Technology
Application of computational fluid & particle dynamics for cement industry
Published
6 years agoon
By
admin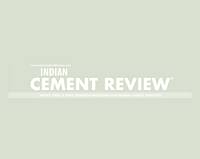
Computational Fluid Dynamics (CFD) is widely used by the global cement Industry to design the process equipment and improve performance. CFD methodology is believed to be a complex technology by the practising engineers. This article by Vivek Vitankar of FluiDimensions, Pune and Ravindra Aglave of Siemens Digital Industries Software, Houston, TX, USA aims to describe the CFD methodology in a detailed but simpler manner.
Cement production is a highly energy intensive (thermal and electrical energy) process. A lot of effort is spent by designers on a trial and error basis to address the energy and pollutant reduction issues. These efforts have helped the industry to achieve a portion the targets over a period of time. On many occasions, the gains are temporary. A scientific approach that is at a lower cost which does not disrupt production and is faster than trial and error approach to identify the problem, its root cause and provide a robust solution is desired.
Virtual process development based (VPD) on numerical models such as Computational fluid Dynamics (CFD) has emerged as a proven technology in the process industry to design and validate the process equipment, debottleneck performance, optimize operating conditions, perform detailed "what if" studies. The equipment performance depends on the operational philosophy, equipment design, the quality of raw materials and the fuel being used. That makes computational fluid dynamics as a best tool to optimize performance equipment individually.
CFD Methodology and Workflow
After identifying an issue or a problem, initial assessment can define the objective of the analysis. Once an objective of the analysis is decided, first step is to draw a three-dimensional CAD geometry based on the GA and internal drawings of the equipment. It is very critical to have the updated drawings with all the dimensions. A site visit or a meeting with designers is recommended at this early stage.
In the second step, meshing, the full scale 3D CAD is discretized into numerous small volume elements. It is in these volume elements, the Navier-Stokes equations are solved. As a general rule, more the volume elements, better is the accuracy of the solution. Figure 1 shows schematic workflow of the entire process with input requirements.
In the third step, the underlying physics and chemistry (if necessary) of the process is represented using the mathematical models available in the CFD software. For example, multiphase physics for gas-solid flow in cyclones, combustion reactions and heat transfer modes modeling in kiln and calciner, NOx reactions etc.
To simulate the problem, an experienced CFD engineer uses the right algorithms, combination of relaxation parameters, tricks of convergence. Adequate knowledge of the software, involved physics and compute resources is a precursor of such work.
The important task of analysing the results starts after the converged solution is obtained. At this stage the understanding of the process and equipment is crucial to connect the link between CFD results and process observations. Analysing overall pressure drop and collection efficiency obtained from CFD results of the cyclone is not sufficient. One needs to look into the detailed velocity contours and vectors at different locations. It is detailed analysis that leads to pinpoint the issues in the performance. Once the issues are identified, most of the times the solution to the problem emerges.
Figure 1. Workflow involved in CFD Analysis
At this stage, we recommend to have discussion with the operations/design team as they can have limitations to implement a theoretically perfect design solution. There could be structural issues, access to the location to carry out implementation or operational challenges.
As the design solution is accepted, the delivery process starts. Delivery package includes engineering design drawings highlighting the changes in the original drawings, fabrication drawings along with the material of construction, total quantity of the material needed and benefits that would be achieved. During the implementation process, CFD engineer needs to guide the fabrication and implementation teams and ensure that the implementation is done in a right way.
Table 1: Benefits achieved in Cement Industry using CFD modeling
*Typical inputs required are drawing details including GA drawings, assembly drawings, refractory drawings, all internals, clearly marked location and sizes of all inlets and outlets. Operating conditions like gas flow rate, temperature, pressure, gas composition, fuel compostion, combustion characteristics etc.
Practices followed at FluiDimensions:
We follow the entire process described above and analyse the performance as per the design and operating conditions with respect to the objective statement. Detailed analysis tools of STAR-CCM+ gives the insight of root cause of the design or operation issue. (for example in Cyclone, Pressure drop and collection efficiency, for Calciner, O2, CO, NOx level at exit, temperature, extent of combustion, residence time distribution, regions of high and low temperature, reducing zones etc). Siemens Simcenter STAR-CCM+ offers a unique feature of design exploration that allows faster optimization over the design or operating variables.
One very important aspect of CFD simulations at FluiDimensions is model validation. It is very important that the CFD results are validated before a design solution is proposed. However, it is not possible to measure detailed velocity, temperature, species concentration at different locations in the industrial setups. Hence, we validate our CFD models and solution methodologies using the experimental data in the published literature. This approach gives us the confidence to solve industrial problems. For example, figure 2 shows comparison of axial velocity and temperature in the IFRF Coal combustion study1 and figure 3 shows the comparison of velocity profiles in cyclone2
Figure 2. Comparison of axial velocity and Temperature with the experimental data [1]
Figure 3. Comparison of tangential velocity and axial velocity with experimental data [2].
The following sections describe few case studies to get better insight of CFD process and value addition.
Case Study I: Performance Improvement of a Cyclone Separator
Based on the GA drawings, a full three dimension actual scale CAD geometry is drawn using CAD features of Siemens Simcenter STAR-CCM+. Next step is to create a polyhedral mesh with required quality criteria. Reynolds stress turbulence model was used as the flow is highly swirling in cyclones. Lagrangian Multiphase model is used to track solid particles in the cyclone. Using the information provided (like gas flow rate, temperature, pressure and solid loading % solids of gas flow rate and particle size distribution), base case simulation were carried out for the gas-solid flow using Simcenter STAR-CCM+. The software gave converged results in @5000 iterations in 8-10 hours using 32 cores. Figure 4 presents the fine polyhedral mesh, velocity and pressure contour obtained from the simulation. The pressure drop and the collection efficiency (87%) were found to match with the plant observation. To improve the collection efficiency, various design modifications (increase dip tube height, increasing roof height, tapered inlet, change involute size etc) were considered for simulation. We used the design exploration feature of STAR-CCM+. This feature automates the whole simulation process leading to rapid optimized solution. In other words, arrive at the solution faster by an automated trial and error method but in virtual space! After simulations, the pressure drop and collection efficiency was noted for every design arriving at optimized design. All the design changes and simulations take over 20-25 days which otherwise would take 30-40 days
Case Study II: Duct design optimization: Cement plants have large ducts to transport air, generally laden with particles from PF Fan, Coal Mill Fan Bag house, ESP, Coal Mills etc. Due to the space constraint, the ducting circuit ends up in multiple sharp bends leading to high pressure drops. Baffles are frequently used to obtain a uniform flow. STAR-CCM+ has been used with an automated work flow to investigate a series of baffle designs in ducts giving most uniform air flow with least pressure drop. In this instance, we used design explorer to rapidly analyse the effects of two design parameters: the number of number of turning vanes (anywhere from 1 to 10) and the dimension of each turning vane’s common radius (from 0.10 meters to 0.50 meters). Figure 5 summarizes the pressure profile for different scenarios.
Figure 5. Duct design optimization
In another case, CFD modelling using STAR-CCM+ was used for a LaFarge cement plant [3] to find an
Before
After
optimum design of a supply duct to an electrostatic precipitator [4]. By increasing the flow uniformity reduced the peak air velocity causing less. This resulted in reduction of number of cleaning cycles per day by 90% and a savings of up to $40,000 per month in maintenance & repair costs [5]. Figure 6 shows the base and modified design.
Figure 6. CFD results of duct to an ESP
Case Study III: Rotary kiln case study: Rotary Kilns consume significant amount of energy and release more than 25 tons of nitrogen oxides (NOx) per year [4] due to the high flame temperatures that result in formation of NOx. Stringent emissions control requirements are forcing operators to develop new and cost effective ways of minimizing/controlling emissions.
The most common post combustion control approaches include Selective Non-Catalytic Reduction (SNCR), and Selective Catalytic Reduction (SCR). The SNCR process involves the injection of ammonia in the form of ammonia water or urea solution in the flue-gas, at a suitable temperature to convert NOx to N2. While the SCR process adds ammonia or urea in the presence of a catalyst to selectively reduce NOx emissions from the exhaust gases.
An SNCR system’s performance in cement kilns depends on the temperature, residence time, reagent injection rate, turbulence or the degree of mixing between the injected reagent and the combustion gases, oxygen content, and baseline NOx levels in the kiln. The process is relatively ineffective at temperatures below 800oC and above 1150oC. At temperatures below 800oC, excessive amounts of ammonia are released to the atmosphere through the stack because of incomplete reagent dissociation, and at higher temperature, the reactions favour NOx formation and significantly higher reagent injection rates are required to meet the target NOx levels. The SNCR system is typically installed in the preheater of a lime kiln or the pre-calciner of a cement kilns.
The use of Computational Fluid Dynamics (CFD) to study the design and improve the performance of these systems is a cost effective alternative to expensive and time-consuming field tests. One recent case study of interest is that done by KFS [5] in which combustion and SNCR modeling of a rotary kiln with preheater in a lime plant was carried out in step wise procedure using Simcenter STAR-CCM+.
Step 1: 3D simulation of the rotary kiln with models for turbulence, chemistry, and heat transfer for the gas phase, which is coupled to an in-house, developed and validated, bed chemistry model to represent the transport and heat transfer of solids in the kiln
Figure 7. Illustration of gas phase and bed chemistry coupling
Step 2: Mapping of the exhaust gas temperature, velocity, turbulence and species profiles to be used as the inlet conditions for the 3D simulation of the preheater.
Figure 8. Flame profiles with different fuel composition
Step 3. Modeling the SNCR process in the preheater by simulating the urea injection and the subsequent reactions to obtain information related to system performance such as mixing profiles, NOx reduction, NH3 slippage etc. The two-step urea decomposition via the thermolysis and hydrolysis pathways are modeled, and the subsequent NOx reduction based on the 7-step reduced kinetic mechanism is used in the simulations.
Useful insights about the effectiveness of mixing, the gas temperatures encountered in the preheater, and the resulting NOx reduction for a given urea injection rate at specified locations can be obtained from the 3D CFD simulations.
The injector positions and the total number of injectors were varied to identify an optimum configuration that could achieve the desired NOx reduction with minimum urea slippage. The best design resulted in approximately 60% NOx reduction of the baseline furnace value with a urea slippage of less than 1 ppm.
The effect of urea flow rate on NOx reduction efficiency for the optimum configuration can then be studied and compared to field data after the installation. In one example the correct trend was captured for the percentage reduction in NOx by the CFD results as the urea flow rate was increased.
Figure 9. Urea injection location and calculated NOx distribution
The results from these studies demonstrate that CFD is a useful tool to help design and optimize the kiln and the SNCR system for effective NOx control. The potential savings associated with operating a thermally efficient kiln, and a well-controlled SNCR process with minimum urea slippage could be significant. The possibilities are endless! CFD along with a carefully planned design exploration study can be used to gain useful insights into system performance and design whether it is a rotary kiln, a cyclone separator, ESP, Calciner, Ducts, Fans, at a fraction of the time and cost that it takes to actually build and test prototypes of these systems.
References
1.Peters and Weber, "Mathematical Modelling of a 2.4 MW Swirling Pulverised Coal Flame", Combustion Science and Technology, 1997,Vol. 122, page 131-182
2.M. D. Slack, R. O. Prasad, A. Bakker, F. Boysan "Advances in Cyclone Modelling Using Unstructured Grids", TransIChemE, Vol. 78, Part A, November 2000, page 1098- 1104.
3.Porter, M. and TroutComputational Fluid Dynamics (CFD) is widely used by the global cement Industry to design the process equipment and improve performance. CFD methodology is believed to be a complex technology by the practising engineers. This article by Vivek Vitankar of FluiDimensions, Pune and Ravindra Aglave of Siemens Digital Industries Software, Houston, TX, USA aims to describe the CFD methodology in a detailed but simpler manner.
Cement production is a highly energy intensive (thermal and electrical energy) process. A lot of effort is spent by designers on a trial and error basis to address the energy and pollutant reduction issues. These efforts have helped the industry to achieve a portion the targets over a period of time. On many occasions, the gains are temporary. A scientific approach that is at a lower cost which does not disrupt production and is faster than trial and error approach to identify the problem, its root cause and provide a robust solution is desired.
Virtual process development based (VPD) on numerical models such as Computational fluid Dynamics (CFD) has emerged as a proven technology in the process industry to design and validate the process equipment, debottleneck performance, optimize operating conditions, perform detailed "what if" studies. The equipment performance depends on the operational philosophy, equipment design, the quality of raw materials and the fuel being used. That makes computational fluid dynamics as a best tool to optimize performance equipment individually.
CFD Methodology and Workflow
After identifying an issue or a problem, initial assessment can define the objective of the analysis. Once an objective of the analysis is decided, first step is to draw a three-dimensional CAD geometry based on the GA and internal drawings of the equipment. It is very critical to have the updated drawings with all the dimensions. A site visit or a meeting with designers is recommended at this early stage.
In the second step, meshing, the full scale 3D CAD is discretized into numerous small volume elements. It is in these volume elements, the Navier-Stokes equations are solved. As a general rule, more the volume elements, better is the accuracy of the solution. Figure 1 shows schematic workflow of the entire process with input requirements.
In the third step, the underlying physics and chemistry (if necessary) of the process is represented using the mathematical models available in the CFD software. For example, multiphase physics for gas-solid flow in cyclones, combustion reactions and heat transfer modes modeling in kiln and calciner, NOx reactions etc.
To simulate the problem, an experienced CFD engineer uses the right algorithms, combination of relaxation parameters, tricks of convergence. Adequate knowledge of the software, involved physics and compute resources is a precursor of such work.
The important task of analysing the results starts after the converged solution is obtained. At this stage the understanding of the process and equipment is crucial to connect the link between CFD results and process observations. Analysing overall pressure drop and collection efficiency obtained from CFD results of the cyclone is not sufficient. One needs to look into the detailed velocity contours and vectors at different locations. It is detailed analysis that leads to pinpoint the issues in the performance. Once the issues are identified, most of the times the solution to the problem emerges.
Figure 1. Workflow involved in CFD Analysis
At this stage, we recommend to have discussion with the operations/design team as they can have limitations to implement a theoretically perfect design solution. There could be structural issues, access to the location to carry out implementation or operational challenges.
As the design solution is accepted, the delivery process starts. Delivery package includes engineering design drawings highlighting the changes in the original drawings, fabrication drawings along with the material of construction, total quantity of the material needed and benefits that would be achieved. During the implementation process, CFD engineer needs to guide the fabrication and implementation teams and ensure that the implementation is done in a right way.
Table 1: Benefits achieved in Cement Industry using CFD modeling
*Typical inputs required are drawing details including GA drawings, assembly drawings, refractory drawings, all internals, clearly marked location and sizes of all inlets and outlets. Operating conditions like gas flow rate, temperature, pressure, gas composition, fuel compostion, combustion characteristics etc.
Practices followed at FluiDimensions:
We follow the entire process described above and analyse the performance as per the design and operating conditions with respect to the objective statement. Detailed analysis tools of STAR-CCM+ gives the insight of root cause of the design or operation issue. (for example in Cyclone, Pressure drop and collection efficiency, for Calciner, O2, CO, NOx level at exit, temperature, extent of combustion, residence time distribution, regions of high and low temperature, reducing zones etc). Siemens Simcenter STAR-CCM+ offers a unique feature of design exploration that allows faster optimization over the design or operating variables.
One very important aspect of CFD simulations at FluiDimensions is model validation. It is very important that the CFD results are validated before a design solution is proposed. However, it is not possible to measure detailed velocity, temperature, species concentration at different locations in the industrial setups. Hence, we validate our CFD models and solution methodologies using the experimental data in the published literature. This approach gives us the confidence to solve industrial problems. For example, figure 2 shows comparison of axial velocity and temperature in the IFRF Coal combustion study1 and figure 3 shows the comparison of velocity profiles in cyclone2
Figure 2. Comparison of axial velocity and Temperature with the experimental data [1]
Figure 3. Comparison of tangential velocity and axial velocity with experimental data [2].
The following sections describe few case studies to get better insight of CFD process and value addition.
Case Study I: Performance Improvement of a Cyclone Separator
Based on the GA drawings, a full three dimension actual scale CAD geometry is drawn using CAD features of Siemens Simcenter STAR-CCM+. Next step is to create a polyhedral mesh with required quality criteria. Reynolds stress turbulence model was used as the flow is highly swirling in cyclones. Lagrangian Multiphase model is used to track solid particles in the cyclone. Using the information provided (like gas flow rate, temperature, pressure and solid loading % solids of gas flow rate and particle size distribution), base case simulation were carried out for the gas-solid flow using Simcenter STAR-CCM+. The software gave converged results in @5000 iterations in 8-10 hours using 32 cores. Figure 4 presents the fine polyhedral mesh, velocity and pressure contour obtained from the simulation. The pressure drop and the collection efficiency (87%) were found to match with the plant observation. To improve the collection efficiency, various design modifications (increase dip tube height, increasing roof height, tapered inlet, change involute size etc) were considered for simulation. We used the design exploration feature of STAR-CCM+. This feature automates the whole simulation process leading to rapid optimized solution. In other words, arrive at the solution faster by an automated trial and error method but in virtual space! After simulations, the pressure drop and collection efficiency was noted for every design arriving at optimized design. All the design changes and simulations take over 20-25 days which otherwise would take 30-40 days
Case Study II: Duct design optimization: Cement plants have large ducts to transport air, generally laden with particles from PF Fan, Coal Mill Fan Bag house, ESP, Coal Mills etc. Due to the space constraint, the ducting circuit ends up in multiple sharp bends leading to high pressure drops. Baffles are frequently used to obtain a uniform flow. STAR-CCM+ has been used with an automated work flow to investigate a series of baffle designs in ducts giving most uniform air flow with least pressure drop. In this instance, we used design explorer to rapidly analyse the effects of two design parameters: the number of number of turning vanes (anywhere from 1 to 10) and the dimension of each turning vane’s common radius (from 0.10 meters to 0.50 meters). Figure 5 summarizes the pressure profile for different scenarios.
Figure 5. Duct design optimization
In another case, CFD modelling using STAR-CCM+ was used for a LaFarge cement plant [3] to find an
Before
After
optimum design of a supply duct to an electrostatic precipitator [4]. By increasing the flow uniformity reduced the peak air velocity causing less. This resulted in reduction of number of cleaning cycles per day by 90% and a savings of up to $40,000 per month in maintenance & repair costs [5]. Figure 6 shows the base and modified design.
Figure 6. CFD results of duct to an ESP
Case Study III: Rotary kiln case study: Rotary Kilns consume significant amount of energy and release more than 25 tons of nitrogen oxides (NOx) per year [4] due to the high flame temperatures that result in formation of NOx. Stringent emissions control requirements are forcing operators to develop new and cost effective ways of minimizing/controlling emissions.
The most common post combustion control approaches include Selective Non-Catalytic Reduction (SNCR), and Selective Catalytic Reduction (SCR). The SNCR process involves the injection of ammonia in the form of ammonia water or urea solution in the flue-gas, at a suitable temperature to convert NOx to N2. While the SCR process adds ammonia or urea in the presence of a catalyst to selectively reduce NOx emissions from the exhaust gases.
An SNCR system’s performance in cement kilns depends on the temperature, residence time, reagent injection rate, turbulence or the degree of mixing between the injected reagent and the combustion gases, oxygen content, and baseline NOx levels in the kiln. The process is relatively ineffective at temperatures below 800oC and above 1150oC. At temperatures below 800oC, excessive amounts of ammonia are released to the atmosphere through the stack because of incomplete reagent dissociation, and at higher temperature, the reactions favour NOx formation and significantly higher reagent injection rates are required to meet the target NOx levels. The SNCR system is typically installed in the preheater of a lime kiln or the pre-calciner of a cement kilns.
The use of Computational Fluid Dynamics (CFD) to study the design and improve the performance of these systems is a cost effective alternative to expensive and time-consuming field tests. One recent case study of interest is that done by KFS [5] in which combustion and SNCR modeling of a rotary kiln with preheater in a lime plant was carried out in step wise procedure using Simcenter STAR-CCM+.
Step 1: 3D simulation of the rotary kiln with models for turbulence, chemistry, and heat transfer for the gas phase, which is coupled to an in-house, developed and validated, bed chemistry model to represent the transport and heat transfer of solids in the kiln
Figure 7. Illustration of gas phase and bed chemistry coupling
Step 2: Mapping of the exhaust gas temperature, velocity, turbulence and species profiles to be used as the inlet conditions for the 3D simulation of the preheater.
Figure 8. Flame profiles with different fuel composition
Step 3. Modeling the SNCR process in the preheater by simulating the urea injection and the subsequent reactions to obtain information related to system performance such as mixing profiles, NOx reduction, NH3 slippage etc. The two-step urea decomposition via the thermolysis and hydrolysis pathways are modeled, and the subsequent NOx reduction based on the 7-step reduced kinetic mechanism is used in the simulations.
Useful insights about the effectiveness of mixing, the gas temperatures encountered in the preheater, and the resulting NOx reduction for a given urea injection rate at specified locations can be obtained from the 3D CFD simulations.
The injector positions and the total number of injectors were varied to identify an optimum configuration that could achieve the desired NOx reduction with minimum urea slippage. The best design resulted in approximately 60% NOx reduction of the baseline furnace value with a urea slippage of less than 1 ppm.
The effect of urea flow rate on NOx reduction efficiency for the optimum configuration can then be studied and compared to field data after the installation. In one example the correct trend was captured for the percentage reduction in NOx by the CFD results as the urea flow rate was increased.
Figure 9. Urea injection location and calculated NOx distribution
The results from these studies demonstrate that CFD is a useful tool to help design and optimize the kiln and the SNCR system for effective NOx control. The potential savings associated with operating a thermally efficient kiln, and a well-controlled SNCR process with minimum urea slippage could be significant. The possibilities are endless! CFD along with a carefully planned design exploration study can be used to gain useful insights into system performance and design whether it is a rotary kiln, a cyclone separator, ESP, Calciner, Ducts, Fans, at a fraction of the time and cost that it takes to actually build and test prototypes of these systems.
References
1.Peters and Weber, "Mathematical Modelling of a 2.4 MW Swirling Pulverised Coal Fl
Economy & Market
Hindalco Buys US Speciality Alumina Firm for $125 Million
Published
2 months agoon
June 25, 2025By
admin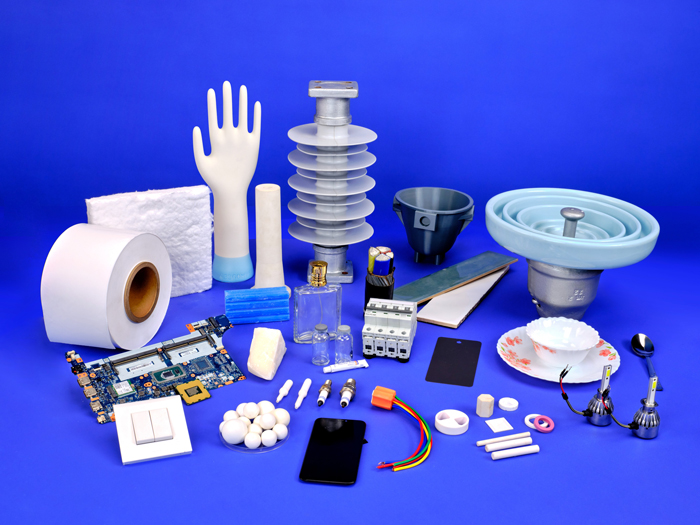
This strategic acquisition marks a significant investment in speciality alumina, a key step by Aditya Birla Group’s metals flagship towards becoming future-ready by scaling its high-value, technology-led materials portfolio.
Hindalco Industries, the world’s largest aluminium company by revenue and the metals flagship of the $28 billion Aditya Birla Group, has announced the acquisition of a 100 per cent equity stake in US-based AluChem Companies—a prominent manufacturer of speciality alumina—for an enterprise value of $125 million. The transaction will be executed through Aditya Holdings, a wholly owned subsidiary.
This acquisition represents a pivotal investment in speciality alumina and advances Hindalco’s strategy to expand its high-value, technology-led materials portfolio.
Hindalco’s speciality alumina business, a key pillar of its value-added strategy, has delivered consistent double-digit growth in recent years. It has emerged as a high-growth, high-margin vertical within the company’s portfolio. As speciality alumina finds expanding applications across electric mobility, semiconductors, and precision ceramics, the deal positions Hindalco further up the innovation curve, enabling next-generation alumina solutions and value-accretive growth.
Kumar Mangalam Birla, Chairman of Aditya Birla Group, called the acquisition an important step in their global strategy to build a leadership position in value-added, high-tech materials.
“Our strategic foray into the speciality alumina space will not only accelerate the development of future-ready, sustainable solutions but also open new pathways to pursue high-impact growth opportunities. By integrating advanced technologies into our value chain, we are reinforcing our commitment to self-reliance, import substitution, and building scale in innovation-led businesses.”
Ronald P Zapletal, Founder, AluChem Companies, said the partnership with Hindalco would provide AluChem the ability and capital to scale up faster and build scale in North America.
“AluChem will benefit from their world-class sustainability and safety standards and practices, access to integrated operations and a consistent, reliable raw material supply chain. Their ability to leverage R&D capabilities and a talented workforce adds tremendous value to our innovation pipeline, helping drive market expansion beyond North America.”
An Eye on the Future
The global speciality alumina market is projected to grow significantly, with rising demand for tailored solutions in sectors such as ceramics, electronics, aerospace, and medical applications. Hindalco currently operates 500,000 tonnes of speciality alumina capacity and aims to scale this up to 1 million tonnes by FY2030.
Commenting on the development, Satish Pai, Managing Director, Hindalco Industries, said the deal reinforced their commitment to innovation and global expansion.
“As alumina gains increasing relevance in critical and clean-tech sectors, AluChem’s advanced chemistry capabilities will significantly enhance our ability to serve these fast-evolving markets. Importantly, it deepens our high-value-added portfolio with differentiated products that drive profitability and strengthen our global competitiveness.”
AluChem adds a strong North American presence to Hindalco’s portfolio, with an annual capacity of 60,000 tonnes across three advanced manufacturing facilities in Ohio and Arkansas. The company is a long-standing supplier of ultra-low soda calcined and tabular alumina, materials prized for their thermal and mechanical stability and widely used in precision engineering and high-performance refractories.
Saurabh Khedekar, CEO of the Alumina Business at Hindalco Industries, said the acquisition unlocked immediate synergies, including market access and portfolio diversification.
“Hindalco plans to work with AluChem’s high performance technology solutions and scale up production of ultra-low soda alumina products to drive a larger global market share.”
The transaction is expected to close in the upcoming quarter, subject to customary closing conditions and regulatory approvals.

As India’s cement industry heads for unprecedented growth, the importance of smart, sustainable and strategic lubrication is gaining ground. From reducing downtime and enhancing energy efficiency to enabling predictive maintenance, lubricants are transforming plant performance. ICR explores how advanced lubrication solutions are becoming critical enablers of reliability, resilience and environmental stewardship in the cement sector.
The Indian cement industry, a cornerstone of the nation’s infrastructure development, is experiencing significant growth. In 2023, India’s cement production reached 374.55 million tonnes, marking a 6.83 per cent year-on-year growth. Projections indicate that the market size will expand from 3.96 billion tonnes in 2023 to 5.99 billion tonnes by 2032, reflecting a compound annual growth rate (CAGR) of 4.7 per cent during 2024-32. This expansion underscores the increasing demand for efficient and sustainable operations within the sector.
In cement manufacturing, equipment such as kilns, crushers, vertical mills, ball mills, conveyors and fans operate under extreme temperatures, heavy loads and high dust exposure. These demanding conditions make proper lubrication not just essential, but mission-critical. Selecting the right type of lubricant and maintaining an effective lubrication regime can drastically improve machine uptime, reduce maintenance costs, and enhance plant safety. In many cases, lubricant-related failures account for a significant proportion of unplanned downtime, underscoring the value of a well-structured lubrication strategy.
The Indian cement sector is also undergoing a technological transformation, with increasing emphasis on automation, predictive maintenance and energy efficiency. In this evolving landscape, lubricants are no longer just consumables—they are enablers of performance, longevity and sustainability. With the growing availability of advanced lubricants and condition-monitoring technologies, Indian cement plants have the opportunity to optimise their lubrication practices in line with global standards. Additionally, tightening environmental regulations and sustainability goals are driving the shift toward eco-friendly lubricants and responsible usage practices, making lubrication management a key factor in both operational and environmental performance.
As the industry moves forward, there is a growing realisation that lubrication excellence can be a competitive differentiator. This article explores the critical role of lubricants in cement manufacturing, the latest technological advancements, the environmental considerations shaping lubricant use, and the challenges and opportunities for cement producers in India aiming to maximise equipment reliability and operational efficiency.
The role of lubricants in cement manufacturing
Cement manufacturing involves heavy-duty machinery operating under extreme conditions—high temperatures, heavy loads and continuous operations. Lubricants are essential in minimising friction, reducing wear and tear, and preventing equipment failures. Proper lubrication ensures that components such as kilns, crushers and grinding mills function optimally, thereby reducing downtime and maintenance costs.
Moreover, the integration of advanced lubrication technologies has enabled predictive maintenance strategies. By monitoring lubricant conditions, operators can anticipate equipment issues before they escalate, allowing for timely interventions and uninterrupted production cycles.
“Lubricants play a crucial role in enhancing the efficiency and reliability of cement plant operations. High-performance lubricants reduce friction and wear in critical machinery such as crushers, kilns, mills, and conveyors, ensuring smoother operation and extending equipment life. By minimising mechanical breakdowns and unplanned downtime, they contribute to consistent production and lower maintenance costs. Additionally, specialised lubricants designed to withstand high temperatures, heavy loads, and dusty environments help maintain optimal performance under demanding conditions. Proper lubrication also improves energy efficiency by reducing power loss due to friction. In essence, the right lubrication strategy not only enhances equipment reliability and operational uptime but also supports overall cost-effectiveness and productivity in cement manufacturing,” says Hiten Ved, Sales Head, Royal Petro Specialities.
In addition to enhancing equipment longevity, lubricants are pivotal in ensuring uninterrupted production cycles. Cement manufacturing is a 24/7 operation, and any unexpected downtime due to mechanical failure can lead to significant financial losses. Lubricants with high thermal stability and oxidation resistance prevent the breakdown of oil films under intense heat, especially in applications like rotary kilns, vertical roller mills and clinker coolers. By reducing the likelihood of equipment seizures or breakdowns, these lubricants act as silent enablers of plant reliability and uptime.
Gaurav Mathur, Director and Chief Executive Officer, Global Technical Services, says, “Wall paintings in tombs show workers using water to move statues, indicating early recognition of lubrication. By 1400 BC, animal fat was used to lubricate chariot axles, ever since then mankind has been relentlessly working to improvise the efficiency of lubricants. Tribological advancements have propelled industrialisation in the world. Machines working in demanding environment need better performance, however merely just better lubricant that is made from highly refined base oils is not good enough. Mineral and synthetic base oils and advanced additives chemistry have given birth to advanced lubricants. These lubricants have better performance characteristics and longer service life.”
“However, the way lubrication is done is more critical and if lubrication is not performed in a proper way, highest performing lubricants would also under perform compared to the lowest specification product. Total Lubrication Management has to be implemented for better machine reliability, equipment availability and lower down time. Implementation of TLM has paid rich dividends in the industry. Pillars of TLM being, contamination free lubrication, regular testing of lubricants to access the lubricant and machine condition and regeneration of lubricants,” he adds.
Lubricants contribute directly to energy efficiency. Friction losses within rotating equipment can account for up to 30 per cent of the total energy consumption in certain plant areas. Advanced synthetic lubricants, with low traction coefficients and superior film strength, reduce this internal resistance, thus improving mechanical efficiency and lowering the plant’s overall energy footprint. As Indian cement plants pursue energy benchmarking and ISO 50001 certifications, the use of high-performance lubricants becomes an integral strategy in achieving energy conservation goals.
“The cement industry has many lubrication points that require NLGI Grade 2 grease that can be used in high temperature applications. These may include bearings on vibrating screens and roller mills; rotating joints on grinding units; and various shafts, pivots, and metal to metal contact points found throughout the plant. CorrLube™ VpCI® Lithium EP Grease has a dropping point of 360 °F (182 °C), allowing it to be used in a broad range of temperatures. For areas that need a slightly harder grease of NLGI Grade 3, EcoLine® Biobased Grease offers a
similar dropping point of 365 °F (185 °C), explain Julie Holmquist, Marketing Content Writer,
Cortec Corporation.
Market dynamics: growth and trends
The Indian industrial lubricants market was valued at $13.05 billion in 2024 and is projected to reach $ 20.72 billion by 2033, growing at a CAGR of 4.12 per cent. This growth is driven by the expanding industrial sector, increased mechanisation, and the adoption of advanced machinery requiring specialised lubricants.
In the cement sector specifically, the demand for high-performance lubricants is rising. The lubricants for cement market are estimated to be $ 2.5 billion in 2024 and is expected to reach $ 3.9 billion by 2033, at a CAGR of 5.3 per cent from 2026 to 2033. This surge is attributed to the need for lubricants that can withstand harsh operating conditions and enhance equipment reliability.
Advancements in lubrication technology
Recent years have witnessed significant advancements in lubrication technology tailored for the cement industry. Synthetic lubricants, known for their superior thermal stability and longer service life, are increasingly being adopted. These lubricants perform effectively under extreme temperatures and heavy loads, common in cement manufacturing processes.
Additionally, the development of bio-based lubricants offers environmentally friendly alternatives without compromising performance. These lubricants, derived from renewable sources, reduce the environmental footprint and align with global sustainability goals. Their biodegradability and low toxicity make them suitable for applications where environmental considerations are paramount.
Smart lubrication systems are another breakthrough in the cement industry. These systems use IoT-enabled sensors and controllers to monitor lubricant condition in real time—tracking parameters such as viscosity, temperature, contamination levels and usage. This data is integrated into plant maintenance software to automate lubricant replenishment and alert operators to potential failures. Predictive lubrication ensures that each component receives the right amount of lubricant at the right time, minimising waste, reducing manual intervention, and extending machinery life.
“Many VpCI® products can be applied to surfaces with minimal pre-cleaning, and the protective VpCI® layer typically does not need to be removed before equipment is put back into service. VpCI® ‘s save significant labor, time, and associated costs compared to methods that require extensive surface preparation (e.g., sandblasting) and post-application cleaning or degreasing. This allows for faster startup after maintenance,” elaborates Ana Juraga, Content Writer, Cortec Corporation.
Furthermore, Original Equipment Manufacturers (OEMs) and lubricant suppliers are collaborating to develop application-specific lubricants tailored to the unique operating conditions of cement manufacturing units. For example, gear oils designed for high-load kilns or open gear systems now come with superior Extreme Pressure (EP) additives and anti-wear properties to cope with shock loading and variable speed operations. These co-developed solutions not only enhance mechanical reliability but also ensure compatibility with diverse materials used in modern cement equipment, ensuring peak performance in both greenfield and brownfield plants.
Sustainability and environmental considerations
The cement industry is under increasing pressure to reduce its environmental impact. Lubricants contribute to this goal by enhancing energy efficiency and reducing emissions. High-quality lubricants decrease friction, leading to lower energy consumption and, consequently, reduced greenhouse gas emissions.
Furthermore, the use of long-life lubricants minimises the frequency of oil changes, thereby reducing waste generation and disposal issues. The shift towards bio-based and recyclable lubricants also supports circular economy principles, promoting resource efficiency and environmental stewardship.
A report by Klüber Lubrication India suggests that sustainability continues to be a key focus for industries, the Securities and Exchange Board of India (SEBI) has mandated Business Responsibility and Sustainability Reporting (BRSR) for the top 1,000 listed companies. This framework requires organisations to disclose their environmental, social and governance (ESG) initiatives, including energy conservation, emission reductions and resource optimisation. Beyond compliance, BRSR reporting allows companies to showcase their sustainability leadership and build investor confidence. Organisations that proactively address sustainability challenges are better positioned to attract long-term investors, secure financing, and maintain a competitive advantage in an evolving regulatory landscape.
The report also states that their high-performance synthetic lubricants play a crucial role in helping cement manufacturers meet these regulatory requirements by enhancing energy efficiency and reducing CO2 emissions in critical machinery such as vertical roller mills (VRMs) and main gearboxes. By adopting our energy-efficient solutions, companies can strengthen their BRSR compliance while achieving tangible operational benefits.
An emerging trend in the lubricant industry is the formulation of biodegradable lubricants specifically tailored for heavy industries like cement manufacturing. These eco-friendly alternatives are made from renewable base stocks and are designed to degrade naturally without leaving behind harmful residues. In environmentally sensitive zones or operations with high spill risk, such as open gear applications or hydraulic systems exposed to the elements, biodegradable lubricants offer a sustainable solution that aligns with stricter environmental regulations and the growing emphasis on corporate social responsibility (CSR) in India’s industrial sector.
KB Mathur, Founder and Director, Global Technical Services, says, “In the world of industrial machinery, lubricating oils while essential; are often misunderstood in terms of their life cycle. When oils are used in machinery, they don’t simply ‘DIE’. Instead, they become contaminated with moisture (water) and solid contaminants like dust, dirt and wear debris. These contaminants degrade the oil’s effectiveness but do not render it completely unusable. Used lubricants can be regenerated via advanced filtration processes/systems and recharged with the use of performance enhancing additives hence restoring them. These oils are brought back to ‘As-New’ levels. This new fresher lubricating oil is formulated to carry out its specific job providing heightened lubrication and reliable performance of the assets with a view of improved machine condition. Hence, contributing to not just cost savings but leading to magnified productivity, and diminished environmental stress.”
Lubricant manufacturers are increasingly focusing on circular economy principles, offering oil analysis, filtration and recycling services that extend lubricant life and minimise waste. Used oil regeneration programs not only reduce disposal costs but also help cement plants meet regulatory norms under the Hazardous Waste Management Rules of India. This closed-loop approach not only lowers the environmental burden but also enhances economic efficiency—making sustainability a dual benefit for operational and ecological performance. As cement companies work towards science-based targets and carbon neutrality, lubricant selection and management play a more strategic role in meeting these broader sustainability commitments.
Challenges and opportunities
Despite the benefits, the adoption of advanced lubricants in the Indian cement industry faces challenges. These include the higher initial costs of synthetic and bio-based lubricants and a lack of awareness about their long-term benefits. Additionally, the integration of lubrication management systems requires investment in training and infrastructure.
However, these challenges present opportunities for innovation and collaboration. Manufacturers
can work closely with lubricant suppliers to develop customised solutions that meet specific operational needs. Moreover, government incentives and regulatory frameworks promoting sustainable practices can accelerate the adoption of advanced lubrication technologies.
Another key challenge is the limited awareness and technical training available at the plant level regarding proper lubrication practices. Many maintenance teams still rely on outdated methods such as manual greasing or fixed-interval lubrication schedules, which often lead to over-lubrication, under-lubrication or lubricant contamination. This results in premature equipment wear and higher operating costs. There is a growing need for skill development programmes and collaboration with lubricant suppliers to train technicians on best practices, condition-based monitoring, and the use of smart lubrication systems.
“Oil in the machine is like blood in the human body. There is no rotating machine that works without lubricants (liquid, semi liquid or solid). Based on the machine component, type of lubricant is used to minimise the mechanical changes in the machine. Lubricant being the product that separates two or more materials under movement. With modern machines being more and more sophisticated and tolerances being finer than before, cleanliness of Lubricants is critical, would the source of contamination be internal wear or external contamination. These contaminations rupture and compromises lubricant film, contamination particles when come in-between the fine tolerances, become cause of catastrophic failure,” expounds Gaurav Mathur.
At the same time, the industry is witnessing an opportunity to leverage digitalisation in lubrication management. Advanced lubrication tracking tools, coupled with ERP and maintenance software, can now offer real-time visibility into lubricant consumption, scheduling and health diagnostics. Integration of AI-powered analytics helps predict equipment failure based on lubricant data, enabling a shift from reactive to predictive maintenance. For Indian cement manufacturers aiming to digitise plant operations as part of Industry 4.0, lubrication is an ideal entry point that delivers immediate ROI and long-term gains in efficiency, asset life and sustainability.
Conclusion
As the Indian cement industry continues its trajectory of growth, the role of high-performance lubricants in ensuring operational reliability, energy efficiency and cost savings cannot be overstated. From kilns and crushers to ball mills and gearboxes, modern lubrication solutions are critical in
reducing downtime and maximising equipment lifespan. With rising demand and increased production pressures, cement plants must adopt a proactive approach to lubrication management—viewing it not as a routine maintenance task, but as a strategic pillar of plant performance.
Recent advancements in lubricant technology, such as synthetic formulations, nano-additives, and smart dispensers, have opened new avenues for boosting equipment efficiency and longevity. Digital tools and IoT-based systems now allow plant operators to monitor lubricant condition in real time, enabling predictive maintenance and minimising the risk of failure. As cement manufacturers increasingly pursue digital transformation and automation under Industry 4.0 frameworks, lubrication systems must be seamlessly integrated into broader asset management strategies.
At the same time, sustainability imperatives are reshaping lubrication choices. There is growing emphasis on biodegradable lubricants, optimised lubricant consumption, and environmentally responsible disposal practices. Overcoming challenges such as limited awareness, inconsistent maintenance practices, and cost sensitivity will require collaboration between lubricant manufacturers, OEMs and cement producers. The opportunities, however, are substantial—by aligning lubrication strategies with efficiency, digitalisation and sustainability goals, the Indian cement industry can significantly enhance its competitiveness and resilience in the years ahead.
– Kanika Mathur
Concrete
We consistently push the boundaries of technology
Published
4 months agoon
April 18, 2025By
admin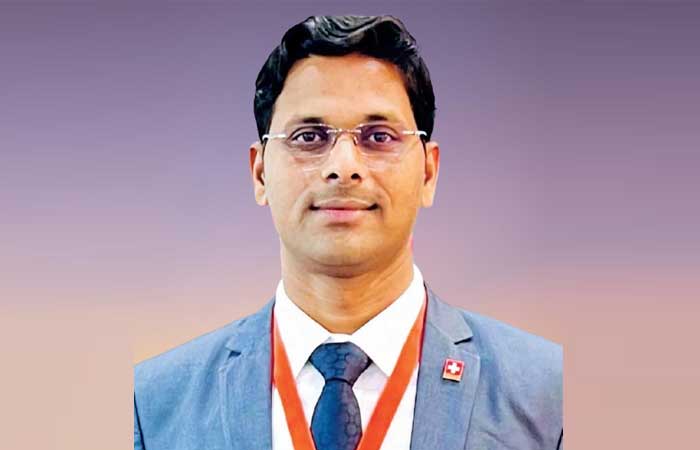
Swapnil Jadhav, Director, SIDSA Environmental, discusses transforming waste into valuable resources through cutting-edge technology and innovative process solutions.
SIDSA Environmental brings decades of experience and expertise to the important niche of waste treatment and process technologies. As a global leader that is at the forefront of sustainable waste management, the company excels in recycling, waste-to-energy solutions and alternative fuel production. In this conversation, Swapnil Jadhav, Director, SIDSA Environmental, shares insights into their advanced shredding technology, its role in RDF production for the cement industry and emerging trends in waste-to-energy solutions.
Can you give us an overview of SIDSA Environmental’s role in waste treatment and process technologies?
SIDSA is a leading innovator in the field of waste treatment and process technologies, dedicated to delivering sustainable solutions that address the growing challenges of waste management.
SIDSA is a more than 52-year-old organisation with worldwide presence and has successfully realised over 1100 projects.
Our expertise is in the engineering and development of cutting-edge systems that enable the conversion of waste materials into valuable resources. This includes recycling technologies, waste-to-energy (W2E) systems, and advanced methods for producing alternative fuels such as refuse derived fuel (RDF). The organisation prioritises environmental stewardship by integrating energy-efficient processes and technologies, supporting industrial sectors—including the cement industry—in reducing their carbon footprint. Through our comprehensive approach, we aim to promote a circular economy where waste is no longer a burden but a resource to be harnessed.
How does SIDSA Environmental’s shredding technology contribute to the cement industry, especially in the production of RDF?
SIDSA’s shredding technology is pivotal in transforming diverse waste streams into high-quality RDF. Cement kilns require fuel with specific calorific values and uniform composition to ensure efficient combustion and operational stability, and this is where our shredding systems excel. In India, we are segment leaders with more than 30 projects including over 50 equipment of varied capacity successfully realised. Some of the solutions were supplied as complete turnkey plants for high capacity AFR processing. Our esteemed client list comprises reputed cement manufacturers and chemical industries. Our technology processes various types of waste—such as plastics, textiles and industrial residues—breaking them down into consistent particles suitable for energy recovery.
Key features include:
- High efficiency: Ensures optimal throughput for large volumes of waste.
- Adaptability: Handles mixed and heterogeneous waste streams, including contaminated or complex materials.
- Reliability: Reduces the likelihood of operational disruptions in RDF production. By standardising RDF properties, our shredding technology enables cement plants to achieve greater energy efficiency while adhering to environmental regulations.
What are the key benefits of using alternative fuels like RDF in cement kilns?
The adoption of RDF and other alternative fuels offers significant advantages across environmental, economic and social dimensions:
- Environmental benefits: Cement kilns using RDF emit fewer greenhouse gases compared to those reliant on fossil fuels like coal or petroleum coke. RDF also helps mitigate the issue of overflowing landfills by diverting waste toward energy recovery.
- Economic savings: Alternative fuels are often more cost-effective than traditional energy sources, allowing cement plants to reduce operational expenses.
- Sustainability and resource efficiency: RDF facilitates the circular economy by repurposing waste materials into energy, conserving finite natural resources.
- Operational flexibility: Cement kilns designed to use RDF can seamlessly switch between different fuel types, enhancing adaptability to market conditions.
What innovations have been introduced in waste-to-energy (W2E) and recycling solutions?
SIDSA’s machinery is meticulously engineered to handle the complex requirements of processing hazardous and bulky waste.
This includes:
- Robust construction: Our equipment is designed to manage heavy loads and challenging waste streams, such as industrial debris, tires and large furniture.
- Advanced safety features: Intelligent sensors and automated controls ensure safe operation when dealing with potentially harmful materials, such as chemical waste.
- Compliance with standards: Machinery is built to adhere to international environmental and safety regulations, guaranteeing reliability under stringent conditions.
- Modular design: Allows for customisation and scalability to meet the unique needs of various waste management facilities.
How does your organisation customised solutions help cement plants improve sustainability and efficiency?
We consistently push the boundaries of technology to enhance waste management outcomes.
General innovations and new product development focus on:
- Energy-efficient shredders: These machines consume less power while maintaining high throughput, contributing to lower operational costs.
- AI-powered sorting systems: Utilise advanced algorithms to automate waste classification, increasing material recovery rates and minimising errors.
- Advanced gasification technologies: Convert waste into syngas (a clean energy source) while minimising emissions and residue.
- Closed-loop recycling solutions: Enable the extraction and repurposing of materials from waste streams, maximising resource use while reducing environmental impact.
What future trends do you foresee in waste management and alternative fuel usage in the cement sector?
Looking ahead, several trends are likely to shape the future of waste management and alternative fuels in the cement industry:
- AI integration: AI-driven technologies will enhance waste sorting and optimise RDF production, enabling greater efficiency.
- Bio-based fuels: Increased use of biofuels derived from organic waste as a renewable and low-carbon energy source.
- Collaborative approaches: Strengthened partnerships between governments, private industries and technology providers will facilitate large-scale implementation of sustainable practices.
- Circular economy expansion: The cement sector will increasingly adopt closed-loop systems, reducing waste and maximising resource reuse.
- Regulatory evolution: More stringent environmental laws and incentives for using alternative fuels will accelerate the transition toward sustainable energy solutions.
(Communication by the management of the company)