt a proactive approach to lubrication management—viewing it not as a routine maintenance task, but as a strategic pillar of plant performance.
Recent advancements in lubricant technology, such as synthetic formulations, nano-additives, and smart dispensers, have opened new avenues for boosting equipment efficiency and longevity. Digital tools and IoT-based systems now allow plant operators to monitor lubricant condition in real time, enabling predictive maintenance and minimising the risk of failure. As cement manufacturers increasingly pursue digital transformation and automation under Industry 4.0 frameworks, lubrication systems must be seamlessly integrated into broader asset management strategies.
At the same time, sustainability imperatives are reshaping lubrication choices. There is growing emphasis on biodegradable lubricants, optimised lubricant consumption, and environmentally responsible disposal practices. Overcoming challenges such as limited awareness, inconsistent maintenance practices, and cost sensitivity will require collaboration between lubricant manufacturers, OEMs and cement producers. The opportunities, however, are substantial—by aligning lubrication strategies with efficiency, digitalisation and sustainability goals, the Indian cement industry can significantly enhance its competitiveness and resilience in the years ahead.
– Kanika Mathur
Concrete
We consistently push the boundaries of technology
Published
5 months agoon
April 18, 2025By
admin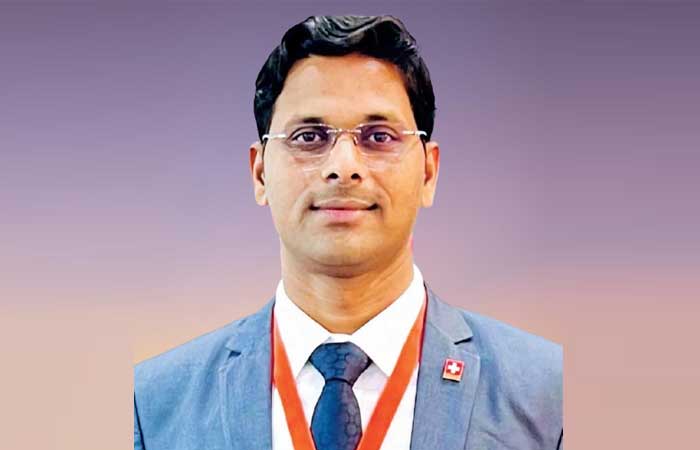
Swapnil Jadhav, Director, SIDSA Environmental, discusses transforming waste into valuable resources through cutting-edge technology and innovative process solutions.
SIDSA Environmental brings decades of experience and expertise to the important niche of waste treatment and process technologies. As a global leader that is at the forefront of sustainable waste management, the company excels in recycling, waste-to-energy solutions and alternative fuel production. In this conversation, Swapnil Jadhav, Director, SIDSA Environmental, shares insights into their advanced shredding technology, its role in RDF production for the cement industry and emerging trends in waste-to-energy solutions.
Can you give us an overview of SIDSA Environmental’s role in waste treatment and process technologies?
SIDSA is a leading innovator in the field of waste treatment and process technologies, dedicated to delivering sustainable solutions that address the growing challenges of waste management.
SIDSA is a more than 52-year-old organisation with worldwide presence and has successfully realised over 1100 projects.
Our expertise is in the engineering and development of cutting-edge systems that enable the conversion of waste materials into valuable resources. This includes recycling technologies, waste-to-energy (W2E) systems, and advanced methods for producing alternative fuels such as refuse derived fuel (RDF). The organisation prioritises environmental stewardship by integrating energy-efficient processes and technologies, supporting industrial sectors—including the cement industry—in reducing their carbon footprint. Through our comprehensive approach, we aim to promote a circular economy where waste is no longer a burden but a resource to be harnessed.
How does SIDSA Environmental’s shredding technology contribute to the cement industry, especially in the production of RDF?
SIDSA’s shredding technology is pivotal in transforming diverse waste streams into high-quality RDF. Cement kilns require fuel with specific calorific values and uniform composition to ensure efficient combustion and operational stability, and this is where our shredding systems excel. In India, we are segment leaders with more than 30 projects including over 50 equipment of varied capacity successfully realised. Some of the solutions were supplied as complete turnkey plants for high capacity AFR processing. Our esteemed client list comprises reputed cement manufacturers and chemical industries. Our technology processes various types of waste—such as plastics, textiles and industrial residues—breaking them down into consistent particles suitable for energy recovery.
Key features include:
- High efficiency: Ensures optimal throughput for large volumes of waste.
- Adaptability: Handles mixed and heterogeneous waste streams, including contaminated or complex materials.
- Reliability: Reduces the likelihood of operational disruptions in RDF production. By standardising RDF properties, our shredding technology enables cement plants to achieve greater energy efficiency while adhering to environmental regulations.
What are the key benefits of using alternative fuels like RDF in cement kilns?
The adoption of RDF and other alternative fuels offers significant advantages across environmental, economic and social dimensions:
- Environmental benefits: Cement kilns using RDF emit fewer greenhouse gases compared to those reliant on fossil fuels like coal or petroleum coke. RDF also helps mitigate the issue of overflowing landfills by diverting waste toward energy recovery.
- Economic savings: Alternative fuels are often more cost-effective than traditional energy sources, allowing cement plants to reduce operational expenses.
- Sustainability and resource efficiency: RDF facilitates the circular economy by repurposing waste materials into energy, conserving finite natural resources.
- Operational flexibility: Cement kilns designed to use RDF can seamlessly switch between different fuel types, enhancing adaptability to market conditions.
What innovations have been introduced in waste-to-energy (W2E) and recycling solutions?
SIDSA’s machinery is meticulously engineered to handle the complex requirements of processing hazardous and bulky waste.
This includes:
- Robust construction: Our equipment is designed to manage heavy loads and challenging waste streams, such as industrial debris, tires and large furniture.
- Advanced safety features: Intelligent sensors and automated controls ensure safe operation when dealing with potentially harmful materials, such as chemical waste.
- Compliance with standards: Machinery is built to adhere to international environmental and safety regulations, guaranteeing reliability under stringent conditions.
- Modular design: Allows for customisation and scalability to meet the unique needs of various waste management facilities.
How does your organisation customised solutions help cement plants improve sustainability and efficiency?
We consistently push the boundaries of technology to enhance waste management outcomes.
General innovations and new product development focus on:
- Energy-efficient shredders: These machines consume less power while maintaining high throughput, contributing to lower operational costs.
- AI-powered sorting systems: Utilise advanced algorithms to automate waste classification, increasing material recovery rates and minimising errors.
- Advanced gasification technologies: Convert waste into syngas (a clean energy source) while minimising emissions and residue.
- Closed-loop recycling solutions: Enable the extraction and repurposing of materials from waste streams, maximising resource use while reducing environmental impact.
What future trends do you foresee in waste management and alternative fuel usage in the cement sector?
Looking ahead, several trends are likely to shape the future of waste management and alternative fuels in the cement industry:
- AI integration: AI-driven technologies will enhance waste sorting and optimise RDF production, enabling greater efficiency.
- Bio-based fuels: Increased use of biofuels derived from organic waste as a renewable and low-carbon energy source.
- Collaborative approaches: Strengthened partnerships between governments, private industries and technology providers will facilitate large-scale implementation of sustainable practices.
- Circular economy expansion: The cement sector will increasingly adopt closed-loop systems, reducing waste and maximising resource reuse.
- Regulatory evolution: More stringent environmental laws and incentives for using alternative fuels will accelerate the transition toward sustainable energy solutions.
(Communication by the management of the company)