Process
Another Brick off the Wall
Published
6 years agoon
By
admin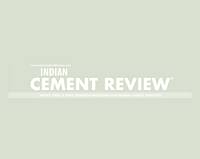
According to the Building Material Promotion Council (BMPTC), India generates an estimated 150 million tonnes of construction and demolition (C&D) waste every year. But the official recycling capacity is a meagre 6,500 tonnes per day (TPD) – just about 1 per cent. What’s more, unofficial estimates of the total waste generated in the country put the figure at three-five times more than the official estimate. A new analysis by Centre for Science and Environment (CSE), released in Delhi on 25th August 2020 at a national online Round Table, has laid bare some of these unpleasant truths about the way the country is managing its C&D waste. Another Brick off the Wall: Improving construction and demolition waste management in Indian cities – as the analysis report is titled – also goes on to recommend a viable plan of action.
Releasing the report at the Round Table, CSE director general Sunita Narain said: "Our study shows that as many as 53 cities were expected to set up recycling facilities to recover material from C&D waste by 2017 – but only 13 cities have done that by 2020. This is unacceptable when the demand for primary building material, including minerals, stone, sand, iron ore, aluminum, and timber, is growing at an unprecedented rate.
She went on to add: "A significant proportion of construction waste can be recycled and reused and brought back to construction to substitute naturally sourced material. This demands a circular economy that can turn C&D waste into a resource. This can help reduce energy intensity and environmental footprints of buildings and infrastructure."
Speaking at the meeting, Anumita Roychowdhury, executive director-research and advocacy, CSE and the head of the Centre’s Sustainable Urbanisation programme, said:"Heaps of concrete, bricks and metal waste from construction are choking waterbodies, green areas and public spaces in our cities. Toxic dust particles from the debris are polluting air, at a time when cities have to reduce their particulate pollution by 20-30 per cent by 2024, under the ongoing National Clean Air Programme (NCAP)."
CSE researchers point out that the sorry state of affairs exists notwithstanding the removal of legal hurdles to using recycled C&D material in construction. The Bureau of Indian Standards (BIS) has allowed the use of concrete made from recycled material and processed C&D waste. The Construction and Demolition Waste Rules and Regulations, 2016 have mandated reuse of recycled material.
Even the Swachh Bharat Mission has recognised the need for C&D waste management. Ranking points for C&D waste management for SwachhSurvekshan2021 have been doubled to 100 points, divided equally between management infrastructure and waste processing efficiency. Cities will need to have a C&D waste collection system in place; notified charges for C&D services; and segregation of waste in five streams. Under waste processing efficiency criteria, ranking points will be awarded based on the percentage of collected waste that is processed and reused.
Said Roychowdhury: "This recognition by the Swachh Bharat Mission and the C&D Waste Rules offers an opportunity – cities will need strong preparedness for this. Our new study has carried out a detailed analysis of the current C&D challenge as well as technical and regulatory barriers to implementation of the Rules. It has identified strategies needed to accelerate the implementation of the Rules and market uptake of recycled material. The analysis is supported by ground-reality checks in multiple cities."
Key highlights
Need robust estimation and characterisation of C&D waste to design systems for material recovery: Cities need comprehensive assessment and quantification of C&D waste generation, to plan adequate infrastructure and systems for treatment and management. ULBs (Urban Local Bodies) to some extent have documented the quantum of C&D waste dumped in landfills or in locations under their direct jurisdiction. However, a significant portion of the waste is diverted to informal markets and for illegal filling beyond the municipal jurisdiction.
Cities must create easily accessible databases of buildings and their physical and legal attributes. Construction/demolition permits need to be inventorised with associated waste management plans attached. Also, characterisation of the C&D waste is necessary for the management plan, including collection, transportation and storage, processing techniques and technologies used, and products to be manufactured out of recycled waste. The method for quantification has to consider the new-age construction materials that is expanding especially under Pradhan Mantri Awas Yojana (PMAY) for the affordable housing sector.
Constraints in finding land for collection and recycling: Nearly all cities are facing the crippling challenge of finding adequate land for collection and recycling of the C&D waste. This is further constrained by outdated zoning requirements and "not in my backyard" sentiment among citizens. There is additional pressure of real-estate value capture that prevents land from being earmarked for waste disposal. Cities fear loss of revenue. Several cities have begun to consider land from no-development zones or ecologically sensitive areas. For instance, Gurugram’s proposal to build its recycling facility in the Aravalli Hills and Kolkata’s proposal to build it in a wetland were blocked by the respective state environment authorities for violating rules for environmentally sensitive areas. Pune has identified land that belonged to the state government outside the city limit.
Challenge of collection and transport of C&D waste: There is considerable variation in C&D waste transportation practices among ULBs. For instance, the responsibility of transporting waste in Delhi lies with the waste generator. They are required to deliver C&D waste at their own expense to the designated collection points. The ULBs then take the waste to the disposal site. But private and informal transporters are often not aware of collection points. Sometime commuting to those points is uneconomical. Sometimes they are asked by the caretakers of sites to pay informal usage fee. This leads to litter. Kolkata on the other hand provides on-call waste collection services. Waste generators are allocated a day and time slot for the pickup, based on payment. This is a better model but also faces the challenge of capacity crunch and the service is not adequately extended citywide.
Concerns about finances and business case: Cities have been found looking for ways to shield themselves from any financial liability while implementing the Rules. In some cases, ULBs have proposed that the contracted party for collection and transportation of C&D waste actually pay the ULB rather than receive a tipping fee for each tonne of C&D waste. Many have proposed that the recycling facility must share profits from recycled products with the ULB. These have deterred development of much needed new entrepreneurship in this sector.
Low involvement of state government agencies/departments: State urban departments are supposed to frame policies on C&D waste management, supplementing the 2016 Rules, to help implementation in the local context. In most cases, their engagement has been poor. There has been some rekindling of interest after C&D waste management has got included in clean air action plans. Moreover, active involvement of state urbandevelopment departmentsis neededfor financial assistance and suitable land identification for establishing wasteprocessing facilities. Also state government agencies such as PWD, Housing Development Board/Authority, City Development Authorities, public sector utility companies etc. involved insignificant construction/demolition work need to coordinate with ULBs for proper disposal and buy recycled products.
Lukewarm response from construction industry, low awareness:The Niti Aayog’s 2019 C&D waste strategy report notes glaring lack of awareness of the C&D waste rules among the construction industry across the nation. In large projects where C&D waste management gets incorporated within the environmental clearance requirement, implementation is a challenge. Incorrect disposal cost Bengaluru heavily during the mega-construction of its Kempegowda International Airport. In its first phase the contractor took advantage of the massive project site and dumped generated C&D waste on the vacant land meant for the second phase of the project. Now, the contractors of the second phase are struggling to clean the site.
The Rules stipulate that large projects should ideally adopt significant in situ utilisation of C&D waste in their projects, wherever feasible. The Rules make the waste generator responsible for managing the waste. But the way this splintered between the developer and third party, there are problem of forged documents to show compliance with C&D waste disposal requirements by project owners as they themselves are not in direct control nor have knowledge of waste disposed. Requirements and responsibilities need to be spelled out clearly in all contacting and subcontracting agreements fora project with proof.
Address pricing of recycled C&D waste products: Trust is quality of recycled waste as building material is improving, for instance Central Public Works Department (CPWD), has already adopted guidelines for usage of recycled products. CPWD has used recycled aggregate products in the new building of the Supreme Court in Delhi. But pricing of it remains a big concern. The Ministry of Housing and Urban Affairs has stipulated in many public forums that the cost of the recycled products need to be at par or lower than the corresponding conventional building material. But in reality recycled C&D waste products are taxed higher than conventional building material. Currently, conventional aggregates are taxed at 5 per cent and manufactured products from the recycled C&D waste are taxed at 18 per cent, making recycled products economically unviable for most customers. GST must be relaxed for C&D waste recycled products, including tiles, paver blocks, bricks, sand and aggregates. Role of informal sector: The C&D Rules failed to take into account the informal economy and livelihoods attached with C&D waste handling. This reduced the scope of informal sector participation. But now Swachch Survekshan 2021’s recognition of reusing C&D waste without processing has opened up opportunity of involving the informal sector in the formal management of C&D waste. This can generate jobs and lively hood. Cities would have to invest way less in C&D waste management infrastructure if they leveraged the existing informal infrastructure. This will allow high-value resource recovery and livelihood generation.
Demolition management: The 2016 Rules classify all building materials, debris and rubble resulting from construction, remodelling, demolition and reparation work as C&D waste. TIFAC’s 2001 assessment of C&D waste had noted that of all the materials produced in demolition, about 25 per cent from old buildings and 75 per cent from new buildings can be recovered for reuse. Given that demolition is the most prominent waste-generating activity, demolition services need attention. ULBs have not developed any system to monitor and regulate big or small demolition contractors. Some kind of official permit or NOC is needed for all building demolition.
For instance, the Chennai Municipal Corporation issues independent demolition permits to construction/demolition contractors. In most cases ULBs issue reconstruction approvals/ demolition. Due to this clubbing of permits, data on demolition is very poor. Multiple ULBs have now made it a requirement for owners or developers to manage their C&D waste responsibly. Lack of any official guidelines on resource recovery during demolition is a major concern.
Preparing for waste management from new generation material: Expanded polystyrene insulation (EPS), styrofoam, plastic spacers, bituminous material and asbestos embedded within new wall assemblies are a recycling challenge. This low-density bulky material, results in high transport cost per unit weight. Thermoplastics (polycarbonate, polyethylene, polypropylene, PVC etc.) can be recycled, but just like EPS their recycling involves high costs, whereas thermosets (epoxy adhesives) are difficult to recycle. This needs special attention.
Infrastructure projects need to set up their own recycling facilities: DMRC has done so. Concrete can be easily recycled. Butt excavated waste is a challenge. Other infrastructure projects like highway and roadwork find recycling of bituminous material waste challenging. Globally, proactive prevention of waste is undertaken through modification of existing on site construction practices etc.
Poor monitoring and lack of resources: ULBs suffering from chronic shortages in both human and financial resources are hard pressed to monitor, collect and dispose of waste. ULBs also lack access to basic scientific tools for waste estimation and to adequate knowledge support and experience for feasibility planning, tendering and so on. Guidance available for the scheme is weak.
What CSE recommends
Need robust estimation of C&D waste: Cities need comprehensive assessment and quantification of C&D waste generation, utilization and disposal to plan adequate infrastructure and systems for management. Create easily accessible databases of buildings and their physical and legal attributes. Construction/demolition permits need to be inventorised with waste management plans attached.
Characterisation of the C&D waste is necessary for the management plan. This is needed toinformcollection, transportation and storage, processing techniques and technologies used, and products to be manufactured out of recycled waste.
Land identification for collection and recycling: Cities need to prioritise identifying land for intermediate collection points and storage of C&D waste instead for a recycling facility. Also need innovative methods to reduce the requirement of land for collection – like providing waste containers to construction sites as part of the building permit as proposed by Pune can be adopted.
Set up transportation system for collection and transfer of C&D waste: Reduce distances to recycling and disposal sites as that adds to the expense. Need dense network of collection points. The cost of the final transportation is paid from the waste-handling fee charged as part of building permit. Cities need to find ways to leverage informal network to cut cost of new infrastructure creation.
Strengthen the governance framework: Niti Aayog’s strategy has suggested that the Ministry of Housing and Urban Affairs (MoHUA) may empanel suitable expert agencies/consultants who can provide handholding assistance to cities for waste mapping, by-law drafting, and public procurement policy for recycled products to identifying financial assistance. Also link C&D waste management facilitation to fiscal support to states. Develop knowledge, templates, guides, manuals and standards. Focus on minimisation of waste, not only monetisation of it.
Responsibility of the construction Industry: The current system provides no incentive to the construction agencies for managing their own waste via waste reduction and on-site reuse and recycling.The Rules have created a push by creating a legal requirement for waste management but the financial drivers are missing. This requires fiscal strategy.
Learn from global practices: In some European countries, high waste tax has achieved a significant level on C&D waste reduction. High level of landfill taxes in Denmark and the Netherlands demonstrated a low dependency on landfill and a high level of waste recovery. Hong Kong has one of the most aggressive C&D waste fee regimes in the world to reduce waste generation in the city. These are combined with stringent in-situ management.
Build confidence in recycled products for quicker uptake: Need strategies to stimulate uptake of recycled products. Reduce current high GST rate (18 per cent). Also do quality control of recycled products.
Integrate Informal sector in C&D waste management and disposal: There is a need to acknowledge livelihoods attached with this waste and it has potential to complement the C&D waste management system of the city. Formal integration can improve performance.
Mandatory adoption of demolition management strategies: Provide formal recognition to demolition contractor and develop a register of them. Develop a separate and independent demolition permit. Encourage deconstruction instead of quick demolition. Mandate on-site construction waste management during construction phase: C&D waste management requirement come bundled with the environmental clearance for big projects. Ensure proper implementation. But need a strategy for compliance for the vast majority of small and medium enterprises.
Advance application of tools for implementation of end-of-life waste recovery, recycling, and circularity: Location-based tools, which are usually GIS enabled, have been developed to provide the location of C&D waste management services. This is applied globally. More efficient waste sorting technologies are needed. Technologies used for waste recovery, recycling and circularity encompass three interrelated methods.
Waste management in infrastructure projects: Agencies will have to develop their own recycling facilities. Roadwork projects require additional technological development for recycling of bituminous material.
Dust control in construction projects: The planning stage of the project requires identification of dust control impacts; careful programming of works to reduce dust impacts; identification of dust mitigation measures among others.
Said Roychowdhury: "Environmental and material challenges associated with the C&D problem need urgent and immediate attention nation-wide to recover material, protect environment, and for clean air."
For more details, or for interviews with experts, please contact Sukanya Nair of The CSE Media Resource Centre, sukanya.nair@cseindia.org, 8816818864.
We acknowledge with thanks to "Centre for Science and Environment (CSE)" New Delhi for a detailed coverage on the subject.
In Box Official estimates say India generates 150 million tonnes of C&D waste annually; unofficial estimates put the number at three-five times more. Country has a recycling capacity for only about 6,500 tonnes per day – just 1.3 per cent of the total C&D waste generated. By 2017, 53 cities were expected to set up recycling facilities to recover material from the waste; only 13 cities have done it till date. There is no uniformity among cities to quantify and characterize C&D waste to know what and how to segregate. Methods have not been updated to bring in new-age construction materials. C&D waste recycling from infrastructure development remains a non-starter – Delhi Metro’s 4th phase is the only good practice is the country. 33 per cent of the waste generation can be avoided if architects design for waste mitigation during the pre-construction stage. It is encouraging that Swachh Survekshan 2021 has given more prominence and scoring points to action on C&D waste. But this has to push right design for segregation, collection, recycling and reuse.
You may like
Process
Price hikes, drop in input costs help cement industry to post positive margins: Care Ratings
Published
4 years agoon
October 21, 2021By
admin
Region-wise,the southern region comprises 35% of the total cement capacity, followed by thenorthern, eastern, western and central region comprising 20%, 18%, 14% and 13%of the capacity, respectively.
The cement industry is expected to post positive margins on decent price hikes over the months, falling raw material prices and marked drop in overall production costs, said an analysis of Care Ratings.
Wholesale and retail prices of cement have increased 11.9% and 12.4%, respectively, in the current financial year. As whole prices have remained elevated in most of the markets in the months of FY20, against the corresponding period of the previous year.
Similarly, electricity and fuel cost have declined 11.9% during 9M FY20 due to drop in crude oil prices. Logistics costs, the biggest cost for cement industry, has also dropped 7.7% (selling and distribution) as the Railways extended the benefit of exemption from busy season surcharge. Moreover, the cost of raw materials, too, declined 5.1% given the price of limestone had fallen 11.3% in the same aforementioned period, the analysis said.
According to Care Ratings, though the overall sales revenue has increased only 1.3%, against 16% growth in the year-ago period, the overall expenditure has declined 3.2% which has benefited the industry largely given the moderation in sales.
Even though FY20 has been subdued in terms of production and demand, the fall in cost of production has still supported the cement industry by clocking in positive margins, the rating agency said.
Cement demand is closely linked to the overall economic growth, particularly the housing and infrastructure sector. The cement sector will be seeing a sharp growth in volumes mainly due to increasing demand from affordable housing and other government infrastructure projects like roads, metros, airports, irrigation.
The government’s newly introduced National Infrastructure Pipeline (NIP), with its target of becoming a $5-trillion economy by 2025, is a detailed road map focused on economic revival through infrastructure development.
The NIP covers a gamut of sectors; rural and urban infrastructure and entails investments of Rs.102 lakh crore to be undertaken by the central government, state governments and the private sector. Of the total projects of the NIP, 42% are under implementation while 19% are under development, 31% are at the conceptual stage and 8% are yet to be classified.
The sectors that will be of focus will be roads, railways, power (renewable and conventional), irrigation and urban infrastructure. These sectors together account for 79% of the proposed investments in six years to 2025. Given the government’s thrust on infrastructure creation, it is likely to benefit the cement industry going forward.
Similarly, the Pradhan Mantri Awaas Yojana, aimed at providing affordable housing, will be a strong driver to lift cement demand. Prices have started correcting Q4 FY20 onwards due to revival in demand of the commodity, the agency said in its analysis.
Industry’s sales revenue has grown at a CAGR of 7.3% during FY15-19 but has grown only 1.3% in the current financial year. Tepid demand throughout the country in the first half of the year has led to the contraction of sales revenue. Fall in the total expenditure of cement firms had aided in improving the operating profit and net profit margins of the industry (OPM was 15.2 during 9M FY19 and NPM was 3.1 during 9M FY19). Interest coverage ratio, too, has improved on an overall basis (ICR was 3.3 during 9M FY19).
According to Cement Manufacturers Association, India accounts for over 8% of the overall global installed capacity. Region-wise, the southern region comprises 35% of the total cement capacity, followed by the northern, eastern, western and central region comprising 20%, 18%, 14% and 13% of the capacity, respectively.
Installed capacity of domestic cement makers has increased at a CAGR of 4.9% during FY16-20. Manufacturers have been able to maintain a capacity utilisation rate above 65% in the past quinquennium. In the current financial year due to the prolonged rains in many parts of the country, the capacity utilisation rate has fallen from 70% during FY19 to 66% currently (YTD).
Source:moneycontrol.com
Process
Wonder Cement shows journey of cement with new campaign
Published
4 years agoon
October 21, 2021By
admin
The campaign also marks Wonder Cement being the first ever cement brand to enter the world of IGTV…
ETBrandEquity
Cement manufacturing company Wonder Cement, has announced the launch of a digital campaign ‘Har Raah Mein Wonder Hai’. The campaign has been designed specifically to run on platforms such as Instagram, Facebook and YouTube.
#HarRaahMeinWonderHai is a one-minute video, designed and conceptualised by its digital media partner Triature Digital Marketing and Technologies Pvt Ltd. The entire journey of the cement brand from leaving the factory, going through various weather conditions and witnessing the beauty of nature and wonders through the way until it reaches the destination i.e., to the consumer is very intriguing and the brand has tried to showcase the same with the film.
Sanjay Joshi, executive director, Wonder Cement, said, "Cement as a product poses a unique marketing challenge. Most consumers will build their homes once and therefore buy cement once in a lifetime. It is critical for a cement company to connect with their consumers emotionally. As a part of our communication strategy, it is our endeavor to reach out to a large audience of this country through digital. Wonder Cement always a pioneer in digital, with the launch of our IGTV campaign #HarRahMeinWonderHai, is the first brand in the cement category to venture into this space. Through this campaign, we have captured the emotional journey of a cement bag through its own perspective and depicted what it takes to lay the foundation of one’s dreams and turn them into reality."
The story begins with a family performing the bhoomi poojan of their new plot. It is the place where they are investing their life-long earnings; and planning to build a dream house for the family and children. The family believes in the tradition of having a ‘perfect shuruaat’ (perfect beginning) for their future dream house. The video later highlights the process of construction and in sequence it is emphasising the value of ‘Perfect Shuruaat’ through the eyes of a cement bag.
Tarun Singh Chauhan, management advisor and brand consultant, Wonder Cement, said, "Our objective with this campaign was to show that the cement produced at the Wonder Cement plant speaks for itself, its quality, trust and most of all perfection. The only way this was possible was to take the perspective of a cement bag and showing its journey of perfection from beginning till the end."
According to the company, the campaign also marks Wonder Cement being the first ever cement brand to enter the world of IGTV. No other brand in this category has created content specific to the platform.
Process
In spite of company’s optimism, demand weakness in cement is seen in the 4% y-o-y drop in sales volume. (Reuters)
Published
4 years agoon
October 21, 2021By
admin
Cost cuts and better realizations save? the ?day ?for ?UltraTech Cement, Updated: 27 Jan 2020, Vatsala Kamat from Live Mint
Lower cost of energy and logistics helped Ebitda per tonne rise by about 29% in Q3
Premiumization of acquired brands, synergistic?operations hold promise for future profit growth Topics
UltraTech Cement
India’s largest cement producer UltraTech Cement Ltd turned out a bittersweet show in the December quarter. A sharp drop in fuel costs and higher realizations helped drive profit growth. But the inherent demand weakness was evident in the sales volumes drop during the quarter.
Better realizations during the December quarter, in spite of the 4% year-on-year volume decline, minimized the pain. Net stand-alone revenue fell by 2.6% to ?9,981.8 crore.
But as pointed out earlier, lower costs on most fronts helped profitability. The chart alongside shows the sharp drop in energy costs led by lower petcoke prices, lower fuel consumption and higher use of green power. Logistics costs, too, fell due to lower railway freight charges and synergies from the acquired assets. These savings helped offset the increase in raw material costs.
The upshot: Q3 Ebitda (earnings before interest, tax, depreciation and amortization) of about ?990 per tonne was 29% higher from a year ago. The jump in profit on a per tonne basis was more or less along expected lines, given the increase in realizations. "Besides, the reduction in net debt by about ?2,000 crore is a key positive," said Binod Modi, analyst at Reliance Securities Ltd.
Graphic by Santosh Sharma/Mint
What also impressed analysts is the nimble-footed integration of the recently merged cement assets of Nathdwara and Century, which was a concern on the Street.
Kunal Shah, analyst (institutional equities) at Yes Securities (India) Ltd, said: "The company has proved its ability of asset integration. Century’s cement assets were ramped up to 79% capacity utilization in December, even as they operated Nathdwara generating an Ebitda of ?1,500 per tonne."
Looks like the demand weakness mirrored in weak sales during the quarter was masked by the deft integration and synergies derived from these acquired assets. This drove UltraTech’s stock up by 2.6% to ?4,643 after the Q3 results were declared on Friday.
Brand transition from Century to UltraTech, which is 55% complete, is likely to touch 80% by September 2020. A report by Jefferies India Pvt. Ltd highlights that the Ebitda per tonne for premium brands is about ?5-10 higher per bag than the average (A cement bag weighs 50kg). Of course, with competition increasing in the arena, it remains to be seen how brand premiumization in the cement industry will pan out. UltraTech Cement scores well among peers here.
However, there are road bumps ahead for the cement sector and for UltraTech. Falling gross domestic product growth, fiscal slippages and lower budgetary allocation to infrastructure sector are making industry houses jittery on growth. Although UltraTech’s management is confident that cement demand is looking up, sustainability and pricing power remains a worry for the near term.