Process
Filter fabrics made from Fibre blends
Published
11 years agoon
By
admin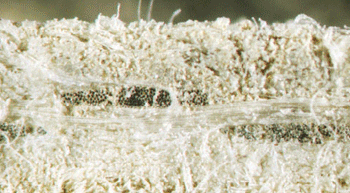
Blends with lobed fibres like P84? constitute a mechanically less sensitive alternative to membrane filter media, writes Dr. Georg Rathwallner.
Fibre blends in dry filter applications are, when properly made, a way to increase filtration efficiency and process stability and reduce the risk of off times. These blends can achieve advantages concerning chemical stability and may offer an economically favorable solution superior to felts made of one blending partner alone. Felt manufacturers provide a wide range of different blended felts and it is not always easy to figure out for what purpose single components are added. Subsequently mentioned examples show some simple but proven ways to utilise fibre blends to gain some understanding of why special blending partners are used. Blending has a rather negative image as often cheaper materials have been used for blending just to offer felts for a lower price than competition. The list of examples is long, e.g., glass blended into polyphenylene sulphide (PPS) or m-aramide, yellow polyester or kermel (polyamidemide) into P84? (polyimide) felts. This kind of blending usually results in reduced felt quality concerning chemical stability and/or filtration efficiency. Premature failures as a result of fibre degradation or blinding and dust penetration are experienced.
This article is not dealing with possibilities to cheat customers by blending but with clearly declared felt compositions that improve quality and ways to find solutions that are economically and technically favourable by blending different fibre materials. After a short theoretical introduction samples for successful applications of fibre blends in different de-dusting applications of the cement industry will be given. When chosen properly, the blend can combine superior filtration behaviour and chemical resistance, and be better than felts made entirely of one sort of fibre. With fibre blends, it has to be noted that chemical and thermal stability are mainly determined by the major blending partner. Addition of smaller amounts of fibres with higher stability does not significantly improve the stability of the blend even an improvement of the filtration behaviour may be achieved. Scrims out of higher resistant material may prolong the bag life by 10-30 per cent and provide mechanical stability in case of beginning deterioration of the batt material. However, the fibre batt still has to provide its structural stability and the entanglement on the scrim.
Theoretical aspects of filtration efficiency for fibre blends
Different fibre cross sections (round, bean or bone-shaped, trilobal and multilobal (Fig.1) and the fibre titres have influence on the pore size and pore size distribution mainly. Furthermore, adhesion between fibres and dust particles play a major role in dust capture. The mechanical adhesion forces between fibres and dust remain mainly unchanged by blending different fibre materials, but another component – the distribution of static charges on the fibre material – varies between different fibre materials and can be influenced by blending of different materials. However, there is no general rule on how to blend fibre materials in order to optimise the distribution of charges on the fibres, and therefore the adhesion of dust due to these forces is available. Ways to increase the filtration efficiency are:
– Implementation of fine fibres:
which increase the fibre surface and decrease pore size. Blends of different fibre titres on the one hand make it possible to use finer fibres than processible on their own and on the other hand, result in derived, narrow pore size distribution.
– Structured fibre cross section: Trilobal and multilobal fibres increase the fibre surface (when the felt weight is kept constant). In addition low velocity areas exist between the lobes of the fibres where dust can be accumulated without an increase of the differential pressure drop. P84 is known for its membrane like filtration efficiency in combination with mechanical robustness. Pure 100 per cent P84 is an alternative to woven glass with PTFE membrane for kiln dedusting. In applications where chemically and thermally less stable fibres are suitable from a chemical point of view, the filtration efficiency of P84 can be utilised by using it as top cap on the dust side or blended into the surface of other base materials.
– Higher felt weight and denser needling: can improve the pressure drop along the bag life due to decreased penetration of particulate into the felt. By a weight increase, additional stability can be obtained for chemical or mechanical challenging applications.
An alternative approach is to increase the filtration efficiency, using a PTFE membrane. On the contrary to needle felts, the membrane is a thin and mechanically susceptible layer. If handling and/or operating conditions do not respect the limits of a membrane, it will be damaged leading to increased emissions and pressure drop, and reduced life.
Kiln/mill filter
In some kiln/mil dedusting systems, PPS is suitable from the chemical and thermal stability point of view (peaks below 200?C and continuous operation at 150?C or lower).
From the filtration efficiency point of view, it is not sufficient for typical design conditions premature failures due to blinding and mechanical damage are often observed far before the expected end of the service if just the chemical stability is considered. Therefore, blends with P84 fine fibres are becoming more common instead of 100 per cent PPS felts and result in a much better performance on a long term.
At higher temperatures, a material with more resistance against oxidation, e.g., P84 which can cover higher peak temperatures, is the economically favourable solution. A P84 felt will pay back the higher price due to the higher bag life in comparison to PPS, especially at continuous temperatures of 130-160?C or if peaks above 200?C (maximum 260?C) have to be considered. Operation at 220-240?C is acceptable when the raw mill is shut down as long as the weighted average of the temperature remains within certain limits. If the average temperature exceeds approximately 180?C, PTFE/P84 blends have an advantage over 100 per cent P84 because oxidation would limit the life of 100 per cent P84.
Finish mills
The typical material for dedusting of finish mills is polyester, besides polyacrylic. The latter has advantages at elevated water contents. The humidity can reach 20 per cent in case the clinker is not stored before grinding. To keep the temperature in the mill in a typical range of 80-90?C, direct cooling with water is used and polyester suffers from hydrolysis under such conditions. Polyacrylic and polyacrylic/polyester composites are suitable at higher humidity.
With the high dust content up to a range of a1 kg/Nm3, the bags often have to be changed after less than one year. Even polyester is not affected chemically at temperatures around 100?C in the air-like environment, bag failures as a result of increased mechanical damage due to blinding can be observed. Due to the accumulation of dust inside the felt, an increasing pressure drop and increased dust emissions through the felt make a change of the bags necessary. The implementation of polyester or acrylic fine fibres does not always bring the desired results.
In a finish mill with low humidity, P84-polyester blends, which consist of a blend of polyester and P84 (fine fibres of both materials are used) in the filtration sided fibre batt, have achieved bag lives of up to five years due to a surface-oriented dust cake build-up (Table 1 and Fig 2). As a result, a low and stable pressure drop was achieved. Therefore, besides the longer bag life, which over-compensates the higher price, fan energy could be saved. Fairly low susceptibility against grinding aids, which considerably effect the filtration behaviour of the cement dust, or peaks in dust content and a/c ratio could be observed. Even more challenging conditions lead to an increased pressure drop but regeneration of the felt after a normalisation of the filtration conditions could be observed.
Clinker cooler
Clinker cooler is not a major challenge chemically, but for most fibre materials concern peak temperatures and abrasive character of the dust. P84 is advantageous due to its temperature and peak temperature stability. m-aramide and polyamide-imide are suitable from the chemical point of view when continuous and peak temperature can be kept on a sufficiently low level. With the latter two materials, the high dust content and peak a/c ratio often lead to dust penetration into the felt and, as a result of increased mechanical burden, leads to bag failures. Blends with P84 can increase the filtration efficiency and reduce the sensibility against upset conditions (in particular, peaks of gas flow and dust load). A similar kind of blends with P84 can be utilised in case cooling is made down to temperatures where polyester and polyacrylic become suitable.
Alkali bypass filter
PTFE is often used besides fibre glass with PTFE membrane. P84/PTFE blends can ensure a lower pressure drop than 100 per cent PTFE felts, even if 100 per cent PTFE felts usually operate to the satisfaction of the end-user with the relatively sticky and easy-to-filter dust.
The 100 per cent P84 is limited to an average operating temperature of approximately 180?C (depending on the life expectation). Blends from PTFE and P84 are suitable to improve filtration efficiency without a restriction of peak temperatures in comparison to PTFE (Fig 3 and 4 and Table 2). Such a blend is suitable for high average temperatures above 180-190?C.
Due to the higher filtration efficiency, mechanical burden is reduced (less differential pressure, longer cleaning cycle times and less abrasion by incorporated dust) and often a higher bag life than with 100 per cent PTFE can be achieved even a chemical less resistant material is used for blending.
Summary
Fibre blends in dry filter applications are, when properly made, a way to increase filtration efficiency and process stability and reduce the risk of off times. Blends with lobed fibres like P84 constitute a mechanically less sensitive alternative to membrane filter media.
Felt manufacturers provide a wide range of different blended felts and it is not always easy to figure out for what purpose single components are added. The above-mentioned examples show some simple but proven ways to utilise fibre blends to get the understanding of why special blending partners are used.
Higher filtration efficiency is required not only to reduce emissions, but also to enable more stable filtration (less penetration of dust into the felt) which can extend the bag life significantly and reduce the energy consumption because of a comparably low and stable pressure drop throughout the life. In many cases, the total costs can be reduced with higher quality filter media.
Even reasonable improvements can be achieved by optimization of the felt material concerning chemical stability and filtration efficiency, conscientiously no miracles are possible. General misfits of filter layout cannot be compensated by the fabric only. To achieve a good performance, a proper cleaning system, air flow and adequate a/c ratios have to be provided.
Operating conditions and felt condition of a polyester fine fibre felt and a P84?/polyester felt in a cement finish mill de-dusting | |||
---|---|---|---|
Polyester fine fibre |
P84?/polyester blend |
||
a/c ratio | m/min | 1.27 | |
Air permeability as received1 | l/dm2 min | 7 | 11 |
Cure time: 1 hr | Cure Time: 7-20 days |
Cure Time: 7-20 days |
Cure Time: 7-20 days |
Air permeability pulse cleaned1 | l/dm2 min (@ 200 Pa) | 10 | 20 |
Total bag life | months | 7 | 48-60 |
1measured after 28 months |
Test conditions (test rig according to VDI 3629, test dust Pural NF – Al2O3) | |||
---|---|---|---|
PTFE | P84?/PTFE blend |
||
Felt weight | g/m2 | 750 | 650 |
Mean mass diameter Al2O3 |
?m | 3.5 | |
Test sequence | 30 cycles cleaning at 1,000 Pa 10.000 cycles ageing/5 sec each 2 hours, cleaning at 1,800Pa |
||
a/c ratio | 2 m/min |
Process
Price hikes, drop in input costs help cement industry to post positive margins: Care Ratings
Published
4 years agoon
October 21, 2021By
admin
Region-wise,the southern region comprises 35% of the total cement capacity, followed by thenorthern, eastern, western and central region comprising 20%, 18%, 14% and 13%of the capacity, respectively.
The cement industry is expected to post positive margins on decent price hikes over the months, falling raw material prices and marked drop in overall production costs, said an analysis of Care Ratings.
Wholesale and retail prices of cement have increased 11.9% and 12.4%, respectively, in the current financial year. As whole prices have remained elevated in most of the markets in the months of FY20, against the corresponding period of the previous year.
Similarly, electricity and fuel cost have declined 11.9% during 9M FY20 due to drop in crude oil prices. Logistics costs, the biggest cost for cement industry, has also dropped 7.7% (selling and distribution) as the Railways extended the benefit of exemption from busy season surcharge. Moreover, the cost of raw materials, too, declined 5.1% given the price of limestone had fallen 11.3% in the same aforementioned period, the analysis said.
According to Care Ratings, though the overall sales revenue has increased only 1.3%, against 16% growth in the year-ago period, the overall expenditure has declined 3.2% which has benefited the industry largely given the moderation in sales.
Even though FY20 has been subdued in terms of production and demand, the fall in cost of production has still supported the cement industry by clocking in positive margins, the rating agency said.
Cement demand is closely linked to the overall economic growth, particularly the housing and infrastructure sector. The cement sector will be seeing a sharp growth in volumes mainly due to increasing demand from affordable housing and other government infrastructure projects like roads, metros, airports, irrigation.
The government’s newly introduced National Infrastructure Pipeline (NIP), with its target of becoming a $5-trillion economy by 2025, is a detailed road map focused on economic revival through infrastructure development.
The NIP covers a gamut of sectors; rural and urban infrastructure and entails investments of Rs.102 lakh crore to be undertaken by the central government, state governments and the private sector. Of the total projects of the NIP, 42% are under implementation while 19% are under development, 31% are at the conceptual stage and 8% are yet to be classified.
The sectors that will be of focus will be roads, railways, power (renewable and conventional), irrigation and urban infrastructure. These sectors together account for 79% of the proposed investments in six years to 2025. Given the government’s thrust on infrastructure creation, it is likely to benefit the cement industry going forward.
Similarly, the Pradhan Mantri Awaas Yojana, aimed at providing affordable housing, will be a strong driver to lift cement demand. Prices have started correcting Q4 FY20 onwards due to revival in demand of the commodity, the agency said in its analysis.
Industry’s sales revenue has grown at a CAGR of 7.3% during FY15-19 but has grown only 1.3% in the current financial year. Tepid demand throughout the country in the first half of the year has led to the contraction of sales revenue. Fall in the total expenditure of cement firms had aided in improving the operating profit and net profit margins of the industry (OPM was 15.2 during 9M FY19 and NPM was 3.1 during 9M FY19). Interest coverage ratio, too, has improved on an overall basis (ICR was 3.3 during 9M FY19).
According to Cement Manufacturers Association, India accounts for over 8% of the overall global installed capacity. Region-wise, the southern region comprises 35% of the total cement capacity, followed by the northern, eastern, western and central region comprising 20%, 18%, 14% and 13% of the capacity, respectively.
Installed capacity of domestic cement makers has increased at a CAGR of 4.9% during FY16-20. Manufacturers have been able to maintain a capacity utilisation rate above 65% in the past quinquennium. In the current financial year due to the prolonged rains in many parts of the country, the capacity utilisation rate has fallen from 70% during FY19 to 66% currently (YTD).
Source:moneycontrol.com
Process
Wonder Cement shows journey of cement with new campaign
Published
4 years agoon
October 21, 2021By
admin
The campaign also marks Wonder Cement being the first ever cement brand to enter the world of IGTV…
ETBrandEquity
Cement manufacturing company Wonder Cement, has announced the launch of a digital campaign ‘Har Raah Mein Wonder Hai’. The campaign has been designed specifically to run on platforms such as Instagram, Facebook and YouTube.
#HarRaahMeinWonderHai is a one-minute video, designed and conceptualised by its digital media partner Triature Digital Marketing and Technologies Pvt Ltd. The entire journey of the cement brand from leaving the factory, going through various weather conditions and witnessing the beauty of nature and wonders through the way until it reaches the destination i.e., to the consumer is very intriguing and the brand has tried to showcase the same with the film.
Sanjay Joshi, executive director, Wonder Cement, said, "Cement as a product poses a unique marketing challenge. Most consumers will build their homes once and therefore buy cement once in a lifetime. It is critical for a cement company to connect with their consumers emotionally. As a part of our communication strategy, it is our endeavor to reach out to a large audience of this country through digital. Wonder Cement always a pioneer in digital, with the launch of our IGTV campaign #HarRahMeinWonderHai, is the first brand in the cement category to venture into this space. Through this campaign, we have captured the emotional journey of a cement bag through its own perspective and depicted what it takes to lay the foundation of one’s dreams and turn them into reality."
The story begins with a family performing the bhoomi poojan of their new plot. It is the place where they are investing their life-long earnings; and planning to build a dream house for the family and children. The family believes in the tradition of having a ‘perfect shuruaat’ (perfect beginning) for their future dream house. The video later highlights the process of construction and in sequence it is emphasising the value of ‘Perfect Shuruaat’ through the eyes of a cement bag.
Tarun Singh Chauhan, management advisor and brand consultant, Wonder Cement, said, "Our objective with this campaign was to show that the cement produced at the Wonder Cement plant speaks for itself, its quality, trust and most of all perfection. The only way this was possible was to take the perspective of a cement bag and showing its journey of perfection from beginning till the end."
According to the company, the campaign also marks Wonder Cement being the first ever cement brand to enter the world of IGTV. No other brand in this category has created content specific to the platform.
Process
In spite of company’s optimism, demand weakness in cement is seen in the 4% y-o-y drop in sales volume. (Reuters)
Published
4 years agoon
October 21, 2021By
admin
Cost cuts and better realizations save? the ?day ?for ?UltraTech Cement, Updated: 27 Jan 2020, Vatsala Kamat from Live Mint
Lower cost of energy and logistics helped Ebitda per tonne rise by about 29% in Q3
Premiumization of acquired brands, synergistic?operations hold promise for future profit growth Topics
UltraTech Cement
India’s largest cement producer UltraTech Cement Ltd turned out a bittersweet show in the December quarter. A sharp drop in fuel costs and higher realizations helped drive profit growth. But the inherent demand weakness was evident in the sales volumes drop during the quarter.
Better realizations during the December quarter, in spite of the 4% year-on-year volume decline, minimized the pain. Net stand-alone revenue fell by 2.6% to ?9,981.8 crore.
But as pointed out earlier, lower costs on most fronts helped profitability. The chart alongside shows the sharp drop in energy costs led by lower petcoke prices, lower fuel consumption and higher use of green power. Logistics costs, too, fell due to lower railway freight charges and synergies from the acquired assets. These savings helped offset the increase in raw material costs.
The upshot: Q3 Ebitda (earnings before interest, tax, depreciation and amortization) of about ?990 per tonne was 29% higher from a year ago. The jump in profit on a per tonne basis was more or less along expected lines, given the increase in realizations. "Besides, the reduction in net debt by about ?2,000 crore is a key positive," said Binod Modi, analyst at Reliance Securities Ltd.
Graphic by Santosh Sharma/Mint
What also impressed analysts is the nimble-footed integration of the recently merged cement assets of Nathdwara and Century, which was a concern on the Street.
Kunal Shah, analyst (institutional equities) at Yes Securities (India) Ltd, said: "The company has proved its ability of asset integration. Century’s cement assets were ramped up to 79% capacity utilization in December, even as they operated Nathdwara generating an Ebitda of ?1,500 per tonne."
Looks like the demand weakness mirrored in weak sales during the quarter was masked by the deft integration and synergies derived from these acquired assets. This drove UltraTech’s stock up by 2.6% to ?4,643 after the Q3 results were declared on Friday.
Brand transition from Century to UltraTech, which is 55% complete, is likely to touch 80% by September 2020. A report by Jefferies India Pvt. Ltd highlights that the Ebitda per tonne for premium brands is about ?5-10 higher per bag than the average (A cement bag weighs 50kg). Of course, with competition increasing in the arena, it remains to be seen how brand premiumization in the cement industry will pan out. UltraTech Cement scores well among peers here.
However, there are road bumps ahead for the cement sector and for UltraTech. Falling gross domestic product growth, fiscal slippages and lower budgetary allocation to infrastructure sector are making industry houses jittery on growth. Although UltraTech’s management is confident that cement demand is looking up, sustainability and pricing power remains a worry for the near term.