Technology
Reaching For the Sun
Published
9 years agoon
By
admin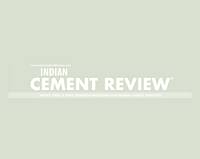
The cement industry can adopt solar energy to reduce greenhouse gas emissions and become cost-competitive, while meeting its statutory obligations, say KAMLESH JOLAPARA, S BHATTACHARYA and S SEN.
Power is a critical component of infrastructure, crucial for the economic growth and welfare of a nation. The existence and development of adequate infrastructure is essential for sustained growth of the Indian economy.
Based on government records as of 30th September 2016, India has a total installed power capacity of 306,358 MW that includes thermal (coal, gas, and diesel), at 213,228 MW; nuclear power at 5,780 MW, hydropower at 43,112 MW, and renewable energy sources account for 44,236 MW.
Ref. Figure 1.
India is heavily dependent on fossil fuels for its energy needs. Most of the power generation is carried out by coal- and gas-based power plants which contribute heavily to greenhouse gas emission.
The Government of India?s immediate goal is to generate two trillion units (kilowatt-hours) of energy by 2019. This means doubling the current generation capacity to provide 24×7 electricity for residential, industrial, commercial and agriculture use.
A transition from conventional energy systems to those based on renewable resources is necessary to meet the ever-increasing demand for energy and to address environmental concerns in a sustainable way.
India ranks 3rd, just behind the US and China, among 40 countries with renewable energy focus, on the back of the strong thrust by the Centre on promoting renewable energy and implementation of projects in a time-bound manner.
In January 2016, the foundation stone for the International Solar Alliance (ISA) was laid in Gurugram, Haryana. The ISA has more than 120 member-countries, most of which are ideally located for solar power generation, wholly or partially between the Tropic of Cancer and the Tropic of Capricon. This emphasises the Government of India?s vision and policy thrust for future solar power generation.
The government has decided to substantially alter the energy mix that powers India in the future, such that at least 40 per cent of India?s total power capacity will come from renewable sources by 2030. This is as per the country?s targets under the Paris climate change agreement.
In order to achieve the country?s ambitious renewable energy targets of adding 175 GW of renewable energy, the Government of India is taking a number of steps and initiatives like the 10-year tax exemption for solar energy projects, and is planning to add 100 GW of solar power by the year 2022. The cumulative solar installations in India have crossed the 8.643 gigawatt (GW) mark in October 2016, according to Mercom Capital Group.
We will explore how the cement industry can integrate the renewable energy sources, especially solar energy, to reduce GHG emissions and to become cost competitive while meeting the obligations under RPO and PAT mechanisms.
Cement Industry in India
India ranks 2nd in the world in the production of cement with a total installed capacity of 378 mtpa in FY 2015.
Cement industry in India can be divided into the five geographical zones of India -North, South, East, West and Central based on localized variations in the consumer profile and supply-demand scenario.
According to Indian Minerals Year Book by Indian Bureau of Mines, TechSci Research, the South zone is largest market, with the highest installed capacity of 132.7 mtpa (FY15 Estimates) and followed by North, West, Central and East zones with installed capacity – 85.6 mtpa, 57.6 mtpa, 52.8 mtpa and 49.4 mtpa respectively. Ref. Figure 2 Currently, India has 210 large cement plants across states and is among the top ten exporters both by value and volume, says Cement Manufacturer?s Association (CMA) and TechSci Research Andhra Pradesh is the leading state with 40 large cement plants, followed by Tamil Nadu and Rajasthan having 21 and 20 plants, respectively. Major cement clusters include – Satna (Madhya Pradesh), Gulbarga (Karnataka), Yerranguntla (Andhra Pradesh), Nalgonda (Andhra Pradesh) and Chandoria (Rajasthan).
Cement demand in India is expected to increase due to government?s push for large infrastructure projects, leading to 45 million tonnes of cement needed in the next three to four years.
India Brand Equity Foundation (IBEF) predicts that India?s cement demand is expected to reach 550-600 Million Tonnes Per Annum (MTPA) by 2025.
Energy Consumption in Cement Industry
Few Industries in India have been identified as energy-intensive industries. These are Aluminum, cement, fertilizer, iron and steel, glass, and paper. Together they account for 17 per cent of manufacturing value of output (VO) and for 39 per cent of all fuels consumed in the manufacturing sector.
Cement industry is one of the most energy intensive industries, and energy costs account for a significant percentage (approximately 30-40 per cent) of the total manufacturing cost.
The annual energy consumption by cement industry contributes close to 10 per cent of the total energy consumed in entire industrial sector.
According to the Cement Manufacturers? Association, modern cement plants consume 68-93 units to produce a ton of cement while the older ones use up 110-120 units of electrical energy.
The cement industry has nearly 4,000 MW of installed captive power capacity, including coal-based plants, diesel generating sets and wind turbines to overcome rising power costs and uncertainty over supply.
Presently, the industry average for Captive Thermal Power generation cost varies between Rs. 3.50 to 4.50 / kWh and most plants are operating at around 30 per cent efficiency.
The major problem of the cement industry are related to ?power availability? that includes drastic cut in the electricity, shortage of coal, inadequate availability of wagons for transport, limited availability of furnace oil.
Some cement producers like Madras Cements, have put up captive power plants to take care of all their electricity requirements, while for others, such as ACC Ltd, captive power meets 72 per cent of its requirement.
The carbon footprint is nearly 1.3 kg/kWh for Captive Thermal Power plants in India. The overall CO2 emission is 866 kg/ ton clinker produced. The CO2 emission is around 670 kg/ ton of cement (PPC).
Sustainability in Cement Industry
Climate change and energy security are global challenges and cement industry recognizes the need to contribute its equitable effort as a function of its techno-economic and socio-economic development.
The cement industry recognizes the significant threat caused by climate change and focuses to develop its own renewable energy assets. This supports the vision to complement the existing power resourcing strategy with green power, efficient energy use planning and investment for better returns with sustainable energy growth. India has joined hands with Switzerland to reduce energy consumption and develop newer methods in the Country for more efficient cement production, which would help India, meet its rising demand for cement in the infrastructure sector.
An enormous energy saving is possible in cement sector by implementing the renewable energy sources especially Waste heat recovery and solar energy plants that reduce operating cost and improve the environment.
Potential Renewable Energy Projects in Cement Plant
The Indian cement industry has realized that strong business growth can be achieved by sustaining manufacturing in an eco-friendly manner. Most of the new cement plants are adopting green processes and green power generation to reduce Green-House-Gas (GHG) emissions. Some of the following renewable energy projects can be introduced in the cement plant to achieve clean and green plant.
Power plants based on renewable sources such as wind and solar energy has a great potential to become an integral part of new cement plants.
Waste Heat Recovery System (WHRS)
WHRS has a potential to generate about 20 per cent to 30 per cent of plant power requirements (reducing purchased/captive power needs). It uses hot gases from the clinker cooler or pre-heater to heat a liquid and generate steam, to generate in turn electricity for powering the cement plant. The power generation methods in WHRS work on Steam Rankine cycle, Organic Rankine cycle and Kalina cycle.
According to IFC (World Bank Group) report, the existing WHR installed capacity is more than 200 MW in India and there is potential to achieve remaining 500-900 MW with estimated investment potential of $1.4 billion.
Solar Power Plant
Solar energy has many merits compared to conventional power sources. The solar prices have been falling, and in many parts of India, the cost of solar power is less than the tariff of power for the industrial sector.
Since the solar plants have a lifetime of typically 25 years, the energy prices are locked in, unlike in the case of power from utility companies, which is only expected to increase every year.
By installing solar power plants and solar water heating systems, cement plants can not only meet the obligations under both RPO and PAT mechanisms, but also reduce greenhouse gas (GHG) emissions.
Most cement plants in India are located in dry and hot areas with enormous solar radiation and have huge amounts of unused, un-shaded arid land. This makes cement sector very ideal for deployment of solar power generation plants. Solar energy can be harnessed either by Solar PV or Solar Thermal (CSP-Concentrated Solar Power) Technologies.
Based on the available area within a cement plant, we can install the solar power plant considering the solar technology suitable for that geographical terrain. Some of the potential applications of solar energy in cement plants are listed below:
- Roof top solar PV panels to meet the power requirement of CCR, Admin buildings, remote lighting applications like mines
- Lighting requirements in Non-Plant Buildings, Internal roads, pumping water, guesthouse, township, parks, canteen, hospital, school and many more
- Energy requirement of auxiliary equipment, utilities
- Preheating of boiler feed water or raw materials
- Hot water requirement
- Other possibilities, if any
Wind Power Plant
A wind turbine is a system which transforms the kinetic energy available in the wind into mechanical or electrical energy that can be used for any required application. Some of the advantages of wind power plant are-one time installation cost, low operational and maintenance cost, no fuel cost, environment friendly and pollution free, lowest gestation period, limited use of land.
Wind farm is located in an area of high wind (usually at a distance to manufacturing facility) with power ?wheeled? through national transmission grid. It helps cement manufacturers to take advantage of solar as well as wind energy for their cement plants.About Solar Energy and Typical Parameters
Two major technologies have been developed to harness solar energy ? Photovoltaic Solar Technology and Solar Thermal Technology. PV solar technology directly converts sunlight into electricity using panels made of semiconductor cells while Solar Thermal Technology captures the sun?s heat that converts to mechanical energy and in turn electricity.
Availability of reliable solar radiation data is vital for the success of solar energy installations in different sites of the country (Refer Image -India Solar Resource). The geological locations having annual Direct Normal Irradiance (DNI) of 5.0 kWh/m2/day and above could be more suitable for solar power plant installation in India.
For solar collectors which are flat in nature, solar radiation data in the form of Global Horizontal Irradiance (GHI) is useful while for designing solar thermal power plants (CSP units); Direct Normal Irradiance (DNI) data is required.
Solar PV Technology
Some of the typical parameters need to be considered before implementing the solar PV power plant, such as:
- Installation type – On ground or Rooftop solar plant
- About 90 per cent solar plants are imple?mented with Polycrystalline as it offers higher efficiency at competitive price.
- Single axis tracking provides 15 per cent to 20 per cent higher output in Central & South India.
- Land requirement – Fixed axis requires 5 acres per MW while single axis tracking needs 6 acres of land per MW.
- The Installation cost of 1 MW solar plant is around INR 5 – 5.5 cr based on current cost parameters.
- Solar power generation depends on location, technology and design of the system. Typically for India – generation of 15,00,000 kWh/MW/year for fixed axis and 18,00,000 kWh/MW/year for single axis tracking can be considered.
- Project Execution – Typical cement plant requirement for RPO only: 1 to 5 MWp. The solar power project can be implemented in 3 to 4 months from the date of starting construction.
The cement plants having captive power plants, as well as those who are purchasing power through Indian Energy Exchange (IEX) are liable for Renewable Purchase Obligation (RPO) as stipulated by the respective state governments.
Regarding captive consumer, those generating and consuming power from captive coal/natural gas power plants (primarily industrial users in cement, steel, chemical etc. sectors.). The Regulatory Commission in each state mandates a certain percentage of electricity generated through the above process to be from renewable sources.
According to Ministry of New and Renewable Energy (MNRE), the National Tariff Policy was amended in January 2011 to prescribe solar-specific RPO be increased from a minimum of 0.25 per cent in 2012 to 3 per cent by 2022.
Many States have come up with up their own Solar Policy and they have their own Solar RPO targets.
Case Study – Solar PV Power Plant
Based on the typical brown-field 3000 TPD cement plant, the available rooftop area is around 18,000-19,000 m2 which shall usually cover all the roof top of the plant buildings, top of shed for material storages including the pre-blending stockpile, etc. which potentially harness rooftop solar power of appx. 1.8-1.9 MW (Open space for ground solar PV is not considered).
A typical 10 MWp PV plant example as per IFC report is given below to understand the various parameters of solar power plant.
- Generic cement plant, 2 million tons p.a. facility
- Power needs 25-30 MW, power consumption 198 GWh/year
- Land requirements : 20-30 ha
- Electricity production from Solar: 18-24 GWh/year or 9-12 per cent of total power needs
- Avoided emissions 15,000-20,000 tCO2e p.a.
- SPV CAPEX ~$ 15 m, Unlevered project IRR 13-15 per cent
- Cement company savings ~$1.2 m p.a. (off-balance sheet)
Solar Thermal (CSP) Technology
Solar thermal technology can be used for industrial processes in several ways. It can provide warm water for processes; hot air for drying the raw materials or it can also be used in preheating the boiler feed water either in captive power plant or WHR system.
Several solar thermal power plants have been built in India, using both flat plate collectors and concentrator technologies. It will continue to provide reliable source for grid-connected power.
Solar thermal (CSP) technology can be integrated with existing (steam cycle) based plants (Coal, nuclear, CCGT, biomass) at various stages in the process (feed water heating, direct steam generation) which can save CAPEX on turbine (including auxi?liaries) and augment conversion efficiency.
Installed Solar Power Plants in Cement Sector in India
Several cement manufacturers like Aditya Birla Group, Zuari Cement, Birla Corp and Ambuja Cement, Dalmia Cement etc. have all ventured into solar power generation in India.
Aditya Birla Group was one of the pioneers, having set up a 100 kW solar power plant in its Rajashree cement plant in Karnataka in 2012. Zuari Cement set up a solar power plant in Yerraguntla district in Andhra Pradesh in 2013.
Cement companies such as Emami cement, OCL India, Ultratech cement, Birla Corp at Satna works have installed the solar power plants of 10.06 MW, 5.5 MW, 2.5 MW, and 1.5 MW capacities respectively.
Favorable Solar Energy Regulations in India
The Indian policy for solar power plant greatly favors investors as it gives many benefits over conventional plants & machinery.
An accelerated depreciation of nearly 80 per cent as compared to 15 per cent for normal plant and machinery is considered for solar plants that results in huge tax savings for the cement manufacturers.
Favorable land laws and other subsidy for solar power generation in cement producing states such as Karnataka, AP, Rajasthan, MP and Telengana.
While cement industries in all states can explore solar projects, those in Karnataka, AP and Telengana states, can benefits due to favorable wheeling, banking and CSS charges for open access model.
Conclusion
As demand for power increases in India due to industrial and population growth, fulfilling the energy requirement could be a challenge in years to come. However, achieving the energy goals will become much easier with more emphasis from the Indian government and corporate world on renewable energy sources especially on solar power plants. Cement industry in India can play a major role in this area. There are many favorable factors for installing the solar power plant in cement industry such as reduction in installation cost of solar plant, increasing fuel cost, Indirect effect on PAT as the RE power is out of boundary limit, possibility for selling E-Certificate if the reduction target is fulfilled and finally but not the least, solar power will be profitable business in years to come.
The government also needs to play a major role, in fast development of this sector by providing necessary policy supports, incentives and judicious tariff plan mechanism.
There will be a few initial hurdles that will have to be crossed before the cement sector becomes truly appreciative of the solar technology for power generation.
-
The solar technology providers will have to educate the users regarding the feasibility of their installations.
-
Consultants like ERCOM will have to technically assist the cement plant owners during all stages of the projects right from initial feasibility study till successful implementation, so that the solar installations are successful.
-
Cement plant owners will have to get over their inhibitions and embrace new technology which will enable them to have sustainable growth while reducing their energy costs and protecting the environment for future generation.
Authors:
Kamlesh Jolapara
Suchismita Bhattacharya
S Sen
All from Ercom Engineers
Energy mix that powers India in the future, such that at least 40 per cent of India?s total power capacity will come from renewable sources by 2030
Economy & Market
Hindalco Buys US Speciality Alumina Firm for $125 Million
Published
2 months agoon
June 25, 2025By
admin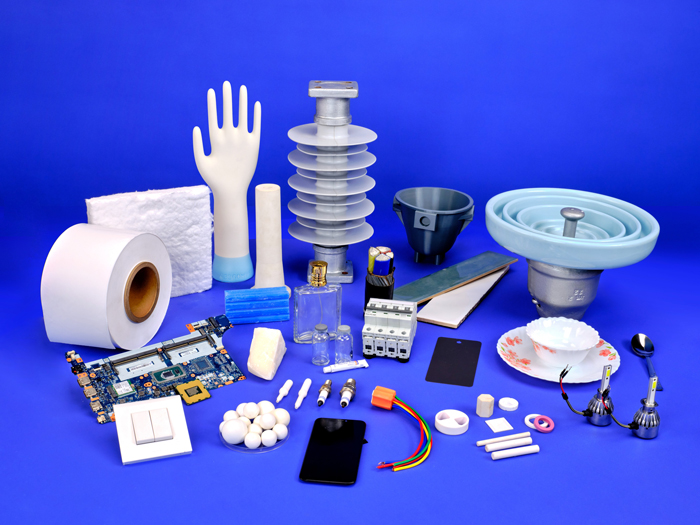
This strategic acquisition marks a significant investment in speciality alumina, a key step by Aditya Birla Group’s metals flagship towards becoming future-ready by scaling its high-value, technology-led materials portfolio.
Hindalco Industries, the world’s largest aluminium company by revenue and the metals flagship of the $28 billion Aditya Birla Group, has announced the acquisition of a 100 per cent equity stake in US-based AluChem Companies—a prominent manufacturer of speciality alumina—for an enterprise value of $125 million. The transaction will be executed through Aditya Holdings, a wholly owned subsidiary.
This acquisition represents a pivotal investment in speciality alumina and advances Hindalco’s strategy to expand its high-value, technology-led materials portfolio.
Hindalco’s speciality alumina business, a key pillar of its value-added strategy, has delivered consistent double-digit growth in recent years. It has emerged as a high-growth, high-margin vertical within the company’s portfolio. As speciality alumina finds expanding applications across electric mobility, semiconductors, and precision ceramics, the deal positions Hindalco further up the innovation curve, enabling next-generation alumina solutions and value-accretive growth.
Kumar Mangalam Birla, Chairman of Aditya Birla Group, called the acquisition an important step in their global strategy to build a leadership position in value-added, high-tech materials.
“Our strategic foray into the speciality alumina space will not only accelerate the development of future-ready, sustainable solutions but also open new pathways to pursue high-impact growth opportunities. By integrating advanced technologies into our value chain, we are reinforcing our commitment to self-reliance, import substitution, and building scale in innovation-led businesses.”
Ronald P Zapletal, Founder, AluChem Companies, said the partnership with Hindalco would provide AluChem the ability and capital to scale up faster and build scale in North America.
“AluChem will benefit from their world-class sustainability and safety standards and practices, access to integrated operations and a consistent, reliable raw material supply chain. Their ability to leverage R&D capabilities and a talented workforce adds tremendous value to our innovation pipeline, helping drive market expansion beyond North America.”
An Eye on the Future
The global speciality alumina market is projected to grow significantly, with rising demand for tailored solutions in sectors such as ceramics, electronics, aerospace, and medical applications. Hindalco currently operates 500,000 tonnes of speciality alumina capacity and aims to scale this up to 1 million tonnes by FY2030.
Commenting on the development, Satish Pai, Managing Director, Hindalco Industries, said the deal reinforced their commitment to innovation and global expansion.
“As alumina gains increasing relevance in critical and clean-tech sectors, AluChem’s advanced chemistry capabilities will significantly enhance our ability to serve these fast-evolving markets. Importantly, it deepens our high-value-added portfolio with differentiated products that drive profitability and strengthen our global competitiveness.”
AluChem adds a strong North American presence to Hindalco’s portfolio, with an annual capacity of 60,000 tonnes across three advanced manufacturing facilities in Ohio and Arkansas. The company is a long-standing supplier of ultra-low soda calcined and tabular alumina, materials prized for their thermal and mechanical stability and widely used in precision engineering and high-performance refractories.
Saurabh Khedekar, CEO of the Alumina Business at Hindalco Industries, said the acquisition unlocked immediate synergies, including market access and portfolio diversification.
“Hindalco plans to work with AluChem’s high performance technology solutions and scale up production of ultra-low soda alumina products to drive a larger global market share.”
The transaction is expected to close in the upcoming quarter, subject to customary closing conditions and regulatory approvals.

As India’s cement industry heads for unprecedented growth, the importance of smart, sustainable and strategic lubrication is gaining ground. From reducing downtime and enhancing energy efficiency to enabling predictive maintenance, lubricants are transforming plant performance. ICR explores how advanced lubrication solutions are becoming critical enablers of reliability, resilience and environmental stewardship in the cement sector.
The Indian cement industry, a cornerstone of the nation’s infrastructure development, is experiencing significant growth. In 2023, India’s cement production reached 374.55 million tonnes, marking a 6.83 per cent year-on-year growth. Projections indicate that the market size will expand from 3.96 billion tonnes in 2023 to 5.99 billion tonnes by 2032, reflecting a compound annual growth rate (CAGR) of 4.7 per cent during 2024-32. This expansion underscores the increasing demand for efficient and sustainable operations within the sector.
In cement manufacturing, equipment such as kilns, crushers, vertical mills, ball mills, conveyors and fans operate under extreme temperatures, heavy loads and high dust exposure. These demanding conditions make proper lubrication not just essential, but mission-critical. Selecting the right type of lubricant and maintaining an effective lubrication regime can drastically improve machine uptime, reduce maintenance costs, and enhance plant safety. In many cases, lubricant-related failures account for a significant proportion of unplanned downtime, underscoring the value of a well-structured lubrication strategy.
The Indian cement sector is also undergoing a technological transformation, with increasing emphasis on automation, predictive maintenance and energy efficiency. In this evolving landscape, lubricants are no longer just consumables—they are enablers of performance, longevity and sustainability. With the growing availability of advanced lubricants and condition-monitoring technologies, Indian cement plants have the opportunity to optimise their lubrication practices in line with global standards. Additionally, tightening environmental regulations and sustainability goals are driving the shift toward eco-friendly lubricants and responsible usage practices, making lubrication management a key factor in both operational and environmental performance.
As the industry moves forward, there is a growing realisation that lubrication excellence can be a competitive differentiator. This article explores the critical role of lubricants in cement manufacturing, the latest technological advancements, the environmental considerations shaping lubricant use, and the challenges and opportunities for cement producers in India aiming to maximise equipment reliability and operational efficiency.
The role of lubricants in cement manufacturing
Cement manufacturing involves heavy-duty machinery operating under extreme conditions—high temperatures, heavy loads and continuous operations. Lubricants are essential in minimising friction, reducing wear and tear, and preventing equipment failures. Proper lubrication ensures that components such as kilns, crushers and grinding mills function optimally, thereby reducing downtime and maintenance costs.
Moreover, the integration of advanced lubrication technologies has enabled predictive maintenance strategies. By monitoring lubricant conditions, operators can anticipate equipment issues before they escalate, allowing for timely interventions and uninterrupted production cycles.
“Lubricants play a crucial role in enhancing the efficiency and reliability of cement plant operations. High-performance lubricants reduce friction and wear in critical machinery such as crushers, kilns, mills, and conveyors, ensuring smoother operation and extending equipment life. By minimising mechanical breakdowns and unplanned downtime, they contribute to consistent production and lower maintenance costs. Additionally, specialised lubricants designed to withstand high temperatures, heavy loads, and dusty environments help maintain optimal performance under demanding conditions. Proper lubrication also improves energy efficiency by reducing power loss due to friction. In essence, the right lubrication strategy not only enhances equipment reliability and operational uptime but also supports overall cost-effectiveness and productivity in cement manufacturing,” says Hiten Ved, Sales Head, Royal Petro Specialities.
In addition to enhancing equipment longevity, lubricants are pivotal in ensuring uninterrupted production cycles. Cement manufacturing is a 24/7 operation, and any unexpected downtime due to mechanical failure can lead to significant financial losses. Lubricants with high thermal stability and oxidation resistance prevent the breakdown of oil films under intense heat, especially in applications like rotary kilns, vertical roller mills and clinker coolers. By reducing the likelihood of equipment seizures or breakdowns, these lubricants act as silent enablers of plant reliability and uptime.
Gaurav Mathur, Director and Chief Executive Officer, Global Technical Services, says, “Wall paintings in tombs show workers using water to move statues, indicating early recognition of lubrication. By 1400 BC, animal fat was used to lubricate chariot axles, ever since then mankind has been relentlessly working to improvise the efficiency of lubricants. Tribological advancements have propelled industrialisation in the world. Machines working in demanding environment need better performance, however merely just better lubricant that is made from highly refined base oils is not good enough. Mineral and synthetic base oils and advanced additives chemistry have given birth to advanced lubricants. These lubricants have better performance characteristics and longer service life.”
“However, the way lubrication is done is more critical and if lubrication is not performed in a proper way, highest performing lubricants would also under perform compared to the lowest specification product. Total Lubrication Management has to be implemented for better machine reliability, equipment availability and lower down time. Implementation of TLM has paid rich dividends in the industry. Pillars of TLM being, contamination free lubrication, regular testing of lubricants to access the lubricant and machine condition and regeneration of lubricants,” he adds.
Lubricants contribute directly to energy efficiency. Friction losses within rotating equipment can account for up to 30 per cent of the total energy consumption in certain plant areas. Advanced synthetic lubricants, with low traction coefficients and superior film strength, reduce this internal resistance, thus improving mechanical efficiency and lowering the plant’s overall energy footprint. As Indian cement plants pursue energy benchmarking and ISO 50001 certifications, the use of high-performance lubricants becomes an integral strategy in achieving energy conservation goals.
“The cement industry has many lubrication points that require NLGI Grade 2 grease that can be used in high temperature applications. These may include bearings on vibrating screens and roller mills; rotating joints on grinding units; and various shafts, pivots, and metal to metal contact points found throughout the plant. CorrLube™ VpCI® Lithium EP Grease has a dropping point of 360 °F (182 °C), allowing it to be used in a broad range of temperatures. For areas that need a slightly harder grease of NLGI Grade 3, EcoLine® Biobased Grease offers a
similar dropping point of 365 °F (185 °C), explain Julie Holmquist, Marketing Content Writer,
Cortec Corporation.
Market dynamics: growth and trends
The Indian industrial lubricants market was valued at $13.05 billion in 2024 and is projected to reach $ 20.72 billion by 2033, growing at a CAGR of 4.12 per cent. This growth is driven by the expanding industrial sector, increased mechanisation, and the adoption of advanced machinery requiring specialised lubricants.
In the cement sector specifically, the demand for high-performance lubricants is rising. The lubricants for cement market are estimated to be $ 2.5 billion in 2024 and is expected to reach $ 3.9 billion by 2033, at a CAGR of 5.3 per cent from 2026 to 2033. This surge is attributed to the need for lubricants that can withstand harsh operating conditions and enhance equipment reliability.
Advancements in lubrication technology
Recent years have witnessed significant advancements in lubrication technology tailored for the cement industry. Synthetic lubricants, known for their superior thermal stability and longer service life, are increasingly being adopted. These lubricants perform effectively under extreme temperatures and heavy loads, common in cement manufacturing processes.
Additionally, the development of bio-based lubricants offers environmentally friendly alternatives without compromising performance. These lubricants, derived from renewable sources, reduce the environmental footprint and align with global sustainability goals. Their biodegradability and low toxicity make them suitable for applications where environmental considerations are paramount.
Smart lubrication systems are another breakthrough in the cement industry. These systems use IoT-enabled sensors and controllers to monitor lubricant condition in real time—tracking parameters such as viscosity, temperature, contamination levels and usage. This data is integrated into plant maintenance software to automate lubricant replenishment and alert operators to potential failures. Predictive lubrication ensures that each component receives the right amount of lubricant at the right time, minimising waste, reducing manual intervention, and extending machinery life.
“Many VpCI® products can be applied to surfaces with minimal pre-cleaning, and the protective VpCI® layer typically does not need to be removed before equipment is put back into service. VpCI® ‘s save significant labor, time, and associated costs compared to methods that require extensive surface preparation (e.g., sandblasting) and post-application cleaning or degreasing. This allows for faster startup after maintenance,” elaborates Ana Juraga, Content Writer, Cortec Corporation.
Furthermore, Original Equipment Manufacturers (OEMs) and lubricant suppliers are collaborating to develop application-specific lubricants tailored to the unique operating conditions of cement manufacturing units. For example, gear oils designed for high-load kilns or open gear systems now come with superior Extreme Pressure (EP) additives and anti-wear properties to cope with shock loading and variable speed operations. These co-developed solutions not only enhance mechanical reliability but also ensure compatibility with diverse materials used in modern cement equipment, ensuring peak performance in both greenfield and brownfield plants.
Sustainability and environmental considerations
The cement industry is under increasing pressure to reduce its environmental impact. Lubricants contribute to this goal by enhancing energy efficiency and reducing emissions. High-quality lubricants decrease friction, leading to lower energy consumption and, consequently, reduced greenhouse gas emissions.
Furthermore, the use of long-life lubricants minimises the frequency of oil changes, thereby reducing waste generation and disposal issues. The shift towards bio-based and recyclable lubricants also supports circular economy principles, promoting resource efficiency and environmental stewardship.
A report by Klüber Lubrication India suggests that sustainability continues to be a key focus for industries, the Securities and Exchange Board of India (SEBI) has mandated Business Responsibility and Sustainability Reporting (BRSR) for the top 1,000 listed companies. This framework requires organisations to disclose their environmental, social and governance (ESG) initiatives, including energy conservation, emission reductions and resource optimisation. Beyond compliance, BRSR reporting allows companies to showcase their sustainability leadership and build investor confidence. Organisations that proactively address sustainability challenges are better positioned to attract long-term investors, secure financing, and maintain a competitive advantage in an evolving regulatory landscape.
The report also states that their high-performance synthetic lubricants play a crucial role in helping cement manufacturers meet these regulatory requirements by enhancing energy efficiency and reducing CO2 emissions in critical machinery such as vertical roller mills (VRMs) and main gearboxes. By adopting our energy-efficient solutions, companies can strengthen their BRSR compliance while achieving tangible operational benefits.
An emerging trend in the lubricant industry is the formulation of biodegradable lubricants specifically tailored for heavy industries like cement manufacturing. These eco-friendly alternatives are made from renewable base stocks and are designed to degrade naturally without leaving behind harmful residues. In environmentally sensitive zones or operations with high spill risk, such as open gear applications or hydraulic systems exposed to the elements, biodegradable lubricants offer a sustainable solution that aligns with stricter environmental regulations and the growing emphasis on corporate social responsibility (CSR) in India’s industrial sector.
KB Mathur, Founder and Director, Global Technical Services, says, “In the world of industrial machinery, lubricating oils while essential; are often misunderstood in terms of their life cycle. When oils are used in machinery, they don’t simply ‘DIE’. Instead, they become contaminated with moisture (water) and solid contaminants like dust, dirt and wear debris. These contaminants degrade the oil’s effectiveness but do not render it completely unusable. Used lubricants can be regenerated via advanced filtration processes/systems and recharged with the use of performance enhancing additives hence restoring them. These oils are brought back to ‘As-New’ levels. This new fresher lubricating oil is formulated to carry out its specific job providing heightened lubrication and reliable performance of the assets with a view of improved machine condition. Hence, contributing to not just cost savings but leading to magnified productivity, and diminished environmental stress.”
Lubricant manufacturers are increasingly focusing on circular economy principles, offering oil analysis, filtration and recycling services that extend lubricant life and minimise waste. Used oil regeneration programs not only reduce disposal costs but also help cement plants meet regulatory norms under the Hazardous Waste Management Rules of India. This closed-loop approach not only lowers the environmental burden but also enhances economic efficiency—making sustainability a dual benefit for operational and ecological performance. As cement companies work towards science-based targets and carbon neutrality, lubricant selection and management play a more strategic role in meeting these broader sustainability commitments.
Challenges and opportunities
Despite the benefits, the adoption of advanced lubricants in the Indian cement industry faces challenges. These include the higher initial costs of synthetic and bio-based lubricants and a lack of awareness about their long-term benefits. Additionally, the integration of lubrication management systems requires investment in training and infrastructure.
However, these challenges present opportunities for innovation and collaboration. Manufacturers
can work closely with lubricant suppliers to develop customised solutions that meet specific operational needs. Moreover, government incentives and regulatory frameworks promoting sustainable practices can accelerate the adoption of advanced lubrication technologies.
Another key challenge is the limited awareness and technical training available at the plant level regarding proper lubrication practices. Many maintenance teams still rely on outdated methods such as manual greasing or fixed-interval lubrication schedules, which often lead to over-lubrication, under-lubrication or lubricant contamination. This results in premature equipment wear and higher operating costs. There is a growing need for skill development programmes and collaboration with lubricant suppliers to train technicians on best practices, condition-based monitoring, and the use of smart lubrication systems.
“Oil in the machine is like blood in the human body. There is no rotating machine that works without lubricants (liquid, semi liquid or solid). Based on the machine component, type of lubricant is used to minimise the mechanical changes in the machine. Lubricant being the product that separates two or more materials under movement. With modern machines being more and more sophisticated and tolerances being finer than before, cleanliness of Lubricants is critical, would the source of contamination be internal wear or external contamination. These contaminations rupture and compromises lubricant film, contamination particles when come in-between the fine tolerances, become cause of catastrophic failure,” expounds Gaurav Mathur.
At the same time, the industry is witnessing an opportunity to leverage digitalisation in lubrication management. Advanced lubrication tracking tools, coupled with ERP and maintenance software, can now offer real-time visibility into lubricant consumption, scheduling and health diagnostics. Integration of AI-powered analytics helps predict equipment failure based on lubricant data, enabling a shift from reactive to predictive maintenance. For Indian cement manufacturers aiming to digitise plant operations as part of Industry 4.0, lubrication is an ideal entry point that delivers immediate ROI and long-term gains in efficiency, asset life and sustainability.
Conclusion
As the Indian cement industry continues its trajectory of growth, the role of high-performance lubricants in ensuring operational reliability, energy efficiency and cost savings cannot be overstated. From kilns and crushers to ball mills and gearboxes, modern lubrication solutions are critical in
reducing downtime and maximising equipment lifespan. With rising demand and increased production pressures, cement plants must adopt a proactive approach to lubrication management—viewing it not as a routine maintenance task, but as a strategic pillar of plant performance.
Recent advancements in lubricant technology, such as synthetic formulations, nano-additives, and smart dispensers, have opened new avenues for boosting equipment efficiency and longevity. Digital tools and IoT-based systems now allow plant operators to monitor lubricant condition in real time, enabling predictive maintenance and minimising the risk of failure. As cement manufacturers increasingly pursue digital transformation and automation under Industry 4.0 frameworks, lubrication systems must be seamlessly integrated into broader asset management strategies.
At the same time, sustainability imperatives are reshaping lubrication choices. There is growing emphasis on biodegradable lubricants, optimised lubricant consumption, and environmentally responsible disposal practices. Overcoming challenges such as limited awareness, inconsistent maintenance practices, and cost sensitivity will require collaboration between lubricant manufacturers, OEMs and cement producers. The opportunities, however, are substantial—by aligning lubrication strategies with efficiency, digitalisation and sustainability goals, the Indian cement industry can significantly enhance its competitiveness and resilience in the years ahead.
– Kanika Mathur
Concrete
We consistently push the boundaries of technology
Published
4 months agoon
April 18, 2025By
admin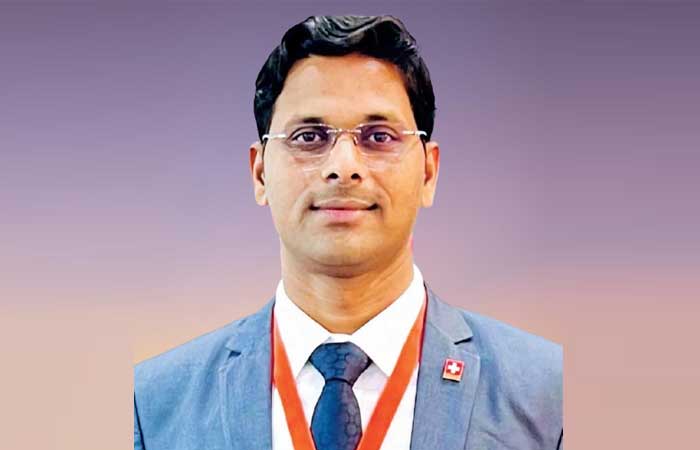
Swapnil Jadhav, Director, SIDSA Environmental, discusses transforming waste into valuable resources through cutting-edge technology and innovative process solutions.
SIDSA Environmental brings decades of experience and expertise to the important niche of waste treatment and process technologies. As a global leader that is at the forefront of sustainable waste management, the company excels in recycling, waste-to-energy solutions and alternative fuel production. In this conversation, Swapnil Jadhav, Director, SIDSA Environmental, shares insights into their advanced shredding technology, its role in RDF production for the cement industry and emerging trends in waste-to-energy solutions.
Can you give us an overview of SIDSA Environmental’s role in waste treatment and process technologies?
SIDSA is a leading innovator in the field of waste treatment and process technologies, dedicated to delivering sustainable solutions that address the growing challenges of waste management.
SIDSA is a more than 52-year-old organisation with worldwide presence and has successfully realised over 1100 projects.
Our expertise is in the engineering and development of cutting-edge systems that enable the conversion of waste materials into valuable resources. This includes recycling technologies, waste-to-energy (W2E) systems, and advanced methods for producing alternative fuels such as refuse derived fuel (RDF). The organisation prioritises environmental stewardship by integrating energy-efficient processes and technologies, supporting industrial sectors—including the cement industry—in reducing their carbon footprint. Through our comprehensive approach, we aim to promote a circular economy where waste is no longer a burden but a resource to be harnessed.
How does SIDSA Environmental’s shredding technology contribute to the cement industry, especially in the production of RDF?
SIDSA’s shredding technology is pivotal in transforming diverse waste streams into high-quality RDF. Cement kilns require fuel with specific calorific values and uniform composition to ensure efficient combustion and operational stability, and this is where our shredding systems excel. In India, we are segment leaders with more than 30 projects including over 50 equipment of varied capacity successfully realised. Some of the solutions were supplied as complete turnkey plants for high capacity AFR processing. Our esteemed client list comprises reputed cement manufacturers and chemical industries. Our technology processes various types of waste—such as plastics, textiles and industrial residues—breaking them down into consistent particles suitable for energy recovery.
Key features include:
- High efficiency: Ensures optimal throughput for large volumes of waste.
- Adaptability: Handles mixed and heterogeneous waste streams, including contaminated or complex materials.
- Reliability: Reduces the likelihood of operational disruptions in RDF production. By standardising RDF properties, our shredding technology enables cement plants to achieve greater energy efficiency while adhering to environmental regulations.
What are the key benefits of using alternative fuels like RDF in cement kilns?
The adoption of RDF and other alternative fuels offers significant advantages across environmental, economic and social dimensions:
- Environmental benefits: Cement kilns using RDF emit fewer greenhouse gases compared to those reliant on fossil fuels like coal or petroleum coke. RDF also helps mitigate the issue of overflowing landfills by diverting waste toward energy recovery.
- Economic savings: Alternative fuels are often more cost-effective than traditional energy sources, allowing cement plants to reduce operational expenses.
- Sustainability and resource efficiency: RDF facilitates the circular economy by repurposing waste materials into energy, conserving finite natural resources.
- Operational flexibility: Cement kilns designed to use RDF can seamlessly switch between different fuel types, enhancing adaptability to market conditions.
What innovations have been introduced in waste-to-energy (W2E) and recycling solutions?
SIDSA’s machinery is meticulously engineered to handle the complex requirements of processing hazardous and bulky waste.
This includes:
- Robust construction: Our equipment is designed to manage heavy loads and challenging waste streams, such as industrial debris, tires and large furniture.
- Advanced safety features: Intelligent sensors and automated controls ensure safe operation when dealing with potentially harmful materials, such as chemical waste.
- Compliance with standards: Machinery is built to adhere to international environmental and safety regulations, guaranteeing reliability under stringent conditions.
- Modular design: Allows for customisation and scalability to meet the unique needs of various waste management facilities.
How does your organisation customised solutions help cement plants improve sustainability and efficiency?
We consistently push the boundaries of technology to enhance waste management outcomes.
General innovations and new product development focus on:
- Energy-efficient shredders: These machines consume less power while maintaining high throughput, contributing to lower operational costs.
- AI-powered sorting systems: Utilise advanced algorithms to automate waste classification, increasing material recovery rates and minimising errors.
- Advanced gasification technologies: Convert waste into syngas (a clean energy source) while minimising emissions and residue.
- Closed-loop recycling solutions: Enable the extraction and repurposing of materials from waste streams, maximising resource use while reducing environmental impact.
What future trends do you foresee in waste management and alternative fuel usage in the cement sector?
Looking ahead, several trends are likely to shape the future of waste management and alternative fuels in the cement industry:
- AI integration: AI-driven technologies will enhance waste sorting and optimise RDF production, enabling greater efficiency.
- Bio-based fuels: Increased use of biofuels derived from organic waste as a renewable and low-carbon energy source.
- Collaborative approaches: Strengthened partnerships between governments, private industries and technology providers will facilitate large-scale implementation of sustainable practices.
- Circular economy expansion: The cement sector will increasingly adopt closed-loop systems, reducing waste and maximising resource reuse.
- Regulatory evolution: More stringent environmental laws and incentives for using alternative fuels will accelerate the transition toward sustainable energy solutions.
(Communication by the management of the company)