Environment
Conveyor Belts Generate Power
Published
9 years agoon
By
admin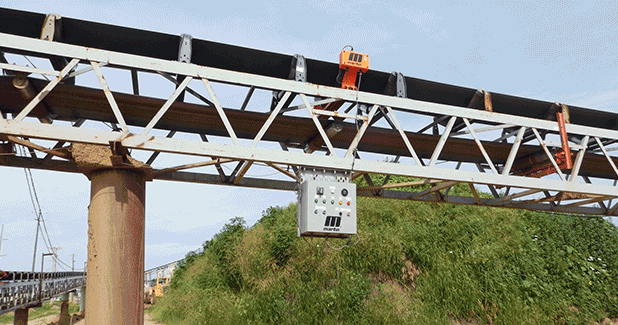
Martin Engineering, a global leader in bulk handling equipment, has introduced an innovative technology that uses the kinetic energy from a moving conveyor belt to generate enough power to run a wide variety of electronic systems.
Martin Engineering designed the Martin? Roll Gen???System to create a self-contained mini-power station that allows operators to run electrical monitoring systems and safety mechanisms. With the ability to be retrofitted on existing idler support structures, operators are not required to maintain a special stock of conveyor rollers, as the generator can be employed on virtually any steel roller. The device is considered a first step toward eliminating power production obstacles, as conveyors move into the next generation of ?smart systems? that are predicted to be more sustainable and autonomous.
Running auxiliary power can be both complicated and costly, requiring expensive labour and oversized cables to accommodate the inevitable voltage drop over long runs, as well as transformers, conduit, junction boxes and other components. Using even a small conventional generator to provide power introduces a different set of issues, including flammable fuels. In many operations, this lack of available power means that any monitoring of the conveyor must be done by technicians physically walking the length of the structure, which can be a difficult and time-consuming task when the systems are long and span difficult terrain.
A more efficient approach is to employ sensors to transmit important data from remote points to a central location where it can be monitored in real time and recorded for later analysis. But intelligent monitoring systems for any conveyor system require power for extended operation. Due to the distances involved, cabled communication systems are not ideal, and therefore wireless communication systems are more advantageous. Options such as solar power are not well suited to the general conditions of a conveyor system, as monitoring devices are often required in an enclosed structure without access to sunlight, or for continuous operation during both day and night.
?We found that we could draw energy from a moving belt by attaching an independent generator directly to one of the rollers,? said Paul Harrison, Global Engineering Manager. ?This way, the conveyor could produce power without altering the structure of the system or affecting its physical configuration.?
Being able to add a generator to a roller delivers the benefit of utilising the proven reliability of existing roller designs, while drawing power from the belt for a wide variety of electronic devices. Product engineers developed a design to accomplish this through the use of a magnetic coupling that attaches to the end of an existing roller. The outside diameter of the generator matches the diameter of the roll, but places the generator outside the material path to avoid the heavy loads and fugitive material that tends to damage existing design attempts. The roll generator is held in a fixed position by the roll support system, but is not normally required to bear any of the material load.
In the new, patent-pending design, a ?drive dog? is attached to the end face of the roll that is resting on the generator, using magnets. The drive dog engages the generator through the outer housing?s machined drive tabs. The magnetic attachment ensures that electrical or mechanical overload does not force the roll to stop; instead, the magnets will slip on the roll face.
The conveyor roll loads are carried by the large support shaft in the generator, which does not rotate and is rigidly mounted to the idler support structure. The generator forms a lightweight driven unit that does not affect the existing roll in any way, except to be rotationally engaged via the magnets, and so draw a small amount of mechanical power in order to generate the electrical energy. The generator is sealed from fugitive material and forms an integral unit independent of the conveyor roll. The bearings of the generator are able to handle the conveyor belt load, as they are of similar size to the roller.
On conveyors that already employ Martin?Trac-Mount Idlers???.. outside of a loading zone, installation is as easy as removing the wing slide on one end and replacing it with the Roll Generator slide, a 2-minute procedure. The TMI design is particularly well-suited to tight spaces, with just 8 inches (203 mm) of clearance needed for 6-inch (152 mm) rolls. While standard rollers can be difficult to replace without ample clearance, the slide-in/slide-out roller frames allow quick service, without the need to raise the belt or remove adjacent idlers.
?The generator can also be installed on its own mount or on other existing support structures, such as a belt tracker,? added Harrison. ?All components to ?condition? the power to a steady 24VDC are enclosed in a protective cabinet, typically mounted directly on the idler support slide.?
The reliable power supply helps bring a new level of sophistication to conveyors, allowing designers to equip their systems with devices such as weigh scales, proximity switches, moisture sensors, pressure switches, solenoids and relays, as well as timers, lights and even additional safety mechanisms. Wireless communication can be used to transmit directly to a central controller, giving operators a cost-effective way to access data that has not been readily available in the past ? and taking another step toward ?smarter? conveyor systems.
?The capability to store power in a small battery bank is already in development,? Harrison added. ?This will allow the generator to produce 5-10x higher amperage for short periods to power higher-wattage devices.?
Martin Engineering is an industry leader in developing and manufacturing flow aids and conveyor products around the world for a wide variety of bulk material applications, including coal, cement/clinker, rock/aggregate, biomass, grain, pharmaceuticals, food and other materials.
For More Information
Martin Engineering, toll-free: (800) 544-2947
Email: info@martin-eng.com
You may like
-
Martin Engineering launches Martin® X-Stand
-
Martin Engineering opens new unit in Kazakhstan
-
Martin engineering issues conveyor fires causes and prevention
-
Martin Engineering launches nextgen tracking technology
-
Martin Engineering disputing ‘Guarding by Location’ in cement industry
-
Consistent flow of materials is a critical aspect
Concrete
India donates 225t of cement for Myanmar earthquake relief
Published
2 months agoon
June 17, 2025By
admin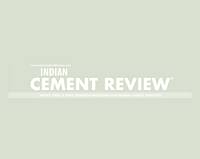
On 23 May 2025, the Indian Navy ship UMS Myitkyina arrived at Thilawa (MITT) port carrying 225 tonnes of cement provided by the Indian government to aid post-earthquake rebuilding efforts in Myanmar. As reported by the Global Light of Myanmar, a formal handover of 4500 50kg cement bags took place that afternoon. The Yangon Region authorities managed the loading of the cement onto trucks for distribution to the earthquake-affected zones.
Concrete
Reclamation of Used Oil for a Greener Future
Published
2 months agoon
June 16, 2025By
admin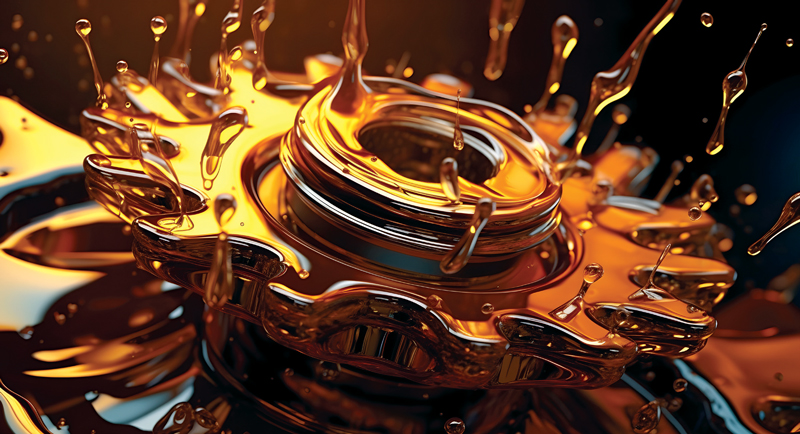
In this insightful article, KB Mathur, Founder and Director, Global Technical Services, explores how reclaiming used lubricants through advanced filtration and on-site testing can drive cost savings, enhance productivity, and support a greener industrial future. Read on to discover how oil regeneration is revolutionising sustainability in cement and core industries.
The core principle of the circular economy is to redefine the life cycle of materials and products. Unlike traditional linear models where waste from industrial production is dumped/discarded into the environment causing immense harm to the environment;the circular model seeks to keep materials literally in continuous circulation. This is achievedthrough processes cycle of reduction, regeneration, validating (testing) and reuse. Product once
validated as fit, this model ensures that products and materials are reintroduced into the production system, minimising waste. The result? Cleaner and greener manufacturing that fosters a more sustainable planet for future generations.
The current landscape of lubricants
Modern lubricants, typically derived from refined hydrocarbons, made from highly refined petroleum base stocks from crude oil. These play a critical role in maintaining the performance of machinery by reducing friction, enabling smooth operation, preventing damage and wear. However, most of these lubricants; derived from finite petroleum resources pose an environmental challenge once used and disposed of. As industries become increasingly conscious of their environmental impact, the paramount importance or focus is shifting towards reducing the carbon footprint and maximising the lifespan of lubricants; not just for environmental reasons but also to optimise operational costs.
During operations, lubricants often lose their efficacy and performance due to contamination and depletion of additives. When these oils reach their rejection limits (as they will now offer poor or bad lubrication) determined through laboratory testing, they are typically discarded contributing to environmental contamination and pollution.
But here lies an opportunity: Used lubricants can be regenerated and recharged, restoring them to their original performance level. This not only mitigates environmental pollution but also supports a circular economy by reducing waste and conserving resources.
Circular economy in lubricants
In the world of industrial machinery, lubricating oils while essential; are often misunderstood in terms of their life cycle. When oils are used in machinery, they don’t simply ‘DIE’. Instead, they become contaminated with moisture (water) and solid contaminants like dust, dirt, and wear debris. These contaminants degrade the oil’s effectiveness but do not render it completely unusable. Used lubricants can be regenerated via advanced filtration processes/systems and recharged with the use of performance enhancing additives hence restoring them. These oils are brought back to ‘As-New’ levels. This new fresher lubricating oil is formulated to carry out its specific job providing heightened lubrication and reliable performance of the assets with a view of improved machine condition. Hence, contributing to not just cost savings but leading to magnified productivity, and diminished environmental stress.
Save oil, save environment
At Global Technical Services (GTS), we specialise in the regeneration of hydraulic oils and gear oils used in plant operations. While we don’t recommend the regeneration of engine oils due to the complexity of contaminants and additives, our process ensures the continued utility of oils in other applications, offering both cost-saving and environmental benefits.
Regeneration process
Our regeneration plant employs state-of-the-art advanced contamination removal systems including fine and depth filters designed to remove dirt, wear particles, sludge, varnish, and water. Once contaminants are removed, the oil undergoes comprehensive testing to assess its physico-chemical properties and contamination levels. The test results indicate the status of the regenerated oil as compared to the fresh oil.
Depending upon the status the oil is further supplemented with high performance additives to bring it back to the desired specifications, under the guidance of an experienced lubrication technologist.
Contamination Removal ? Testing ? Additive Addition
(to be determined after testing in oil test laboratory)
The steps involved in this process are as follows:
1. Contamination removal: Using advanced filtration techniques to remove contaminants.
2. Testing: Assessing the oil’s properties to determine if it meets the required performance standards.
3. Additive addition: Based on testing results, performance-enhancing additives are added to restore the oil’s original characteristics.
On-site oil testing laboratories
The used oil from the machine passes through 5th generation fine filtration to be reclaimed as ‘New Oil’ and fit to use as per stringent industry standards.
To effectively implement circular economy principles in oil reclamation from used oil, establishing an on-site oil testing laboratory is crucial at any large plants or sites. Scientific testing methods ensure that regenerated oil meets the specifications required for optimal machine performance, making it suitable for reuse as ‘New Oil’ (within specified tolerances). Hence, it can be reused safely by reintroducing it in the machines.
The key parameters to be tested for regenerated hydraulic, gear and transmission oils (except Engine oils) include both physical and chemical characteristics of the lubricant:
- Kinematic Viscosity
- Flash Point
- Total Acid Number
- Moisture / Water Content
- Oil Cleanliness
- Elemental Analysis (Particulates, Additives and Contaminants)
- Insoluble
The presence of an on-site laboratory is essential for making quick decisions; ensuring that test reports are available within 36 to 48 hours and this prevents potential mechanical issues/ failures from arising due to poor lubrication. This symbiotic and cyclic process helps not only reduce waste and conserve oil, but also contributes in achieving cost savings and playing a big role in green economy.
Conclusion
The future of industrial operations depends on sustainability, and reclaiming used lubricating oils plays a critical role in this transformation. Through 5th Generation Filtration processes, lubricants can be regenerated and restored to their original levels, contributing to both environmental preservation and economic efficiency.
What would happen if we didn’t recycle our lubricants? Let’s review the quadruple impacts as mentioned below:
1. Oil Conservation and Environmental Impact: Used lubricating oils after usage are normally burnt or sold to a vendor which can be misused leading to pollution. Regenerating oils rather than discarding prevents unnecessary waste and reduces the environmental footprint of the industry. It helps save invaluable resources, aligning with the principles of sustainability and the circular economy. All lubricating oils (except engine oils) can be regenerated and brought to the level of ‘As New Oils’.
2. Cost Reduction Impact: By extending the life of lubricants, industries can significantly cut down on operating costs associated with frequent oil changes, leading to considerable savings over time. Lubricating oils are expensive and saving of lubricants by the process of regeneration will overall be a game changer and highly economical to the core industries.
3. Timely Decisions Impact: Having an oil testing laboratory at site is of prime importance for getting test reports within 36 to 48 hours enabling quick decisions in critical matters that may
lead to complete shutdown of the invaluable asset/equipment.
4. Green Economy Impact: Oil Regeneration is a fundamental part of the green economy. Supporting industries in their efforts to reduce waste, conserve resources, and minimise pollution is ‘The Need of Our Times’.
About the author:
KB Mathur, Founder & Director, Global Technical Services, is a seasoned mechanical engineer with 56 years of experience in India’s oil industry and industrial reliability. He pioneered ‘Total Lubrication Management’ and has been serving the mining and cement sectors since 1999.
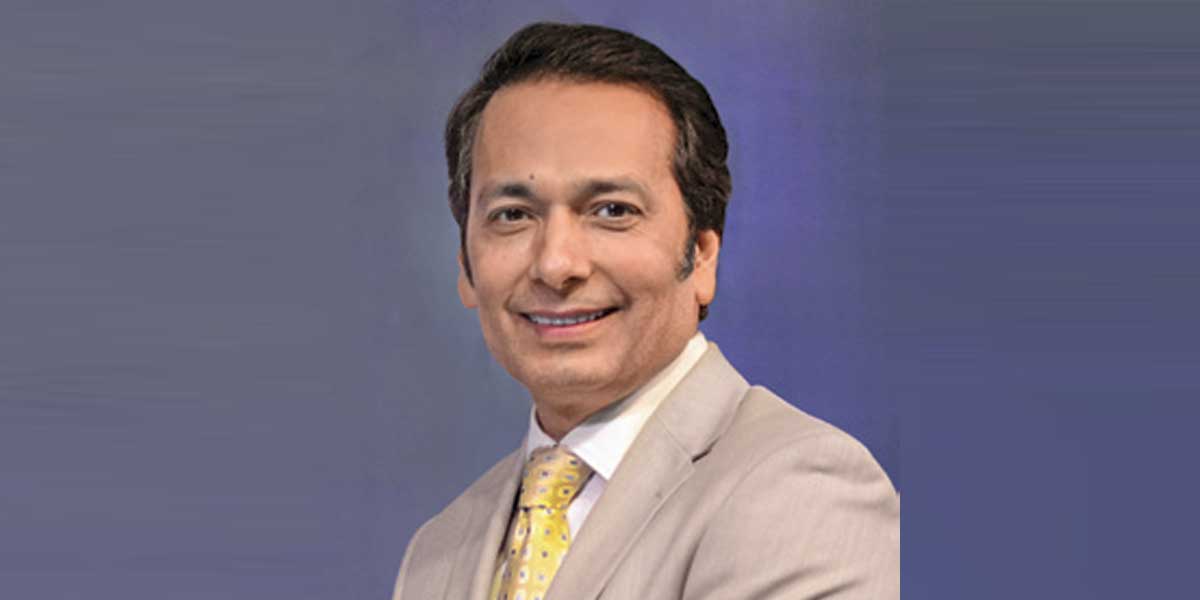
The Indian cement industry has reached a critical juncture in its sustainability journey. In a landmark move, the Ministry of Environment, Forest and Climate Change has, for the first time, announced greenhouse gas (GHG) emission intensity reduction targets for 282 entities, including 186 cement plants, under the Carbon Credit Trading Scheme, 2023. These targets, to be enforced starting FY2025-26, are aligned with India’s overarching ambition of achieving net zero emissions by 2070.
Cement manufacturing is intrinsically carbon-intensive, contributing to around 7 per cent of global GHG emissions, or approximately 3.8 billion tonnes annually. In India, the sector is responsible for 6 per cent of total emissions, underscoring its critical role in national climate mitigation strategies. This regulatory push, though long overdue, marks a significant shift towards accountability and structured decarbonisation.
However, the path to a greener cement sector is fraught with challenges—economic viability, regulatory ambiguity, and technical limitations continue to hinder the widespread adoption of sustainable alternatives. A major gap lies in the lack of a clear, India-specific definition for ‘green cement’, which is essential to establish standards and drive industry-wide transformation.
Despite these hurdles, the industry holds immense potential to emerge as a climate champion. Studies estimate that through targeted decarbonisation strategies—ranging from clinker substitution and alternative fuels to carbon capture and innovative product development—the sector could reduce emissions by 400 to 500 million metric tonnes by 2030.
Collaborations between key stakeholders and industry-wide awareness initiatives (such as Earth Day) are already fostering momentum. The responsibility now lies with producers, regulators and technology providers to fast-track innovation and investment.
The time to act is now. A sustainable cement industry is not only possible—it is imperative.