Process
Precast will be the next best thing in construction industry
Published
6 years agoon
By
admin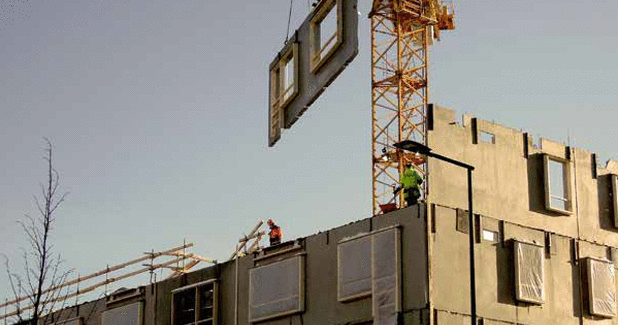
– Sunny Tethele, Chief Operating Officer, Suraksha City, Vasai, Maharashtra
Brief our readers about the project you are handling. At what stage of construction it is?
The project we are currently pursuing is a mass housing project under PMAY spread across 400 acres in Vasai, which is considered to be gateway to Mumbai. The project will be known as Suraksha Smart City and is poised to deliver 1,00,000 apartments, which will be combination of economically weaker section (EWS) 30 sq m, low income group 45 and 60 sq m under PMAY guidelines. Project has just completed its planning stage and we broke the ground in February 2020 and started with piling work.
What are time lines of the project?
Project is scheduled to be delivered in the next five years as we have time commitment towards PMAY. MHADA being governing body in Maharashtra, they will be monitoring the timeline and other aspects of project.
How is the construction planned and is there any new construction technology being considered?
The volume we are looking at is huge. We are aiming at 25 lakh cubic meters of concrete and 2,50,000 tonnes of reinforcement to be consumed over the next five years. It becomes extremely difficult to deliver such a high volume with conventional construction methods. Even if we consider system like Mivan, the labour requirements will be no less than 10,000 per shift. Other technologies like tunnel form have its limitations of design flexibility.
So the only feasible option we could see was "precast" construction. But the biggest negative of precast construction in India was water seepage through joints. Thanks to some really compromised precast construction by big construction houses in major cities of India like Delhi and Mumbai. Considering the project is aimed at first time home buyers, we wanted to give them pleasant experience at least by mitigating the leakage and dampness issue.
We put our brains in understanding, studying, analysing the reasons contributing to weaker joints and thus seepage and leakage. After a comprehensive study, we concluded that it cannot be conventional precast which will help us. To achieve watertight joints, speed, quality and waterproofing in wet areas, we decided to go with 3D construction.
In India, a few construction houses had tried 3D precast, but that was limited to only non load bearing, light weigh toilet areas.What we planned was extremely unique and path breaking. We are doing 3D precast, which is load bearing in fact the only load bearing element consisting of all wet areas in building including kitchen, toilet and bath which is 140 sqft and weighing around 25 tonnes.
So our project is combination of 3D, 2D , some special elements for lift, beam and staircase and hollow core slabs. The design is so optimised that compared to conventional design we optimised steel and reinforcement coefficient by almost 15 percent.
What are the basic grounds on which one should prefer precast technology for the houses being constructed under PMAY?
Every construction project has its own requirement. In India, majority residential projects don’t demand speed. Most of them progress as per velocity of sales. Now RERA coming as governing authority, the speed is committed but still speed is not the only criteria. So majority suitably use conventional systems of construction.
A few construction projects have voluntarily adopted to precast but failed as the capex was high and the progress achieved by precast was not supported by inflow of sales/funds. The ideal situation is to opt for precast, where sales are committed for residential projects or the early completion is going to pay premium for commercial projects like hotels, office spaces, Malls etc are advised in precast as its early completions shall give early revenues.
Further residential projects, which are under PMAY, where allocation of units is done and one has to deliver in stipulated time. It is not possible to complete the project with conventional methods but use modern technology instead.
The primary requirement in deciding precast as construction technologies are: speed of construction, volume of construction and positive cash flows. A project with 5,000 apartments to be delivered in two years is ideal size for precast project provided there are no cash flow issues.
In terms of cost and speed if one uses conventional method of construction over precast what will be the shortcomings?
In terms of speed, conventional construction system can never match the speed given by precast.About the cost there are few dimensions to it.
If the volume is less than 2 million sq ft
Precast manufacturing facility is not on site and away more than 100 km
Project tenure is more than three years
Skilled precast manpower not available
Concrete quality – specially SCC and early strength concrete is not achieved In above situations,precast becomes expensive than conventional construction system.
Does the defect liability period for prefab/ precast house differ from that of conventionally constructed house?
Ideally the quality of construction achieved in precast is far superior to conventional construction methods. The only challenge in precast in joinery. Defect liability period in precast is governed by one monsoon cycle unlike in conventional which ranges from six months to 24 months.
How has been the buyer’s preference for prefab/precast houses?
At few high-end apartments including row houses, bungalows the acceptance for precast is good. But at EWS and allied category as the customer belong to bottom of pyramid being ignorant of modern construction practices like precast was showing some resistance to precast. But with technology spread through social media is so fast that acceptance for precast at least in metro cities for all customer base is moderate.
In olden days many have attempted to popularise the precast housing in India but failed miserably; what can be the reasons?
Precast is a system; a concept needs to be adapted according to your local conditions. Meaning when you think of precast it comes with mechanised way of production, advanced logistic management, erection or installations and most importantly skilled manpower to execute from production to erection.In India, we lacked appropriate capex in technology. People have invested in localised precast machinery and equipment. The quality of precast elements produced was compromised.
The skilled and trained manpower was never available. Over a period, enterprises did not make efforts on skill development and retention of trained manpower. So the product at the end was compromised.
The material science of precast is very crucial especially with concrete. Precast demands a robust concrete mix design with SCC (self-compacted concrete) properties, early strength for lifting. Failing this the Element quality is compromised and production cycle is compromised if early strength concrete is not designed. To summarise, the machinery, manpower, material and money all were not invested seriously and hence failed miserably.
It is learnt that for using precast technology of construction, one needs trained and highly skilled man power. What is the situation in our country with specific reference to your project?
Skilled manpower is must. And considering that we are planning 3D construction, the requirement becomes much more significant and unavoidable.India is practising precast for quite a long time now. The skilled manpower is available in India but is scattered. We already identified the required skill set. We have already employed management and supervision level trained manpower. We are also in touch with specialised skilled manpower in Gulf, Asian counties like Singapore, Thailand and European countries.
For us, being 3D precast producer, our manpower requirement which is worked out on per cum basis is significantly low. Compared to other 2D precast the manpower requirement is reduced by 25 to 30 percent per cum.
It is said that architecture of the dwelling units should gel with the environment. Prefab/precast technology is coming from outside, how it is adapted to the local conditions?
What is critically important in precast is planning. Precast does not allow much alterations in design once precast facility is set.I would say its myth that precast technology is not Architecture design friendly. What is important is an optimised architectural design which needs to be designed keeping precast as technology in mind.Elevations projections, other artistic details everything is possible in precast.
Please comment on the applicability of 3D printing technology to mass housing. Is it used in any part of the world?
Three-dimensional (3D) printing is great technology in construction. But it comes with its own limitations. It’s good for small houses or low-rise buildings. It’s not suitable for high-rise buildings. Further its most expensive technology so far may be because the volume is much low.
What do you think is the future of prefab/precast construction in India? Can one expect luxury houses also being constructed with Prefab technology?
India is going to be biggest precast market of Asia. This decade is "precast decade". You will see many projects executed through precast technology. The investment in "precast technology" is huge. The sales of precast machine manufactures in last year have been highest in decade. International players are entering India to execute precast jobs gives same indication that India in next big thing for precast.
Luxury villas with precast is something which is possible and done inafew parts of India like Delhi, Hyderabad and Baroda. The concrete surface is so clean and engineered that there no need of secondary treatment like paint. Some good textures give great character to outer facade and to structure.It can be clearly said that precast is next best thing to look forward in construction industry.
You may like
Process
Price hikes, drop in input costs help cement industry to post positive margins: Care Ratings
Published
4 years agoon
October 21, 2021By
admin
Region-wise,the southern region comprises 35% of the total cement capacity, followed by thenorthern, eastern, western and central region comprising 20%, 18%, 14% and 13%of the capacity, respectively.
The cement industry is expected to post positive margins on decent price hikes over the months, falling raw material prices and marked drop in overall production costs, said an analysis of Care Ratings.
Wholesale and retail prices of cement have increased 11.9% and 12.4%, respectively, in the current financial year. As whole prices have remained elevated in most of the markets in the months of FY20, against the corresponding period of the previous year.
Similarly, electricity and fuel cost have declined 11.9% during 9M FY20 due to drop in crude oil prices. Logistics costs, the biggest cost for cement industry, has also dropped 7.7% (selling and distribution) as the Railways extended the benefit of exemption from busy season surcharge. Moreover, the cost of raw materials, too, declined 5.1% given the price of limestone had fallen 11.3% in the same aforementioned period, the analysis said.
According to Care Ratings, though the overall sales revenue has increased only 1.3%, against 16% growth in the year-ago period, the overall expenditure has declined 3.2% which has benefited the industry largely given the moderation in sales.
Even though FY20 has been subdued in terms of production and demand, the fall in cost of production has still supported the cement industry by clocking in positive margins, the rating agency said.
Cement demand is closely linked to the overall economic growth, particularly the housing and infrastructure sector. The cement sector will be seeing a sharp growth in volumes mainly due to increasing demand from affordable housing and other government infrastructure projects like roads, metros, airports, irrigation.
The government’s newly introduced National Infrastructure Pipeline (NIP), with its target of becoming a $5-trillion economy by 2025, is a detailed road map focused on economic revival through infrastructure development.
The NIP covers a gamut of sectors; rural and urban infrastructure and entails investments of Rs.102 lakh crore to be undertaken by the central government, state governments and the private sector. Of the total projects of the NIP, 42% are under implementation while 19% are under development, 31% are at the conceptual stage and 8% are yet to be classified.
The sectors that will be of focus will be roads, railways, power (renewable and conventional), irrigation and urban infrastructure. These sectors together account for 79% of the proposed investments in six years to 2025. Given the government’s thrust on infrastructure creation, it is likely to benefit the cement industry going forward.
Similarly, the Pradhan Mantri Awaas Yojana, aimed at providing affordable housing, will be a strong driver to lift cement demand. Prices have started correcting Q4 FY20 onwards due to revival in demand of the commodity, the agency said in its analysis.
Industry’s sales revenue has grown at a CAGR of 7.3% during FY15-19 but has grown only 1.3% in the current financial year. Tepid demand throughout the country in the first half of the year has led to the contraction of sales revenue. Fall in the total expenditure of cement firms had aided in improving the operating profit and net profit margins of the industry (OPM was 15.2 during 9M FY19 and NPM was 3.1 during 9M FY19). Interest coverage ratio, too, has improved on an overall basis (ICR was 3.3 during 9M FY19).
According to Cement Manufacturers Association, India accounts for over 8% of the overall global installed capacity. Region-wise, the southern region comprises 35% of the total cement capacity, followed by the northern, eastern, western and central region comprising 20%, 18%, 14% and 13% of the capacity, respectively.
Installed capacity of domestic cement makers has increased at a CAGR of 4.9% during FY16-20. Manufacturers have been able to maintain a capacity utilisation rate above 65% in the past quinquennium. In the current financial year due to the prolonged rains in many parts of the country, the capacity utilisation rate has fallen from 70% during FY19 to 66% currently (YTD).
Source:moneycontrol.com
Process
Wonder Cement shows journey of cement with new campaign
Published
4 years agoon
October 21, 2021By
admin
The campaign also marks Wonder Cement being the first ever cement brand to enter the world of IGTV…
ETBrandEquity
Cement manufacturing company Wonder Cement, has announced the launch of a digital campaign ‘Har Raah Mein Wonder Hai’. The campaign has been designed specifically to run on platforms such as Instagram, Facebook and YouTube.
#HarRaahMeinWonderHai is a one-minute video, designed and conceptualised by its digital media partner Triature Digital Marketing and Technologies Pvt Ltd. The entire journey of the cement brand from leaving the factory, going through various weather conditions and witnessing the beauty of nature and wonders through the way until it reaches the destination i.e., to the consumer is very intriguing and the brand has tried to showcase the same with the film.
Sanjay Joshi, executive director, Wonder Cement, said, "Cement as a product poses a unique marketing challenge. Most consumers will build their homes once and therefore buy cement once in a lifetime. It is critical for a cement company to connect with their consumers emotionally. As a part of our communication strategy, it is our endeavor to reach out to a large audience of this country through digital. Wonder Cement always a pioneer in digital, with the launch of our IGTV campaign #HarRahMeinWonderHai, is the first brand in the cement category to venture into this space. Through this campaign, we have captured the emotional journey of a cement bag through its own perspective and depicted what it takes to lay the foundation of one’s dreams and turn them into reality."
The story begins with a family performing the bhoomi poojan of their new plot. It is the place where they are investing their life-long earnings; and planning to build a dream house for the family and children. The family believes in the tradition of having a ‘perfect shuruaat’ (perfect beginning) for their future dream house. The video later highlights the process of construction and in sequence it is emphasising the value of ‘Perfect Shuruaat’ through the eyes of a cement bag.
Tarun Singh Chauhan, management advisor and brand consultant, Wonder Cement, said, "Our objective with this campaign was to show that the cement produced at the Wonder Cement plant speaks for itself, its quality, trust and most of all perfection. The only way this was possible was to take the perspective of a cement bag and showing its journey of perfection from beginning till the end."
According to the company, the campaign also marks Wonder Cement being the first ever cement brand to enter the world of IGTV. No other brand in this category has created content specific to the platform.
Process
In spite of company’s optimism, demand weakness in cement is seen in the 4% y-o-y drop in sales volume. (Reuters)
Published
4 years agoon
October 21, 2021By
admin
Cost cuts and better realizations save? the ?day ?for ?UltraTech Cement, Updated: 27 Jan 2020, Vatsala Kamat from Live Mint
Lower cost of energy and logistics helped Ebitda per tonne rise by about 29% in Q3
Premiumization of acquired brands, synergistic?operations hold promise for future profit growth Topics
UltraTech Cement
India’s largest cement producer UltraTech Cement Ltd turned out a bittersweet show in the December quarter. A sharp drop in fuel costs and higher realizations helped drive profit growth. But the inherent demand weakness was evident in the sales volumes drop during the quarter.
Better realizations during the December quarter, in spite of the 4% year-on-year volume decline, minimized the pain. Net stand-alone revenue fell by 2.6% to ?9,981.8 crore.
But as pointed out earlier, lower costs on most fronts helped profitability. The chart alongside shows the sharp drop in energy costs led by lower petcoke prices, lower fuel consumption and higher use of green power. Logistics costs, too, fell due to lower railway freight charges and synergies from the acquired assets. These savings helped offset the increase in raw material costs.
The upshot: Q3 Ebitda (earnings before interest, tax, depreciation and amortization) of about ?990 per tonne was 29% higher from a year ago. The jump in profit on a per tonne basis was more or less along expected lines, given the increase in realizations. "Besides, the reduction in net debt by about ?2,000 crore is a key positive," said Binod Modi, analyst at Reliance Securities Ltd.
Graphic by Santosh Sharma/Mint
What also impressed analysts is the nimble-footed integration of the recently merged cement assets of Nathdwara and Century, which was a concern on the Street.
Kunal Shah, analyst (institutional equities) at Yes Securities (India) Ltd, said: "The company has proved its ability of asset integration. Century’s cement assets were ramped up to 79% capacity utilization in December, even as they operated Nathdwara generating an Ebitda of ?1,500 per tonne."
Looks like the demand weakness mirrored in weak sales during the quarter was masked by the deft integration and synergies derived from these acquired assets. This drove UltraTech’s stock up by 2.6% to ?4,643 after the Q3 results were declared on Friday.
Brand transition from Century to UltraTech, which is 55% complete, is likely to touch 80% by September 2020. A report by Jefferies India Pvt. Ltd highlights that the Ebitda per tonne for premium brands is about ?5-10 higher per bag than the average (A cement bag weighs 50kg). Of course, with competition increasing in the arena, it remains to be seen how brand premiumization in the cement industry will pan out. UltraTech Cement scores well among peers here.
However, there are road bumps ahead for the cement sector and for UltraTech. Falling gross domestic product growth, fiscal slippages and lower budgetary allocation to infrastructure sector are making industry houses jittery on growth. Although UltraTech’s management is confident that cement demand is looking up, sustainability and pricing power remains a worry for the near term.