Environment
Skill development initiatives in India
Published
7 years agoon
By
admin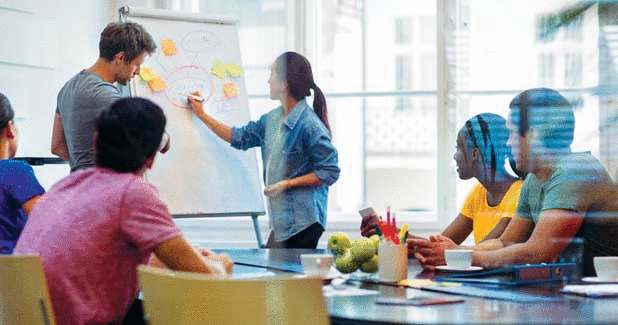
Skill development is a major challenge and initiatives have been taken not only by the Government but also by industry to facilitate skill development, but the task is gigantic and more needs to be done, says Dr Rajen Mehrotra.
To benefit from the demographic dividend, the Government of India both during the United Progressive Alliance (UPA) Government (i.e. 2004-14) plus the National Democratic Front (NDF) Government (i.e. 2014-24) have been making efforts by coming forward with various initiatives / schemes to improve the availability of skilled youth in India. Around 90 per cent of the workforce in developed countries is vocationally qualified, while in India the number is still only 5-7 per cent[1]. Skill development is a major challenge and initiatives have been taken not only by the Government but also by industry to facilitate skill development, but the task is gigantic and more needs to be done.
Apart from skill development, skill up gradation is a continuous process. Skill up-gradation is needed in all the fields not only in manufacturing but also in services. Upgradation can be from basic to advanced and finally to expert and can be at various stages, however this article is dealing with skill development at the initial stage for the youth of the country. India needs basically expertise through skill advancement for the youth in various fields. Along with skill development mentoring is an important area during skill upgradation and having good mentors helps the candidate to develop and grow. Industrial training institutes
Industrial training institutes (ITIs) with a focus on skill development were started in 1950 in India. These are presently under the Ministry of Skill Development and Entrepreneurship. The Government of India is running 2,293 ITIs and there are 10,812 private ITIs, thus having a total strength of 13,105 ITIs in the country as per published figures in April 2016. Vocational training of quite many ITI’s is not necessarily meeting the present-day requirement of advanced manufacturing enterprises, hence after completing the courses the young students passing out struggle to find meaningful employment.
The United Progressive Alliance (UPA) Government in 2007 went in for a Public Private Partnership (PPP) scheme asking industry to help upgrade the quality of training in the Government run ITIs. Quite many enterprises collaborated with the Government in this task of upgradation. Under PPP scheme, the Government of India provided interest free loan of Rs. 25 million to the Institutes Management Committee (IMC) Society of the partnered ITI and the repayment of the loan had a moratorium of 10 years from the year in which the loan had been received by the IMC Society. After the moratorium the loan amount had to be repaid in equal annual instalments over a period of 20 years, the first instalment repayable from the 11th anniversary of the date of receipt of money. This was a unique PPP scheme primarily aimed at improving the quality of training to benefit the students of the ITI in improved knowledge and skill for better chances of employability or being self employed. Many enterprises of the corporate sector supported this scheme, so as to improve the quality of skill development of the students and also improved the infrastructure of ITI’s which needed upgradation, though much more needed to be done.
Enterprises Running Training Institute
Certain manufacturing companies in order to get skilled workers in specific trades use to run a basic training centre wherein the youth acquired the requisite skill and also went through some knowledge acquisition by attending classes. In quite many cases these were confined to trades relevant to the industry in which the enterprise operated. Some of these enterprises got their trainees to qualify for the trades specified under the ITIs and some did not do that. I had an experience of this when I worked with Mukand Iron & Steel Works (now called Mukand) and also with ACC. There are quite many old companies that had this practice and still continue with this practice, as it helps the youth of the country to develop.
The modern vocational institutes set by companies like Mahindra and Mahindra, L&T and many leading companies are very good and the trainees from such institutions have no problem getting meaningful employment. Also, the trainees have competencies to set up small start-up’s and do well over time as they are trained with modern technology unlike the ones from the traditional ITIs. Some old enterprises have discontinued this practice later, as they were not in a position to absorb these trainees and it tended to create industrial relations problems. Most enterprises including the small and medium enterprises cannot undertake such an activity, and hence expect such trained personnel to be provided by the Government or by private agencies.
The Apprenticeship Act, 1961
In India we have The Apprenticeship Act, 1961 under which enterprises engaged the youth of this country as an apprentice in their premises to undergo apprenticeship training. This Act went through a major amendment in 2014 when the Apprentices (Amendment) Act 2014 came with the concept of "optional trade", which means any trade or occupation or any subject field in engineering or non-engineering or technology or any vocational course as may be determined by the employer for the purpose of the Act. There were enterprises that have introduced the provision of "optional trade" based on the business of the enterprise got their certified industrial employment standing orders amended to engage apprentices for a fixed duration of training. Some of these enterprises in the initial period have absorbed the enterprise apprentices as regular workers based on vacancies, however later they are finding it tough to absorb this trained youth.
National Employment Enhancement Mission (NEEM)
The Government through All India Council for Technical Education (AICTE) in April 2013 has launched a program known as National Employment Enhancement Mission (NEEM). The objective of the programme as mentioned is to develop a competent workforce which could take the country ahead in the industrial world. Under the programme, a NEEM agent can place a maximum number of 5,000 trainees in industry and the trainees can be a person between the age of 18 to 40 years, who has discontinued studies or is studying any course or completed a course leading to a graduation/diploma in any technical/non-technical stream. The period of training can be for a minimum period of three months and a maximum period of thirty-six months and the NEEM agent shall pay all enrolled NEEM trainees a stipend, which shall be at par with the prescribed minimum wage for unskilled category in the enterprise where they are placed.
The NEEM trainees in any enterprises are to be taken through a registered NEEM agent, who shall have at least a turnover of Indian Rs.50 million per financial year for the previous three financial years or a section 25 company (not for profit company under section 25 of The Companies Act, 1956. Which presently is called section 8 company under The Companies Act, 2013) is formed to meet the objectives of NEEM. This scheme has become very popular in the last three years and a large number of manufacturing enterprises are taking NEEM trainees who work along with regular workers of the enterprise.
Skill India Initiative
The NDA Government from 2014 launched various SKILL INDIA initiative to improve employability of the youth by enhancing their skill sets. Some of these initiatives are given below:
Deen Dayal Upadhyaya Grameen Kaushalya Yojana (2014) [2]: The Ministry of Rural Development (MoRD) announced the Deen Dayal Upadhyaya Grameen Kaushalya Yojana (DDU-GKY) Antyodaya Diwas, on September 25, 2014. DDU-GKY is a part of the National Rural Livelihood Mission (NRLM), tasked with the dual objectives of adding diversity to the incomes of rural poor families and cater to the career aspirations of rural youth. Over 180 million or 69 per cent of the country’s youth population between the ages of 18 and 34 years lives in rural area and around 55 million of them falls in the bottom of pyramid with no/marginal employment. DDU-GKY aims to skill such rural youth by providing them with jobs and ensuring regular monthly wages or above the minimum wages. DDU-GKY is present in 28 States and UTs, across 669 districts, impacting youth from over 7,294 blocks. It currently has over 1,242 projects being implemented by over 557 partners, in more than 585 trades from 50 industry sectors. Over 7.9 lakh candidates have been trained and over 3.6 lakh candidates have been placed in jobs as on July 11, 2019.
Pradhan Mantri Kaushal Vikas Yojana (2015) [3]: This scheme was launched by the Ministry of Skill Development and Entrepreneurship to formulate and implement the Pradhan Mantri Kaushal Vikas Yojana (PMKVY) through the National Skill Development Corporation in March 2015. Individuals with prior learning experience or skills will also be assessed and certified under Recognition of Prior Learning (RPL).
Here the government provides training with the help of third-party training partners. Apart from the training, the candidates shall also go through an assessment at the end of the training schedule. A certificate of merit shall also be issued to candidates at the end of this training period based on the assessment. Training and Assessment fees are completely paid by the Government and on an average a sum of Rs 8000 is to be rewarded to an individual enrolled in the scheme.
Financial Assistance for Skill Training of Persons with Disabilities (2015) [4]: This scheme helps in empowering the 26.8 million disabled population in India in accordance with the existing "The Persons with Disability Act 1995". The scheme provides special training stipend for person with disability less than 40 per cent and between the age group from 19 to 59. The scheme also consists of facilities such as hostels and accommodation, cost of transport and other incentives to the candidate enrolled. Also, an all-inclusive training cost of Rs 5,000 per trainee per month shall be provided for the entire duration of the training. The benefits are to be transferred in four instalments.
National Apprenticeship Promotion Scheme (2016) [5]: This scheme is the newest amongst the cluster. It was launched in August 2016, which promotes apprenticeship by sharing 25 per cent of the prescribed stipend of the apprenticeship burden (maximum of Rs 1,500 per month).
Craftsmen Training Scheme (1950) [6]: The scheme was launched in year 1950 to shape the future workmen. Because of this scheme, only at present Craftsmen Training Scheme are being offered through a network of 15,042 it is (Government: 2738 + Private: 12,304) located all over the country with total of 22.82 lakh trainees enrolled. This scheme has played and has been playing a significant role in restoring the traditional arts and crafts skills of the traditional Indian.
Pradhan Mantri Kaushal Kendra (2018) [7]: This scheme focuses on establishing special Model Training Centres (MTCs) established in every district of the country by Ministry of Skill Development and Entrepreneurship (MSDE). The model training centres envisage to:
Create benchmark institutions that demonstrate inspirational value for competency-based skill development training.
Focus on elements of quality, sustainability and connection with stakeholders in skills delivery process.
Transform from a mandate-driven footloose model to a sustainable institutional model.
These training centres can be built by receiving an amount of 75 per cent of the project investment from central government.
Skill Development for Minorities (2013) [8]: The scheme called "Learn and Earn" has been launched specially for minorities in 2013 to help the minorities to get better chances of employment even with minimum qualifications (at least class V). The Ministry of Minority Affairs has developed courses include majority of traditional skills being practiced by the minority communities, e.g. embroidery, chikankari, zardosi, patch work, gem and jewelry, weaving, wooden works, leather goods, brass metal works, glass wares, carpet, etc. The scheme bears full cost of the projects as per prescribed financial norms and also provides stipend and post placement support to the candidate.
Green Skill Development Programme (2017) [9]: The Green Skill Development Programme (GSDP) aims to fill the gap between the need and availability of skill sets to help sustain environment at various levels. It enhances the employability of people in jobs that contribute to preserving or restoring the quality of the environment with help of the 67 centres established by the government. The first GSDP course was formulated for skilling biodiversity conservationists (basic course) and Para-taxonomists (Advance Course) of 3 months’ duration each on a pilot basis in ten select districts of the country. BSI and ZSI were the nodal centres for the pilot programme.
All Indian Computer Siksha Mission (1999) [10]: The scheme has been in addition to the existing Rajeev Gandhi Computer Saksharta Mission. The Government of India has initiated Computer skill centres in association with the third-party partners where, candidates can get certificate courses, diploma courses, advance diploma courses, vocational courses to showcase their technical skills for better employment opportunities. AICSM has trained above 1.5 lakh till 2017 and placed above 42,000 students.
Challenges
India has more than 600 million people under the age of 25 years with a potential of being the most employable country in Asia Pacific. Every year, 25 million people attain the age of 21 years and come to work, so skilling such a large number is not easy. According to All India Survey of Higher Education by Azim Premji University of the 8 million students who graduate every year, only around 1 million receive professional degrees. Hence, skill development of youth who are non-graduates is a priority area. The Government of India has been working since 2009 by having launched The National Skills Development Corporation (NSDC). The Pradhan Mantri Kaushal Vikas Yojana was launched in 2015 with a separate budget of Rs 15 billion. There is also scope for skill development in the field of agriculture, horticulture, dairy, poultry etc. and this can facilitate in generating better quality jobs for the youth in rural India. This is an area where more focus is needed. Despite these many years of working on the problem there still persist two major challenges: Informational asymmetries and limited quality assurance.
A major hitch in India is that except for some leading companies, majority of the enterprises do not take much interest in supporting the skill development initiative. Many enterprises misuse the young trainees as a substitute for regular workers to achieve a cost arbitrage by utilising these youngsters to do regular nature of jobs in the garb of training; this is especially true with reference to NEEM trainees. Industry has a role and responsibility as part of corporate citizenship and needs to wholeheartedly support the skill development initiative in the nation’s interest.
A major challenge is that the youth today is inclined towards desiring to have higher education by studying in the college and university rather than acquiring skills under various schemes listed above. For this barrier to break enterprises and citizens will not only have to pay well to skilled category of workers but also treat them with dignity, so that they are attracted towards acquiring skills. In the western world, the skilled handy man who by and large is self-employed is paid well and treated well, so that he/she is happy doing that work rather than going in for higher college and university education.
References
1.https://www.thehindu.com/education/careers/A-potted-historyof-skilling-in-India/article17287918.ece
2.http://ddugky.gov.in/content/about-us-0
3.https://www.india.gov.in/spotlight/pradhan-mantri-kaushal-vikasyojana#tab=tab-1
4.http://disabilityaffairs.gov.in/upload/uploadfiles/files/fas1.pdf
5.http://www.mescindia.org/naps.php
6.https://dgt.gov.in/CTS
7.https://nsdcindia.org/pmkk
8.http://www.minorityaffairs.gov.in/schemesperformance/seekho-aurkamaolearn-earn-scheme-skill-development-minorities
9.http://www.gsdp-envis.gov.in/
10.https://www.aicsm.com/aicsmAimGoal.htm
Acknowledgement
The author is grateful to Mr. Vineet Kumar Oswal, First Year student of Post Graduate Programme in Management at Indian Institute of Management (IIM) Sirmaur for compiling information on the 9 schemes listed under Skill India. Published in November 2019 issue of Current Labour Reports and Arbiter.
The author is Past President of Industrial Relations Institute of India (IRII), Former Senior Employers’ Specialist for South Asian Region with Internation.al Labour Organization (ILO) and Former Corporate Head of HR with ACC and Former Corporate Head of Manufacturing and HR with Novartis India. He can be contacted on: Email: rajenmehrotra@gmail.com
Concrete
India donates 225t of cement for Myanmar earthquake relief
Published
3 months agoon
June 17, 2025By
admin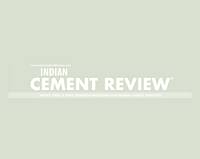
On 23 May 2025, the Indian Navy ship UMS Myitkyina arrived at Thilawa (MITT) port carrying 225 tonnes of cement provided by the Indian government to aid post-earthquake rebuilding efforts in Myanmar. As reported by the Global Light of Myanmar, a formal handover of 4500 50kg cement bags took place that afternoon. The Yangon Region authorities managed the loading of the cement onto trucks for distribution to the earthquake-affected zones.
Concrete
Reclamation of Used Oil for a Greener Future
Published
3 months agoon
June 16, 2025By
admin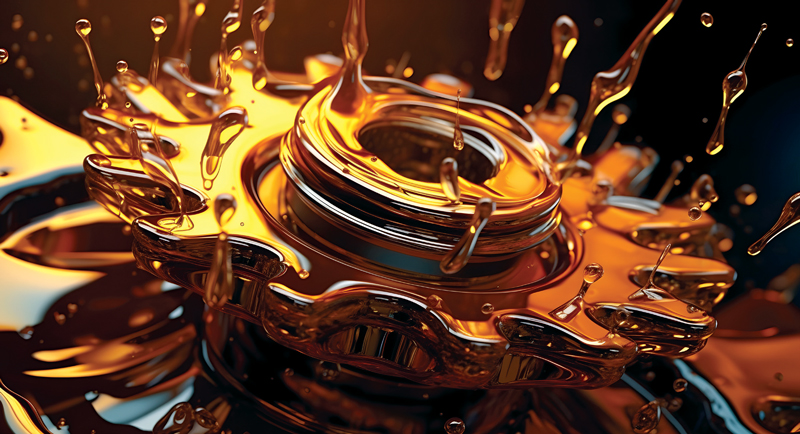
In this insightful article, KB Mathur, Founder and Director, Global Technical Services, explores how reclaiming used lubricants through advanced filtration and on-site testing can drive cost savings, enhance productivity, and support a greener industrial future. Read on to discover how oil regeneration is revolutionising sustainability in cement and core industries.
The core principle of the circular economy is to redefine the life cycle of materials and products. Unlike traditional linear models where waste from industrial production is dumped/discarded into the environment causing immense harm to the environment;the circular model seeks to keep materials literally in continuous circulation. This is achievedthrough processes cycle of reduction, regeneration, validating (testing) and reuse. Product once
validated as fit, this model ensures that products and materials are reintroduced into the production system, minimising waste. The result? Cleaner and greener manufacturing that fosters a more sustainable planet for future generations.
The current landscape of lubricants
Modern lubricants, typically derived from refined hydrocarbons, made from highly refined petroleum base stocks from crude oil. These play a critical role in maintaining the performance of machinery by reducing friction, enabling smooth operation, preventing damage and wear. However, most of these lubricants; derived from finite petroleum resources pose an environmental challenge once used and disposed of. As industries become increasingly conscious of their environmental impact, the paramount importance or focus is shifting towards reducing the carbon footprint and maximising the lifespan of lubricants; not just for environmental reasons but also to optimise operational costs.
During operations, lubricants often lose their efficacy and performance due to contamination and depletion of additives. When these oils reach their rejection limits (as they will now offer poor or bad lubrication) determined through laboratory testing, they are typically discarded contributing to environmental contamination and pollution.
But here lies an opportunity: Used lubricants can be regenerated and recharged, restoring them to their original performance level. This not only mitigates environmental pollution but also supports a circular economy by reducing waste and conserving resources.
Circular economy in lubricants
In the world of industrial machinery, lubricating oils while essential; are often misunderstood in terms of their life cycle. When oils are used in machinery, they don’t simply ‘DIE’. Instead, they become contaminated with moisture (water) and solid contaminants like dust, dirt, and wear debris. These contaminants degrade the oil’s effectiveness but do not render it completely unusable. Used lubricants can be regenerated via advanced filtration processes/systems and recharged with the use of performance enhancing additives hence restoring them. These oils are brought back to ‘As-New’ levels. This new fresher lubricating oil is formulated to carry out its specific job providing heightened lubrication and reliable performance of the assets with a view of improved machine condition. Hence, contributing to not just cost savings but leading to magnified productivity, and diminished environmental stress.
Save oil, save environment
At Global Technical Services (GTS), we specialise in the regeneration of hydraulic oils and gear oils used in plant operations. While we don’t recommend the regeneration of engine oils due to the complexity of contaminants and additives, our process ensures the continued utility of oils in other applications, offering both cost-saving and environmental benefits.
Regeneration process
Our regeneration plant employs state-of-the-art advanced contamination removal systems including fine and depth filters designed to remove dirt, wear particles, sludge, varnish, and water. Once contaminants are removed, the oil undergoes comprehensive testing to assess its physico-chemical properties and contamination levels. The test results indicate the status of the regenerated oil as compared to the fresh oil.
Depending upon the status the oil is further supplemented with high performance additives to bring it back to the desired specifications, under the guidance of an experienced lubrication technologist.
Contamination Removal ? Testing ? Additive Addition
(to be determined after testing in oil test laboratory)
The steps involved in this process are as follows:
1. Contamination removal: Using advanced filtration techniques to remove contaminants.
2. Testing: Assessing the oil’s properties to determine if it meets the required performance standards.
3. Additive addition: Based on testing results, performance-enhancing additives are added to restore the oil’s original characteristics.
On-site oil testing laboratories
The used oil from the machine passes through 5th generation fine filtration to be reclaimed as ‘New Oil’ and fit to use as per stringent industry standards.
To effectively implement circular economy principles in oil reclamation from used oil, establishing an on-site oil testing laboratory is crucial at any large plants or sites. Scientific testing methods ensure that regenerated oil meets the specifications required for optimal machine performance, making it suitable for reuse as ‘New Oil’ (within specified tolerances). Hence, it can be reused safely by reintroducing it in the machines.
The key parameters to be tested for regenerated hydraulic, gear and transmission oils (except Engine oils) include both physical and chemical characteristics of the lubricant:
- Kinematic Viscosity
- Flash Point
- Total Acid Number
- Moisture / Water Content
- Oil Cleanliness
- Elemental Analysis (Particulates, Additives and Contaminants)
- Insoluble
The presence of an on-site laboratory is essential for making quick decisions; ensuring that test reports are available within 36 to 48 hours and this prevents potential mechanical issues/ failures from arising due to poor lubrication. This symbiotic and cyclic process helps not only reduce waste and conserve oil, but also contributes in achieving cost savings and playing a big role in green economy.
Conclusion
The future of industrial operations depends on sustainability, and reclaiming used lubricating oils plays a critical role in this transformation. Through 5th Generation Filtration processes, lubricants can be regenerated and restored to their original levels, contributing to both environmental preservation and economic efficiency.
What would happen if we didn’t recycle our lubricants? Let’s review the quadruple impacts as mentioned below:
1. Oil Conservation and Environmental Impact: Used lubricating oils after usage are normally burnt or sold to a vendor which can be misused leading to pollution. Regenerating oils rather than discarding prevents unnecessary waste and reduces the environmental footprint of the industry. It helps save invaluable resources, aligning with the principles of sustainability and the circular economy. All lubricating oils (except engine oils) can be regenerated and brought to the level of ‘As New Oils’.
2. Cost Reduction Impact: By extending the life of lubricants, industries can significantly cut down on operating costs associated with frequent oil changes, leading to considerable savings over time. Lubricating oils are expensive and saving of lubricants by the process of regeneration will overall be a game changer and highly economical to the core industries.
3. Timely Decisions Impact: Having an oil testing laboratory at site is of prime importance for getting test reports within 36 to 48 hours enabling quick decisions in critical matters that may
lead to complete shutdown of the invaluable asset/equipment.
4. Green Economy Impact: Oil Regeneration is a fundamental part of the green economy. Supporting industries in their efforts to reduce waste, conserve resources, and minimise pollution is ‘The Need of Our Times’.
About the author:
KB Mathur, Founder & Director, Global Technical Services, is a seasoned mechanical engineer with 56 years of experience in India’s oil industry and industrial reliability. He pioneered ‘Total Lubrication Management’ and has been serving the mining and cement sectors since 1999.
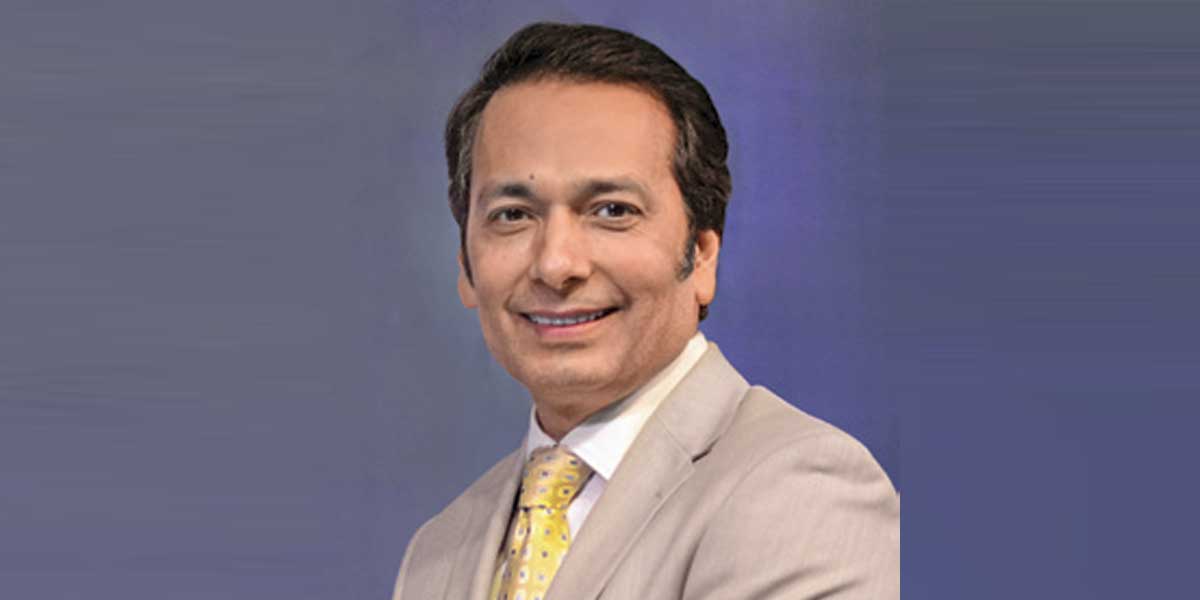
The Indian cement industry has reached a critical juncture in its sustainability journey. In a landmark move, the Ministry of Environment, Forest and Climate Change has, for the first time, announced greenhouse gas (GHG) emission intensity reduction targets for 282 entities, including 186 cement plants, under the Carbon Credit Trading Scheme, 2023. These targets, to be enforced starting FY2025-26, are aligned with India’s overarching ambition of achieving net zero emissions by 2070.
Cement manufacturing is intrinsically carbon-intensive, contributing to around 7 per cent of global GHG emissions, or approximately 3.8 billion tonnes annually. In India, the sector is responsible for 6 per cent of total emissions, underscoring its critical role in national climate mitigation strategies. This regulatory push, though long overdue, marks a significant shift towards accountability and structured decarbonisation.
However, the path to a greener cement sector is fraught with challenges—economic viability, regulatory ambiguity, and technical limitations continue to hinder the widespread adoption of sustainable alternatives. A major gap lies in the lack of a clear, India-specific definition for ‘green cement’, which is essential to establish standards and drive industry-wide transformation.
Despite these hurdles, the industry holds immense potential to emerge as a climate champion. Studies estimate that through targeted decarbonisation strategies—ranging from clinker substitution and alternative fuels to carbon capture and innovative product development—the sector could reduce emissions by 400 to 500 million metric tonnes by 2030.
Collaborations between key stakeholders and industry-wide awareness initiatives (such as Earth Day) are already fostering momentum. The responsibility now lies with producers, regulators and technology providers to fast-track innovation and investment.
The time to act is now. A sustainable cement industry is not only possible—it is imperative.