Product development
Monolithic refractories for cement kiln system
Published
10 years agoon
By
admin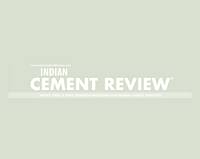
Castable technology is gaining more importance in cement rotary kiln system, feels Deepak Banawalikar of Dalmia Refractories Ltd.
The Indian cement industry – since its de-regularization in 1982 – has attracted huge investments. India from importing cement in 80s now has became the second largest producer of cement in the world, next to China. S
Modern kilns with modern pyro-processing technologies have increased productivity substantially but at the cost of severe abuses on the refractory materials. The higher capacities in turn higher thermal load clubbed with costly downtime has enhanced the criticality of the refractory materials. Chemical abuses due to alternate fuel further aggravated the operational parameters. To address these challenges refractory producers have come up with new refractory products with higher hot properties.
Dalmia Group has played an important duel role in this growth story by raising installed cement capacity to 24 mn t in cement Production while Dalmia Refractory Limited (DRL) executed major turn-key projects with new business strategy. DRL?s presence in shaped alumina refractories for cement industry was always at the top with leading brands of Lofal, Dalsint, Dalkar of 90s were further reinforced with Dalburn, Dalsupreme & DAL-CR range of products with evolving cement technology. If we closely study the usage of monolithic refractory in cement segment, it is gaining importance & being used in critical application areas. DRL has come up with many ranges of monolithic refractories from conventional (dense & insulating), low & ultra-low cement castables, speciality castables like non-wetting to no-cement along with gunning a variety for diversified applications in the cement industry. Dalmia Institute of Scientific & Industrial Research?s (DISIR) contribution in technical support is also commendable. With in-depth study in development & application of these monolithic products an attempt is made to review the monolithic refractories scenario in modern cement plants.
Indian cement scenario & technological challenges
The present per capita cement consumption in India is around 190 kg against world average of 500 kg. Domestic cement consumption is given in fig. 1. It is growing at CAGR of 15.7 per cent and expected to touch 398 mn t by 2017. Thus cement manufacturing capacity, which is presently at 366 mn t is going to touch 421 mn t by 2017. In this capacity enhancement, DRL has played a major share. Table-1 is the cement projects executed by DRL in last few years in India.
With these modern projects it was observed that in cement industry monolithic refractories have made impacts in a wide variety of applications in line with the global trend. Conventionally insulating & dense castables were applied widely in pre-heaters & kiln hood, etc. With the advent of low cement castable application areas got extended to cooler, tip casting, bull-nose areas. Gunning technology further helped in lowering the down time in wide variety of applications including TAD bends, pre-heaters and coolers.
Alternate fuel concept brought in many challenges. Cement industry is one of the largest consumers of the fuel. Fuel cost economy is very crucial. In recent past cement rotary kiln is being considered as incinerators & a wide variety of waste materials including used tyres & other chemicals like waste oil, etc. created differential combustion behaviour abusing refractory substantially. Pet-coke the bye-product of refineries became one of the major alternate fuels. Pet-coke being high sulphur fuel has further disturbed the balance of alkali/sulphur vapour ratio creating build up problems in the smoke chamber, lower cyclones and riser ducts. Thus non-wetting castables have been developed. In recent past no-cement castables are developed with niche properties and are making strong inroads in variety of applications from bull-nose, tip casting and for burners. Thus importance of monolithic refractories in cement industry have enhanced substantially over a period of time.
Clinkerisation process & volatile cycle
Raw meal is the mix of limestone, quartz, clay with corrective lateritic materials. Briefly clinkerisation process can be simplified in following manner:
- The decomposition of limestone into CaO and dehydration of clay leading to release of quartz
- This triggers the reaction sequence of formation of C2S & C12A7 with some amount of C3A
- As temperature rises above 14000 C in the main burning zone liquid concentration rises to around 24-30 per cent
- On cooling C3S & C4AF phases recrystallises out in final clinker with very abrasive nature
The silica & alumina moduli, lime saturation factor (LSF) along with liquid content decide the burnability of the raw meal. This burnability factor has bearing on refractory performance throughout the kiln system. Finally operational parameters, in conjunction with above indices decide the mineral phase assemblage, which define the quality of cement.
The raw meal & fuel brings in very small quantities of salts of sodium, potassium, sulphur & chlorine in the kiln burning environment. Alkali oxides are very low melting materials with 400 & 1,100o C meting points for K2O & Na2O respectively. They tend to form sulphates and chlorides of sodium / potassium. Even these salts are having very low melting points in the range of 800 to 1,070o C. These salts tend to get partially volatalised as they enter the kiln burning zone and rest escapes with clinker. These vapours travel along with flue gases towards kiln inlet areas and condesnses on the raw meal in the colder regions of the up-stream. Now raw meal rich in alkali salts enters the kiln thus setting up the volatalization-condensation cycle.
This volatalisation & subsequent condensation of semi-fused mass of alkali salts on the incoming raw meal or refractory surafce developes stickyness. Incoming raw meal keeps on depositing on alkali coated refractory. This slowely leads to build ups.
The nature of compounds formed in the kiln environment is function of Alkali Sulphur Ratio or ASR.
This phenomenon disturbs the smooth flow of raw meal de-stabilising the kiln system & productivity. This is very common in lower riser ducts, kiln inlets, smoke chambers affecting the production.
Operating conditions of cement kiln system
Nowadays the output of the average kiln is around 4,500 to 5,500 tpd. With technological advent, new projects are coming up with 8,000-10,000 tpd. This enhances thermal loads substantially above 5.5 Gw/m2h. Due to thermo-chemical constraints, monolithic refractories have not made inroads inside the rotary kiln. Attempts are being made for development of Basic Castable for its obvious advantages. Monolithic refractories have presently limited to tip casting area of the rotary kiln. Beyond rotary kiln diversified applications have been developed for monolithic refractories. Thus relevant operating conditions are being discussed herewith.
Prevailing operating conditions of modern cement kiln systems are given in Table 2. From the point of criticality of the operating parameters, refractory can be broadly classified in following categories in isolation OR in combination.
- Thermal shock resistant
- Coating/chemical resistant
- Abrasion resistant
- Application friendly
Thermal shock resistant castable: Areas of cement kiln system observe very high thermal fluctuations are tip casting, grate cooler & burners. This thermal fluctuation is the main cause of developing stresses in the refractory body. The stress intensity is the function of thermal expansion. The low coefficient of thermal expansion & low MOE helps refractories withstand these thermo-mechanical stresses. Andalucite based Low Cement castables are preferred due to intrinsic lower thermal expansion of these materials.
In last few decades the low cement technology with use of lower high alumina cement (HAC) in combination with micro-fines has totally changed the concept. It helped in development of high strength castables. High strength in turn helped in improving thermal shock resistance in combination with spall resistant materials.
The behaviour of these materials is dependent on
- Suitable use of micro-fines
- Effective use of quality de-flocculating agents
With captive manufacture of high alumina cement under controlled conditions at Katni Dalmia Refractories could develop consistent vast range of engineered products. In practice usage of one property cannot be considered in isolation. Thus we need to have a combination of desired properties to make product effective.
Coating repellent castable: Porosity is the inherent part of general refractories but for fuse-cast refractories like AZS. The extent of porosity can be defined while designing the product. As mentioned above, alkali salt vapor carried by flue gases starts condensing on cooler parts of the refractories. Alkali vapours first infiltrate into these pores and react with alumino-silicate refractories forming expansive low melting feldspathic compounds. Infiltration of these materials first densifies & then initiates cracks due to heavy expansion on cooling thus making refractory failure eminent. This phenomenon is known as alkali bursting. At the kiln outlet also atmosphere are normally alkaline due to liquid in the clinker.
Thus new class of refractory has been developed to prevent the deposition & infiltration of the alkali salts. The coating repellent refractories are modified on surface of silicon carbide making it non-wetting.
SiC (s) + 3/2 O2 (g) ? SiO2 (s) + CO (g)
SiO2 (s) + Na2CO3 (l) ) ?
Na2SiO3 (glass) + CO2 (g)
SiO2 (s) Na2SO4 (l) + 2C + 3/2 O2
(g) ? Na2SiO3 (glass) + SO2 (g) + 2CO2 (g)
SiC is converted to vitreous silicate glass on the surface making smooth surface minimising any adherence of semi-fused sticky mass. Thus build up can definitely be minimised. Same property has been used to develop the alkali resistance also in other parts of the kiln system.
DRL has come up with range of SiC-based castables under the name of Dalresicoat class of castables with varying range of SiC with the severity of alkali attack. The quality of SiC is very crucial for this development. The microstructure of the SiC used for this is attached in Fig. 2. Microstructure clubbed with purity defines the quality. This class of refractories performed successfully in host of the cement plants applications. The non-wetting characteristic of clearly seen in compatibility test carried out with alkali test as shown in fig 3 a & b.
Considering alkali attack by environment special quality burner castable was developed having combination of alkali resistance with thermal shock resistance. This product Dalresicoat-B (BP) has performed excellently in Central Indian plant. Fig: 4 shows the very good condition of the burner after four months usage and continued further.
Abrasion resistant castable: The clinker formed in the burning zone is gushing out of the discharge zone. Abrasion is the major mechanical abuse clubbed with thermal cycling and alkali environment. Thus tip casting material also needs very high abrasion resistant with very high thermal shock resistance. Making the product alkali resistant further improves the performance. Conventionally corundum based LC castable or andalucite-based LC castables were used in kiln outlet/tip casting area with satisfactory performance. In modern kilns with environmental conditions, Andalucite & corundum-based LC Castables started showing performance limitations. To overcome these limitations, DRL has now developed Dalresicoat-B (TC), which is specially developed highly abrasion resistant and can withstand both thermal shock as well as an alkali attack. Fig 5 shows the very good condition of tip casting after six months in Central Indian cement kiln with 6,000 tpd capacity.
In new development 90 per cent alumina corundum based no-cement castable is gaining importance both in tip casting and bull nose areas. The advantages with no cement castable are as follows:
- Very extended shelf life as no binder in dry mix
- Setting mechanism is based on condensation reaction forming Si-O-Si bond system
- Moisture is free & can be driven out fast. Dry-out thus not by dehydration
- Si-O-Si bond forming reaction accelerates with dry-out resulting in very high strength
- No calcium aluminate phases in matrix this enhances hot properties
- High sulphur & alkali resistance
- Do not require high shear mixing as in LC castable
- Installation & dry-out can be very fast lowering turn-around time substantially
Dalmia Refractories has developed this no-cement castable under the name Dalultima and is being promoted. This castable is having excellent properties. DRL has applied it in critical use of burner in North East cement plant & running satisfactorily. Expected life is more than eight months.
Take off duct & tertiary aid Ducts are other areas, which demand very high abrasion resistance materials. This is mainly due to dust laden gases. Depending upon the plant specific severity various grades of low cement castables are used in these applications. Commonly 45 per cent Al2O3 LC castables are used. For very severe application, DRL has developed Rapidense-60, which with proven performance. This is specially engineered with high purity, low porosity alumino-silicates with excellent abrasion resistance.
Application-friendly castables: With high capacities, modern Indian kilns is desirable to have scheduled maintenance and shut down. Down-time being a very costly affair it is always better to have application friendly materials which can help in lowering of turn-around time.
Different application techniques and product technologies may be thought over for this purpose. These products can be looked from different perspectives like
1.Installation technology like gunning
2.Product technologyb
In second case products like newly developed no-cement castable can be considered. In this case although application can be made using vibro-casting but as mentioned earlier material characteristics helps in simplified faster application with efficient dry-out. Gunning products are being developed in developed using no-cement technology. Dalmia Refractories range of speciality castables are given in Table 3
Conclusion
In short castable technology is gaining more importance in cement rotary kiln system. Major usage of castable is outside the main rotary kiln except for tip casting & discharge zone. Development of high strength LC Castables paved way for use of castable in many critical areas. The alternate fuel added woes to refractory materials. Development of non-wetting castables followed by gunning materials further increased the castable consumption in the cement industry. If we analyse the monolithic consumption in projects it ranges from 0.6 to 0.8 kg per mn t of clinker and will vary for different OEMs. Also in running plants, monolithic refractory consumption hovers around 0.08 kg per mn t of clinker, which is significant.
References
1)Cement Industry in India -August 2015 by Indian Brand Equity Foundation
2)Swapan Kumar Das & Co. – Indian Ceramic Society-2012 (Bangalore Chapter) (71-78)
3)I. N. Chakraborty – IREFCON-2012 (48-53)
4)Reni von der Heyde & Co. – IREFCON-2014 (152-157)
(SO3/80)
Q (ASR) = –
{(Na2O/62) + (K2O/94)
+ (Cl/71)}
When Q = 1 Alkalis Salts are in balanced condition in environment
When Q > 1 Environment contains Alkali salts with Free SO3
When Q < 1 Environment contains Salts with Free Alkali Oxides
Table 1: Turn-key projects handled by Dalmia Refractories
Year | Project Name | Kiln Capacity (tpd) |
---|---|---|
2012-13 | Heidelberg | 5,000 |
2012-13 | Wonder Cement Line-I | 6,500 |
2013-14 | Siddhi Vinayak Cement | 4,500 |
2013-14 | Dalmia Cement | 4,500 |
2013-14 | JK Cement | 5,000 |
2013-14 | Calcom Cement | 3,500 |
2014-15 | Wonder Cement Line-II | 8,000 |
2015-16 | Emami Cement | 9,000 |
Table 2: Operating Conditions 120oC
Critical Kiln Zone | Gas Temp. oC | Material Temp. oC |
Chemical/Slag Attack |
Thermal Shock |
Abrasion |
---|---|---|---|---|---|
Pre-Heater Stage IV | 570-960 | 710 | Medium to V. High | Low | Low |
Pre-Heater Stage V | 750-1130 | 790 | V. High | Low | Medium |
Pre-Heater Stage VI | 880-1260 | 820 | V. High | Low | Medium |
Calciner | 1250-1400 | 850 | V. High | Low | High |
TAD | 900-1300 | NA | V. Low | Medium | V. High |
Inlet Hood | 1200-1400 | 1020 | V. High | Low | High |
Tip Casting | 2000-2300 | 1400-1550 | Medium to High | V. High | V. High |
Firing Hood | 1350-1550 | NA | Medium | High | High |
Bull Nose | 1250-1400 | 1370-1550 | Medium | Medium | High |
Grate Cooler Hot End | 1100-1300 | 1370-1550 | Low | V. High | High |
Grate Cooler Cold End | 200-450 | 200-450 | Low | High | Medium |
Take Off Duct | 900-1300 | NA | Low | Low | V. High |
You may like
Concrete
Conveyor belts are a vital link in the supply chain
Published
3 months agoon
June 16, 2025By
admin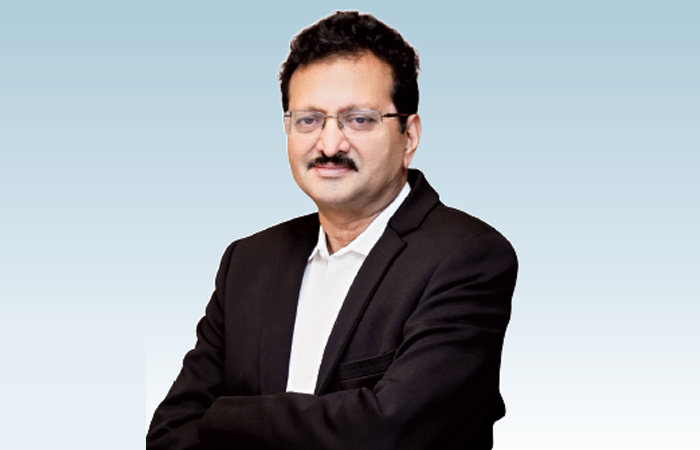
Kamlesh Jain, Managing Director, Elastocon, discusses how the brand delivers high-performance, customised conveyor belt solutions for demanding industries like cement, mining, and logistics, while embracing innovation, automation, and sustainability.
In today’s rapidly evolving industrial landscape, efficient material handling isn’t just a necessity—it’s a competitive advantage. As industries such as mining, cement, steel and logistics push for higher productivity, automation, and sustainability, the humble conveyor belt has taken on a mission-critical role. In this exclusive interview, Kamlesh Jain, Managing Director, Elastocon, discusses how the company is innovating for tougher terrains, smarter systems and a greener tomorrow.
Brief us about your company – in terms of its offerings, manufacturing facilities, and the key end-user industries it serves.
Elastocon, a flagship brand of the Royal Group, is a trusted name in the conveyor belt manufacturing industry. Under the brand name ELASTOCON, the company produces both open-end and endless belts, offering tailor-made solutions to some of the most demanding sectors such as cement, steel, power, mining, fertiliser, and logistics. Every belt is meticulously engineered—from fabric selection to material composition—to ensure optimal performance in tough working conditions. With advanced manufacturing facilities and strict quality protocols, Elastocon continues to deliver high-performance conveyor solutions designed for durability, safety, and efficiency.
How is the group addressing the needs for efficient material handling?
Efficient material handling is the backbone of any industrial operation. At Elastocon, our engineering philosophy revolves around creating belts that deliver consistent performance, long operational life, and minimal maintenance. We focus on key performance parameters such as tensile strength, abrasion resistance, tear strength, and low elongation at working tension. Our belts are designed to offer superior bonding between plies and covers, which directly impacts their life and reliability. We also support clients
with maintenance manuals and technical advice, helping them improve their system’s productivity and reduce downtime.
How critical are conveyor belts in ensuring seamless material handling?
Conveyor belts are a vital link in the supply chain across industries. In sectors like mining, cement, steel, and logistics, they facilitate the efficient movement of materials and help maintain uninterrupted production flows. At Elastocon, we recognise the crucial role of belts in minimising breakdowns and increasing plant uptime. Our belts are built to endure abrasive, high-temperature, or high-load environments. We also advocate proper system maintenance, including correct belt storage, jointing, roller alignment, and idler checks, to ensure smooth and centered belt movement, reducing operational interruptions.
What are the key market and demand drivers for the conveyor belt industry?
The growth of the conveyor belt industry is closely tied to infrastructure development, increased automation, and the push for higher operational efficiency. As industries strive to reduce labor dependency and improve productivity, there is a growing demand for advanced material handling systems. Customers today seek not just reliability, but also cost-effectiveness and technical superiority in the belts they choose. Enhanced product aesthetics and innovation in design are also becoming significant differentiators. These trends are pushing manufacturers to evolve continuously, and Elastocon is leading the way with customer-centric product development.
How does Elastocon address the diverse and evolving requirements of these sectors?
Our strength lies in offering a broad and technically advanced product portfolio that serves various industries. For general-purpose applications, our M24 and DINX/W grade belts offer excellent abrasion resistance, especially for RMHS and cement plants. For high-temperature operations, we provide HR and SHR T2 grade belts, as well as our flagship PYROCON and PYROKING belts, which can withstand extreme heat—up to 250°C continuous and even 400°C peak—thanks to advanced EPM polymers.
We also cater to sectors with specialised needs. For fire-prone environments like underground mining, we offer fire-resistant belts certified to IS 1891 Part V, ISO 340, and MSHA standards. Our OR-grade belts are designed for oil and chemical resistance, making them ideal for fertiliser and chemical industries. In high-moisture applications like food and agriculture, our MR-grade belts ensure optimal performance. This diverse range enables us to meet customer-specific challenges with precision and efficiency.
What core advantages does Elastocon offer that differentiate it from competitors?
Elastocon stands out due to its deep commitment to quality, innovation, and customer satisfaction. Every belt is customised to the client’s requirements, supported by a strong R&D foundation that keeps us aligned with global standards and trends. Our customer support doesn’t end at product delivery—we provide ongoing technical assistance and after-sales service that help clients maximise the value of their investments. Moreover, our focus on compliance and certifications ensures our belts meet stringent national and international safety and performance standards, giving customers added confidence.
How is Elastocon gearing up to meet its customers’ evolving needs?
We are conscious of the shift towards greener and smarter manufacturing practices. Elastocon is embracing sustainability by incorporating eco-friendly materials and energy-efficient manufacturing techniques. In parallel, we are developing belts that seamlessly integrate with automated systems and smart industrial platforms. Our vision is to make our products not just high-performing but also future-ready—aligned with global sustainability goals and compatible with emerging technologies in industrial automation and predictive maintenance.
What trends do you foresee shaping the future of the conveyor belt industry?
The conveyor belt industry is undergoing a significant transformation. As Industry 4.0 principles gain traction, we expect to see widespread adoption of smart belts equipped with sensors for real-time monitoring, diagnostics, and predictive maintenance. The demand for recyclable materials and sustainable designs will continue to grow. Furthermore, industry-specific customisation will increasingly replace standardisation, and belts will be expected to do more than just transport material—they will be integrated into intelligent production systems. Elastocon is already investing in these future-focused areas to stay ahead of the curve.

Advertising or branding is never about driving sales. It’s about creating brand awareness and recall. It’s about conveying the core values of your brand to your consumers. In this context, why is branding important for cement companies? As far as the customers are concerned cement is simply cement. It is precisely for this reason that branding, marketing and advertising of cement becomes crucial. Since the customer is unable to differentiate between the shades of grey, the onus of creating this awareness is carried by the brands. That explains the heavy marketing budgets, celebrity-centric commercials, emotion-invoking taglines and campaigns enunciating the many benefits of their offerings.
Marketing strategies of cement companies have undergone gradual transformation owing to the change in consumer behaviour. While TV commercials are high on humour and emotions to establish a fast connect with the customer, social media campaigns are focussed more on capturing the consumer’s attention in an over-crowded virtual world. Branding for cement companies has become a holistic growth strategy with quantifiable results. This has made brands opt for a mix package of traditional and new-age tools, such as social media. However, the hero of every marketing communication is the message, which encapsulates the unique selling points of the product. That after all is crux of the matter here.
While cement companies are effectively using marketing tools to reach out to the consumers, they need to strengthen the four Cs of the branding process – Consumer, Cost, Communication and Convenience. Putting up the right message, at the right time and at the right place for the right kind of customer demographic is of utmost importance in the long run. It is precisely for this reason that regional players are likely to have an upper hand as they rely on local language and cultural references to drive home the point. But modern marketing and branding domain is exponentially growing and it would be an interesting exercise to tabulate and analyse its impact on branding for cement.
Concrete
Indian cement industry is well known for its energy and natural resource efficiency
Published
3 years agoon
November 18, 2022By
admin
Dr Hitesh Sukhwal, Deputy General Manager – Environment, Udaipur Cement Works Limited (UCWL) takes us through the multifaceted efforts that the company has undertaken to keep emissions in check with the use of alternative sources of energy and carbon capture technology.
Tell us about the policies of your organisation for the betterment of the environment.
Caring for people is one of the core values of our JK Lakshmi Cement Limited. We strongly believe that we all together can make a difference. In all our units, we have taken measures to reduce carbon footprint, emissions and minimise the use of natural resources. Climate change and sustainable development are major global concerns. As a responsible corporate, we are committed with and doing consistent effort small or big to preserve and enrich the environment in and around our area of operations.
As far as environmental policies are concerned, we are committed to comply with all applicable laws, standards and regulations of regulatory bodies pertaining to the environment. We are consistently making efforts to integrate the environmental concerns into the mainstream of the operations. We are giving thrust upon natural resource conservation like limestone, gypsum, water and energy. We are utilising different kinds of alternative fuels and raw materials. Awareness among the employees and local people on environmental concerns is an integral part of our company. We are adopting best environmental practices aligned with sustainable development goals.
Udaipur Cement Works Limited is a subsidiary of the JK Lakshmi Cement Limited. Since its inception, the company is committed towards boosting sustainability through adopting the latest art of technology designs, resource efficient equipment and various in-house innovations. We are giving thrust upon renewable and clean energy sources for our cement manufacturing. Solar Power and Waste Heat Recovery based power are our key ingredients for total power mix.
What impact does cement production have on the environment? Elaborate the major areas affected.
The major environmental concern areas during cement production are air emissions through point and nonpoint sources due to plant operation and emissions from mining operation, from material transport, carbon emissions through process, transit, noise pollution, vibration during mining, natural resource depletion, loss of biodiversity and change in landscape.
India is the second largest cement producer in the world. The Indian cement industry is well known for its energy and natural resource efficiency worldwide. The Indian cement industry is a frontrunner for implementing significant technology measures to ensure a greener future.
The cement industry is an energy intensive and significant contributor to climate change. Cement production contributes greenhouse gases directly and indirectly into the atmosphere through calcination and use of fossil fuels in an energy form. The industry believes in a circular economy by utilising alternative fuels for making cement. Cement companies are focusing on major areas of energy efficiency by adoption of technology measures, clinker substitution by alternative raw material for cement making, alternative fuels and green and clean energy resources. These all efforts are being done towards environment protection and sustainable future.
Nowadays, almost all cement units have a dry manufacturing process for cement production, only a few exceptions where wet manufacturing processes are in operation. In the dry manufacturing process, water is used only for the purpose of machinery cooling, which is recirculated in a closed loop, thus, no polluted water is generated during the dry manufacturing process.
We should also accept the fact that modern life is impossible without cement. However, through state-of-the-art technology and innovations, it is possible to mitigate all kinds of pollution without harm to the environment and human beings.
Tell us about the impact blended cement creates on the environment and emission rate.
Our country started cement production in 1914. However, it was introduced in the year 1904 at a small scale, earlier. Initially, the manufacturing of cement was only for Ordinary Portland Cement (OPC). In the 1980s, the production of blended cement was introduced by replacing fly ash and blast furnace slag. The production of blended cement increased in the growth period and crossed the 50 per cent in the year 2004.
The manufacturing of blended cement results in substantial savings in the thermal and electrical energy consumption as well as saving of natural resources. The overall consumption of raw materials, fossil fuel such as coal, efficient burning and state-of-the-art technology in cement plants have resulted in the gradual reduction of emission of carbon dioxide (CO2). Later, the production of blended cement was increased in manifolds.
If we think about the growth of blended cement in the past few decades, we can understand how much quantity of , (fly ash and slag) consumed and saved natural resources like limestone and fossil fuel, which were anyhow disposed of and harmed the environment. This is the reason it is called green cement. Reduction in the clinker to cement ratio has the second highest emission reduction potential i.e., 37 per cent. The low carbon roadmap for cement industries can be achieved from blended cement. Portland Pozzolana Cement (PPC), Portland Slag Cement (PSC) and Composite Cement are already approved by the National Agency BIS.
As far as kilogram CO2 per ton of cement emission concerns, Portland Slag Cement (PSC) has a larger potential, other than PPC, Composite Cement etc. for carbon emission reduction. BIS approved 60 per cent slag and 35 per cent clinker in composition of PSC. Thus, clinker per centage is quite less in PSC composition compared to other blended cement. The manufacturing of blended cement directly reduces thermal and process emissions, which contribute high in overall emissions from the cement industry, and this cannot be addressed through adoption of energy efficiency measures.
In the coming times, the cement industry must relook for other blended cement options to achieve a low carbon emissions road map. In near future, availability of fly ash and slag in terms of quality and quantity will be reduced due to various government schemes for low carbon initiatives viz. enhance renewable energy sources, waste to energy plants etc.
Further, it is required to increase awareness among consumers, like individual home builders or large infrastructure projects, to adopt greener alternatives viz. PPC and PSC for more sustainable
resource utilisation.
What are the decarbonising efforts taken by your organisation?
India is the world’s second largest cement producer. Rapid growth of big infrastructure, low-cost housing (Pradhan Mantri Awas Yojna), smart cities project and urbanisation will create cement demand in future. Being an energy intensive industry, we are also focusing upon alternative and renewable energy sources for long-term sustainable business growth for cement production.
Presently, our focus is to improve efficiency of zero carbon electricity generation technology such as waste heat recovery power through process optimisation and by adopting technological innovations in WHR power systems. We are also increasing our capacity for WHR based power and solar power in the near future. Right now, we are sourcing about 50 per cent of our power requirement from clean and renewable energy sources i.e., zero carbon electricity generation technology. Usage of alternative fuel during co-processing in the cement manufacturing process is a viable and sustainable option. In our unit, we are utilising alternative raw material and fuel for reducing carbon emissions. We are also looking forward to green logistics for our product transport in nearby areas.
By reducing clinker – cement ratio, increasing production of PPC and PSC cement, utilisation of alternative raw materials like synthetic gypsum/chemical gypsum, Jarosite generated from other process industries, we can reduce carbon emissions from cement manufacturing process. Further, we are looking forward to generating onsite fossil free electricity generation facilities by increasing the capacity of WHR based power and ground mounted solar energy plants.
We can say energy is the prime requirement of the cement industry and renewable energy is one of the major sources, which provides an opportunity to make a clean, safe and infinite source of power which is affordable for the cement industry.
What are the current programmes run by your organisation for re-building the environment and reducing pollution?
We are working in different ways for environmental aspects. As I said, we strongly believe that we all together can make a difference. We focus on every environmental aspect directly / indirectly related to our operation and surroundings.
If we talk about air pollution in operation, every section of the operational unit is well equipped with state-of-the-art technology-based air pollution control equipment (BagHouse and ESP) to mitigate the dust pollution beyond the compliance standard. We use high class standard PTFE glass fibre filter bags in our bag houses. UCWL has installed the DeNOx system (SNCR) for abatement of NOx pollution within norms. The company has installed a 6 MW capacity Waste Heat Recovery based power plant that utilises waste heat of kiln i.e., green and clean energy source. Also, installed a 14.6 MW capacity solar power system in the form of a renewable energy source.
All material transfer points are equipped with a dust extraction system. Material is stored under a covered shed to avoid secondary fugitive dust emission sources. Finished product is stored in silos. Water spraying system are mounted with material handling point. Road vacuum sweeping machine deployed for housekeeping of paved area.
In mining, have deployed wet drill machine for drilling bore holes. Controlled blasting is carried out with optimum charge using Air Decking Technique with wooden spacers and non-electric detonator (NONEL) for control of noise, fly rock, vibration, and dust emission. No secondary blasting is being done. The boulders are broken by hydraulic rock breaker. Moreover, instead of road transport, we installed Overland Belt Conveying system for crushed limestone transport from mine lease area to cement plant. Thus omit an insignificant amount of greenhouse gas emissions due to material transport, which is otherwise emitted from combustion of fossil fuel in the transport system. All point emission sources (stacks) are well equipped with online continuous emission monitoring system (OCEMS) for measuring parameters like PM, SO2 and NOx for 24×7. OCEMS data are interfaced with SPCB and CPCB servers.
The company has done considerable work upon water conservation and certified at 2.76 times water positive. We installed a digital water flow metre for each abstraction point and digital ground water level recorder for measuring ground water level 24×7. All digital metres and level recorders are monitored by an in-house designed IoT based dashboard. Through this live dashboard, we can assess the impact of rainwater harvesting (RWH) and ground water monitoring.
All points of domestic sewage are well connected with Sewage Treatment Plant (STP) and treated water is being utilised in industrial cooling purposes, green belt development and in dust suppression. Effluent Treatment Plant (ETP) installed for mine’s workshop. Treated water is reused in washing activity. The unit maintains Zero Liquid Discharge (ZLD).
Our unit has done extensive plantations of native and pollution tolerant species in industrial premises and mine lease areas. Moreover, we are not confined to our industrial boundary for plantation. We organised seedling distribution camps in our surrounding areas. We involve our stakeholders, too, for our plantation drive. UCWL has also extended its services under Corporate Social Responsibility for betterment of the environment in its surrounding. We conduct awareness programs for employees and stakeholders. We have banned Single Use Plastic (SUP) in our premises. In our industrial township, we have implemented a solid waste management system for our all households, guest house and bachelor hostel. A complete process of segregated waste (dry and wet) door to door collection systems is well established.
Tell us about the efforts taken by your organisation to better the environment in and around the manufacturing unit.
UCWL has invested capital in various environmental management and protection projects like installed DeNOx (SNCR) system, strengthening green belt development in and out of industrial premises, installed high class pollution control equipment, ground-mounted solar power plant etc.
The company has taken up various energy conservation projects like, installed VFD to reduce power consumption, improve efficiency of WHR power generation by installing additional economiser tubes and AI-based process optimisation systems. Further, we are going to increase WHR power generation capacity under our upcoming expansion project. UCWL promotes rainwater harvesting for augmentation of the ground water resource. Various scientifically based WHR structures are installed in plant premises and mine lease areas. About 80 per cent of present water requirement is being fulfilled by harvested rainwater sourced from Mine’s Pit. We are also looking forward towards green transport (CNG/LNG based), which will drastically reduce carbon footprint.
We are proud to say that JK Lakshmi Cement Limited has a strong leadership and vision for developing an eco-conscious and sustainable role model of our cement business. The company was a pioneer among cement industries of India, which had installed the DeNOx (SNCR) system in its cement plant.