Process
Grinding Solutions
Published
11 years agoon
By
admin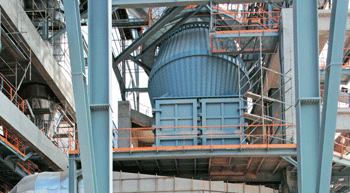
From hub-and-spoke model to split grinding; from single-grinding solution to a combination of system solutions; and from energy-intensive traditional ball mill to upgraded versions and use of pre-grinders, the cement industry is shifting towards more energy-efficient grinding solutions. ICR trains its spotlight on the current technology trends.
The cement industry in India is probably the most efficient in the world and has a well deserved reputation for technology upgradation. The proper selection of plant and machinery, and process systems and auxiliary equipment is not only important from the energy efficiency point of view, but also critical from the plant?s reliability point of view, as well as its ability to run continuously, avoiding stoppages. Most of the major players have taken initiatives to meet the energy efficiency demands. Installation of variable frequency drives; thermal imaging of kiln and pre-heaters to identify major thermal loss areas, carrying of CFD studies on major process equipment are some of the measures. Replacement of inefficient pumps, motors, fans and compressors with highly efficient and operational improvements like arresting of leakages, ?optimisation of mills?, interlocking of auxiliaries to avoid idle runs are some other areas. Most of them are also conducting regular energy saving opportunities.
Energy efficient grinding
Utilising a vertical roller mill or roll press circuit in finish grinding mode for raw material grinding is the industry norm today and this makes for a significant energy cost reduction when compared to traditional closed circuit ball mill system. Likewise for coal grinding, a vertical mill is used and for the energy-intensive finish grinding process, the ball mill plus roll press system is widely popular. Says Dr. Suchismita Bhattacharya, Process, Head, Penta India Cement and Minerals, ?Today the predominant factor in setting up a new plant is sustainability. Owners will want to minimise their operating costs. Hence, equipment which will have lower specific power consumption will be preferred. Along with the mills, separator technology has also seen improvement to maintain the required consistency in cement product particle size distribution.?
DT Arjun, Vice President (Business Development & Projects), WIL, throws light on the current scenario. ?Grinding is a highly energy consuming process and major shift in the industry is towards energy-efficient grinding. With time, the quality norms have become stringent and manufacturers are forced to grind finer to cope up with the market requirement, which in turn, calls for more energy per tonne of product.
Variety of systems/solutions/products have been developed over time which gives a correct balance of quality with energy.? According to him, some of the most-sought solutions in grinding system optimisation are:
Close circuit ball mill system
Ball mill + vertical pre-grinder system
Ball mill + roller press system
Vertical mill system
Grinding process is the most energy consuming part in the cement manufacturing process. Therefore, the focus of Indian cement industry has always been to adopt the most energy-efficient and reliable technology for the grinding process. Says Malay Das, Joint Managing Director, ThyssenKrupp Industries India, ?High Pressure Grinding Roll (HPGR or Polycom) along with the Vertical Roller Mill (VRM) provides the answer with which both the requirements are effectively met. It can, therefore, be observed that the number of HPGR or Polycom installations ws on the rise in the last decade. The factors which have contributed towards this shift, apart from being the energy-efficient technologies, are based on the need for higher throughputs, product quality requirements, raw material quality, and reliability of equipment as well as ease and cost of maintenance.? He adds, ?With regard to the products, the trends are definitely towards composite cement with enhanced utilisation of fly ash, pozollana and granulated blast furnace slag (GBFS).?
KV Anjani Kumar, Senior General Manager (Process & Commissioning), LNV Technology, had this to say. ?In the present scenario, plants are more inclined towards improving the cement quality with effective usage of power. For example, in case of raw meal, reduction of +212 ? fraction without reducing the +90 ? fraction has become the priority. Similarly, increasing the fraction between 3 to 30 ? without increasing the specific power consumption for achieving higher strength has become the norm of the industry.? He adds, ?Adopting the latest technology like fourth generation classifiers, high-efficiency roller mills and high-pressure grinding roll systems will ensure the desired particle distribution with optimum power consumption. The new technology can easily be fitted to get the maximum benefits in the existing systems by a professional cement technology supplier.?
Split grinding
From the traditional ?hub-and-spoke? model, the trend is towards split grinding. Says Kumar, ?As of now, the industry is mostly on the principle of ?hub-and-spoke process?, but the concept of ?split grinding? is slowly finding its way and in next 5-6 years down the line, we should be able to see more of split grinding units in India.
The reasons for opting split grinding units depend on the lesser transport cost, availability of manpower, and market demands. The advantage of split grinding unit is its adoptability for grinding special cements and supply to the customer whenever the need arises, by procuring a suitable raw material.?
Speaking about this shift, Jayanta Saha, Director, Penta India Cement & Minerals, had this to say. ?In the last few years, we have seen the rise of separate grinding units. These require less space and lower investments. Hence, such projects are chosen by new entrants into the cement market who want to start making a presence quickly and with less risk. Grinding units are also put up near power plants where fly ash is available or near steel plants where slag is available. This reduces the cost of transporting raw material which can constitute 35-45 per cent of the PPC or PSC product. We expect that split locations will be on the rise near the consumption location. On the other hand, integrated units will find favour close to the limestone mines.?
According to Das, the concept of split grinding units has been in vogue for quite some time now. ?However,? Das says, ?We cannot say that there is a definitive trend of grinding clinker at a split location or at the hub. In any project, the concept of grinding clinker depends on several factors like markets to be served, transportation costs, availability of raw materials etc, which definitely could lead decision makers to adopt ?split grinding? or ?hub-and-spoke process.?
Arjun shares his views on the logistical aspects of the move towards split grinding. ?Cement industry, like other mineral processing industries, is resource-oriented with limestone being its key ingredient (approximately 85 per cent). This is the main reason for the cement industry being mushroomed around limestone-rich belt and have quite specified presence across India. India being a demographically diverse and price conscious market, always keeps the cement producer on toes. Logistics expense to cater to the diverse market from centralised source adds an extra burden which ultimately gets passed on to the end-user and results in loss in competitiveness. Off late, cement manufacturers have realised this fact and found split location grinding unit as an appropriate answer for the same, wherein they can nullify the logistic cost with proper planning.?
He further adds, ?We see a great potential of split grinding unit in northern and western part of India and have witnessed substantial movement in recent past. As far as industry is concerned, yes, still it is on the principle of hub-and-spoke process, i.e., basically the industry is being conceptualized to cater to the local market, but as the competition is getting fierce, manufacturers have started exploring other markets, wherein split grinding unit comes quite handy.?
?No business is going to come up and nothing is going to start unless there is techno-commercial viability. Currently, there is more encouragement in utilising alternate materials. Since cement requirement is also becoming specific, the grinding requirement with a separate plant becomes a better viability. If you have a slag grinding unit besides a power plant, it is a big advantage, because you get these materials free and you are able to send it back to the market as a finished product. So there is a better viability in this case. But if you talk only OPC point of view, then it is completely different on where you want to set up the unit,? says Debasis Bera, Director – Technical & Operations, BQB Infra Technorium. He adds, ?You can only do split grinding if there is viability, like if you are using slag, and it depends on what kind of cement you are making and the market requirement. If you are making slag cement, you can take the clinker to where the slag is available depending on viability.?
Prashant Gadekar, Deputy General Manager – Account Management, Humboldt Wedag India, says, oMost of the cement companies are setting up small satellite grinding units near their integrated cement plants to use substitute materials or in other words cement additives like flyash, slag and secondly producing the cement near to consumption area to preserve the quality, reduce losses and also to reduce the uncertainty in logistic from long distance. The railway connectivity is the best in terms of transportation compared to road transportation which is not economic as distance increases. That is why people are coming out with more split grinding units/satellite grinding units within radius of 300-400 km of integrated plants.? According to Kumar, there is huge growth potential for split grinding due to closer vicinity to the markets. The growth potential also depends on the availability of suitable land and other logistics like transportation and power etc. In the present scenario, procuring land in the scheduled time period is a huge task. Qualified personnel can also become a key factor at different locations. In case, these two factors are taken care, there is definitely a big scope for split grinding units in India as the demand for the cement is no more a cause for concern.
Ball mills – tech upgrade
?Grinding solution has seen major technological changes with the time. According to Arjun, in ball mill grinding solution, the shift is from open circuit to close circuit resulting in better PSD and ultimately in quality cement. Inception of roller press has opened up an option to the industry to double the grinding capacity of existing mill with inclusion of roller press, with savings in specific energy. Vertical mill came up as solution for voluminous grinding with least energy consumption. Arjun says, ?Each of the above solution is, of course, an efficient grinding solution and can be adopted as upgrade but is capital-intensive. We foresee the uses of pre-grinder and roller presses a novel way to capacity upgrade with attractive payback.?
Says Das, ?Grinding systems with ball mills, though with low maintenance requirements, are high energy consuming systems. Close circuit ball mills with high efficiency separators are being preferred by Indian cement producers, in cases where the capacity requirements are low. Upgradation of ball mill systems is driven mainly by the resulting energy efficiency vis-a-vis the payback periods.?
Saha is on the same page. He says, ?Today there are a variety of pre-grinders that have helped to optimise capacity of ball mills. The cost of new ball mill systems is around one-third of that of the VRMs and roller press systems. However, cost is not the major criterion for selection of new mill system. The major challenge with brownfield projects is the designing of an optimum layout of the new equipment without disturbing the existing system. Project execution without minimum disturbance to existing operation is another challenge for which consultants have to come up with out-of-box solutions.?
Highlighting some of the improvements in the ball mill system, Kumar had this to say. ?Many developments took place for improving the efficiency of ball mills. Much progress has been achieved in terms of liners design which could improve the productivity of ball mills by almost 10 per cent. Similarly, development in diaphragm designs helped in improving the efficiency of ball mills. Continuous improvement in terms of composition of grinding media helped in reducing the wear rate and also increasing the mill performance. Normally, cost is not a major factor in up-grading the ball mill as there will be an improvement, not only in the production capacity of the ball mill but also reduction in over all power consumption and improvement in the product quality. Normally, the payback period is between 12-18 months.? However, he adds, ?More and more manufacturers are opting for high-efficiency vertical roller mills or roller presses because of their lower power consumption and increased reliability, thanks to technological developments.?
According to Bera, developments in optimisation of ball mills are basically related to the grinding process. He explains,?Grinding happens linear with a circulation factor to it. One might use a grinding equipment to grind to a certain level where the particle size is at the desired level. The rejected particles are sent back to the system by a classifier. Using classifier with the normal mill can save energy.?
He adds, ?Another development is the use of roller press with ball mill, which almost doubles the capacity because the mill doesn?t have to do too much of work. The throughput to the mill will increase. Therefore, if you have components such as roller press, you can double the performance of mills. These are the changes that are actually occurred to make the ball mill much smarter. The ball mill is actually very sturdy, and hassle-free but consumes a lot of power. So, the input size to the mill has to be reduced. If you attach a roller press with the mill, you are crushing the material first and then feeding into the ball mill. Here, you are trying to reduce the inefficiency of the mill by feeding in smaller size materials so that the mill has to grind lesser. So a combination of roller press and ball mill becomes easier for grinding and doubling the capacity.? He further adds, ?Cost-effectiveness directly comes from power consumption. When we use smarter equipment or components with the main equipment, it increases the grinding capacity which reduces power consumption considerably.?
Selection parameters
According to Das, the factors considered to decide the grinding concept in integrated cement plants remain unchanged vis-a-vis the split grinding units. The focus continues to remain on employing energy-efficient technologies along with a host of other factors. For split locations, HPGR or Polycom is more apt as water requirement is totally avoided.
Says Arjun, ?The selection parameters of different mills depend on parameters such as type of cement to be produced – OPC/PSC/PPC; market segment to be catered, availability of heat source, and capital expenditure; and ultimately being dictated by the end-user ?needs.? For high-capacity grinding, the return on energy saving is substantially higher, which eventually nullifies the capital investment resulting in shorter payback, whereas for smaller capacity grinding, the payback period for surplus investment is quite high. An investor looks for the break-even point and WIL supports them to make a judicious decision with proper back up.?
Says Dr Bhattacharya, ?While new grinding units may be chosen based on the type of cement product (such as OPC, PPC or PSC), energy efficiency, parameters such as project execution time and ability of the OEM to give good service will also play an important role in the choice of technology. Many a times, the prior experience of decision makers with a certain kind of technology may also be a factor in choosing the system. Reliability of the equipment is an additional factor in choosing the OEM.? She adds, ?Again, the commitment of the owners to remaining in the industry is an important parameter. New players who want to minimise the risk of investment go for the low-cost options, whereas established cement industry majors have an affinity towards the OEMs who have supplied to them in the past.?
?Power consumption and product quality are the main factors for selecting the grinding concept/equipment. In addition to these factors, economic factors like initial investment also play a decisive role in the selection of a particular grinding concept. The other factors include reliability, simple operation and easy installation with minimum shut down period,? says Kumar. He adds, ?Capacity requirement is one of the selection parameters. It is not economical to opt for a VRM or roller press for smaller capacities, whereas these are best suited in case of higher capacities. Other parameters include power consumption, amount of feed moisture, i.e. drying requirement etc.?
On the selection parameters of grinding solutions, Bera had this to say. ?When there are materials difficult to grind, like slag, we would rather prefer a Horomill, than a vertical roller mill, ball mill or anything else. Anything harder to grind means more energy requirement. So it all depends on the type of material to be ground. If the material is softer, we can use cheaper equipment where the power consumption is just for normal grinding of the material on a theoretical basis. On the other hand, grinding harder materials like slag will consume more power, for which we have to choose smarter equipment that saves power in the overall grinding process.?
Gadekar says, ?For higher energy efficiency, everybody is going for roller presses or VRM. Selection depends upon payback period. In today?s context energy-efficient machines are top most priority of the individual. Installation and operating cost are also one of the major selection parameters. Overall, 50 per cent of the preferences are based on the nature of raw material, and the remaining are technology preferences, user-friendliness, capex affordability etc.
Market
According to Arjun, ball mill being the traditional and most reliable and simple grinding solution, rules the market with a share accounting around 70 per cent, followed by VRM and ball mill + roller press (BM+RP). VRM and roller press; of course is an energy-efficient grinding solution but with lots of operational complexities coupled with higher capital expenditure. Roller presses are slowly getting acceptance in the market, whereas VRM acceptance is still a question mark. According to him, energy efficiency is the major contributing factor for the shift of grinding solution from ball mill alone to ball mill and roller press combination. He adds, ?Each system has its own advantage and limitation and a judicial decision is required for the proper selection of grinding system.?
Combinations of systems
Gadekar elaborates, ?Basically, ball mills are being used in clinker grinding but in the last couple of decades, cement companies have started using roller presses with ball mills. Roller presses are majorly contributing to the ball mill technology in the grinding process. Using ball mills with roller presses saves energy, power and have less wear and tear. Also, infrastructure cost/operating cost in roller press circuit is slightly cheaper as compared to VRM. VRM requires hot gas generation system in split grinding whereas roller press operates without hot gases. One of the main advantages of RP is system availability is more compared to VRMs. People prefer VRM also but we have a larger share of roller presses in India compared to VRMs. In ball mills, you have the advantage of putting up roller press is either using ball mill or roller press individually, which is not possible in VRM. In ball mill, you can attach roller press and you have the liberty to use only roller press, if the ball mill is under maintenance or roller press in finish mode if ball mill is under maintenance.?
He further adds, ?We have sold over 84 roller presses in India, out of which majority are in clinker grinding and the rest are in raw and slag grinding (both in finish mode). Currently, ball mills with roller presses are in demand. Existing players are having ball mills and in order to increase the capacity roller presses are being installed which are not possible with VRMs. Whether to choose a ball mill, roller press or VRM, depends on the physical and chemical nature of the clinker, physical properties of the raw materials, moisture content, etc. Clients select these equipment based on specific technology preferences, particle size of the materials, and prevailing norms in that area.?
Highlighting the current market trends and technology upgradation, Bera elaborates. ?The commonly used mills are ball mills and tube mills with the support of roller press or pre-grinder to reduce the size of input materials to the ball mill. But the ball mill utilisation is only 8-10 per cent of the total energy you put into the system and the rest is heat and noise.? He further explains, ?The next level of technology in grinding available is vertical roller mills, which use 12 per cent of the total energy. This is more compact, vertically installed and the power requirement is less.? According to Bera, another technology in grinding introduced almost a decade back is Horomill from FCB France. This has 10-15 per cent extra utilisation of the total energy on the main motor. So this is a more efficient system than ball mills and vertical roller mills today. But the number of installations across the globe is very less. He says, ?In technology, the most efficient is Horomill, than a vertical roller mill, a combination of roller press and mill, and a horizontal mill. This is the line of sequence. Of course, the rest comes with better cyclones for separation, better classifier, etc, so they add on a couple of units here and there in energy saving. Nevertheless, in the grinding and separation technology, we also have a first generation separator, second generation, third generation or fourth generation technology, with which you would have a 30-35 per cent of increase in mill productivity. With this classifier added to it, you can have a 20-30 per cent increase in production very easily. If the collecting efficiency of cyclone is 90 per cent with a 50 per cent pressure drop, then the power gets reduced. Now there are integration of smaller components which add to the power. Auxiliary equipment also needs to be efficient so that in totality, the whole workshop looks smarter.?
Integrated cement plants
Says Arjun, ?In case of integrated cement plant, it does solely depend on the capacity of installation. For instance, a smaller capacity plant, say till 2,000 tpd, the grinding requirement is around 100 tph, which will be economical to produce by installation of ball mill as compared to other available grinding solution, prime reason being initial capital expenditure. For bigger capacity plants, the trend is to go with BM+RP configuration.? He adds, ?WIL has developed a solution wherein we keep the flexibility in system for future integration of roller press/vertical pre-grinder for capacity upgrade and energy savings.?
According to Gadekar, this mainly depends upon the technology preference of client, when in addition to brownfield plant, client prefers/selects the existing/running technology mainly to save inventory cost/ expertises. ?Various factors which affect the selection i.e. installation cost, system reliability etc. It also depends on the nature of material, whether it is hard, soft, moisture content, desired output, and availability of resources like water. Client also compared the technology used by the customers in the nearby areas. It also depends on the system flexibility, i.e, ball mill + roller press has more flexibility than VRMs, as the system can run in commode (RP+BM) as well as finish mode (either BM or RP).
Lead time issues
ICR team tried to find out the impact of extra lead time taken for VRMs. Says Das, ?No doubt that delivery time for vertical roller mills is longer compared to the ball mills, mainly on account of the involvement of overseas noble parts. However, in recent times, the gap has narrowed significantly. For example, if delivery time of a ball mill is around 10-11 months (ex-works basis), the vertical mill can be delivered in around 12-13 months on (ex-works/FOB basis).? He adds, ?However, we at ThyssenKrupp believe that the shortened delivery time for vertical roller mills is possible mainly on account of the optimised sourcing of components backed by our vendor development initiatives.?
Says Arjun, ?Longer delivery time for vertical mill is governed by imports. ?Make in India? is the solution which perfectly address the delivery issue. WIL believes in the same and lives by example of having state-of-the-art manufacturing facilities wherein critical VRM components are manufactured in-house.?
Says Saha, ?Project management with emphasis on prioritising the choice of long lead items is one solution. Sometimes owners start the process of ordering machinery while legal clearances are being obtained from the authorities. As a result, some engineering activities can be completed early. Moreover, many owners also place repeat orders so that the engineering time is crunched. OEMs also have some off-the-shelf offerings with minimum customisation and they can reduce the delivery times if found feasible for the project requirement. The delivery time is now a challenge for OEMs to beat completion and they may have to standardise certain options.?
However, according to Kumar, longer lead time is not an issue. He says, ?It is no more an issue and with the present set-up of SINOMA, we are able to reduce the delivery time of VRM by almost 30 per cent by standardising the hydraulic systems as well as other critical parts like table and roller liners. These critical parts are designed in such a way that the same size parts can be fitted for any model of the mill as they are available in modules. We also manufacture and keep long delivery parts like gear reducer readily available for all the standard mills at any given point of time.?
Advantage roller presses
?Roller press / HPGR in finish grinding mode is a highly energy-efficient grinding solution wherein about 4-5 units savings are envisaged vis-a-vis the vertical roller mills, opines Das. According to him, during the last decade, roller press / HPGR in finish grinding mode has emerged as the most optimum/energy efficient solution for raw material grinding in India, especially when the raw material is ?hard to grind? and ?dry?. He adds, ?ThyssenKrupp has a strong market presence in this segment of raw material grinding ?finish grinding mode?, having successful operating installations at Vasavadatta Cement, Reliance Cementation, Vicat, and JK Cement.?
?Roller press in finished grinding is not a widely accepted and established solution, primarily due to higher water demand (water required to get the cementation property), says Arjun. However, he cautions, ?Roller press alone produces cement in finished mode which calls for exceptionally big mechanical transport and system is always at risk. WIL doesn?t advocate for this solution.?
According to Kumar, the scope of RP for finish grinding is tremendous due to very less specific power consumption and simple operation. The major equipment in a RP circuit are RP itself, de-agglomerator and dynamic separator and fans along with collection equipment like cyclones and bag filters. All these equipment are simple to operate and maintain. He says, ?The main benefits are improved particle size distribution (increased strengths) and lower power consumption as compared to other systems. The reliability of RP is much higher than VRM circuit. Since the operating cost is less, there is an excellent scope for RP in finish grinding.?
?The scope of the roller presses depends on the capacity, client preferences and budget. Certainly compared to ball mills, this is cost-effective equipment, it has less wear and tear, availability is high, easy to maintain, low energy consumption, longer lifetime, etc are major advantages,? says Gadekar.
Says Dr Bhattacharya, ?There is definitely a shift towards VRMs and roller presses. Roller presses are being popularly used in semi-finish and finish grinding mode. VRMs have been accepted for cement grinding and are used in many places for raw material grinding as well. A new entrant in the Indian cement industry is the Horomill which promises lower power consumption without need to add water to maintain the grinding bed. Lower operating cost and consistent product quality is also an important factor for the shift.?
Demand from retrofitting
There is a good market potential for retrofitting the existing old generation ball mill systems with ?close circuiting? solution. A significant shift in trend is seen, with increased number of requirements for converting the existing ball mill systems installing roller press/HPGR in ?semi-finish grinding? mode. This is primarily on account of high output requirements (at optimised energy consumption), driven by the enhanced clinker production from the existing pyro systems, according to Das. Kumar opines, ?Most of the plants before 1990 era, are either mini plants or 1-mtpa plants with ball mills as grinding equipment that consume very high power. With exponential increase in the cost of power generation, it is practically becoming impossible to operate a plant with such a high power consumption and need to be either modified or replaced with new technology for reducing the overall operating costs in terms of power and maintenance. Few of these plants are already started replacing the old systems with new ones and still many to follow; and there is a good demand for advanced grinding systems. With automation, these new systems can produce even much better results.?
?It is possible to upgrade some of the older grinding systems. Replacement of separators with new generation technology or close circuiting of open ball mill circuit is one such possibility. Another option is addition of pre-grinder to existing ball mill circuit. Usually, in such cases, it is essential to carry out a thorough study of the existing system, to check for any bottlenecks and accordingly design the modifications. System engineering plays an important role in ensuring that the augmented circuit capacity is balanced with the flow in the existing circuit so that new bottlenecks are not created. The existing mill itself can be modified by some OEMs to suit to the requirements of augmented capacity,? says Saha.
Arjun sums up, ?Advance grinding systems are slowly making its place in the industry, however the major chunk of the industry is still running with ball mill. We have observed that customer tends to upgrade the system with inclusion of roller press/pre-grinder which is much more economical and easy than going for a new advance technology.?
Ball mills have a market with share accounting around 70 per cent
This is followed by VRM and BM+RP, VRM and roller press
Liners design helped improve the productivity of ball mills by 10 per cent.
Development in diaphragm designs helped improvi
You may like
Process
Price hikes, drop in input costs help cement industry to post positive margins: Care Ratings
Published
4 years agoon
October 21, 2021By
admin
Region-wise,the southern region comprises 35% of the total cement capacity, followed by thenorthern, eastern, western and central region comprising 20%, 18%, 14% and 13%of the capacity, respectively.
The cement industry is expected to post positive margins on decent price hikes over the months, falling raw material prices and marked drop in overall production costs, said an analysis of Care Ratings.
Wholesale and retail prices of cement have increased 11.9% and 12.4%, respectively, in the current financial year. As whole prices have remained elevated in most of the markets in the months of FY20, against the corresponding period of the previous year.
Similarly, electricity and fuel cost have declined 11.9% during 9M FY20 due to drop in crude oil prices. Logistics costs, the biggest cost for cement industry, has also dropped 7.7% (selling and distribution) as the Railways extended the benefit of exemption from busy season surcharge. Moreover, the cost of raw materials, too, declined 5.1% given the price of limestone had fallen 11.3% in the same aforementioned period, the analysis said.
According to Care Ratings, though the overall sales revenue has increased only 1.3%, against 16% growth in the year-ago period, the overall expenditure has declined 3.2% which has benefited the industry largely given the moderation in sales.
Even though FY20 has been subdued in terms of production and demand, the fall in cost of production has still supported the cement industry by clocking in positive margins, the rating agency said.
Cement demand is closely linked to the overall economic growth, particularly the housing and infrastructure sector. The cement sector will be seeing a sharp growth in volumes mainly due to increasing demand from affordable housing and other government infrastructure projects like roads, metros, airports, irrigation.
The government’s newly introduced National Infrastructure Pipeline (NIP), with its target of becoming a $5-trillion economy by 2025, is a detailed road map focused on economic revival through infrastructure development.
The NIP covers a gamut of sectors; rural and urban infrastructure and entails investments of Rs.102 lakh crore to be undertaken by the central government, state governments and the private sector. Of the total projects of the NIP, 42% are under implementation while 19% are under development, 31% are at the conceptual stage and 8% are yet to be classified.
The sectors that will be of focus will be roads, railways, power (renewable and conventional), irrigation and urban infrastructure. These sectors together account for 79% of the proposed investments in six years to 2025. Given the government’s thrust on infrastructure creation, it is likely to benefit the cement industry going forward.
Similarly, the Pradhan Mantri Awaas Yojana, aimed at providing affordable housing, will be a strong driver to lift cement demand. Prices have started correcting Q4 FY20 onwards due to revival in demand of the commodity, the agency said in its analysis.
Industry’s sales revenue has grown at a CAGR of 7.3% during FY15-19 but has grown only 1.3% in the current financial year. Tepid demand throughout the country in the first half of the year has led to the contraction of sales revenue. Fall in the total expenditure of cement firms had aided in improving the operating profit and net profit margins of the industry (OPM was 15.2 during 9M FY19 and NPM was 3.1 during 9M FY19). Interest coverage ratio, too, has improved on an overall basis (ICR was 3.3 during 9M FY19).
According to Cement Manufacturers Association, India accounts for over 8% of the overall global installed capacity. Region-wise, the southern region comprises 35% of the total cement capacity, followed by the northern, eastern, western and central region comprising 20%, 18%, 14% and 13% of the capacity, respectively.
Installed capacity of domestic cement makers has increased at a CAGR of 4.9% during FY16-20. Manufacturers have been able to maintain a capacity utilisation rate above 65% in the past quinquennium. In the current financial year due to the prolonged rains in many parts of the country, the capacity utilisation rate has fallen from 70% during FY19 to 66% currently (YTD).
Source:moneycontrol.com
Process
Wonder Cement shows journey of cement with new campaign
Published
4 years agoon
October 21, 2021By
admin
The campaign also marks Wonder Cement being the first ever cement brand to enter the world of IGTV…
ETBrandEquity
Cement manufacturing company Wonder Cement, has announced the launch of a digital campaign ‘Har Raah Mein Wonder Hai’. The campaign has been designed specifically to run on platforms such as Instagram, Facebook and YouTube.
#HarRaahMeinWonderHai is a one-minute video, designed and conceptualised by its digital media partner Triature Digital Marketing and Technologies Pvt Ltd. The entire journey of the cement brand from leaving the factory, going through various weather conditions and witnessing the beauty of nature and wonders through the way until it reaches the destination i.e., to the consumer is very intriguing and the brand has tried to showcase the same with the film.
Sanjay Joshi, executive director, Wonder Cement, said, "Cement as a product poses a unique marketing challenge. Most consumers will build their homes once and therefore buy cement once in a lifetime. It is critical for a cement company to connect with their consumers emotionally. As a part of our communication strategy, it is our endeavor to reach out to a large audience of this country through digital. Wonder Cement always a pioneer in digital, with the launch of our IGTV campaign #HarRahMeinWonderHai, is the first brand in the cement category to venture into this space. Through this campaign, we have captured the emotional journey of a cement bag through its own perspective and depicted what it takes to lay the foundation of one’s dreams and turn them into reality."
The story begins with a family performing the bhoomi poojan of their new plot. It is the place where they are investing their life-long earnings; and planning to build a dream house for the family and children. The family believes in the tradition of having a ‘perfect shuruaat’ (perfect beginning) for their future dream house. The video later highlights the process of construction and in sequence it is emphasising the value of ‘Perfect Shuruaat’ through the eyes of a cement bag.
Tarun Singh Chauhan, management advisor and brand consultant, Wonder Cement, said, "Our objective with this campaign was to show that the cement produced at the Wonder Cement plant speaks for itself, its quality, trust and most of all perfection. The only way this was possible was to take the perspective of a cement bag and showing its journey of perfection from beginning till the end."
According to the company, the campaign also marks Wonder Cement being the first ever cement brand to enter the world of IGTV. No other brand in this category has created content specific to the platform.
Process
In spite of company’s optimism, demand weakness in cement is seen in the 4% y-o-y drop in sales volume. (Reuters)
Published
4 years agoon
October 21, 2021By
admin
Cost cuts and better realizations save? the ?day ?for ?UltraTech Cement, Updated: 27 Jan 2020, Vatsala Kamat from Live Mint
Lower cost of energy and logistics helped Ebitda per tonne rise by about 29% in Q3
Premiumization of acquired brands, synergistic?operations hold promise for future profit growth Topics
UltraTech Cement
India’s largest cement producer UltraTech Cement Ltd turned out a bittersweet show in the December quarter. A sharp drop in fuel costs and higher realizations helped drive profit growth. But the inherent demand weakness was evident in the sales volumes drop during the quarter.
Better realizations during the December quarter, in spite of the 4% year-on-year volume decline, minimized the pain. Net stand-alone revenue fell by 2.6% to ?9,981.8 crore.
But as pointed out earlier, lower costs on most fronts helped profitability. The chart alongside shows the sharp drop in energy costs led by lower petcoke prices, lower fuel consumption and higher use of green power. Logistics costs, too, fell due to lower railway freight charges and synergies from the acquired assets. These savings helped offset the increase in raw material costs.
The upshot: Q3 Ebitda (earnings before interest, tax, depreciation and amortization) of about ?990 per tonne was 29% higher from a year ago. The jump in profit on a per tonne basis was more or less along expected lines, given the increase in realizations. "Besides, the reduction in net debt by about ?2,000 crore is a key positive," said Binod Modi, analyst at Reliance Securities Ltd.
Graphic by Santosh Sharma/Mint
What also impressed analysts is the nimble-footed integration of the recently merged cement assets of Nathdwara and Century, which was a concern on the Street.
Kunal Shah, analyst (institutional equities) at Yes Securities (India) Ltd, said: "The company has proved its ability of asset integration. Century’s cement assets were ramped up to 79% capacity utilization in December, even as they operated Nathdwara generating an Ebitda of ?1,500 per tonne."
Looks like the demand weakness mirrored in weak sales during the quarter was masked by the deft integration and synergies derived from these acquired assets. This drove UltraTech’s stock up by 2.6% to ?4,643 after the Q3 results were declared on Friday.
Brand transition from Century to UltraTech, which is 55% complete, is likely to touch 80% by September 2020. A report by Jefferies India Pvt. Ltd highlights that the Ebitda per tonne for premium brands is about ?5-10 higher per bag than the average (A cement bag weighs 50kg). Of course, with competition increasing in the arena, it remains to be seen how brand premiumization in the cement industry will pan out. UltraTech Cement scores well among peers here.
However, there are road bumps ahead for the cement sector and for UltraTech. Falling gross domestic product growth, fiscal slippages and lower budgetary allocation to infrastructure sector are making industry houses jittery on growth. Although UltraTech’s management is confident that cement demand is looking up, sustainability and pricing power remains a worry for the near term.