Environment
Yet to catch up
Published
7 years agoon
By
admin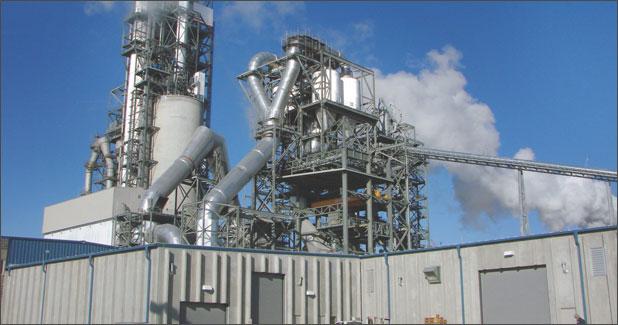
Environmental protection norms that have been revised and updated since 2014 are considered not too stringent going by global benchmarks. But the Indian industry and authorities are still in the process of finding a common ground.
The Ministry of Environment, Forest & Climate Change (MoEF&CC) has notified the new pollution norms for the Indian cement industry, which is the second largest producer in the world, in May 2016, with the primary aim of minimising pollution, in line with the country’s intent/commitments made at CoP21 at Paris last year. The deadline for which was set at March 31, 2017.
It may be recalled that India’s Paris commitments include reduction of the emissions intensity of its GDP by 33 to 35 per cent by 2030, from 2005 level; achieving about 40 per cent cumulative electric power installed capacity from non-fossil fuel based energy resources by 2030, and introduction of new, more efficient and cleaner technologies in thermal power generation.
The new pollution limits, after consultations with the industry and regulators, were notified on May 9-10, 2016, with a deadline to comply by March 31, 2017. The new norms have made particulate matter (PM) emissions stringent by bringing them from 50-150 milligrams per cubic metre (mg/Nm3) to 30 mg/Nm3. This limit depends upon the age and location of the plant.
The new norms relaxed the emission limit of sulphur dioxide and nitrogen oxide, one of the two key polluting gases released from industries. The limit of sulphur dioxide emitted from a cement plant was increased from 100 mg/Nm3 to 100-1,000mg/Nm3. This limit depends on sulphur content in limestone, a raw material for making cement. The limit for nitrogen oxide was relaxed from 600 to 800 mg/Nm3 to 600-1,000 mg/Nm3.
‘This should come as a surprise because China, which is the largest producer of cement, has set the limit for the former to 200 mg/Nm3 and for the latter to 400-800 mg/Nm3,’ say Kanika Bahel, Sanjeev Kumar Kanchan of Centre for Science and Environment (CSE). Sources of pollution
Air pollution: The cement industry is one of the major air polluting industries due to generation of dust in various processes. There are three categories of dust emission in the industry – points of emissions like raw mill, kiln, clinker cooler, cement mill and coal mill; fugitive emission sources like transfer of raw materials, intermediates and final products and during their loading/ unloading; and kiln is the primary source of dust emissions.
The dust emission can be controlled by providing adequate pollution control equipment – cyclone, ESP, bag-filters, etc., based on size of dust particles, flue gas characteristics, techno – economic feasibility and collection efficiency.Gaseous pollutants: Gaseous pollutants from the kiln are oxides of N (NOx) and SO2. Ammonia is injected into the flue gas in the high temperature zone at exit of the kiln where NOx is reduced to N2 in the presence of O2. Hydrated lime Ca (OH) 2 is injected into the flue gas to arrest SO2. Water pollution: Unlike in power plants, water is not a major pollutant in cement plants. Only the cooling tower blow-down associated with the gas conditioning tower (GCT) is a source of waste water generation, though not a major water pollutant. Noise pollution: Operation of heavy duty machines like crushers, tube mills, ball mills, fans, coolers, etc. in cement process generates noise. Noise level depends mainly upon nature, size and capacity of machines, running speed and feed material. The noise level generally varies from 70 – 118 dB.
Principally cement plants use vibration damping pads, isolating vibrating parts to reduce noise pollution, and by enclosing the source and insulating it. Personal noise protectors like, ear plugs and ear muffs are used by those working in or visiting the plants.Norms
For the first time, environment protection rules were introduced in early 1980s, through stringent dust emission regulations, where the emission standards were 250 mg/Nm3. During this period, most of the cement plants adopted ESP for all applications.
Subsequently, when the emission standards were tightened to 150 mg/Nm3, cement plants have upgraded the ESP with modern controllers, additional fields and change of electrodes. When dust emission standards have reduced to 50 mg/Nm3, cement kilns have shifted to reverse air baghouses with fibre glass bags and other applications like coal mill, cement mill, raw mill etc., shifted to low temperature bags like polyester/acrylic bags with or without antistatic treatment. However, the clinker cooler and captive plants continued with ESP technology.
In 2014, first time in India, gaseous emission standards (SO2, NOx, VOC, Mercury, NH3, heavy metals, dioxins and furans) for cement kilns and simultaneously dust emissions standards reduced to 30mg/Nm3 instead of 50 mg/Nm3, which are on par with the global best practices. Apart from the emission standards, CPCB issued a direction on February 5, 2014 about the online reporting of emissions (both Stack and ambient air) and effluents from 17 categories of industries. Further, CPCB released guidelines for continuous emission monitoring system during July 2017.
The notification calls for online reporting of emissions from all process stacks and ambient air quality stations to SPCB and CPCB on 24×7 basis and stringent reporting and compliance standard. In 2015, captive power plant (CPPs) emission reduction standard (Dust, SOx, NOx and Mercury) were introduced with varied emissions based on the vintage of the plant and also size of the plant.
Compliance timelines in both the cases, i.e., cement plants, March 31, 2017 and for CPPs up to December 7, 2017. ‘In both the cases, industry faced many technical as well as financial challenges to complete these projects. Based on the industry request, the Cement plants have been given time line extension up to August 31, 2018 and for the power plants, time line extension is not yet finalised,’ says KN Rao, Director ? Energy, Environment & Sustainability, ACC Limited.Equipment
Various types of pollution control equipment are intensively used in the cement industry to minimise dust, nuisance in the plant area so as to maintain dust free atmosphere and to maintain the dust emission level within acceptable limits. Cement plant machinery work under negative pressure to prevent dust from escaping into the atmosphere. The common pollution control equipment used in cement plants include: electrostatic precipitator (ESP), dust-bag filters, gravel-bed filters and glass bag-house.Monitoring and reporting
The monitoring and reporting protocol is also a major challenge in terms of technology option. As per the standard, the emissions are measured on a 15 minute average and non-compliance alerts are given to the companies. By design, emission from ESP varies with the process conditions and also emissions goes up while cleaning system of the electrodes takes place, especially in the outlet field. ‘This becomes a big challenge when complying with the 15 minute duration constant emission from any ESP. Global compliance standards takes one day average or 3-day emissions average or 30 days rolling average to issue compliance alert and also to action of non-compliance. Indian standard on monitoring and reporting protocol is the toughest standard at this moment,’ says Rao. Technology selection
The reporting issues posed biggest challenge for the technology selection for the control equipment. From early 1980s, there is a rapid advancement in terms of fabric filtration technology and currently newer fabrics and membranes have been developed to reduce the emissions to below 5 mg/Nm3 with a lower pressure drop and guaranteed longer life of up to 6 to 8 years. Apart from dust, the current advanced filter media is capable of reducing heavy metals, dioxins, furans and mercury. Latest regulations
MoEF&CC has issued notification on revised emission norms to cement plants on August 25, 2014 against various parameters such as PM, SO2 & NOx emissions with varied compliance timelines for various parameters from January 1, 2016 to June 1, 2016.
Final compliance timelines were further extended August 31, 2018. (Please see the emission limits for various parameters in the accompanying article by KN Rao).
Environmental NGO, CSE, is decrying dilution of the latest norms drawing parallels with that in China. Last year, the Department of Industrial Policy and Promotion (DIPP) of the Centre has recommended to MoEF&CC to relax the deadline for compliance of environment emission standards by cement units by two years.
China, which is the largest producer of cement, has set the limit for sulphur dioxide to 200 milligrams per cubic metre (mg/Nm3). India’s new norms, on the other hand, stipulate the emission limit for sulphur dioxide from 100-1,000 mg/Nm3.Global benchmarks
Countries like South Africa, Australia, Germany and many other European countries have stipulated the emission limits for sulphur dioxide as low as 50 mg/Nm3. Similarly, countries like Colombia, Germany and other European countries have nitrogen oxides emission limit as low as are 200 mg/Nm3. Besides, many countries have stipulated limits for mercury, which India is yet to do, CSE says.
Calling these latest norms as far more relaxed compared to those stipulated in other countries, CSE said the industry ‘should prepare a pragmatic action plan and implement it in a time-bound manner with proper consultation and approval from the ministry.’
In January 2018, Cement manufacturers breathed a sigh of relief after the Supreme Court of India lifted its ban on the use of petroleum coke in the cement and limestone industries. The order stated that ‘pet coke should be utilised only in industries where sulphur is absorbed in the manufacturing process, for example, [in the] cement industry, [and] gasification plants.’ The ban on pet coke first came into place in October 2017 in an attempt to address Delhi’s severe air pollution.Pollution-abbreviations
SO2: Sulphur dioxide
NOX: Oxides of Nitrogen
HCl: Hydrogen Chloride
HF: Hydrogen Flouride
TOC: Total Organic Carbon
Hg: Mercury
Cd: Cadmium
Tl: Thallium
Sb: Antimony
As: Arsenic
Pb: Lead
Co: Cobalt
Cr: Chromium
Cu: Copper
Mn: Manganese
Ni: Nickel
V: Vanadium
– B.S. SRINIVASALU REDDY
Concrete
India donates 225t of cement for Myanmar earthquake relief
Published
2 months agoon
June 17, 2025By
admin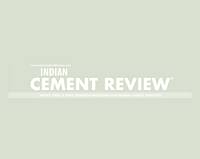
On 23 May 2025, the Indian Navy ship UMS Myitkyina arrived at Thilawa (MITT) port carrying 225 tonnes of cement provided by the Indian government to aid post-earthquake rebuilding efforts in Myanmar. As reported by the Global Light of Myanmar, a formal handover of 4500 50kg cement bags took place that afternoon. The Yangon Region authorities managed the loading of the cement onto trucks for distribution to the earthquake-affected zones.
Concrete
Reclamation of Used Oil for a Greener Future
Published
2 months agoon
June 16, 2025By
admin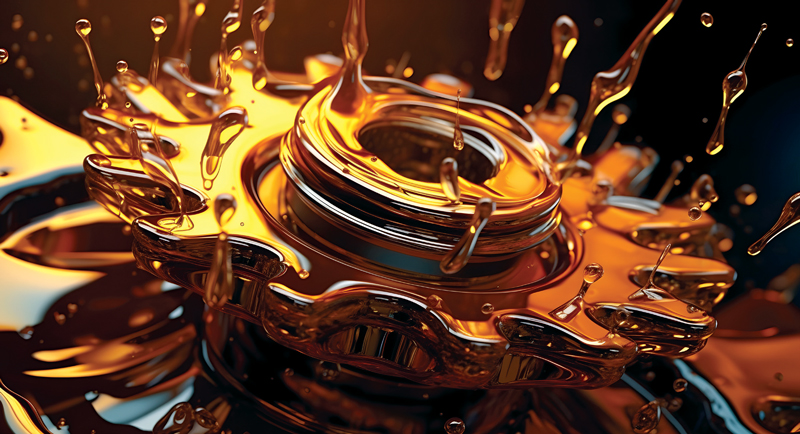
In this insightful article, KB Mathur, Founder and Director, Global Technical Services, explores how reclaiming used lubricants through advanced filtration and on-site testing can drive cost savings, enhance productivity, and support a greener industrial future. Read on to discover how oil regeneration is revolutionising sustainability in cement and core industries.
The core principle of the circular economy is to redefine the life cycle of materials and products. Unlike traditional linear models where waste from industrial production is dumped/discarded into the environment causing immense harm to the environment;the circular model seeks to keep materials literally in continuous circulation. This is achievedthrough processes cycle of reduction, regeneration, validating (testing) and reuse. Product once
validated as fit, this model ensures that products and materials are reintroduced into the production system, minimising waste. The result? Cleaner and greener manufacturing that fosters a more sustainable planet for future generations.
The current landscape of lubricants
Modern lubricants, typically derived from refined hydrocarbons, made from highly refined petroleum base stocks from crude oil. These play a critical role in maintaining the performance of machinery by reducing friction, enabling smooth operation, preventing damage and wear. However, most of these lubricants; derived from finite petroleum resources pose an environmental challenge once used and disposed of. As industries become increasingly conscious of their environmental impact, the paramount importance or focus is shifting towards reducing the carbon footprint and maximising the lifespan of lubricants; not just for environmental reasons but also to optimise operational costs.
During operations, lubricants often lose their efficacy and performance due to contamination and depletion of additives. When these oils reach their rejection limits (as they will now offer poor or bad lubrication) determined through laboratory testing, they are typically discarded contributing to environmental contamination and pollution.
But here lies an opportunity: Used lubricants can be regenerated and recharged, restoring them to their original performance level. This not only mitigates environmental pollution but also supports a circular economy by reducing waste and conserving resources.
Circular economy in lubricants
In the world of industrial machinery, lubricating oils while essential; are often misunderstood in terms of their life cycle. When oils are used in machinery, they don’t simply ‘DIE’. Instead, they become contaminated with moisture (water) and solid contaminants like dust, dirt, and wear debris. These contaminants degrade the oil’s effectiveness but do not render it completely unusable. Used lubricants can be regenerated via advanced filtration processes/systems and recharged with the use of performance enhancing additives hence restoring them. These oils are brought back to ‘As-New’ levels. This new fresher lubricating oil is formulated to carry out its specific job providing heightened lubrication and reliable performance of the assets with a view of improved machine condition. Hence, contributing to not just cost savings but leading to magnified productivity, and diminished environmental stress.
Save oil, save environment
At Global Technical Services (GTS), we specialise in the regeneration of hydraulic oils and gear oils used in plant operations. While we don’t recommend the regeneration of engine oils due to the complexity of contaminants and additives, our process ensures the continued utility of oils in other applications, offering both cost-saving and environmental benefits.
Regeneration process
Our regeneration plant employs state-of-the-art advanced contamination removal systems including fine and depth filters designed to remove dirt, wear particles, sludge, varnish, and water. Once contaminants are removed, the oil undergoes comprehensive testing to assess its physico-chemical properties and contamination levels. The test results indicate the status of the regenerated oil as compared to the fresh oil.
Depending upon the status the oil is further supplemented with high performance additives to bring it back to the desired specifications, under the guidance of an experienced lubrication technologist.
Contamination Removal ? Testing ? Additive Addition
(to be determined after testing in oil test laboratory)
The steps involved in this process are as follows:
1. Contamination removal: Using advanced filtration techniques to remove contaminants.
2. Testing: Assessing the oil’s properties to determine if it meets the required performance standards.
3. Additive addition: Based on testing results, performance-enhancing additives are added to restore the oil’s original characteristics.
On-site oil testing laboratories
The used oil from the machine passes through 5th generation fine filtration to be reclaimed as ‘New Oil’ and fit to use as per stringent industry standards.
To effectively implement circular economy principles in oil reclamation from used oil, establishing an on-site oil testing laboratory is crucial at any large plants or sites. Scientific testing methods ensure that regenerated oil meets the specifications required for optimal machine performance, making it suitable for reuse as ‘New Oil’ (within specified tolerances). Hence, it can be reused safely by reintroducing it in the machines.
The key parameters to be tested for regenerated hydraulic, gear and transmission oils (except Engine oils) include both physical and chemical characteristics of the lubricant:
- Kinematic Viscosity
- Flash Point
- Total Acid Number
- Moisture / Water Content
- Oil Cleanliness
- Elemental Analysis (Particulates, Additives and Contaminants)
- Insoluble
The presence of an on-site laboratory is essential for making quick decisions; ensuring that test reports are available within 36 to 48 hours and this prevents potential mechanical issues/ failures from arising due to poor lubrication. This symbiotic and cyclic process helps not only reduce waste and conserve oil, but also contributes in achieving cost savings and playing a big role in green economy.
Conclusion
The future of industrial operations depends on sustainability, and reclaiming used lubricating oils plays a critical role in this transformation. Through 5th Generation Filtration processes, lubricants can be regenerated and restored to their original levels, contributing to both environmental preservation and economic efficiency.
What would happen if we didn’t recycle our lubricants? Let’s review the quadruple impacts as mentioned below:
1. Oil Conservation and Environmental Impact: Used lubricating oils after usage are normally burnt or sold to a vendor which can be misused leading to pollution. Regenerating oils rather than discarding prevents unnecessary waste and reduces the environmental footprint of the industry. It helps save invaluable resources, aligning with the principles of sustainability and the circular economy. All lubricating oils (except engine oils) can be regenerated and brought to the level of ‘As New Oils’.
2. Cost Reduction Impact: By extending the life of lubricants, industries can significantly cut down on operating costs associated with frequent oil changes, leading to considerable savings over time. Lubricating oils are expensive and saving of lubricants by the process of regeneration will overall be a game changer and highly economical to the core industries.
3. Timely Decisions Impact: Having an oil testing laboratory at site is of prime importance for getting test reports within 36 to 48 hours enabling quick decisions in critical matters that may
lead to complete shutdown of the invaluable asset/equipment.
4. Green Economy Impact: Oil Regeneration is a fundamental part of the green economy. Supporting industries in their efforts to reduce waste, conserve resources, and minimise pollution is ‘The Need of Our Times’.
About the author:
KB Mathur, Founder & Director, Global Technical Services, is a seasoned mechanical engineer with 56 years of experience in India’s oil industry and industrial reliability. He pioneered ‘Total Lubrication Management’ and has been serving the mining and cement sectors since 1999.
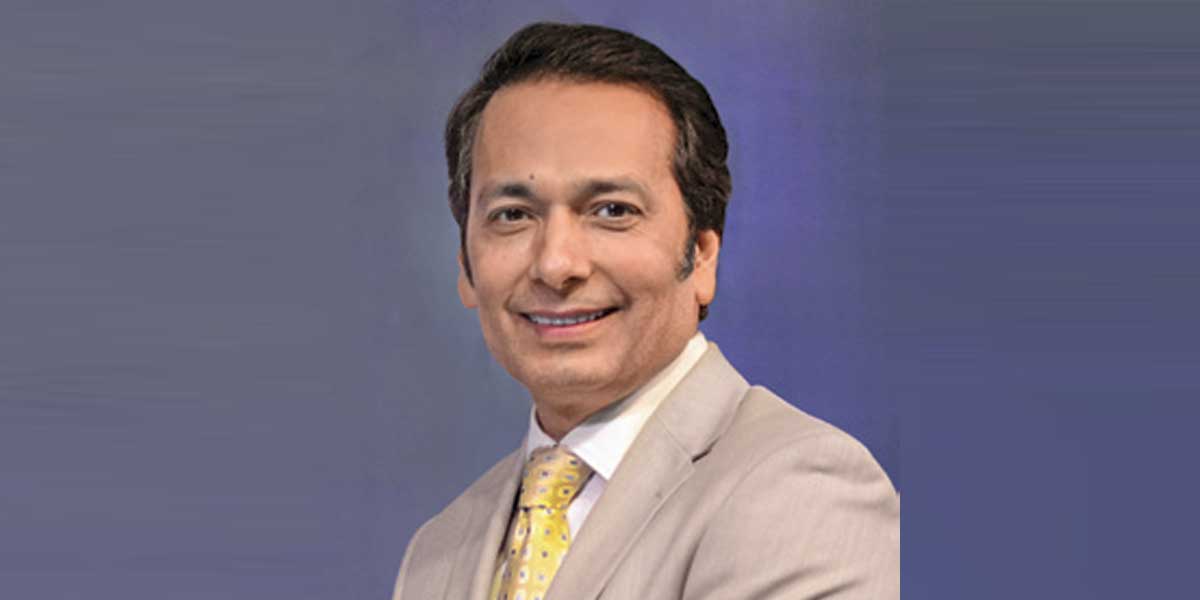
The Indian cement industry has reached a critical juncture in its sustainability journey. In a landmark move, the Ministry of Environment, Forest and Climate Change has, for the first time, announced greenhouse gas (GHG) emission intensity reduction targets for 282 entities, including 186 cement plants, under the Carbon Credit Trading Scheme, 2023. These targets, to be enforced starting FY2025-26, are aligned with India’s overarching ambition of achieving net zero emissions by 2070.
Cement manufacturing is intrinsically carbon-intensive, contributing to around 7 per cent of global GHG emissions, or approximately 3.8 billion tonnes annually. In India, the sector is responsible for 6 per cent of total emissions, underscoring its critical role in national climate mitigation strategies. This regulatory push, though long overdue, marks a significant shift towards accountability and structured decarbonisation.
However, the path to a greener cement sector is fraught with challenges—economic viability, regulatory ambiguity, and technical limitations continue to hinder the widespread adoption of sustainable alternatives. A major gap lies in the lack of a clear, India-specific definition for ‘green cement’, which is essential to establish standards and drive industry-wide transformation.
Despite these hurdles, the industry holds immense potential to emerge as a climate champion. Studies estimate that through targeted decarbonisation strategies—ranging from clinker substitution and alternative fuels to carbon capture and innovative product development—the sector could reduce emissions by 400 to 500 million metric tonnes by 2030.
Collaborations between key stakeholders and industry-wide awareness initiatives (such as Earth Day) are already fostering momentum. The responsibility now lies with producers, regulators and technology providers to fast-track innovation and investment.
The time to act is now. A sustainable cement industry is not only possible—it is imperative.