Environment
Utilisation of High Silica Low Grade Limestone
Published
7 years agoon
By
admin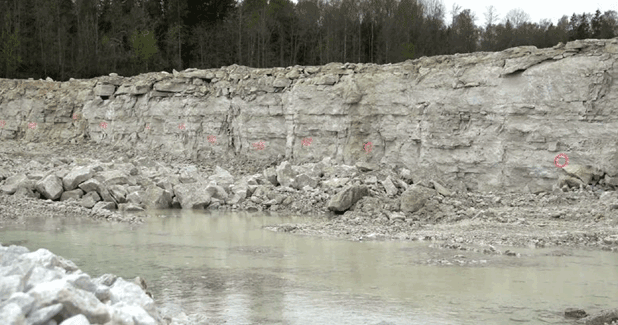
With depletion of high cement grade limestone, [presently] Indian cement industry is facing an acute cement raw material problem for smooth plant operation and manufacture of higher grades of cement. Although India is bestowed with huge limestone deposits but most of the deposits in India presently available for cement manufacture are either marginal grade or low grade.The situation is further aggravated due to allocation of low grade coal to the cement industries. Some of the cement plants start with a simple limestone deposit with more or less uniform quality of limestone however with the consumption of the high grade limestone, the deposits are converted into intricate leaving behind low heterogeneous grade.
Hence urgently a serious thought is essential not only for detailed exploration of limestone deposits to convert the resources to reserves (as per UNFC), but also for development of a cost- effective dry beneficiation techniques for up gradation of low and sub-marginal grade high siliceous limestone in India for production of quality cements.
Scenario of limestone deposits in India
Limestone is the basic raw materials for cement manufacture and the growth of the cement industry depends on the availability of right grade cement grade limestone. India is having huge limestone deposits distributed throughout the geological stratigraphic horizon starting from Archaean to tertiary formations. The quality variation of limestone from deposit to deposit is very wide in India. The geographical distribution of limestone deposits in India is also not uniform. Some states do not have any limestone deposits.
Around 95 per cent of cement grade limestone deposits are concentrated in 10 states, although the cement grade limestone is occurring in 23 States in India in smaller quantities. Limestone deposits have not been reported from states like Punjab, Mizoram, Goa, Sikkim and Tripura. Whereas Haryana, Manipur, West Bengal, Andaman and Nicobar Islands have very meager reserves not suitable for large capacity cement plants. Based on the prima-facie availability of freehold cement grade limestone deposits, there is very limited scope for further addition of cement manufacturing capacity in the state of Kerala, Tamil Nadu, Bihar, Uttar Pradesh and Odisha. However, the States of Andhra Pradesh, Telangana, Assam, Gujarat, Himachal Pradesh, Karnataka, Chattisgarh, Meghalaya and Rajasthan have potential for further creation of cement manufacturing capacity.
The qualitative and quantitative assessment of limestone deposits have been carried out by various Central Government agencies, State Directorate of Geology and Mining and private companies. Based on the exploration data generated by these agencies at present the total cement limestone resource as estimated by Indian Bureau of Mines (IBM) is 124,539.551 million tonnes (MT). The zone wise and state wise cement grade limestone reserves and resources as per IBM are as under: Regarding quality of limestone, except limestone occurring in the North – Eastern states, Gujarat, few patches of Andhra Pradesh, Telangana, Rajasthan and Madhya Pradesh most of the deposits are low grade, either having high silica content (SiO2 16-20 per cent) or high magnesia containing 6-12 per cent MgO or even more. In this article only high silica low grade limestone will be discussed. In the March, 2018 issue we have discussed in detail about the use of high Magnesia Limestone in India.These limestone cannot be used for manufacture of cement as such and would need beneficiation.
Further, out of total limestone resources of 124539.91 MT, 30 per cent falls under the forest cover, restricted area and eco-sensitive zones, and hence not permissible for exploitation. As a result further 34677.19 million tonnes of limestone are not available for the cement industries, although some of the deposits are very good cement grade limestone. Hence from the available remaining 89862.361 Mts. limestone resources, cement grade limestone reserve is only 8948.926 MT (UNFC Code (111),(121) and (122)) as per UNFC classification of mineral deposits.
Although the consumption ratio of limestone to cement has gone down in India due to production of more blended cements, the limestone quantity requirement for cement manufacture has increased 1.5 times in last 15 years. Further the demand for high grade limestone has also increased due to production of more 43 and 53 grade OPC. It has been observed that the demand of high grade limestone further increases the mines rejects in case of low to marginal grade limestone deposits. The limestone requirement for production of 71.28 MT of clinker during 1997-98 was 106.92 MT and in the year 2016-17 it has enhanced to 300.00 MT. From an estimate it has been seen that for production of 500 MT of clinker ( as anticipated) by the end of 2020 the limestone requirement will be around 700 MT.
Sustainable Development Of Limestone Deposits
From an estimate it has been observed that with the present rate of consumption of available limestone reserves of India can sustain only 40 years. More over the low grade limestone deposits during mining is generating huge mine rejects during exploitation creating a major environmental problem. To overcome such problems the following actions are essential for trouble free operation of cement plants in India. Establishment of limestone reserves: It is the imperative need that government and private sector should go for massive exploration activity and establish and convert the inferred grade of limestone into measured grade. The will help the cement industry to plan to meet the future requirements. The systematic exploration activity and computerised deposit evaluation will help the development of accurate deposit model. The computerised 3-D deposit model for the each and every deposit is essential for planning of mining which will help in utilisation of low grade limestone and even the mine rejects in cement production as additives.
Systematic deposit exploitation plan: There are various methods adopted by the Indian cement industry presently to utilise the low grade limestone for cement manufacture. The computerised mine planning, pit head quality control, multimine scheduling are very effective techniques for blending of low and high grade limestone. This enhances the utilisation of low grade limestone to some extent. In spite of these techniques a considerable quantity of quarry rejects are generated every year, which has no use and creating additional environmental problem.
In India most of the cement plants are operating on heterogeneous intricate limestone deposits with the result that mine reject generation is high. Besides low grade its variability is extremely high due to intercalation of clay, pegmatite, schist etc. Therefore, the computerised mine planning with pit head quality control provides an elegant solution to utilise low grade limestone.
The mine planning software documents the deposit exploration data systematically, estimate the grade ? tonnage to higher degree of confidence level. It creates accurate deposit inventory with various deposit graphics. The multiple blending options of estimated deposit block not only helps in production of homogeneous raw materials but also enhance the quarry life. The block model concept created by Surpac/Datamine not only provides exhaustive information about the deposit but also forms the basis of mine scheduling offering flexibility in mining with multiple blending options. This can be one of the steps towards the judicial use of the limestone and conservation of national inventory of cement and high grade limestone.
Remote quarry management: Conservation of high grade, optimal use of low and marginal grade limestone is now possible by IT enabled technology supported by state of art mining softwares to monitor quarry operations. Lafarge Kamloops plant in BC, Canada was doomed to be exhausted of cement grade deposit in its existing quarry way back in 2012. Lafarge Technical Centre(CTS) in Montreal stepped in and by remote management established that there is enough limestone to run the plant for another 10 years from the same running quarry.
CTS monitored regularly the bore hole results which was sent to them before a blast and the results of blasts was monitored online from a Cross-belt analyser through VPN. A dedicated highly experienced geologist was made the champion of Kamloops plant. He could guide the plant mining contractor on the areas to be taken up for blasting well in advance. He had full information of exploration data, quarry hardware and plant requirements in terms of quality and quantity. He used the block model and pit design technique using sophisticated softwares and guided the contractor regularly ensuring high grade is conserved and low and sub marginal grade limestone used optimally. He visits the quarry only once in six months for detailed surveys and upgrades the data in software.
Holtec India has reported extension of limestone quarry belonging to a cement plant in North Ethopia by 16 years using this concept of remote quarry management. This should work out well with the Indian cement plants too. The local mines teams in most of the plants may not have the knowledge or expertise to use IT enabled modern technology with an array of softwares. Moreover there could be short cuts in local operation which kills the concept of conservation of high grade limestone. With the pressure of enhanced production in plants and generally with limited resources the long term mine planning is jeopardised leading to an unsustainable situation. Thus the remote quarry management model can be the best business model for mining management in Indian Cement Industry for sustainability.
An external unbiased eye equipped with all modern techniques can do wonders especially for plants in a group with remote monitoring from their technical centre or a central location in a cluster.
Bulk or cross belt analyser based on Prompt Gamma Neutron Activation analysis (PGNAA) is proving to be an useful tool in increasing quarry life by effective blending of various grades of limestone in intricate quarries. Since limestone analysis is available every minute after crusher this technique also helps in validation of the block model. Latest version of this equipment with upgraded software also help in pile management and control. This equipment is a must for intricate and heterogenous quarries to extend quarry life.
Beneficiation of low grade high silica limestone: To make use of low grade high siliceous limestone various beneficiation techniques have been tried by number of R&D institutions and industries. With the present day dry process manufacturing technology the wet beneficiation technology such as froth flotation method and semi wet process like bacterial leaching are not cost effective. Dry beneficiation is only suitable for the present day manufacturing technology of Portland cement clinker. Some of the dry process techniques are showing excellent result in lab scale studies but unfortunately not yet cost effective. Further studies and establishment of potential techniques is the need of the hour to conserve the limestone deposits. Some studies carried out to upgrade high siliceous limestone are given below.
In case of low grade siliceous limestone deposits most of the plant are using the crossing and screening techniques to separate the interstitial clay and impurities associated with the limestone to some extent. If the clay content is more some times washing is more beneficial. Before adoption of such technique a detailed study on the impurities associated with the limestone is essential. A liberation study is required to find out at what size fraction the impurities are separating from the limestone otherwise while separating a considerable good grade limestone may be lost. This study can starts with petrographic analysis of the limestone and impurities .With the petrographic analysis data, lab scale analysis is essential to establish the technique suitable for separation of impurities as the nature of the impurities and limestone varies from deposit to deposit.
Case study
The limestone deposit of this case study belongs to geologically Delhi Super Group. The formations are consist of mainly calcareous meta-sediments viz., calc-gneisses, calc-schists and calcitic limestone with minor bands of schist and quartzite. Considerable amount of limestone reserve is 38- 40 per cent CaO with Silica about 16-18 per cent. It was observed during exploration drilling that the core recovery is varying because of intercalation of clay, phylite etc. The intercalation clay is soft and fine grained where as the limestone is medium grained and hard. This has been confirmed by the petrographic study of the limestone deposit. Laboratory study indicates that the size fraction below 10mm is mostly clay and phylites. With the screening of clay and phylites the silica in limestone reduced from 16.66 per cent to 13.10 per cent and CaO enhanced from 38 per cent to 42 per cent making the limestone blendable. A double deck screen section is provided in this case in the crusher plant, -75mm limestone along with the clay goes directly to the screening plant section prior to crushing. On screening this material the -10mm fraction is rejected as it is mainly clay whereas the +10mm materials goes to the raw material stacker.
The size fraction of liberation varies from deposit to deposit depends on the grain size of limestone and physical quality of impurities. A thorough petrographic study is needed for best screening result.
For beneficiation of coarse grained high silica limestone, a study has been tried through differential grinding technique and results are as given in table-2. The grain size of quartz and calcite in the limestone under study is around 2 ? 150 ?m and the chemical composition is 15.90 per cent (SiO2) and 43.26 per cent (CaO) respectively. From the results of this study it has been observed that this technique has potentiality to reduce silica from limestone economically. However, in case of the fine grained limestone it is required to grind the material finer which involves high energy consumption.
Among all the electronic ore sorter developed, optical sorting is a highly potential technique and can be used for beneficiation of limestone having impurities with significant color difference such as amphibolites, pyroxenes etc. This technique has already been adopted in one of the cement plants in India and the plant has reported encouraging results.
It has been observed that quartz and dolomites are weakly magnetic with relative attractivity of 0.37 and 0.22 respectively, whereas calcite is non-magnetic with relative attractivity of 0.03. Hence, with high magnetic separator the silica and dolomite can be effectively separated from limestone. In case of electrostatic separation, it is difficult to separate the calcite and silica as they have almost same relative empirical conductivity (voltage-10,920). Whereas the relative empirical conductivity of Dolomite (voltage-8,268) is much lower than the calcite and quartz, as a result the dolomite crystals can be effectively separated from limestone by electrostatic separation methods.
The separation of silica and calcite by air classifier is also a very effective technique. Calcites (CaCO3), being lower in specific gravity than the silica (SiO2) are collected as overflow. In one case of a siliceous limestone this technique has been tried and the CaO in the limestone got enriched from 34.19 per cent to 44.23 per cent and also reduced silica considerably (Table-3). In case of separation of dolomite and calcite it is more effective as the specific gravity difference is higher.
Use of high calorific low ash fuel
Further the use of high silica limestone became difficult for production quality clinker with the Indian coal allocated to the cement industry. These coals are low grade with ash content as high as 35 per cent. During pyro-processing the absorption of coal ash increase the silica content in the raw meal making it difficult for production of quality clinker. In case of where high silica limestone is to be used, Pet coke and lignite are the best fuels to control the silica content. Although these fuels are have high sulfur content which can be controlled by maintaining alkali-sulphur ratio close to one.
Alternate cementitious production from low and marginal grade limestone
Manufacture of Sulpho-aluminate belite cement: In recent years Sulfo-Aluminate-Belite cement is receiving a lot of interest as it can be manufactured from various industrial wastes and low grade limestone. It is environmental friendly and requires less thermal energy for manufacture compared to OPC clinker manufacture.
Raw mixes for C4A3S clinker differ from the Portland cement as they contain significant amount of sulphate. Therefore, the reactions and product are quite different from those normally found in Portland cement production. The total lime requirement for production of such cement is less than 50 wt. per cent as against the about 65 wt. per cent for Portland cement. This indicates that for production of Sulfo- Aluminate Belite cement low grade limestone is suitable. The Sulfo-Aluminate Belite clinker can be produced by burning limestone, bauxite and gypsum at around 12000C. For production of Sulfo-Aluminate Belite cement the Lime Saturation Factor (LSF) requirement is low around 0.67, which reduces the consumption of limestone stone in manufacture. As the consumption of lime is less, the manufacture of this type of cement leads to around 35 per cent less CO2 than Portland cement. The requirement of thermal energy for production of Sulfo-Aluminate Belite clinker is also much less than the Portland cement clinker as it is manufactured at 12000C. It has been found that the Sulfo-Aluminate Belite is having very good dimensional stability, sulfate resistance, compressive strength development and better resistance to atmospheric carbonation comparable to commercial Portland cement. Presently these cements are produced commercially in countries such as China, Japan, Russia etc. successfully. These cements are best suitable for the construction in the coastal areas owing to their better sulphate resistance property.
Sulfo-Aluminates Belite Cement contains C4A3S as main component together with Calcium Sulfate, Dicalcium Silicate (C2S), Tetracalcium Iron Aluminate (C4AF), Calcium Aluminate (C3A,CA,&C12A7) and Silicoaluminates (C2AS, CAS3). The mineralogical composition of the Sulfo-Aluminate Belite cement are quite different than the Portland cement ( Table -4) as it contains relatively high concentration of C2S, C4A3S and C4AF, shows different properties during hydration. Chemical composition of Sulfo-Aluminate Belite cement is markedly different from the Portland cement. A comparison of chemical composition and properties of typical Portland cement and Sulfo-Aluminate Belite cement is given in table-5.
The rapid setting of Sulfo-Aluminate cement is mainly due to quick conversion of C4A3S to hydration product during early age hydration. On hydration the gypsum reacts with C4A3S and from ettringite (C6AS3H32). This regulates the technical properties of Sulfo-Aluminate Belite cement.
4 CaO3Al2O3SO3+8CaSO4+6CaO+93H2O ? 3 (CaOAl2O3CaSO431H2O) The formation of ettringite is very fast in this case which results in reduced workability of the cement and therefore requires a retarder. The C2S present in this cement adds to the compressive strength and durability. Mortars made from such cements have comparable compressive strengths and total porosity as compared to Portland cement. The mortar prepared from the Sulfo-Aluminate Belite cement release less quantity of Ca(OH)2 on hydration which helps in reducing the porosity of concrete. The higher content of gypsum in the Sulfo-Aluminate Belite cement also decrease the carbonation of concrete. The Sulfo-Aluminate Belite cement exhibits better protective for the steel reinforcement corrosion.
Another advantage of this cement clinkers is that it requires less electrical energy in cement grinding. Since it requires less amount of limestone in the kiln mix, large quantity of industrial by-products such as fly ash, LD slag, red mud etc can be utilised as raw materials. Phospho-gypsum and flue gas desulfurisation gypsum can replace entirely the requirement of natural gypsum for production of these cements. Further, it has also been experimented that the bottom ash from the thermal power plant can be used as the raw material for production of Sulfo-Aluminate Belite cement as this material has little use at present and increasingly piling up in thermal power plants. Manufacture of limestone calcined clay cement: This is a new development based on researches carried out by Karen Scrivener?s lab at the Swiss Federal Institute of Technology (EPFL) at Lausanne in Switzerland. This technology which is named as LC3 technology looks to be very promising for India considering the saving of clinker in making such cements. It is reported that a composition of 50 per cent clinker ,30 per cent calcined clay, 15 per cent limestone and 5 per cent gypsum gives a product which has equivalent performance as OPC.
IIT Delhi, IIT Madras and Tara (Technology and action for rural development) has tied up with EPFL to develop LC3 with Indian calcined clays and limestones. J.K.Laxmi Jhazzar unit has carried a commercial production of LC3. Plants would need only a calciner for calcining clay as an additional equipment for manufacturing LC3. It is claimed that LC3 can give good performance even with low grade limestone and calcined clays made from poor quality clays at the finish grinding stage. Extensive research is needed to prove the point whether this product can reduce the consumption of Indian cement grade limestone and enable use of large deposits of low grade limestone and over burden clays accumulating in the mines of cement plants. Reactive belite cement: Most of the clinkers manufactured in India are predominantly belitic in nature. Efforts are needed to activate the belite phase in a cost effective manner so as to achieve similar performance as C3S rich clinker and also make finish grinding easier. More research efforts are necessary in this area as this could result in conserving our limited high grade limestone deposits.
Customer education and use of right cement for an application
Indian cement customer especially in the rural regions need extensive education to use the right type of cement for a particular application. For eg. 33 grade OPC is more than sufficient for general construction but customers use 43 grade. The contention is that one can use less cement if it of higher strength. This concept is technically detrimental to concrete. Also in many regions there is an apathy to use PPC and more so in Government projects which is a waste of natural resources . Masonary cements are not in vogue in the country and plastering also is done by 43 grade. This has to be taken up as a national movement with the participation of R&D organisations and the industry. When we use more of lower grade cements and blended cements we are ultimately conserving our reserves of cement grade limestones.
Conclusions
From the above study it can be concluded that there is an urgent need for detailed exploration of limestone deposits in India to establish more limestone reserves from the existing resources as per UNFC classification. Systematic mine planning and multi-mine scheduling is essential to maximise the use of quarry rejects. This should be the thrust area for immediate implementation. Remote Quarry Management especially for plants in a group can prove to be the best business model for mining management in Indian Cement Industry. This model uses the concept of utilising an external expert with all modern IT-enabled services supported by state of art mining software to monitor mining operations. More studies on cost effective dry beneficiation techniques for enrichment of low grade limestone is essential.
The encouragement for production of reactive belite cement, Sulfo-aluminate (C4A3S) belite cement and LC3 in India will provide better solutions for conserving high grade limestone deposits in a sustainable manner. Presently Sulpho-aluminate belite cements are produced commercially in many countries for various applications successfully. More over these cements have immense potential for utilisation of low grade limestone as well as various industrial wastes for manufacture and they are eco-friendly as they release much less CO2 in production as compared to Portland cements. Cements using less and less clinker component needs to be promoted in the country.
Acknowledgement
The authors are thankful to AKS University, Satna management to provide all the support and permission to publish this article.
References
1.Reports of the Working Group on Cement Industry for XII Five Year Plan: Department of Industrial Policy and Promotion, Ministry of Commerce and Industry, Govt of India ( December 2011).
2.Performance of Sulfo-aluminate belite cement with high C4A3S Content: Ivan Janotka, L?udovitKrajci, Subhash C Manjumdar : Ceramic ?Silikaty 31 (2) 74-81 (2007).
3.Synthesis of Calcium Sulfoaluminate Cements from Al2O3-Rich by products from Aluminium Industry. Milena Marro, Maria Lucia Pace, AnotonioTelesica and Gian Lorenzo Valenti: Second International Conference on Sustainable Construction Materials and Technologies: 28-30 June, 2010 UniversitaPolitecnicadella Marche, Ancona, Italy.
4.Beneficiation studies of the Limestone of Malkhed Areas, Gulbarga District, Karnataka: Chinnaiah, Sunil Kumar R K, Basavarajappa H T and Madesh P. International Journal of Earth Science and Engineering: Volume 05, No.01 : February 2012: pp 186-192.
5.Hydrating Behaviour of Activated Belite Sulfoaluminate Cements : Aranda, M A G., Cuberos, A J M., Cuesta A., Alvarez-Pinazo, De la , A G.
6.Beneficiation studies on low grade limestone of Shahabad Area, Shahabad, Gulbarga District, Karnataka: MR Patil and M V Rudramuniyappa : Proceedings of the XI International Seminar on Mineral Processing Technology (MPT-2010): pp 725-729.
7.Remote Quarry Management- S.S. Rawat and P.K.Sarkar, Holtec Consulting Pvt. Ltd.
Around 95% of cement grade limestone deposits are concentrated in 10 states, although the cement grade limestone is occurring in 23 States in smaller quantities.
In India most of the cement plants are operating on heterogeneous intricate limestone deposits with the result that mine reject generation is high..
Authors: HKN Bhattacharjee and GC Mishra of AKS University, Satna (Madhya Pradesh), India.
You may like
Concrete
India donates 225t of cement for Myanmar earthquake relief
Published
2 months agoon
June 17, 2025By
admin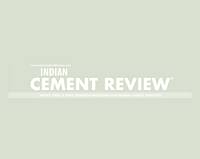
On 23 May 2025, the Indian Navy ship UMS Myitkyina arrived at Thilawa (MITT) port carrying 225 tonnes of cement provided by the Indian government to aid post-earthquake rebuilding efforts in Myanmar. As reported by the Global Light of Myanmar, a formal handover of 4500 50kg cement bags took place that afternoon. The Yangon Region authorities managed the loading of the cement onto trucks for distribution to the earthquake-affected zones.
Concrete
Reclamation of Used Oil for a Greener Future
Published
2 months agoon
June 16, 2025By
admin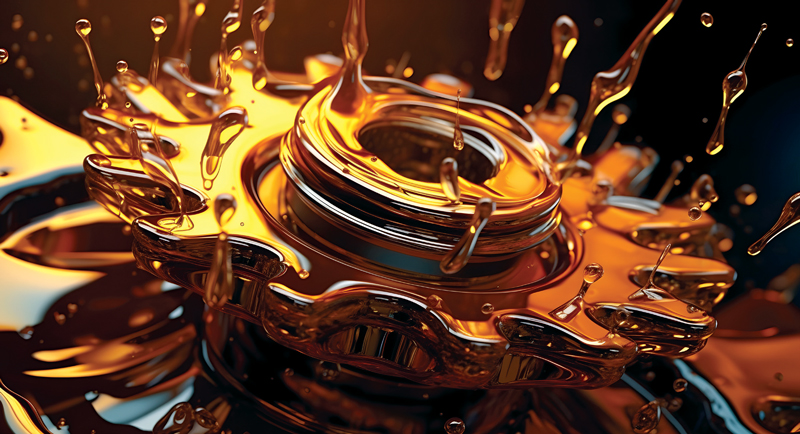
In this insightful article, KB Mathur, Founder and Director, Global Technical Services, explores how reclaiming used lubricants through advanced filtration and on-site testing can drive cost savings, enhance productivity, and support a greener industrial future. Read on to discover how oil regeneration is revolutionising sustainability in cement and core industries.
The core principle of the circular economy is to redefine the life cycle of materials and products. Unlike traditional linear models where waste from industrial production is dumped/discarded into the environment causing immense harm to the environment;the circular model seeks to keep materials literally in continuous circulation. This is achievedthrough processes cycle of reduction, regeneration, validating (testing) and reuse. Product once
validated as fit, this model ensures that products and materials are reintroduced into the production system, minimising waste. The result? Cleaner and greener manufacturing that fosters a more sustainable planet for future generations.
The current landscape of lubricants
Modern lubricants, typically derived from refined hydrocarbons, made from highly refined petroleum base stocks from crude oil. These play a critical role in maintaining the performance of machinery by reducing friction, enabling smooth operation, preventing damage and wear. However, most of these lubricants; derived from finite petroleum resources pose an environmental challenge once used and disposed of. As industries become increasingly conscious of their environmental impact, the paramount importance or focus is shifting towards reducing the carbon footprint and maximising the lifespan of lubricants; not just for environmental reasons but also to optimise operational costs.
During operations, lubricants often lose their efficacy and performance due to contamination and depletion of additives. When these oils reach their rejection limits (as they will now offer poor or bad lubrication) determined through laboratory testing, they are typically discarded contributing to environmental contamination and pollution.
But here lies an opportunity: Used lubricants can be regenerated and recharged, restoring them to their original performance level. This not only mitigates environmental pollution but also supports a circular economy by reducing waste and conserving resources.
Circular economy in lubricants
In the world of industrial machinery, lubricating oils while essential; are often misunderstood in terms of their life cycle. When oils are used in machinery, they don’t simply ‘DIE’. Instead, they become contaminated with moisture (water) and solid contaminants like dust, dirt, and wear debris. These contaminants degrade the oil’s effectiveness but do not render it completely unusable. Used lubricants can be regenerated via advanced filtration processes/systems and recharged with the use of performance enhancing additives hence restoring them. These oils are brought back to ‘As-New’ levels. This new fresher lubricating oil is formulated to carry out its specific job providing heightened lubrication and reliable performance of the assets with a view of improved machine condition. Hence, contributing to not just cost savings but leading to magnified productivity, and diminished environmental stress.
Save oil, save environment
At Global Technical Services (GTS), we specialise in the regeneration of hydraulic oils and gear oils used in plant operations. While we don’t recommend the regeneration of engine oils due to the complexity of contaminants and additives, our process ensures the continued utility of oils in other applications, offering both cost-saving and environmental benefits.
Regeneration process
Our regeneration plant employs state-of-the-art advanced contamination removal systems including fine and depth filters designed to remove dirt, wear particles, sludge, varnish, and water. Once contaminants are removed, the oil undergoes comprehensive testing to assess its physico-chemical properties and contamination levels. The test results indicate the status of the regenerated oil as compared to the fresh oil.
Depending upon the status the oil is further supplemented with high performance additives to bring it back to the desired specifications, under the guidance of an experienced lubrication technologist.
Contamination Removal ? Testing ? Additive Addition
(to be determined after testing in oil test laboratory)
The steps involved in this process are as follows:
1. Contamination removal: Using advanced filtration techniques to remove contaminants.
2. Testing: Assessing the oil’s properties to determine if it meets the required performance standards.
3. Additive addition: Based on testing results, performance-enhancing additives are added to restore the oil’s original characteristics.
On-site oil testing laboratories
The used oil from the machine passes through 5th generation fine filtration to be reclaimed as ‘New Oil’ and fit to use as per stringent industry standards.
To effectively implement circular economy principles in oil reclamation from used oil, establishing an on-site oil testing laboratory is crucial at any large plants or sites. Scientific testing methods ensure that regenerated oil meets the specifications required for optimal machine performance, making it suitable for reuse as ‘New Oil’ (within specified tolerances). Hence, it can be reused safely by reintroducing it in the machines.
The key parameters to be tested for regenerated hydraulic, gear and transmission oils (except Engine oils) include both physical and chemical characteristics of the lubricant:
- Kinematic Viscosity
- Flash Point
- Total Acid Number
- Moisture / Water Content
- Oil Cleanliness
- Elemental Analysis (Particulates, Additives and Contaminants)
- Insoluble
The presence of an on-site laboratory is essential for making quick decisions; ensuring that test reports are available within 36 to 48 hours and this prevents potential mechanical issues/ failures from arising due to poor lubrication. This symbiotic and cyclic process helps not only reduce waste and conserve oil, but also contributes in achieving cost savings and playing a big role in green economy.
Conclusion
The future of industrial operations depends on sustainability, and reclaiming used lubricating oils plays a critical role in this transformation. Through 5th Generation Filtration processes, lubricants can be regenerated and restored to their original levels, contributing to both environmental preservation and economic efficiency.
What would happen if we didn’t recycle our lubricants? Let’s review the quadruple impacts as mentioned below:
1. Oil Conservation and Environmental Impact: Used lubricating oils after usage are normally burnt or sold to a vendor which can be misused leading to pollution. Regenerating oils rather than discarding prevents unnecessary waste and reduces the environmental footprint of the industry. It helps save invaluable resources, aligning with the principles of sustainability and the circular economy. All lubricating oils (except engine oils) can be regenerated and brought to the level of ‘As New Oils’.
2. Cost Reduction Impact: By extending the life of lubricants, industries can significantly cut down on operating costs associated with frequent oil changes, leading to considerable savings over time. Lubricating oils are expensive and saving of lubricants by the process of regeneration will overall be a game changer and highly economical to the core industries.
3. Timely Decisions Impact: Having an oil testing laboratory at site is of prime importance for getting test reports within 36 to 48 hours enabling quick decisions in critical matters that may
lead to complete shutdown of the invaluable asset/equipment.
4. Green Economy Impact: Oil Regeneration is a fundamental part of the green economy. Supporting industries in their efforts to reduce waste, conserve resources, and minimise pollution is ‘The Need of Our Times’.
About the author:
KB Mathur, Founder & Director, Global Technical Services, is a seasoned mechanical engineer with 56 years of experience in India’s oil industry and industrial reliability. He pioneered ‘Total Lubrication Management’ and has been serving the mining and cement sectors since 1999.
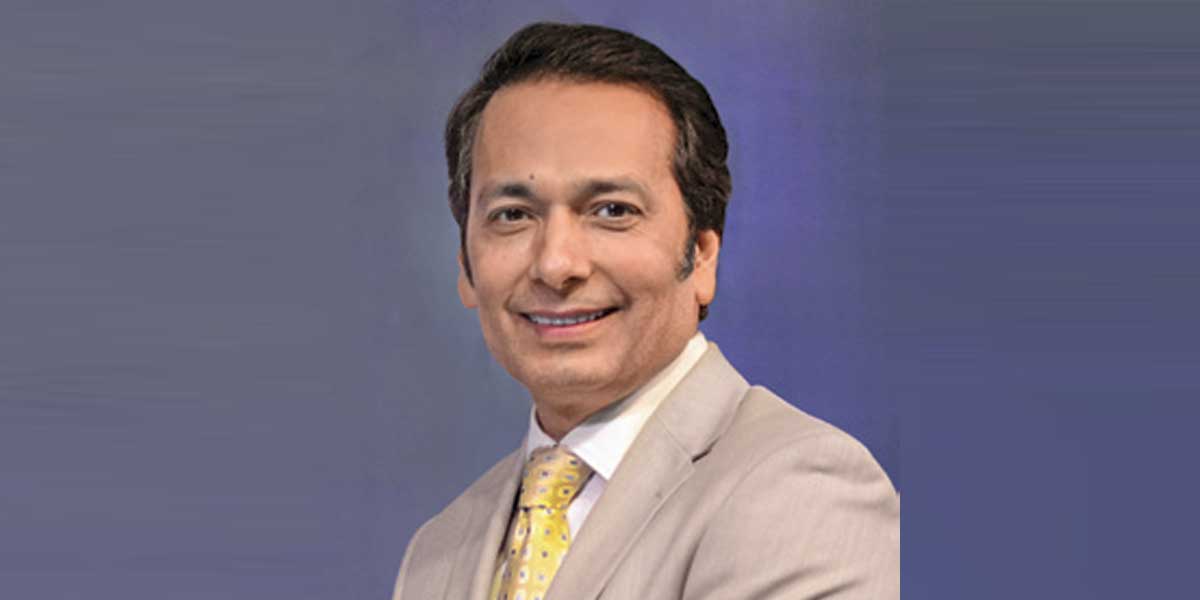
The Indian cement industry has reached a critical juncture in its sustainability journey. In a landmark move, the Ministry of Environment, Forest and Climate Change has, for the first time, announced greenhouse gas (GHG) emission intensity reduction targets for 282 entities, including 186 cement plants, under the Carbon Credit Trading Scheme, 2023. These targets, to be enforced starting FY2025-26, are aligned with India’s overarching ambition of achieving net zero emissions by 2070.
Cement manufacturing is intrinsically carbon-intensive, contributing to around 7 per cent of global GHG emissions, or approximately 3.8 billion tonnes annually. In India, the sector is responsible for 6 per cent of total emissions, underscoring its critical role in national climate mitigation strategies. This regulatory push, though long overdue, marks a significant shift towards accountability and structured decarbonisation.
However, the path to a greener cement sector is fraught with challenges—economic viability, regulatory ambiguity, and technical limitations continue to hinder the widespread adoption of sustainable alternatives. A major gap lies in the lack of a clear, India-specific definition for ‘green cement’, which is essential to establish standards and drive industry-wide transformation.
Despite these hurdles, the industry holds immense potential to emerge as a climate champion. Studies estimate that through targeted decarbonisation strategies—ranging from clinker substitution and alternative fuels to carbon capture and innovative product development—the sector could reduce emissions by 400 to 500 million metric tonnes by 2030.
Collaborations between key stakeholders and industry-wide awareness initiatives (such as Earth Day) are already fostering momentum. The responsibility now lies with producers, regulators and technology providers to fast-track innovation and investment.
The time to act is now. A sustainable cement industry is not only possible—it is imperative.