Process
Binani Cement Ltd: Transforming vision into reality
Published
15 years agoon
By
admin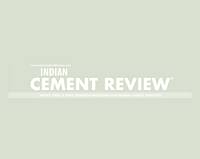
The Indian cement industry has been passing through a rough patch with a host of issues haunting the industry like, volatility in cement prices, high input costs and raw material costs, irrational import duties on raw materials and so on. Amidst these unfavourable circumstances, Binani Cement stood tall with its performance over the years, be it the scale of production, new manufacturing facilities, spreading wings in overseas markets, etc. Read on to know how the company has transformed its imagination and vision into reality.
Genesis
Binani Cement started operations in 1996 under the name Dynasty Dealer Pvt Ltd and manufacturing began in 1997. The name was changed to Binani Cement Pvt Ltd on April 23, 1998 and subsequently converted into a public limited company, bearing the name Binani Cement Ltd on October 6, 1998. The company is certified with ISO 9001, ISO 14001 and OHSAS 18001 within a short span of commencement, an achievement that clearly illustrates its commitment to quality, efficiency, and environment. Binani Cement has set a global benchmark with presence in countries like China, Dubai, Mauritius, etc. The company’s product portfolio includes Ordinary Portland Cement (OPC), Pozzolana Portland Cement (PPC) and Ground Granulated Blast Furnace Slag (GGBFS in Dubai). The products are marketed under the premium ‘Binani Cement’ brand name and enjoy significant market share in Rajasthan and other regions in northern and western India, sharing top-notch status with many of the nation’s leading cement brands.
Transformation
For Binani Group, cement business is a means to transform imagination and vision into reality. To transform this dream into reality, the company established manufacturing facility in Sirohi, Rajasthan and clinker grinding unit, Neem Ka Thana at Sikar, Rajasthan. The company’s cement plant located at Pindwara, Sirohi, is in close proximity to the customers in the state and also caters extensively to markets in Gujarat, Haryana and the north central region. The company has two limestone mines in village Amli and Thandiberi located at a distance of 2 km and 7 km respectively from the plant premises. These mines are leased to the company by the Government of Rajasthan initially for a period of 20 years which is renewable after every 20 years. The total estimated reserves in both the mines till date is 175 million tonne. The Sirohi plant was set up in April 1997 with an initial production capacity of 1.65 MTPA, which was later increased to 4.85 MTPA through modifications and de-bottlenecking.
In order to consolidate its presence in north Indian markets, Binani Cement increased its clinker production capacity by 2.3 MTPA with the commissioning of a separate cement manufacturing facility (Line-2) at the existing sites in July 2007 along with a 44.6 MW (2 x 22.3 MW) captive power plant. The clinker manufacturing capacity was further increased to 2.7 MTPA in May 2010 through process improvement.
The clinker grinding plant lies in close proximity to the customers of eastern Rajasthan and nearby states of northern India. The facility is well-connected by road and rail. The plant was set up with the technical support from FL Smidth, Denmark. The unit commenced its commercial production in March, 2008 with an installed capacity of 1.40 MTPA cement grinding. The unit acquired, stand-alone third-party certifications conforming to ISO 9001, ISO 14001 and OHSAS 18001 for its quality, environment and OHS management systems, respectively from Intertek Systems Certification, Ahmedabad in July 2009.
The unit has obtained separate environment clearance from the Ministry of Environment & Forests (MoEF) and all other consents from the State Pollution Control Board for manufacturing 1.40 MTPA of cement. The environmental performance of the unit in terms of control on air, water and land pollution is monitored by the MoEF and RSPCB.
Global presence
Binani Cement has spread its wings towards overseas markets with plants in China, the Middle East and Mauritius. The company formed Shandong Binani Rongan Cement Co Ltd (SBRCCL) after acquiring management control of Rizhao Rongan Construction Materials Co Ltd, a two-year old operational 1,100 TPD clinker manufacturing unit. The plant is strategically located within close proximity to the two operating ports of Rizhao and Lanshan and the upcoming port of c, in Shandong Province. The plant was upgraded from 1,100 TPD to 1,600 TPD with the addition of a cement grinding unit of 0.3 MTPA in 2008. SBRCCL is currently implementing a brownfield expansion for clinker manufacturing, which starts from limestone crushing till clinker dispatch and it is also constructing a split grinding station of 0.98 MTPA of bulk and bagged cement.
The Binani Cement Factory LLC, established in 1996, is located in the Jebel Ali Industrial Area. With its close proximity to the major ports, and a construction hub, it serves as a perfect vantage point for Binani Cement to tap the potential markets. In 2006, responding to the ever-increasing demands, Binani Cement showcased its unmatched capabilities by expanding the capacity of its plant from 0.5 million tonne to an overwhelming 1 million tonne of OPC and GGBFS. Subsequently, in 2007 grinding capacity was increased to 1.2 MTPA. In 2009, slag-grinding facility has been added and total production capacity increased to 2 MTPA by adding third clinker grinding line. A subsidiary, Binani Cement Factory (SFZ) Ltd has been established in Sudan for marketing cement produced in Dubai plant. To capitalise on the demand of cement in East African and other neighbouring countries, the company has set up marketing offices through its subsidiaries in Sudan, Djibouti, Ethiopia, Tanzania, Kuwait and other East African countries.
Binani Cement Factory (Mauritius) Ltd is a wholly owned subsidiary of Binani Cement Factory LLC, Dubai, UAE. The plant in Mauritius is part of Binani Cement’s aggressive overseas expansion plans and it will create employment for various local communities and will also generate additional revenue for both the port as well as the economy of Mauritius.
World-class technology
Binani Cement has set up plants with internationally acclaimed technologies from leading firms. Major equipment and technology for cement plant was sourced from FL Smidth, Denmark while those in the thermal plants were sourced from Shin Nippon, Japan, Cethar Vessels Ltd, AEG Siemens and Stork Cattle, Sweden. Major plant and machinery consists of one cement mill (180 TPH capacity), one electronic packer (240 TPH capacity), clinker, fly ash, cement storage silos, etc. The unit has its own railway siding, which was commissioned in mid 2009.
The unit is licensed to manufacture Ordinary Portland Cement (OPC 43 and 53 Grades) and Portland Pozzolana Cement (PPC). Currently it is producing 100 per cent PPC for which clinker is supplied from the parent unit, ie, Binani Cement Ltd, Binanigram while fly ash is sourced from the thermal power plants located at NTPC, Dadri (Haryana), Suratgarh (Rajasthan), Bhatinda (Punjab), etc.
Looking ahead
Binani Cement has recently signed a memorandum of understanding with Gujarat Government to invest Rs 4,200 crore for setting up a greenfield cement plant of 5 MTPA capacity. The company has recently delisted from the India Stock. Binani Cement is actively scouting for new business in emerging markets in Africa and other countries. The company is well placed financially and with large infrastructure and housing projection coming up, Binani is poised for a giant leap.
Awards
Binani Cement has won many wards and recognition both national and international which include:
- ITC CII Sustainability Award 2009
- Greentech Environment Excellence Gold Award 2009
- National Award for Excellence in Water Management 2009
- National Award for Excellence in Energy Management 2009
- Certificate of Merit for 2007-08 for Productivity Improvements
- Certificate of Excellence
- Udyog Bharati Award 2009 and Indian Achievers Award for Quality Excellence
Process
Price hikes, drop in input costs help cement industry to post positive margins: Care Ratings
Published
4 years agoon
October 21, 2021By
admin
Region-wise,the southern region comprises 35% of the total cement capacity, followed by thenorthern, eastern, western and central region comprising 20%, 18%, 14% and 13%of the capacity, respectively.
The cement industry is expected to post positive margins on decent price hikes over the months, falling raw material prices and marked drop in overall production costs, said an analysis of Care Ratings.
Wholesale and retail prices of cement have increased 11.9% and 12.4%, respectively, in the current financial year. As whole prices have remained elevated in most of the markets in the months of FY20, against the corresponding period of the previous year.
Similarly, electricity and fuel cost have declined 11.9% during 9M FY20 due to drop in crude oil prices. Logistics costs, the biggest cost for cement industry, has also dropped 7.7% (selling and distribution) as the Railways extended the benefit of exemption from busy season surcharge. Moreover, the cost of raw materials, too, declined 5.1% given the price of limestone had fallen 11.3% in the same aforementioned period, the analysis said.
According to Care Ratings, though the overall sales revenue has increased only 1.3%, against 16% growth in the year-ago period, the overall expenditure has declined 3.2% which has benefited the industry largely given the moderation in sales.
Even though FY20 has been subdued in terms of production and demand, the fall in cost of production has still supported the cement industry by clocking in positive margins, the rating agency said.
Cement demand is closely linked to the overall economic growth, particularly the housing and infrastructure sector. The cement sector will be seeing a sharp growth in volumes mainly due to increasing demand from affordable housing and other government infrastructure projects like roads, metros, airports, irrigation.
The government’s newly introduced National Infrastructure Pipeline (NIP), with its target of becoming a $5-trillion economy by 2025, is a detailed road map focused on economic revival through infrastructure development.
The NIP covers a gamut of sectors; rural and urban infrastructure and entails investments of Rs.102 lakh crore to be undertaken by the central government, state governments and the private sector. Of the total projects of the NIP, 42% are under implementation while 19% are under development, 31% are at the conceptual stage and 8% are yet to be classified.
The sectors that will be of focus will be roads, railways, power (renewable and conventional), irrigation and urban infrastructure. These sectors together account for 79% of the proposed investments in six years to 2025. Given the government’s thrust on infrastructure creation, it is likely to benefit the cement industry going forward.
Similarly, the Pradhan Mantri Awaas Yojana, aimed at providing affordable housing, will be a strong driver to lift cement demand. Prices have started correcting Q4 FY20 onwards due to revival in demand of the commodity, the agency said in its analysis.
Industry’s sales revenue has grown at a CAGR of 7.3% during FY15-19 but has grown only 1.3% in the current financial year. Tepid demand throughout the country in the first half of the year has led to the contraction of sales revenue. Fall in the total expenditure of cement firms had aided in improving the operating profit and net profit margins of the industry (OPM was 15.2 during 9M FY19 and NPM was 3.1 during 9M FY19). Interest coverage ratio, too, has improved on an overall basis (ICR was 3.3 during 9M FY19).
According to Cement Manufacturers Association, India accounts for over 8% of the overall global installed capacity. Region-wise, the southern region comprises 35% of the total cement capacity, followed by the northern, eastern, western and central region comprising 20%, 18%, 14% and 13% of the capacity, respectively.
Installed capacity of domestic cement makers has increased at a CAGR of 4.9% during FY16-20. Manufacturers have been able to maintain a capacity utilisation rate above 65% in the past quinquennium. In the current financial year due to the prolonged rains in many parts of the country, the capacity utilisation rate has fallen from 70% during FY19 to 66% currently (YTD).
Source:moneycontrol.com
Process
Wonder Cement shows journey of cement with new campaign
Published
4 years agoon
October 21, 2021By
admin
The campaign also marks Wonder Cement being the first ever cement brand to enter the world of IGTV…
ETBrandEquity
Cement manufacturing company Wonder Cement, has announced the launch of a digital campaign ‘Har Raah Mein Wonder Hai’. The campaign has been designed specifically to run on platforms such as Instagram, Facebook and YouTube.
#HarRaahMeinWonderHai is a one-minute video, designed and conceptualised by its digital media partner Triature Digital Marketing and Technologies Pvt Ltd. The entire journey of the cement brand from leaving the factory, going through various weather conditions and witnessing the beauty of nature and wonders through the way until it reaches the destination i.e., to the consumer is very intriguing and the brand has tried to showcase the same with the film.
Sanjay Joshi, executive director, Wonder Cement, said, "Cement as a product poses a unique marketing challenge. Most consumers will build their homes once and therefore buy cement once in a lifetime. It is critical for a cement company to connect with their consumers emotionally. As a part of our communication strategy, it is our endeavor to reach out to a large audience of this country through digital. Wonder Cement always a pioneer in digital, with the launch of our IGTV campaign #HarRahMeinWonderHai, is the first brand in the cement category to venture into this space. Through this campaign, we have captured the emotional journey of a cement bag through its own perspective and depicted what it takes to lay the foundation of one’s dreams and turn them into reality."
The story begins with a family performing the bhoomi poojan of their new plot. It is the place where they are investing their life-long earnings; and planning to build a dream house for the family and children. The family believes in the tradition of having a ‘perfect shuruaat’ (perfect beginning) for their future dream house. The video later highlights the process of construction and in sequence it is emphasising the value of ‘Perfect Shuruaat’ through the eyes of a cement bag.
Tarun Singh Chauhan, management advisor and brand consultant, Wonder Cement, said, "Our objective with this campaign was to show that the cement produced at the Wonder Cement plant speaks for itself, its quality, trust and most of all perfection. The only way this was possible was to take the perspective of a cement bag and showing its journey of perfection from beginning till the end."
According to the company, the campaign also marks Wonder Cement being the first ever cement brand to enter the world of IGTV. No other brand in this category has created content specific to the platform.
Process
In spite of company’s optimism, demand weakness in cement is seen in the 4% y-o-y drop in sales volume. (Reuters)
Published
4 years agoon
October 21, 2021By
admin
Cost cuts and better realizations save? the ?day ?for ?UltraTech Cement, Updated: 27 Jan 2020, Vatsala Kamat from Live Mint
Lower cost of energy and logistics helped Ebitda per tonne rise by about 29% in Q3
Premiumization of acquired brands, synergistic?operations hold promise for future profit growth Topics
UltraTech Cement
India’s largest cement producer UltraTech Cement Ltd turned out a bittersweet show in the December quarter. A sharp drop in fuel costs and higher realizations helped drive profit growth. But the inherent demand weakness was evident in the sales volumes drop during the quarter.
Better realizations during the December quarter, in spite of the 4% year-on-year volume decline, minimized the pain. Net stand-alone revenue fell by 2.6% to ?9,981.8 crore.
But as pointed out earlier, lower costs on most fronts helped profitability. The chart alongside shows the sharp drop in energy costs led by lower petcoke prices, lower fuel consumption and higher use of green power. Logistics costs, too, fell due to lower railway freight charges and synergies from the acquired assets. These savings helped offset the increase in raw material costs.
The upshot: Q3 Ebitda (earnings before interest, tax, depreciation and amortization) of about ?990 per tonne was 29% higher from a year ago. The jump in profit on a per tonne basis was more or less along expected lines, given the increase in realizations. "Besides, the reduction in net debt by about ?2,000 crore is a key positive," said Binod Modi, analyst at Reliance Securities Ltd.
Graphic by Santosh Sharma/Mint
What also impressed analysts is the nimble-footed integration of the recently merged cement assets of Nathdwara and Century, which was a concern on the Street.
Kunal Shah, analyst (institutional equities) at Yes Securities (India) Ltd, said: "The company has proved its ability of asset integration. Century’s cement assets were ramped up to 79% capacity utilization in December, even as they operated Nathdwara generating an Ebitda of ?1,500 per tonne."
Looks like the demand weakness mirrored in weak sales during the quarter was masked by the deft integration and synergies derived from these acquired assets. This drove UltraTech’s stock up by 2.6% to ?4,643 after the Q3 results were declared on Friday.
Brand transition from Century to UltraTech, which is 55% complete, is likely to touch 80% by September 2020. A report by Jefferies India Pvt. Ltd highlights that the Ebitda per tonne for premium brands is about ?5-10 higher per bag than the average (A cement bag weighs 50kg). Of course, with competition increasing in the arena, it remains to be seen how brand premiumization in the cement industry will pan out. UltraTech Cement scores well among peers here.
However, there are road bumps ahead for the cement sector and for UltraTech. Falling gross domestic product growth, fiscal slippages and lower budgetary allocation to infrastructure sector are making industry houses jittery on growth. Although UltraTech’s management is confident that cement demand is looking up, sustainability and pricing power remains a worry for the near term.