Environment
A Case for Energy-Efficient Motors
Published
8 years agoon
By
admin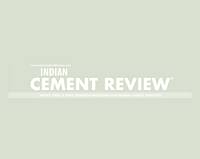
In most continuous running plants, the installed base of motors is already over a decade old, say ANIL NAIK and AJAY BHALERAO.
Electric motors are estimated to consume around 65 per cent of the electrical energy consumed by the industry. Moreover, energy costs over the typical life-cycle of a motor can be as high as twenty times the original capital cost of the motor. Energy-efficient motors thus offer an opportunity to significantly reduce energy costs and their collateral environmental effects.
Increasingly, there is a strong economic – and environmental – case for choosing high-efficiency motors over conventional ones. Instead of repairing or rewinding a failed motor, organisations may profitably consider replacing them with energy-efficient motors or motor driven systems; this can bring about significant reduction in energy consumption.
Over the past two decades, motor-efficiency measurement standards have undergone extensive changes. At the same time, technological advances and greater end-user awareness have resulted in higher availability and application of energy-efficient motors, particularly IE2, IE3 and now even IE4.
However in most continuous running plants, the installed base of motors is already over 10 years old, inefficient, oversized and operating on fluctuating load between 40-80 per cent without a Variable Frequency Drive. Rewound motors also cause a 10 to 15 per cent loss of power.
Motors in the Cement Industry
The cement industry uses a large number of electric motors, right from MW ratings in 11/6.6/3.3 kV to much smaller ratings in 415 V supply. Since energy costs form a significant component of the production costs in a cement plant, plant managers and plant designers are constantly looking for energy savings solutions. Since large power ratings already have high efficiencies, the emphasis is on smaller rating motors, where the improvement in efficiency is much higher. The increased efficiency can result in very short payback periods.
Some of the manufacturing stages (or areas) where these smaller rating motors are used in the cement plants are:
Almost all new cement plants now specify IE2 or IE3 motors. Existing plants can also greatly benefit from the replacement of existing old motors with new IE3 or even superior efficiency class motors.
The Indian government has mandated that with effect from October 2017, all induction motors manufactured and sold in the country must have minimum IE2 (high-efficiency) levels. This will ensure that no low-efficiency motor is sold in India. However, for those industries where motors run for significant amount of time selection of efficiencies even higher than IE2, IE3 (premium efficiency) or IE4 (super-premium efficiency) motors can make strong economic sense.
With power tariff rates increasing at a Compounded Annual Growth Rate (CAGR) of over 5 per cent, IE4 motors can have a payback period of less than a year. Considering a motor life of 15 years, the lifetime saving in energy costs for a typical 15 kW motor – for an incremental investment of Rs 50,000 – can be as high as Rs 11.7 lakh.
Performance of higher efficiency class motors
Operating speed and slip
In general, motors with higher efficiencies have a higher operating speed, i.e., a reduced slip compared to motors of lower efficiency. Usually the slip is reduced by some 20 to 30 per cent for the next higher-efficiency class for motors of the same rated output power.
Most of the difficulties observed in not obtaining the expected power savings during field trial, testing and at customers plants when they replace standard motors with high efficiency motors are due to the effect of increase in speed of high efficiency motors.
Operational Problems
Several customers have faced the problem of input power increasing when the customer has replaced existing standard motors with IE2/IE3/IE4 motors. The reason for the increase in power consumption is explained below.
Applications where load-torque is increasing with speed (pumps, fans and compressors)As a general rule, high-efficiency cage-induction motors, with more active material, have a lower slip (see table-1), i.e a higher speed of rotation, than motors of lower efficiency. On the average, higher efficiency class motors run 5 to 20 rpm faster than standard motors.
When the torque of the application is a function of the square of the speed (centrifugal loads), like in pumps, fans, compressors, etc., the increase in speed will lead to an increase in output power (torque) which could in some circumstances defeat the benefits from the improved energy efficiency.
Even a minor change in the motor’s full-load speed translates into a significant change in the magnitude of the load and energy consumption. The "fan" or "parabolic law" shows that the kilowatt loading on a motor varies as the third power (cube) of its rotational speed. In contrast, the quantity of air delivered varies linearly with speed.
This is explained in the following example:
Existing standard motor speed = 1440 rpm. New higher-efficiency class motor considered runs at = 1460 rpm.
As per the centrifugal fan or pump affinity rules,
(Where kW2 and kW1 are pump motor loads at RPM2 and RPM1).
A relatively minor 20 rpm increase in a motor’s rotational speed, from 1,440 to 1,460 rpm, results in a 1.39 per cent increase in the load placed upon the motor by the rotating equipment; at the same time, with little increase in delivery, boosting energy consumption by 4.22 per cent, exceeding any efficiency advantages expected from purchase of a higher efficiency class motor. Predicted energy savings will not materialize -in fact, energy consumption will substantially increase.
Therefore, in applications when a motor of lower efficiency is retrofitted by a motor of increased efficiency, the input power may not reduce as much as anticipated when comparing the efficiencies of the two motors.
In some cases the input power of the energy-efficient motor may actually increase compared to the motor of lower efficiency. The user should be aware of the sensitivity of load and energy requirements to rated motor speed while replacing a standard motor with a higher efficiency class motor in a centrifugal pump or fan application.
One method is to use a VFD to reduce the speed to the original value, but this introduces the additional losses of the VFD, which may defeat the purpose of using an energy-efficient motor, unless the customer is already using a VFD for energy savings on the pump.
If a belt and pulley system is being used, one can reduce the pulley diameter and bring down the speed of the pump. If the pump is directly coupled to the motor, the only other alternative is to trim the impellor.
If the motor operates at a higher, an appropriate retrofit arrangement to trim the pump, impellers must be adopted to capture the full energy-conservation benefits. As a thumb rule, one could reduce the diameter (trim) of the impeller inversely to the increase in the speed, e.g., if the speed increases by 3 per cent, then reduce the diameter of the impellor by 3 per cent. This is valid for a trim of maximum 5 per cent. Instructions on how to calculate the amount of trimming are available on many Internet sites. A simple search will give a lot of information. The pump manufacturer can be contacted for guidelines.
Due to the increase in rated speed of high-efficiency motors, it is possible that the input power does not come down as expected in pumps and fans after replacing the motor. This is because the pump is delivering more output. Using the affinity laws, one can estimate the power savings by reducing the input power in cube ratio of the speed increase and confirm that there are savings. However, to actually save that power, it is necessary to trim the impeller to get the true savings, while continuing to get the same (existing) output from the pump. This is clearly mentioned in the CIGRE report.
It should be also noted that in spite of the increased speed of high efficiency motors sometimes we have measured energy savings even in pumps and fans. This can be attributed to the possibility that the efficiency of the existing motor with the customer is actually very low. As per the affinity laws of pumps the power input will always increase in cube of the speed increase.
Starting performance
Energy efficient cage-induction motors are typically built with more active material, i.e., longer core length and/or higher core diameter in order to achieve higher efficiencies. For these reasons, the starting performance of energy-efficient motors differs somewhat from motors with a lower efficiency. On an average, the locked-rotor motor rotor current increases by 10 to 15 per cent for motors from one efficiency class compared to motors of the next higher efficiency class with the same output power. Individually, this difference depends on the design principle of the motors, and should be checked with the manufacturer when replacing motors in an existing installation.
Power Factor
Some customers give more importance to the total kVAR consumption rather that the kW consumption. In other words, they would prefer a motor with high PF rather than high efficiency, as long as the total kVA comes down.
References:
- IEC 60034-30-1
- CIGRE Draft Report: "GUIDE ON USE OF PREMIUM EFFICIENCY IE3 MOTORS & DETERMINING BENEFITS OF GREEN HOUSE GAS EMISSION REDUCTION.
About the authorsAnil Naik is Chairman, IEEMA’s Rotating Machines Division and Ajay Bhalerao is former Managing Committee Member Electrical Research and Development Association, and Former Member, Standards Committee of BIS – ETD 15 & 22. Both are associated with Bharat Bijlee.
Concrete
India donates 225t of cement for Myanmar earthquake relief
Published
1 month agoon
June 17, 2025By
admin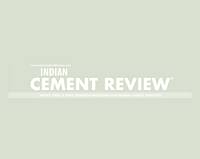
On 23 May 2025, the Indian Navy ship UMS Myitkyina arrived at Thilawa (MITT) port carrying 225 tonnes of cement provided by the Indian government to aid post-earthquake rebuilding efforts in Myanmar. As reported by the Global Light of Myanmar, a formal handover of 4500 50kg cement bags took place that afternoon. The Yangon Region authorities managed the loading of the cement onto trucks for distribution to the earthquake-affected zones.
Concrete
Reclamation of Used Oil for a Greener Future
Published
1 month agoon
June 16, 2025By
admin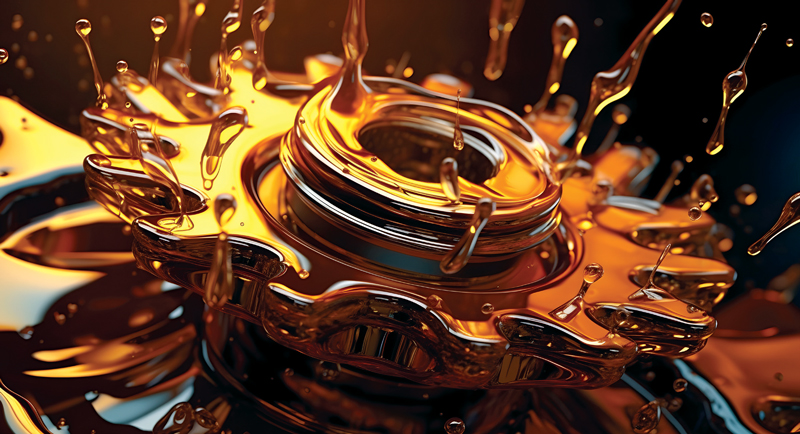
In this insightful article, KB Mathur, Founder and Director, Global Technical Services, explores how reclaiming used lubricants through advanced filtration and on-site testing can drive cost savings, enhance productivity, and support a greener industrial future. Read on to discover how oil regeneration is revolutionising sustainability in cement and core industries.
The core principle of the circular economy is to redefine the life cycle of materials and products. Unlike traditional linear models where waste from industrial production is dumped/discarded into the environment causing immense harm to the environment;the circular model seeks to keep materials literally in continuous circulation. This is achievedthrough processes cycle of reduction, regeneration, validating (testing) and reuse. Product once
validated as fit, this model ensures that products and materials are reintroduced into the production system, minimising waste. The result? Cleaner and greener manufacturing that fosters a more sustainable planet for future generations.
The current landscape of lubricants
Modern lubricants, typically derived from refined hydrocarbons, made from highly refined petroleum base stocks from crude oil. These play a critical role in maintaining the performance of machinery by reducing friction, enabling smooth operation, preventing damage and wear. However, most of these lubricants; derived from finite petroleum resources pose an environmental challenge once used and disposed of. As industries become increasingly conscious of their environmental impact, the paramount importance or focus is shifting towards reducing the carbon footprint and maximising the lifespan of lubricants; not just for environmental reasons but also to optimise operational costs.
During operations, lubricants often lose their efficacy and performance due to contamination and depletion of additives. When these oils reach their rejection limits (as they will now offer poor or bad lubrication) determined through laboratory testing, they are typically discarded contributing to environmental contamination and pollution.
But here lies an opportunity: Used lubricants can be regenerated and recharged, restoring them to their original performance level. This not only mitigates environmental pollution but also supports a circular economy by reducing waste and conserving resources.
Circular economy in lubricants
In the world of industrial machinery, lubricating oils while essential; are often misunderstood in terms of their life cycle. When oils are used in machinery, they don’t simply ‘DIE’. Instead, they become contaminated with moisture (water) and solid contaminants like dust, dirt, and wear debris. These contaminants degrade the oil’s effectiveness but do not render it completely unusable. Used lubricants can be regenerated via advanced filtration processes/systems and recharged with the use of performance enhancing additives hence restoring them. These oils are brought back to ‘As-New’ levels. This new fresher lubricating oil is formulated to carry out its specific job providing heightened lubrication and reliable performance of the assets with a view of improved machine condition. Hence, contributing to not just cost savings but leading to magnified productivity, and diminished environmental stress.
Save oil, save environment
At Global Technical Services (GTS), we specialise in the regeneration of hydraulic oils and gear oils used in plant operations. While we don’t recommend the regeneration of engine oils due to the complexity of contaminants and additives, our process ensures the continued utility of oils in other applications, offering both cost-saving and environmental benefits.
Regeneration process
Our regeneration plant employs state-of-the-art advanced contamination removal systems including fine and depth filters designed to remove dirt, wear particles, sludge, varnish, and water. Once contaminants are removed, the oil undergoes comprehensive testing to assess its physico-chemical properties and contamination levels. The test results indicate the status of the regenerated oil as compared to the fresh oil.
Depending upon the status the oil is further supplemented with high performance additives to bring it back to the desired specifications, under the guidance of an experienced lubrication technologist.
Contamination Removal ? Testing ? Additive Addition
(to be determined after testing in oil test laboratory)
The steps involved in this process are as follows:
1. Contamination removal: Using advanced filtration techniques to remove contaminants.
2. Testing: Assessing the oil’s properties to determine if it meets the required performance standards.
3. Additive addition: Based on testing results, performance-enhancing additives are added to restore the oil’s original characteristics.
On-site oil testing laboratories
The used oil from the machine passes through 5th generation fine filtration to be reclaimed as ‘New Oil’ and fit to use as per stringent industry standards.
To effectively implement circular economy principles in oil reclamation from used oil, establishing an on-site oil testing laboratory is crucial at any large plants or sites. Scientific testing methods ensure that regenerated oil meets the specifications required for optimal machine performance, making it suitable for reuse as ‘New Oil’ (within specified tolerances). Hence, it can be reused safely by reintroducing it in the machines.
The key parameters to be tested for regenerated hydraulic, gear and transmission oils (except Engine oils) include both physical and chemical characteristics of the lubricant:
- Kinematic Viscosity
- Flash Point
- Total Acid Number
- Moisture / Water Content
- Oil Cleanliness
- Elemental Analysis (Particulates, Additives and Contaminants)
- Insoluble
The presence of an on-site laboratory is essential for making quick decisions; ensuring that test reports are available within 36 to 48 hours and this prevents potential mechanical issues/ failures from arising due to poor lubrication. This symbiotic and cyclic process helps not only reduce waste and conserve oil, but also contributes in achieving cost savings and playing a big role in green economy.
Conclusion
The future of industrial operations depends on sustainability, and reclaiming used lubricating oils plays a critical role in this transformation. Through 5th Generation Filtration processes, lubricants can be regenerated and restored to their original levels, contributing to both environmental preservation and economic efficiency.
What would happen if we didn’t recycle our lubricants? Let’s review the quadruple impacts as mentioned below:
1. Oil Conservation and Environmental Impact: Used lubricating oils after usage are normally burnt or sold to a vendor which can be misused leading to pollution. Regenerating oils rather than discarding prevents unnecessary waste and reduces the environmental footprint of the industry. It helps save invaluable resources, aligning with the principles of sustainability and the circular economy. All lubricating oils (except engine oils) can be regenerated and brought to the level of ‘As New Oils’.
2. Cost Reduction Impact: By extending the life of lubricants, industries can significantly cut down on operating costs associated with frequent oil changes, leading to considerable savings over time. Lubricating oils are expensive and saving of lubricants by the process of regeneration will overall be a game changer and highly economical to the core industries.
3. Timely Decisions Impact: Having an oil testing laboratory at site is of prime importance for getting test reports within 36 to 48 hours enabling quick decisions in critical matters that may
lead to complete shutdown of the invaluable asset/equipment.
4. Green Economy Impact: Oil Regeneration is a fundamental part of the green economy. Supporting industries in their efforts to reduce waste, conserve resources, and minimise pollution is ‘The Need of Our Times’.
About the author:
KB Mathur, Founder & Director, Global Technical Services, is a seasoned mechanical engineer with 56 years of experience in India’s oil industry and industrial reliability. He pioneered ‘Total Lubrication Management’ and has been serving the mining and cement sectors since 1999.
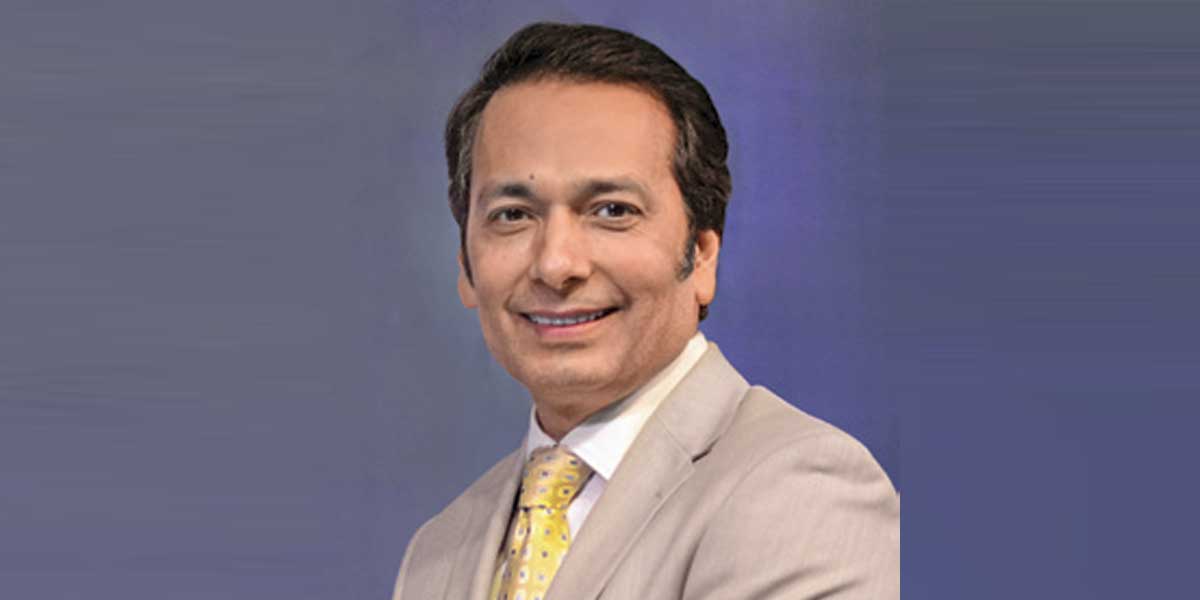
The Indian cement industry has reached a critical juncture in its sustainability journey. In a landmark move, the Ministry of Environment, Forest and Climate Change has, for the first time, announced greenhouse gas (GHG) emission intensity reduction targets for 282 entities, including 186 cement plants, under the Carbon Credit Trading Scheme, 2023. These targets, to be enforced starting FY2025-26, are aligned with India’s overarching ambition of achieving net zero emissions by 2070.
Cement manufacturing is intrinsically carbon-intensive, contributing to around 7 per cent of global GHG emissions, or approximately 3.8 billion tonnes annually. In India, the sector is responsible for 6 per cent of total emissions, underscoring its critical role in national climate mitigation strategies. This regulatory push, though long overdue, marks a significant shift towards accountability and structured decarbonisation.
However, the path to a greener cement sector is fraught with challenges—economic viability, regulatory ambiguity, and technical limitations continue to hinder the widespread adoption of sustainable alternatives. A major gap lies in the lack of a clear, India-specific definition for ‘green cement’, which is essential to establish standards and drive industry-wide transformation.
Despite these hurdles, the industry holds immense potential to emerge as a climate champion. Studies estimate that through targeted decarbonisation strategies—ranging from clinker substitution and alternative fuels to carbon capture and innovative product development—the sector could reduce emissions by 400 to 500 million metric tonnes by 2030.
Collaborations between key stakeholders and industry-wide awareness initiatives (such as Earth Day) are already fostering momentum. The responsibility now lies with producers, regulators and technology providers to fast-track innovation and investment.
The time to act is now. A sustainable cement industry is not only possible—it is imperative.