Technology
Paradigm shift in RMC safety
Published
6 years agoon
By
admin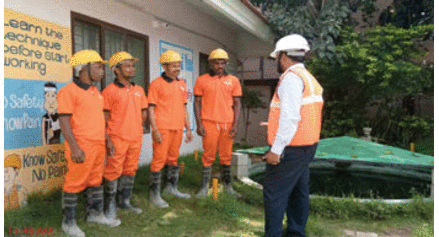
Challenges of creating a safe environment in "ready mix industry" is compounded by the interlinked but distinct environment. RDC Concrete believe that the challenges are catalyst in creating safe working spaces.
Life is the invaluable gift given to us. For centuries, we survived on instinct and many of our forefathers perished as instinct is not always right and even if it is right, it is many times too late to react. This has now been recognised and form safety systems and audit have been put in place for many decades now. Developed world is far advanced in implementing safety systems and processes. In India, we are far behind. More specifically, construction is not known for complying with safety measures. Although wearing helmets and safety shoes are now compulsory, one can look at any site and we will find a large number of people working there bare-headed and in slippers.
Ready mix concrete (RMC) is not exactly construction industry but is inseparably linked with it. There are variety of hazards involved during the processes of receiving the raw materials, processing it in a plant (plant safety), transporting it on the road (road safety) and delivering the finish product at the customer construction site (site safety). At customer’s site, it is poured in to formwork manually or by pumping to a required height reaching up to 400 m. Challenges in creating a safe environment in ready-mix industry is thus compounded by the interlinked but three distinct environments. In RDC, the challenges are the catalyst in creating safe working spaces. While it is difficult to compute deaths in RMC industry in percentage terms; based on the data presented, it is quite obvious that "Falls" and "Road Accidents" constitutes the main element of deaths in this industry. Road accidents frequently occur because the transit mixer carrying RMC while rotating it in a drum is an additional hazard on the road. Falls occur because of working at height while pouring concrete at higher levels. These are the primary challenges that need to be addressed in this industry. RDC concrete has had zero fatality in the last many years.
Delivering concrete is basically a three step process 1) Manufacturing it at batching plant 2)carrying it to the customer site using transit mixer 3) Pumping and levelling it in to the desired shuttering. All these processes have their own safety, environmental and health impacts. To mitigate these hazards and impact, we trust that our systems shall be fool-proofed. In journey to achieve this aim we implemented many best practices in our plants, in transit mixers and at delivery sites also. Some of amongst them are:
Design safety: First and foremost important is the planning for safe operations, while making layout selection of equipment and building safety features during construction of RMC plant. Plant layout has to be good to avoid criss-crossing of vehicles and smooth flow with minimum reversing of any vehicle. Hence special attention is required during construction of RMC plant of all equipment suppliers, user and safety expert.
During construction stage all safety provisions in plant should be provided like barricading of moving parts like belt conveyor, blower, compressor, isolation lock out tag out during maintenance, containment of diesel storage, barricading of water tank pits, locking arrangement for silo ladder to avoid unauthorised access, fire extinguishers, water sprinkling system to prevent dust during aggregate unloading, bag filters for silos to contain cement/fly ash dust during unloading, RCCBs to prevent electrocution, fire extinguishers for different applications, proper covering of all electrical panels, adequate earthing and lightening arrestors, first aid box, PPEs, fall arrestor, etc.
Training: Training to staff and workers is one of the main aspects for improving safety compliance as attrition rate is very high among plant workers, drivers and pump gang. Display of safety provisions, SOP posters, assembly points, etc. should be done adequately in plant.
Health check: To ensure the good health of employee and workers routines check on blood pressure, sugar, eye sight and BMI, etc. are to be regularly carried out in the plant using portable BP/BMI machines or organising camp at plant. Employee’s annual health check is also should be done as per company policy to detect any warning signs.
Safety in plant operations
A-Type Lock: This is mechanical interlocking between the main operating panel and plant mixer’s gate, using two special lock having only one common key. As there is only one key operator can either keep the panel on or keep the mixer open, that means when the main panel is on no one can open mixer gate and when the mixer gate will open no one can start the mixer panel. This will completely eliminate chances of accidents during mixer maintenance, whenever people are inside the mixer for chipping or repairs.
Silo top PRV cover: Pressure release valves (PRV) are installed on silo top, which gets open in case of sudden increase in pressure inside silo during material filling. We must ensure that this safety item is procured from reputed parties and regularly cleaned to avoid dust accumulation, which hinders spring mechanism to function.
Flushing of Bulker during unloading: Due to faulty bulker design, all material like cement or fly ash is not getting unloaded in to silo by blowing at normal pressure of 0.9bar and driver resort to pressuring bulker by closing outlet and suddenly releasing it to flush out last left out material in bulker. This is leading to opening of PRV and discharging material in surrounding atmosphere creating pollution and nuisance for neighbors. To control this we created a handy cover over PRV to contain this emitted dust and transfer it to dust collector at bottom. The design is in-house made and created with very low cost, using spare/ used chemical drums, but giving excellent result in dust control.
Calibration from Ground floor: Earlier in plants, employees were risking their life by climbing on mixer top for calibration of cement hopper, this activity is now made risk free by extending cables from the cement hopper till ground floors, with platform hanging on it. This arrangement facilitate employees to do the calibration from ground floor itself, thus avoiding the hazard of falling from height.
Lifeline and grabber: Plant people have to regularly climb on vertical ladder of silo for many jobs Like, PRV checking, stock measurement, etc. All silo’s vertical ladders are now equipped with lifeline and grabber system, this eliminate the risk of falling from silo height. In case of person slip from ladder the grabber will get locked on lifeline and hold the person in its position. Alternatively scaffold staircase should be installed in silo for safe climbing with all silos interconnected at top.
Safety during transportation
To ensure the safety in transportation of concrete, all the aspects of road safety need to be covered. Concrete carrying trucks have agitator drum to delay onset of hardening process of concrete. This drum revolution of 3RPM, shifts concrete on one side leading to shifting of centre of gravity, which keep on changing at curve roads. At high speed at road turning, combined effect of tilting of drum and moment of inertia may lead to toppling of concrete trucks. Many instances of concrete truck toppling reported in various cities due to this reason. Hence training to driver is of utmost importance because driving a concrete truck is a different ball game than an ordinary truck.
To avoid road accident and toppling of trucks due to over speeding, speed limit for transit mixer has to be kept 40 km/hr, and it is to be made sure by installing speed governors in TM, which will not allow driver to increase speed beyond limit set in speed governor. GPS are being installed in trucks to get alert for over-speeding and also voice alert for drivers. Immediate SMS is also going to the truck owner, plant in-charge and safety officer of the organisation. Drivers are being rewarded for safe driving and with minimum violations. It additionally prompts for wearing seat belt also once vehicle is started.
On road, drivers have to deal with various unseen factors that can affect their driving and they have to be fully trained to handle such factors. Training on defensive driving should be given to improve their driving skills and reducing their driving risks by anticipating situations and making safe well-informed decisions.
Driving under the influence of alcohol and drugs is one of the major causes of all road accidents. Alcohol checking should be done for drivers before leaving and coming back to the plant and educate to them about the life threatening consequences of having alcohol during driving. Engagement programme by involving drivers family helps in improving behavior change were quite successful. A poster showing family and message saying "your family is waiting for you at home is fixed in all transit mixers and form that points onwards we observed a considerable reduction in rash driving cases. To improve the safety condition of transit mixer and safety of driver all the transit mixer should be well maintained and equipped with side guard, front guard, reflective stickers, condition of brakes, reverse horn and side mirrors. Drivers have to ensure that safety inspection of TM is done regularly and pictorial checklist is maintained. Drivers should be in full PPE during driving and on site. All the road safety rules need to be followed such as seatbelt, road signs, maintain safe distance, etc. One experienced driver can be entrusted the job of checking condition of all trucks by driving it for certain distance helps in identifying issues while driving.
Safety during pumping operations
Placing of concrete at site is done by various means like pumping, tower crane, builder’s hoist, etc. and it has to be ensured that all the safety rules are followed. During pumping of concrete, safe site condition needs to be ensured by proper inspection of site before placement of pump at safe location. Soil and ground condition where concrete pump need to be placed, should be properly levelled and clear accessibility of trucks to the concrete pump maintained. Pipe line should not be very old or with leakage as pumping pressure in pipeline is very high and deteriorated pipeline can leads to major accident. Magnetic thickness gauge should be used to check thickness of pipe and pipes with lesser thickness than desired should be discarded. Scaffolding condition of slab needs to be check before start of pipe line laying, which should be dependent of the scaffold supporting the pipeline to avoid transmission of jerk to the main slab scaffold. Bamboo scaffolding must be avoided proper interconnection is not possible as compared to steel scaffold which has locks and pins to ensure good connection.
Pipe lifting clamp: Site gang were struggling from long time to carry concrete pipes. As per earlier practice, two persons used to lift pipes facing each other, but after using this holding clamp, both person can now walk in forward direction. Pump gang should use proper PPEs required for the job like hard helmet, safety shoe, reflective jacket, safety harness and goggles. Training should be given to them about all possible hazards and their mitigation plan. Pump supervisor must be made responsible during shifting and laying of pipeline safely.
Pump should be maintained with necessary safety features and no bypassing should be allowed. Regular inspection by equipment manufacturer helps in detecting the bypassing of any safety feature. The concrete pump operator should be well trained in the operation of the pump and should be made accountable for the safety in and around the pump. He also ensures the placing crew and the ready-mix driver are observing safe practices for a successful concrete placement. Concrete pumping is the most efficient way to place concrete and if all safety concerns are addressed before, during, and after a placement, the chance for accidents will be minimized.
Barricade around slab is normally missing during concrete operations and it should be brought to the notice of contractor and installed. Slab openings left uncovered at lower floors with poor lighting also pose serious danger to the pipeline gang during pipe shifting operation. Lift shaft should be avoided for pipeline laying if intermediate platforms are not made for proper pipeline laying. No overhead crane should work just above the pump and truck position to avoid falling of any object due to loose material and serious damage.
Remote indicator for Pump at site: On the site when pump placed at ground floor and delivery going on at some elevated floor, gang supervisor many time need to come to the edge of shuttering to instruct pump operator, this involves high risk of falling from height. To eliminate this we developed remote signalling system for pump operator. Gang supervisor is using handheld remote control to give signal to pump operator to start or stop the pump without risking his life.
Hazards reporting: Hazards reporting is the key in plant safety, and we should make the best use of available technologies. Plant staff can use their smartphone to report hazards with a photograph in the Google forms and the same is instantly get shared with other plants for information and action. Almost all reports can be in Google forms or on Google Drive, which can save a lot of time, and thus help in immediate action to attend to safety issue.
The article is authored by Anil Kumar Banchhor, MD & CEO of RDC Concrete since June 2016. Earlier he was CEO- Concrete Business of ACC Limited and also worked in Tata Consulting Engineers. He is a civil engineer with PG Diploma in Business management having 30 years of experience in construction, consultancy and Ready mix concrete. He worked with several construction and consultancy assignments in India and abroad. He is a panel member of the codal committee of BIS (Bureau of Indian standards) and was council member of "Indian Roads Congress" in 2006.
You may like
Economy & Market
We are shaping the future of clean air
Published
1 month agoon
April 16, 2024By
admin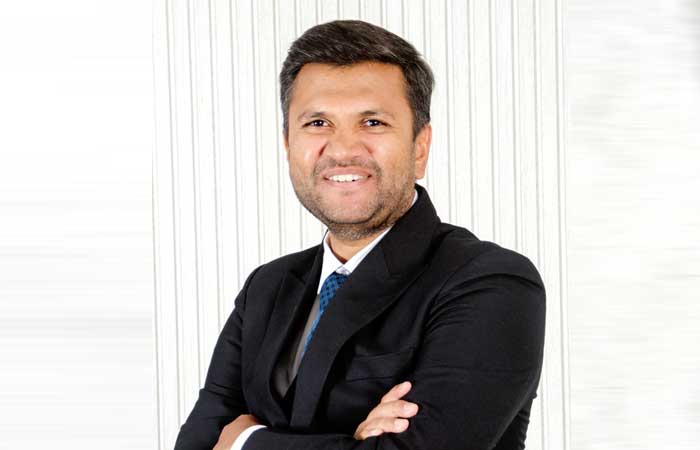
Monil Parikh, Managing Director, Techflow Enterprises Pvt Ltd, leads us to a better understanding of how cutting-edge designs and advanced technologies are revolutionising the process of filtration, driving efficiency and environmental responsibility within the cement sector.
Tell us about your air pollution control systems.
Techflow Enterprises, operating from our expansive 30,000 sq m facility, which is one of India’s largest, manufactures a comprehensive suite of air pollution control systems specifically designed for cement plants. Our solutions include:
Pulse Jet Bag Filters: Employing compressed air for efficient cleaning, these capture fine dust particles generated during grinding and packing. Techflow’s bag filters are designed to restrict the outlet emission up to 5mg/Nm3.
Electrostatic Precipitators (ESPs): Ideal for ultra-fine particulate matter in kiln exhaust gases, ESPs utilise an electric field for superior dust capture with 99.9 per cent capacity.
Centrifugal Fans: We offer various fans like induced draft (ID) fans for draft creation, process fans for dust-laden air transport, and kiln fans for high-temperature gas streams.
Techflow’s commitment to quality is evident in our proven track record. We are actively supplying solutions to leading cement players like Adani Cements, Ambuja and ACC Cement, Dalmia Bharat Cement and Wonder Cement. Our installations across India and Asia stand as a testament to our expertise in handling cement plant dust control challenges.
How do your products and systems integrate with cement plants?
Techflow’s air pollution control systems seamlessly integrate into your existing cement plant. Our pulse jet bag filters fit effortlessly downstream of grinding mills and packing stations, effectively capturing fine dust particles generated during these processes. Electrostatic Precipitators (ESPs) excel in kiln exit gas streams, working alongside existing cyclones to achieve ultra-fine particulate control, a critical step in maintaining clean air emissions.
Techflow’s comprehensive offering of centrifugal fans ensures a perfect fit for any application. Our ID fans seamlessly integrate into the kiln system, creating the necessary draft to pull exhaust gases through the air pollution control equipment. Process fans, strategically placed throughout the plant, efficiently convey dust-laden air from various generation points, like clinker coolers and raw material handling, towards the filtration units. This modular approach minimises disruption during installation and ensures optimal dust collection across your entire cement production process.
How do your innovative designs better the process of filtration at cement plants bringing efficiency to the process?
Techflow’s commitment to innovation translates to superior filtration efficiency and operational cost savings for cement plants. Our pulse jet bag filters incorporate features like:
- High-efficiency filter media: Designed for specific dust types, this media minimises pressure drop across the filter, reducing energy consumption.
- Improved flue gas entry design
- Low Pressure Cleaning Systems
- Optimised pulse cleaning systems: These systems efficiently dislodge dust cake buildup using compressed air, maximising filter media life, and minimising downtime.
Our ESPs utilise advanced electrode designs to enhance particle collection and reduce maintenance intervals. Furthermore, Techflow’s centrifugal fans are meticulously crafted for superior aerodynamic performance, leading to lower energy consumption and improved overall plant efficiency.
Techflow has developed a SMART-LINK automation module for better maintenance and real-time remote tracking of performance of each equipment. Cement plants equipped with Techflow’s systems experience reduced operational costs, minimised downtime and compliance with ever-evolving environmental regulations.
What is the key differentiator between traditional filters and modern filters?
Traditional bag filter systems often relied on manual cleaning methods, leading to inconsistent performance, increased downtime, and potential worker exposure to dust. Modern pulse jet bag filters, like those offered by Techflow, address these limitations.
Our systems leverage automated cleaning mechanisms, ensuring consistent filtration efficiency and minimal operator intervention. Additionally, advanced filter media materials in Techflow’s bag filters offer superior dust capture capabilities compared to traditional fabric filters.
This commitment to modern technology translates to a safer and more efficient and environmentally friendly dust control solution for cement plants.
Can your designs be customised as per the requirement of the customers?
At Techflow, we understand that every cement plant has unique dust control requirements. That is why we prioritise customisation across our entire product range:
Pulse Jet Bag Filters: Filter media type and micron rating based on dust properties, number of filter bags, and pulse cleaning system configuration like cycle time and pressure can all be adjusted to optimise performance for your specific dust and airflow. The system can be designed to achieve less than 5mg/Nm3 outlet emission standards as well.
- Electrostatic Precipitators (ESP): ESP design can be customised with features like the number of electrode rows, electrode spacing, and power input like voltage and current to achieve the desired dust collection efficiency for your specific outlet emission capacity less than 20mg/Nm3.
- Centrifugal Fans: Fan designs are tailored by adjusting factors like impeller diameter, blade design, and motor size to meet the specific pressure and flow requirements of various processes within a cement plant.
This focus on customisation ensures Techflow’s air pollution control systems perfectly match your cement plant’s needs, guaranteeing optimal dust capture and efficient operation.
What is the role of technology and automation in building filtration systems?
Techflow has designed a SMART-LINK System that can be integrated to our equipment which tracks and monitors performance of equipment in real time.
- Continuous diagnostics
- Condition-based maintenance
- Prevention of unplanned downtime
- Early problem detection using AI
- Data collection for process optimisation and efficiency maximisation
- Auto alert with warning driving timely human interactions
- Remote maintenance assistance by Techflow Team.
What are the major challenges in the filtration process and your system integration at cement plants?
The cement industry’s focus on sustainability, higher production and diverse fuel sources creates filtration hurdles. Adapting to changing dust properties, handling increased dust loads, and integrating seamlessly within space constraints are key challenges.
Techflow tackles these issues through advanced design techniques, exploration of innovative filter media, and modular system design. This ensures our filtration systems remain adaptable, efficient and seamlessly integrated within your cement plant, empowering your success.
How do you plan to further better your products and bring innovation in the future?
At Techflow, we are not just building filtration systems, we are shaping the future of clean air in the Indian cement industry. After successful expansion of the manufacturing facility in 2023, now it is time to improve designs and process optimisation. The future holds exciting possibilities: next-generation filter media with self-cleaning properties and
extended lifespans, minimising maintenance and maximising efficiency.
Techflow’s legendary after-sales support is about to get even better. We are expanding our global service network to provide you with 24/7 access to a team of India’s most experienced filtration specialists, ensuring your system operates flawlessly throughout its lifecycle.
Together, we will lead the way towards a sustainable future, paving the path for a greener tomorrow with green cement.
- –Kanika Mathur
Economy & Market
Digitalisation is changing the logistics landscape
Published
1 month agoon
April 16, 2024By
admin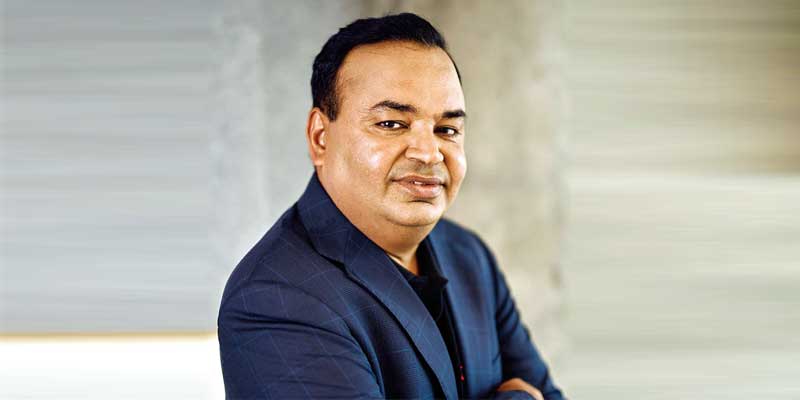
Haresh Calcuttawala, CEO and Co-Founder, Trezix, explains how their platform streamlines export processes, optimises logistics operations, and addresses the challenges faced by the cement industry.
How does your platform help in the compliance of cement exports?
The Trezix platform helps with the end-to-end processes for exporters, ensuring complete visibility of these processes focusing on shipments, documents, compliances, etc. The platform is also integrated with various stakeholders’ part of the export process including integration with Unified Logistics Integration Platform (ULIP) by the Government of India.
What is the impact of your systems on the cost and productivity of a cement plant?
The Trezix platform helps to optimise the turnaround time, visibility of shipment and improving efficiencies, which results in optimisation in logistics cost and improvement in working capital.
What are the major challenges in logistics and how can that be resolved?
A major challenge in the cement industry is the logistics cost and time for delivery. This can only be resolved with faster turnaround time, complete visibility of shipments, delivery lead time and process control to adhere to compliance.
Tell us your views on the change technology is bringing to logistics.
In the cement industry, so far technology has been more focused on internal process, and optimising demand and supply in the area of supply chain. However, now the focus has completely shifted to external stakeholders and their processes, and how have we integrated processes to further optimise the logistics execution.
Can your systems and solutions be customised based on customer requirements?
Every customer has some unique value proposition for their customer segment. Trezix has flexibility by way of configuration to adhere to industry needs and specific customer needs, keeping in mind the regulatory processes are not deviated to fulfil statutory requirements.
How do you foresee the face of logistics changing for the cement industry?
Digitalisation is one of the biggest waves you can see in the logistics space, which is changing the face of the industry. Digitalisation is changing the logistics landscape. Various concepts like Just In Time (JIT) to customer delivery are now a reality. Vehicle utilisation, fuel efficiency, delivery visibility, vehicle tracking through RFID, Fastag, FOIS (rail receipt tracking), container/cargo tracking across geography is now a reality.
- –Kanika Mathur

Ankit Kumar, Co-Founder and CEO, Skye Air, highlights the advantages of drone deliveries for the cement industry to improve the overall operational efficiency and cost-effectiveness of the supply chain.
What is the environmental impact that drone deliveries can create?
Drone deliveries have the potential to significantly reduce environmental impact compared to conventional delivery methods. By utilising drones, the carbon footprint of last-mile delivery can be slashed by eliminating the need for vehicles and vans, which emit greenhouse gases during transport. In fact, studies have shown that drone deliveries can reduce carbon emissions by up to 80 per cent compared to traditional delivery methods. Additionally, drones provide more direct routes, minimising congestion and further lowering emissions.
Furthermore, Skye Air’s implementation of drone technology can contribute to a substantial decrease in air pollution. Traditional delivery vehicles, powered by fossil fuels, contribute significantly to air pollution, whereas drones operate on cleaner energy sources, such as electricity. As a result, the adoption of drone technology by Skye Air could lead to a notable reduction in harmful pollutants released into the atmosphere.
It’s worth noting that Skye Air is committed to continuous monitoring and optimisation of its operations to ensure that the environmental benefits of drone delivery are maximised. Through data-driven analysis and innovative strategies, Skye Air aims to further enhance the efficiency and sustainability of its drone delivery services.
In conclusion, while drone deliveries offer significant environmental benefits, rigorous management and innovation are essential to mitigate any potential negative effects and ensure the long-term viability of drone delivery operations.
Tell us about the efficiency created by drone delivery systems.
Skye Air has spearheaded a paradigm shift in the logistics industry by substantially augmenting efficiency in their drone deliveries. Drones can help circumvent traditional road networks, bypass traffic congestion and surmount logistical impediments, facilitating expeditious and direct transportation of goods. This heightened efficiency is particularly conspicuous in exigent circumstances, such as the delivery of medical supplies to remote regions or the expeditious fulfillment of urgent orders. By harnessing the capabilities of drones, Skye Air optimises delivery routes, curtails fuel consumption, and mitigates the overall operational costs inherent in conventional delivery methodologies.
Indeed, empirical data underscores the efficacy of drone deliveries, showcasing a significant reduction in delivery times by up to 50 per cent compared to traditional methods. Moreover, drone deliveries have been shown to minimise fuel usage by approximately 60 per cent, contributing to substantial environmental conservation efforts.
Furthermore, the automation of the delivery process not only expedites operations but also bolsters efficiency, resulting in enhanced customer satisfaction rates. With streamlined processes and expedited turnaround times, Skye Air sets a new standard for excellence in the logistics domain.
What is the role of digitalisation and technology in your delivery and transport system?
In Skye Air, digitalisation and technology serve as pivotal catalysts in revolutionising our delivery and transport system. Through the integration of cutting-edge drone technology like Skye UTM, we have established a streamlined and efficient delivery process. Our drones are equipped with state-of-the-art navigation systems and sensors, enabling precise and secure delivery routes. Skye UTM stands as the most advanced and indigenised Aerial Traffic Management platform, designed to furnish situational awareness, autonomous navigation, risk assessment, and traffic management to all drone and aerial mobility operators across the airspace. Skye UTM has already facilitated successful BVLOS (Beyond Visual Line of Sight) drone flights. The Skye UTM captures over 255+ parameters of UAV movements, storing them in its ‘Black box’, which comprises a published systematic description of the entire flight. This platform offers the inaugural 3-Dimensional view of the drone airspace, alongside operations and regulations mapping servers, furnishing the latest airspace status, verified paths, and exhibiting real-time UAV movements. Furthermore, our digital platforms empower customers to seamlessly place orders and track their deliveries in real-time. This digitalisation not only amplifies the velocity and precision of our deliveries but also ensures transparency and accountability throughout the entire process.
Can drone deliveries be incorporated with the cement industry in the future?
In the foreseeable future, the incorporation of drone deliveries holds promise for integration within the cement industry, presenting efficient and swift transportation solutions for materials. The sophisticated drone technology prevalent in logistics stands poised to collaborate seamlessly with cement companies, optimising their supply chain operations. Drones can ferry small batches of cement or other construction materials to remote or challenging-to-access locations, thereby diminishing reliance on conventional transportation modes such as trucks and mitigating logistical complexities. Through the strategic utilisation of drones, the cement industry stands to bolster its efficiency, curtail costs and elevate overall operational efficacy.
- –Kanika Mathur

Cementing a Greener Future

Digital Evolution

Streamlining supply chains will become paramount

We intend to use C&D waste as a raw material

Digitalising the value chain could be a game changer
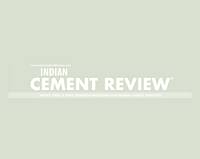
Environment Ministry revises rules of solid waste management

M-sand boards new terrain

Concrete: A Highly Sustainable Building Material
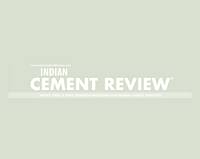
Process and quality optimization in cement plant.

Adani Group eyes Jaiprakash Associates’ Shahabad cement plant
Trending News
-
Concrete3 weeks ago
JK Cement Boosts Production Capacity with New Production Line at Panna Plant
-
Economy & Market1 month ago
RAHSTA will drive road construction innovation: Sundaresan
-
Concrete3 weeks ago
Ultratech sources VRM from Gebr. Pfeiffer
-
Economy & Market4 weeks ago
RAHSTA to showcase cutting-edge road construction tech, says NCC Director