Process
WtE & co-processing will only cover part of the problem
Published
6 years agoon
By
admin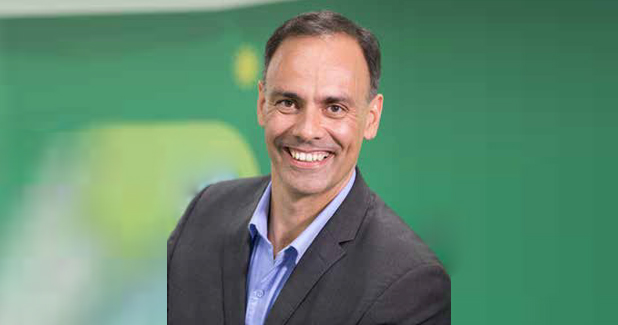
– Berthold Kren, Head of Geocycle Asia, Geocycle
Give us a brief on the activities of Geocycle in the Southeast region and then specifically in India.
Globally, Geocycle is a brand of LafargeHolcim and by far the biggest organisation in pre and co-processing waste worldwide. Geocycle manages the waste material for the LafargeHolcim cement kilns wherever it is present. Currently, we are present in over 45 countries across the globe. The SEA footprint of Geocycle is currently fully focused on Bangladesh, Philippines and India, where Geocycle supports both Ambuja Cement and ACC by managing about 1.3 to 1.4 MT (million tonne) of waste without any emission to the environment.
It was ACC and Ambuja Cement that brought co-processing into India through the LH Group in 2006. In the meantime Geocycle India has seven pre-processing platforms and 14 co-processing sites, where we process about 1 MT of waste (approximately 950 kt in 2019). We employ 160 people and offer waste management solutions to more than 600 customers. All platforms are of international standards and have state-of-the-art equipment to safely pre-process waste. Close to 3,000 tonnes of waste are safely handled every day and our Geocycle employees are knowledgeable and best in the industry. We take pride from the fact that we make the equivalent of a huge landfill disappear year after year. It’s the Geocycle knowledge and the efforts put by Ambuja Cement and ACC that contribute to a greener and cleaner India.
What has been the performance of Geocycle India in the last two years in terms of TSR and in terms of income, expenditure? What do you think about the next three years?
Since 2017, we have increased our business activity by over 60 percent, by offering a lot of services and solutions to our customers. Indeed this also happened with massive investments in previous years and still a lot more have to be invested to grow the activity. When it comes to thermal substitution rate (TSR) the development was not as we would like it to be. In 2020, we hope to reach 7 per cent but we have already ambitious plans to go to 25 percent in the coming years. The problem for average TSR rates is the geographic spread. Because Ambuja and ACCs plants are spread all over the country, the availability and feasibility of waste to be co-processed is limited in some places, which tears down the TSR rate.
In ACC, we have already seen TSR rates in kilns of 30 percent with solid waste, so we proved that it is doable also in India with the right waste mix. Unfortunately we cannot sustain this since neither the quality nor the quantity of waste is available at the moment.
Both ACC and Ambuja Cement continue to invest at several places and we expect the TSR to jump to 12 to 15 percent within the next three years and a roadmap for 25 percent TSR is already in the pipeline.
In order to run waste management sustainably, we indeed have to provide a proper payback to our shareholders. This is considered to be one of the challenges in the business. In other countries, like the Philippines, Indonesia, Malaysia and several African countries, the TSR rates are growing much faster and the business is more attractive. The payback is in acceptable ranges. In India the payback is still poor. We are glad that we started investing already eight years ago, so the burden is not too heavy. Nevertheless, we have the full support of the LH Group and Ambuja Cement and ACC, as we all see Geocycle as an important pillar to push our sustainability goals. Connecting an acknowledged waste management solution with the purpose of producing a greener cement is the perfect symbiosis.
What do you think needs to be done to improve the overall TSR numbers in the country?
I think there are three main points that need to be considered in order to boost TSR: Waste management in general: There needs to be a shift in the mindset and awareness. Neither the volume nor the composition of the waste is fully understood. Scientific studies exist, but need to be made on a broader and national scale. All this information needs to be brought into a National Indian Waste Management Plan. Then the right strategies and decisions can be made on a national level. Based on a profound understanding of the waste generation, the collection, followed by treatment and then proper disposal of waste can be decided. This is valid for segregated and unsegregated waste, recyclable or non-recyclable waste. The cities and industrial clusters are currently the burning points. It is also clear that a significant increase in waste utilisation in cement kilns and hence TSR will only happen with RDF from municipal waste.
Only 70 percent of the daily generated municipal waste gets collected and most of it (80 percent) is dumped untreated and without control which has a direct effect in causing Air, Water and Soil Pollution. This is a huge liability for future generations and a huge burden for the country. The government started off to the right direction but the legislation needs proper implementation and guidance. I am sure this will happen, but it simply takes time and a proper plan, considering existing and future capacities, broken down to states, regions and cities. This plan can initiate a proper development.
Polluter pays principle: The current waste management rules clearly established the waste hierarchy, the 3/5 R rules as well as the "polluter pays principle".
Unfortunately in India, there is still a prevailing belief that waste generates wealth for the waste generator, no matter what. It seems to be a cultural thing. The idea of a circular economy is the one to aspire for but it cannot be realised with zero infrastructure and a proper economy behind it. Proper disposal is required to reduce negative impact for the generator. The waste can contain recyclables or materials that might be repurposed, but for that the streams need to be segregated and treated. In India, the first task is to reduce waste that is dumped. The question is: How to achieve proper disposal? Trash to Cash, Waste to Wealth, Circular Economy are well known buzz phrases. These concepts need time to be developed and are based on availability of recyclable waste that is properly collected, treated and reversed back to recyclers. But this has no impact on our TSR, since we don’t utilise recyclable waste, the manual intervention would not provide enough material and would be way too expensive as well. Similar to waste-to-energy (WtE) and landfills, cement offers a sustainable solution to reduce the waste volume for the non-recyclables, though in an economical and ecological way. Managing the waste effectively is a service to the generator/customer and thus requires capital cost. It cannot come for free and it must not come for free.
The target for the society is to produce less waste. Societies will not thrive to reduce waste if they get paid for it. If you get paid for the waste that you generate, will you produce more or less?
This principle applies for every single person including the corporations, cities, or countries. For almost 40 years of waste management, the polluter pays principle has been proven in most of the countries in the western world. If there is no consequence to the behaviour, there is no improvement and definitely not on a bigger scale. A proper cost for landfilling and dumping will automatically provide economical room to develop for any other solution and drive innovation. Anything that comes in cheaper is to the benefit of the society and the economy. Establishing such a system in India is a tough task, but it has to start. All of it comes at a significant cost, but the longer we wait, the more expensive it will get. The principles of waste hierarchy and the polluters responsibility can be found in the Indian legislation already, but it is not considered.
Landfilling is not a solution, but is and will be required for a while. WtE and co-processing will only cover part of the problem and are not universal solutions either. With a proper economy behind waste management, investors will get drawn to it and innovation will be happening. A whole waste industry can develop. Unfortunately zero cost for dumping is the reality, hence there is no room to do anything with waste. Mixed fresh waste cannot go to recycling or co-processing and due to the high organic content is highly inefficient in WtE. In addition there is also a problem with distances. Whilst WtE and recyclers can settle close to the cities, the cement plants are often very far away from the cities. This generates additional cost. The total cost associated with treating the waste, making a fuel out of it and bringing it to the plant make it completely unviable for the industry to invest into co-processing. The attempts to force the industry to take waste at a cost are short sighted and are actually violating basic principles of Indian Waste Management legislation. This does not solve the problem. It is simply a cheap attempt to push the responsibility for proper waste disposal from the municipalities to the industries. This is not what the country needs. The disposal of waste needs to be well organised in the most ecological and economical lines, based on a sound collection and treatment system.
TSR will be a natural consequence if these three things happen. Proper RDF will be available, at a proper quality, and in a viable way. Whether the industry will then have to pay or get paid for using waste, will be a question of supply and demand. But currently there is no demand at all, since it is totally unviable. Hence no significant step forward in TSR.
Are you handling industrial or any hazardous waste at any of the plants under your control? Kindly provide us details.
Yes, we are handling industrial hazardous and non-hazardous waste. The industries have recognised their responsibilities and some of them are also thriving already towards a zero landfill policy. We, as Geocycle, offer a variety of services beyond standard pre- and co-processing to enable this.More than 60 per cent of our volume is industrial waste.
The fact that these customers are working with us is to optimise and reduce their waste volume on the one hand and to eliminate or reduce the landfilled volume, shows that the principles work successfully. We are not sourcing waste. We do have customers that keep coming back for the level of compliance and service that we are offering. We are selling the service of compliant waste management. In regards to hazardous waste, we do all kinds of incinerable hazardous waste, whether liquid, sludge or solid, we even do gaseous waste. We are proud to have well equipped installations to process any kind of waste. It is quite costly for ACC and Ambuja to maintain these operations. However, moving incinerable hazardous waste away from landfills is the real value proposition in the waste management industry.
Provide us with more details on the platform that has been created for handling hazardous waste.
Hazardous waste has to be handled with utmost care. We do have full scale environmental labs in every site where we pre-process hazardous waste. This is a must. You have to understand the waste and every truck needs to be tested properly before it can be treated. We have a variety of tanks and pumps for the liquid installations, impregnation pits for sludges and proper shredding and screening equipment to treat and mix the waste.
We have leachate containment and control systems, automated fire detection and fighting methods, even fire water retention basins for the worst of all cases. Gas and emission detectors as well as odour control systems are a must. But most importantly, we have the knowledge, the experience and people with the right mindset. They are by far the best in the industry. We are proud to represent a global brand and work for and with Ambuja Cement and ACC, top brands in India.
Can hazardous waste and other waste materials go together in the kiln or have to be moved separately?
There is no general rule. It depends on the type and consistency of waste. Mixing the wrong wastes can be very dangerous. This is why we spend a lot of money in monitoring consistency and qualitative analysis. Specific hazardous waste has to be fed through separate lines. Under no circumstance, it shall be mixed with raw material or coal/petcoke. Besides the uncontrolled exposure, the environmental impact could be disastrous. Mixing hazardous waste with non-hazardous waste is possible to a certain extent, but needs to be done by experts. Something I am absolutely proud to say. We have the best people in the industry in India to carry out such critical processes.
Tell us something on the pre-processing that is required for hazardous waste.
The key target for pre-processing is to make a consistent and stable fuel out of a variety of different waste streams with changing consistency, composition and properties. It is a key to understand each waste into detail. Prior to allowing a new waste arrival at our facility, we do an in-depth assessment based on the samples and a visit to the customer. We assess the risks and the way of pre-processing within our platform so as to foresee the waste. Our operations and technical experts decide which is the best route for waste through our installations and what are the impacts on the cement production and plant.
Also if required, we do customise installations for processing certain types of waste keeping safe operations, zero harm to the people and the environment as the priorities. Any step in pre-processing needs to ensure a stabilised fuel that is not interacting/changing in the course of pre and co-processing with zero negative impact on the cement quality. Again, you need real experts for that and by the way the process is the same for any kind of waste, not only the hazardous waste. At Geocycle, we take waste management and quality assurance very seriously.
What has been your experience in moving the waste across the state borders after the introduction of GST? To what extent the movement has become less painful?
Initially, when the GST concept was newly introduced which resulted in creating confusion. However over the period of time, we have gained clarity and the process is running quite well. This has also resulted in easing the "Transboundary Shipments" of waste. We have observed that, still a few states are limiting or prohibiting the "Transboundary Shipments" despite the central regulations being quite clear about that. This is actually astonishing me. Not every state has sufficient capacity and it would be in the interest of the nation to ensure that the maximum of waste is kept off from landfills. It seems that some states are not aligned with that. Regardless of whether transboundary shipments are possible or not, we will always prioritise local volumes whereas in many cases we have sufficient capacity to serve others too.
It is said that processing of any kind of waste is not a problem but the issue is of logistics and getting waste at plant at right price? How do you think the problem can be solved?
It is wrong that any kind of waste can be pre and co-processed. This is one major misperception. A cement kiln is not a waste incinerator. ACC and Ambuja ensure top quality cement to their customers. The waste that is introduced must not interfere with the quality of the cement.
As for the second statement: Yes, distance and logistics are major issues. We brought the first walking floor truck to optimise transportation and we will bring more technologies to India, but this will help only in a few specific cases. Principally, I believe that dumping/landfilling in India is too cheap. If the real cost for landfilling is factored into the price, the cost for transporting the waste to a co-processing site, as an alternative, will be less of an issue.
The prevailing cost for landfilling does not even suffice to build proper secured landfills, not even talking about financing the aftercare and closing of a landfill. People tend to forget that a landfill needs to be looked after for the next 100 years. What will happen with the landfill afterwards? Our future coming generations will pay a horrific price for this negligence. Waste needs to be segregated and then densified for transportation.
Do you think that Indian plants have been handling waste in a safe manner that will not cause harm to the society in general? Is safety standard under the existing law is adequate to take care of the communities around?
For Geocycle, I can answer these questions with absolute certainty. Yes, we have built the system and platforms along western standards and are a beacon in terms of technology. Ambuja Cement and ACC do everything technically possible to avoid any harm and our installations are above the legally required standard. All our health and safety related topics, which also include environmental harm, are monitored centrally from Switzerland with the same methodology and rules worldwide. It is safe to say that the same rules apply for Geocycle India than for Geocycle in Germany and Switzerland for instance. We work along the same set of rules and requirements operationally and organisationally. We work with organisations like GIZ and support with our knowledge to raise the standards globally and indeed also in India, we try to showcase the newest technologies.
We regularly get appraised for our work standards by the authorities and auditors. We foster a close relationship with our stakeholders and communities and indeed we reach out to them, so they understand what we do. We try to raise their awareness towards waste avoidance and indeed we also service the neighbouring communities. In general the safety standards and the regulations are good, much better than in many other countries in the region. I cannot answer the question for the whole industry though. I just can strongly recommend to them that they uphold the standards and operate with care for the employees, stakeholders and the environment. The legal standards are generally good. The right implementation though is key.
Process
Price hikes, drop in input costs help cement industry to post positive margins: Care Ratings
Published
4 years agoon
October 21, 2021By
admin
Region-wise,the southern region comprises 35% of the total cement capacity, followed by thenorthern, eastern, western and central region comprising 20%, 18%, 14% and 13%of the capacity, respectively.
The cement industry is expected to post positive margins on decent price hikes over the months, falling raw material prices and marked drop in overall production costs, said an analysis of Care Ratings.
Wholesale and retail prices of cement have increased 11.9% and 12.4%, respectively, in the current financial year. As whole prices have remained elevated in most of the markets in the months of FY20, against the corresponding period of the previous year.
Similarly, electricity and fuel cost have declined 11.9% during 9M FY20 due to drop in crude oil prices. Logistics costs, the biggest cost for cement industry, has also dropped 7.7% (selling and distribution) as the Railways extended the benefit of exemption from busy season surcharge. Moreover, the cost of raw materials, too, declined 5.1% given the price of limestone had fallen 11.3% in the same aforementioned period, the analysis said.
According to Care Ratings, though the overall sales revenue has increased only 1.3%, against 16% growth in the year-ago period, the overall expenditure has declined 3.2% which has benefited the industry largely given the moderation in sales.
Even though FY20 has been subdued in terms of production and demand, the fall in cost of production has still supported the cement industry by clocking in positive margins, the rating agency said.
Cement demand is closely linked to the overall economic growth, particularly the housing and infrastructure sector. The cement sector will be seeing a sharp growth in volumes mainly due to increasing demand from affordable housing and other government infrastructure projects like roads, metros, airports, irrigation.
The government’s newly introduced National Infrastructure Pipeline (NIP), with its target of becoming a $5-trillion economy by 2025, is a detailed road map focused on economic revival through infrastructure development.
The NIP covers a gamut of sectors; rural and urban infrastructure and entails investments of Rs.102 lakh crore to be undertaken by the central government, state governments and the private sector. Of the total projects of the NIP, 42% are under implementation while 19% are under development, 31% are at the conceptual stage and 8% are yet to be classified.
The sectors that will be of focus will be roads, railways, power (renewable and conventional), irrigation and urban infrastructure. These sectors together account for 79% of the proposed investments in six years to 2025. Given the government’s thrust on infrastructure creation, it is likely to benefit the cement industry going forward.
Similarly, the Pradhan Mantri Awaas Yojana, aimed at providing affordable housing, will be a strong driver to lift cement demand. Prices have started correcting Q4 FY20 onwards due to revival in demand of the commodity, the agency said in its analysis.
Industry’s sales revenue has grown at a CAGR of 7.3% during FY15-19 but has grown only 1.3% in the current financial year. Tepid demand throughout the country in the first half of the year has led to the contraction of sales revenue. Fall in the total expenditure of cement firms had aided in improving the operating profit and net profit margins of the industry (OPM was 15.2 during 9M FY19 and NPM was 3.1 during 9M FY19). Interest coverage ratio, too, has improved on an overall basis (ICR was 3.3 during 9M FY19).
According to Cement Manufacturers Association, India accounts for over 8% of the overall global installed capacity. Region-wise, the southern region comprises 35% of the total cement capacity, followed by the northern, eastern, western and central region comprising 20%, 18%, 14% and 13% of the capacity, respectively.
Installed capacity of domestic cement makers has increased at a CAGR of 4.9% during FY16-20. Manufacturers have been able to maintain a capacity utilisation rate above 65% in the past quinquennium. In the current financial year due to the prolonged rains in many parts of the country, the capacity utilisation rate has fallen from 70% during FY19 to 66% currently (YTD).
Source:moneycontrol.com
Process
Wonder Cement shows journey of cement with new campaign
Published
4 years agoon
October 21, 2021By
admin
The campaign also marks Wonder Cement being the first ever cement brand to enter the world of IGTV…
ETBrandEquity
Cement manufacturing company Wonder Cement, has announced the launch of a digital campaign ‘Har Raah Mein Wonder Hai’. The campaign has been designed specifically to run on platforms such as Instagram, Facebook and YouTube.
#HarRaahMeinWonderHai is a one-minute video, designed and conceptualised by its digital media partner Triature Digital Marketing and Technologies Pvt Ltd. The entire journey of the cement brand from leaving the factory, going through various weather conditions and witnessing the beauty of nature and wonders through the way until it reaches the destination i.e., to the consumer is very intriguing and the brand has tried to showcase the same with the film.
Sanjay Joshi, executive director, Wonder Cement, said, "Cement as a product poses a unique marketing challenge. Most consumers will build their homes once and therefore buy cement once in a lifetime. It is critical for a cement company to connect with their consumers emotionally. As a part of our communication strategy, it is our endeavor to reach out to a large audience of this country through digital. Wonder Cement always a pioneer in digital, with the launch of our IGTV campaign #HarRahMeinWonderHai, is the first brand in the cement category to venture into this space. Through this campaign, we have captured the emotional journey of a cement bag through its own perspective and depicted what it takes to lay the foundation of one’s dreams and turn them into reality."
The story begins with a family performing the bhoomi poojan of their new plot. It is the place where they are investing their life-long earnings; and planning to build a dream house for the family and children. The family believes in the tradition of having a ‘perfect shuruaat’ (perfect beginning) for their future dream house. The video later highlights the process of construction and in sequence it is emphasising the value of ‘Perfect Shuruaat’ through the eyes of a cement bag.
Tarun Singh Chauhan, management advisor and brand consultant, Wonder Cement, said, "Our objective with this campaign was to show that the cement produced at the Wonder Cement plant speaks for itself, its quality, trust and most of all perfection. The only way this was possible was to take the perspective of a cement bag and showing its journey of perfection from beginning till the end."
According to the company, the campaign also marks Wonder Cement being the first ever cement brand to enter the world of IGTV. No other brand in this category has created content specific to the platform.
Process
In spite of company’s optimism, demand weakness in cement is seen in the 4% y-o-y drop in sales volume. (Reuters)
Published
4 years agoon
October 21, 2021By
admin
Cost cuts and better realizations save? the ?day ?for ?UltraTech Cement, Updated: 27 Jan 2020, Vatsala Kamat from Live Mint
Lower cost of energy and logistics helped Ebitda per tonne rise by about 29% in Q3
Premiumization of acquired brands, synergistic?operations hold promise for future profit growth Topics
UltraTech Cement
India’s largest cement producer UltraTech Cement Ltd turned out a bittersweet show in the December quarter. A sharp drop in fuel costs and higher realizations helped drive profit growth. But the inherent demand weakness was evident in the sales volumes drop during the quarter.
Better realizations during the December quarter, in spite of the 4% year-on-year volume decline, minimized the pain. Net stand-alone revenue fell by 2.6% to ?9,981.8 crore.
But as pointed out earlier, lower costs on most fronts helped profitability. The chart alongside shows the sharp drop in energy costs led by lower petcoke prices, lower fuel consumption and higher use of green power. Logistics costs, too, fell due to lower railway freight charges and synergies from the acquired assets. These savings helped offset the increase in raw material costs.
The upshot: Q3 Ebitda (earnings before interest, tax, depreciation and amortization) of about ?990 per tonne was 29% higher from a year ago. The jump in profit on a per tonne basis was more or less along expected lines, given the increase in realizations. "Besides, the reduction in net debt by about ?2,000 crore is a key positive," said Binod Modi, analyst at Reliance Securities Ltd.
Graphic by Santosh Sharma/Mint
What also impressed analysts is the nimble-footed integration of the recently merged cement assets of Nathdwara and Century, which was a concern on the Street.
Kunal Shah, analyst (institutional equities) at Yes Securities (India) Ltd, said: "The company has proved its ability of asset integration. Century’s cement assets were ramped up to 79% capacity utilization in December, even as they operated Nathdwara generating an Ebitda of ?1,500 per tonne."
Looks like the demand weakness mirrored in weak sales during the quarter was masked by the deft integration and synergies derived from these acquired assets. This drove UltraTech’s stock up by 2.6% to ?4,643 after the Q3 results were declared on Friday.
Brand transition from Century to UltraTech, which is 55% complete, is likely to touch 80% by September 2020. A report by Jefferies India Pvt. Ltd highlights that the Ebitda per tonne for premium brands is about ?5-10 higher per bag than the average (A cement bag weighs 50kg). Of course, with competition increasing in the arena, it remains to be seen how brand premiumization in the cement industry will pan out. UltraTech Cement scores well among peers here.
However, there are road bumps ahead for the cement sector and for UltraTech. Falling gross domestic product growth, fiscal slippages and lower budgetary allocation to infrastructure sector are making industry houses jittery on growth. Although UltraTech’s management is confident that cement demand is looking up, sustainability and pricing power remains a worry for the near term.