Process
Ready Mix Concrete: Raring to excel
Published
15 years agoon
By
admin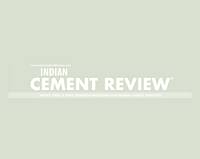
The extent of ready mix concrete (RMC) used in construction industry determines the maturity of the industry. Due to mechanisation, consumption of cement has increased manifold, but in India, only about 7-8 per cent of the concrete is produced as RMC, while in developed countries it is around 50-55 per cent. In spite of being the second largest producer of cement, the penetration for RMC in India is abysmal. On the positive side, with infrastructure projects line-up and demand from housing picking up, the RMC industry is on a growth path. Read on to get the latest updates on the industry.
RMC is the answer for today’s construction where there is space limitation, shorter deadlines, labour shortage and need for mechanisation. RMC refers to concrete that is batched for delivery from a central plant instead of being mixed on the job site. Each batch of ready mixed concrete is tailor-made according to the specifications of the contractor and is delivered to the contractor in a plastic condition, usually in the cylindrical trucks often known as cement mixers.
RMC has opened a new vista in construction as they are available in all mix designs and volumes. Though RMC cost more than on site concrete, because of the quality and strength, it is in demand when it comes to large infrastructural projects. "The RMC commercial plants produce around 25 million cubic metre of concrete in India. Twenty five million cubic metre consumes around 8-10 mt of cement which is still very low. Say, if we are producing around 200 mt of cement then only about 5 per cent goes into commercial ready mix concrete. In many developed countries, this figure is around 50-55 per cent. So as you can see, in India, this industry still has huge potential to grow," says Anand K Jain, Technical Advisor, Ultratech Cement.
"RMC is produced in proper batching plants which ensure consistency of the mix. The supply and storage of the required ingredients (aggregates, sand, cement and water) is consistent in comparison with the congested environment at the job side. So, the quality of RMC should be higher," says Michael Schmid-Lindenmayer, Managing Director Putzmeister Concrete Machines Pvt Ltd.
"RMC can be ordered in all volumes and mix designs. The know-how on mix design which comes normally along with the decision to use RMC is a great advantage," explains Michael Schmid-Lindenmayer.
Advantages of RMC:
- A centralised concrete batching plant can serve a wide area
- Better quality concrete is produced
- Elimination of storage space for basic materials at site
- Elimination of procurement/hiring of plant and machinery
- Wastage of basic materials is avoided
- Labour associated with production of concrete is eliminated
- Time required is greatly reduced
- Reduction in noise and dust pollution
The world’s first RMC plant was set up 100 years ago, but in India RMC became well known only from the 1990s. Narendra Patel, Chairman, Ariisto Developers & Builders, narrated an interesting anecdote about how the RMC was introduced in India. Manohar Kelkar, an engineer from India, was on a visit to Bauma Exhibition. He was standing near a stall of Putzmeister. The attendant at the stall enquired and Kelkar replied that he was interested in concrete making. The attendant registered his name and address. Kelkar returned to India and after six months, a representative of Putzmeister visited his residence at Pune. The representative requested Kelkar to visit Putzmeister RMC plants in Germany. He visited the RMC plants in Germany and was convinced that the future belongs to RMC. He returned to India, but at that time, import of RMC machinery was not allowed. He approached Miller Mixer and struck a deal, in which Miller was given a certain percentage in profit. This was how the first known RMC plant was set up in India.
Three principal categories:
??Central-mixed concrete, which is completely mixed at the plant and then transported in a truck-mixer or agitator truck. Freshly mixed concrete may be transported in an open dump truck if the jobsite is near the plant. Slight agitation of the concrete during transit prevents segregation of the materials and reduces the amount of slump loss.
??Transit-mixed (also known as truck-mixed) concrete, materials are batched at a central plant and are completely mixed in the truck in transit. Frequently, the concrete is partially mixed in transit and mixing is completed at the jobsite. Transit-mixing keeps the water separate from the cement and aggregates and allows the concrete to be mixed immediately before placement at the construction site. This method avoids the problems of premature hardening and slump loss that result from potential delays in transportation or placement of central-mixed concrete. Additionally, transit-mixing allows concrete to be hauled to construction sites further away from the plant.
??Shrink-mixed concrete is used to increase the truck’s load capacity and retain the advantages of transit-mixed concrete. In shrink-mixed concrete, concrete is partially mixed at the plant to reduce or shrink the volume of the mixture and mixing is completed in transit or at the jobsite.
Major constrains
"Ready mix has still a low penetration rate in India. We estimate that only 7 to 8 per cent of the concrete is produced as ready mix. The RMC business sector is still struggling to convince the Indian customer on the added value which the concept of RMC is providing to the consumer", says Michael Schmid-Lindenmayer.
Initially, in India, RMC was treated as manufactured product. Due to this, sales tax and excise duty were levied by the government. The sales tax and excise duty put together amounted to 32 per cent. This can also be one of the reasons for the slow growth of the industry. Now, the government has done away with excise duty and the manufacturer can claim rebate on sales tax. The input cost is a big constrain, "if you take land on lease or buy it, the cost is very high and adds to the input cost.
Secondly, towns and cities are very congested and the movement is very slow. Therefore the throughput of a transit mixer is very less and the transportation cost becomes very high", says Anand Jain. Then, there are the unorganised RMC manufacturers who offer RMC to end-consumer at discounted prices or at lower rates. Many a times, it is seen that control on quality is not maintained. There are chances of RMC manufacturer making mistakes or negate certain aspects, which puts a question mark on the strength and quality of the concrete. "There should be independent organisation or quality control people to check the quality," recommends Narendra Patel. Taxation is another deterrent, while RMC manufactures have to pay value added tax (VAT), the same is not applicable for on site concrete. The materials are batched at a central plant, and the mixing begins at that plant, so the travelling time from the plant to the site is critical over longer distances. Some sites are far away and RMC has a limited time span between mixing and going-off means that ready mix should be placed within a certain time of batching at the plant, which is also one of the hindrances. "There is no mention of the amount of fly ash used in RMC in India, so there is always doubt about the strength of RMC. In developed countries like Germany the amount of fly ash is always mentioned", laments an RMC user. The boom in construction brought in fly-by-night RMC manufacture, as in India there is no norms or guidelines by government authorities to set up RMC plant, while in developed countries like Germany there are a proper guidelines and standards for manufacturing RMC. The Ready-Mixed Concrete Manufacturers’ Association (RMCMA), an independent body located in Mumbai, ensures checks on quality for its members. "Our external auditors conduct stringent quality check at RMC production facility before issuing a certificate of compliance," says Vijay R Kulkarni, Principal Consultant, RMCMA.
Machinery
As early as 1909, concrete was delivered by a horse-drawn mixer that used paddles turned by the cart’s wheels to mix concrete en route to the jobsite. In 1916, Stephen Stepanian of Ohio, USA developed a self-discharging motorised transit mixer that was the predecessor of the modern ready-mixed concrete truck. Today, the market is flooded with intelligent RMC machinery and the process has been made fully automated to keep pace with the rapid need of the industry.
RMC machinery manufacturers have registered an impressive growth year-on-year. Estimate put the growth to be 100 per cent. The growth is mainly due to the demands for good quality concrete in the tier-2 and tier-3 cities. "Even in tier-2 and tier-3 cities like Kolhapur, Ludhiana, Nashik, Vishakhapatnam, Vijayawada, Mysore, etc all these places are responding positively to the ready mix concrete", says Anand Jain. Debasis Bhattacharya, Ajax Fiori Engineers, confirms the same and adds "we started from tier-3 cities, the market for RMC machinery is growing and we are in the process of setting up offices in major cities of the country". There are also foreign players like Erisim Makina, Wolfgang Kaiblinger and others, who plan to enter the Indian market. "India is a lucrative market", says Cevdet Karaibrahimoglu of Erisim Makina, a Turkish company. "As of now we are not setting up manufacturing facility in India, but we are bringing in our technologies" says Wolfgang Kaiblinger, from Doubrava GmbH & Co KG. New user-friendly machineries.
Growth prospects
The RMC industry was badly hit by 2008-2009 recession. A booming RMC market was brought to a stand still. But now things are looking bright. "The RMC market has picked up in last quarter. And if this continues, things may come back on track," says Ranjeet Moray, Managing Director, Universal Construction Machinery & Equipments Ltd. Universal Construction Machinery & Equipments exports RMC machinery to 45 countries. "Majority of the global players are already active in India. These players try to adjust their global business model to the very competitive Indian market environment keeping their high quality and safety standards at the same time. Also, there is an unorganised sector which consists of a lot of smaller, regional player which offers very competitive prices," points out Michael Schmid-Lindenmayer. With the growth in RMC, the supporting equipment for batching plant has also witnessed a huge demand. The industry has also witnessed a lot of changes, "previously one person was putting a batching plant and he used to supply it to 10 builders, now the trend has changed and all these 10 builders are putting their own plants," said a spokesperson from Readymix Construction Machinery. These changes are mainly because of the new user-friendly high-technology machinery that are easy to operate. "We expect that the dynamics of the Indian market will further increase. In metro cities, the demand for modern construction equipment will increase and in the tier 2 and tier 3 cities, the demand for simple cost-competitive construction machines will grow in a fast pace. The entire development is driven by the requirement for shorter construction times, higher quality and safety" says says Michael Schmid-Lindenmayer.
Optimistic future
The demand for RMC from the commercial and residential segments is expected to grow. The increase in cement capacity and the steadily expanding demand for RMC will see many new RMC plants from organised and unorganised players. With a number of infrastructure projects lined up and compulsory use of RMC in metros and in government projects like Jawaharlal Nehru National Urban Renewal Mission, the future of the RMC industry looks positive.
Process
Price hikes, drop in input costs help cement industry to post positive margins: Care Ratings
Published
4 years agoon
October 21, 2021By
admin
Region-wise,the southern region comprises 35% of the total cement capacity, followed by thenorthern, eastern, western and central region comprising 20%, 18%, 14% and 13%of the capacity, respectively.
The cement industry is expected to post positive margins on decent price hikes over the months, falling raw material prices and marked drop in overall production costs, said an analysis of Care Ratings.
Wholesale and retail prices of cement have increased 11.9% and 12.4%, respectively, in the current financial year. As whole prices have remained elevated in most of the markets in the months of FY20, against the corresponding period of the previous year.
Similarly, electricity and fuel cost have declined 11.9% during 9M FY20 due to drop in crude oil prices. Logistics costs, the biggest cost for cement industry, has also dropped 7.7% (selling and distribution) as the Railways extended the benefit of exemption from busy season surcharge. Moreover, the cost of raw materials, too, declined 5.1% given the price of limestone had fallen 11.3% in the same aforementioned period, the analysis said.
According to Care Ratings, though the overall sales revenue has increased only 1.3%, against 16% growth in the year-ago period, the overall expenditure has declined 3.2% which has benefited the industry largely given the moderation in sales.
Even though FY20 has been subdued in terms of production and demand, the fall in cost of production has still supported the cement industry by clocking in positive margins, the rating agency said.
Cement demand is closely linked to the overall economic growth, particularly the housing and infrastructure sector. The cement sector will be seeing a sharp growth in volumes mainly due to increasing demand from affordable housing and other government infrastructure projects like roads, metros, airports, irrigation.
The government’s newly introduced National Infrastructure Pipeline (NIP), with its target of becoming a $5-trillion economy by 2025, is a detailed road map focused on economic revival through infrastructure development.
The NIP covers a gamut of sectors; rural and urban infrastructure and entails investments of Rs.102 lakh crore to be undertaken by the central government, state governments and the private sector. Of the total projects of the NIP, 42% are under implementation while 19% are under development, 31% are at the conceptual stage and 8% are yet to be classified.
The sectors that will be of focus will be roads, railways, power (renewable and conventional), irrigation and urban infrastructure. These sectors together account for 79% of the proposed investments in six years to 2025. Given the government’s thrust on infrastructure creation, it is likely to benefit the cement industry going forward.
Similarly, the Pradhan Mantri Awaas Yojana, aimed at providing affordable housing, will be a strong driver to lift cement demand. Prices have started correcting Q4 FY20 onwards due to revival in demand of the commodity, the agency said in its analysis.
Industry’s sales revenue has grown at a CAGR of 7.3% during FY15-19 but has grown only 1.3% in the current financial year. Tepid demand throughout the country in the first half of the year has led to the contraction of sales revenue. Fall in the total expenditure of cement firms had aided in improving the operating profit and net profit margins of the industry (OPM was 15.2 during 9M FY19 and NPM was 3.1 during 9M FY19). Interest coverage ratio, too, has improved on an overall basis (ICR was 3.3 during 9M FY19).
According to Cement Manufacturers Association, India accounts for over 8% of the overall global installed capacity. Region-wise, the southern region comprises 35% of the total cement capacity, followed by the northern, eastern, western and central region comprising 20%, 18%, 14% and 13% of the capacity, respectively.
Installed capacity of domestic cement makers has increased at a CAGR of 4.9% during FY16-20. Manufacturers have been able to maintain a capacity utilisation rate above 65% in the past quinquennium. In the current financial year due to the prolonged rains in many parts of the country, the capacity utilisation rate has fallen from 70% during FY19 to 66% currently (YTD).
Source:moneycontrol.com
Process
Wonder Cement shows journey of cement with new campaign
Published
4 years agoon
October 21, 2021By
admin
The campaign also marks Wonder Cement being the first ever cement brand to enter the world of IGTV…
ETBrandEquity
Cement manufacturing company Wonder Cement, has announced the launch of a digital campaign ‘Har Raah Mein Wonder Hai’. The campaign has been designed specifically to run on platforms such as Instagram, Facebook and YouTube.
#HarRaahMeinWonderHai is a one-minute video, designed and conceptualised by its digital media partner Triature Digital Marketing and Technologies Pvt Ltd. The entire journey of the cement brand from leaving the factory, going through various weather conditions and witnessing the beauty of nature and wonders through the way until it reaches the destination i.e., to the consumer is very intriguing and the brand has tried to showcase the same with the film.
Sanjay Joshi, executive director, Wonder Cement, said, "Cement as a product poses a unique marketing challenge. Most consumers will build their homes once and therefore buy cement once in a lifetime. It is critical for a cement company to connect with their consumers emotionally. As a part of our communication strategy, it is our endeavor to reach out to a large audience of this country through digital. Wonder Cement always a pioneer in digital, with the launch of our IGTV campaign #HarRahMeinWonderHai, is the first brand in the cement category to venture into this space. Through this campaign, we have captured the emotional journey of a cement bag through its own perspective and depicted what it takes to lay the foundation of one’s dreams and turn them into reality."
The story begins with a family performing the bhoomi poojan of their new plot. It is the place where they are investing their life-long earnings; and planning to build a dream house for the family and children. The family believes in the tradition of having a ‘perfect shuruaat’ (perfect beginning) for their future dream house. The video later highlights the process of construction and in sequence it is emphasising the value of ‘Perfect Shuruaat’ through the eyes of a cement bag.
Tarun Singh Chauhan, management advisor and brand consultant, Wonder Cement, said, "Our objective with this campaign was to show that the cement produced at the Wonder Cement plant speaks for itself, its quality, trust and most of all perfection. The only way this was possible was to take the perspective of a cement bag and showing its journey of perfection from beginning till the end."
According to the company, the campaign also marks Wonder Cement being the first ever cement brand to enter the world of IGTV. No other brand in this category has created content specific to the platform.
Process
In spite of company’s optimism, demand weakness in cement is seen in the 4% y-o-y drop in sales volume. (Reuters)
Published
4 years agoon
October 21, 2021By
admin
Cost cuts and better realizations save? the ?day ?for ?UltraTech Cement, Updated: 27 Jan 2020, Vatsala Kamat from Live Mint
Lower cost of energy and logistics helped Ebitda per tonne rise by about 29% in Q3
Premiumization of acquired brands, synergistic?operations hold promise for future profit growth Topics
UltraTech Cement
India’s largest cement producer UltraTech Cement Ltd turned out a bittersweet show in the December quarter. A sharp drop in fuel costs and higher realizations helped drive profit growth. But the inherent demand weakness was evident in the sales volumes drop during the quarter.
Better realizations during the December quarter, in spite of the 4% year-on-year volume decline, minimized the pain. Net stand-alone revenue fell by 2.6% to ?9,981.8 crore.
But as pointed out earlier, lower costs on most fronts helped profitability. The chart alongside shows the sharp drop in energy costs led by lower petcoke prices, lower fuel consumption and higher use of green power. Logistics costs, too, fell due to lower railway freight charges and synergies from the acquired assets. These savings helped offset the increase in raw material costs.
The upshot: Q3 Ebitda (earnings before interest, tax, depreciation and amortization) of about ?990 per tonne was 29% higher from a year ago. The jump in profit on a per tonne basis was more or less along expected lines, given the increase in realizations. "Besides, the reduction in net debt by about ?2,000 crore is a key positive," said Binod Modi, analyst at Reliance Securities Ltd.
Graphic by Santosh Sharma/Mint
What also impressed analysts is the nimble-footed integration of the recently merged cement assets of Nathdwara and Century, which was a concern on the Street.
Kunal Shah, analyst (institutional equities) at Yes Securities (India) Ltd, said: "The company has proved its ability of asset integration. Century’s cement assets were ramped up to 79% capacity utilization in December, even as they operated Nathdwara generating an Ebitda of ?1,500 per tonne."
Looks like the demand weakness mirrored in weak sales during the quarter was masked by the deft integration and synergies derived from these acquired assets. This drove UltraTech’s stock up by 2.6% to ?4,643 after the Q3 results were declared on Friday.
Brand transition from Century to UltraTech, which is 55% complete, is likely to touch 80% by September 2020. A report by Jefferies India Pvt. Ltd highlights that the Ebitda per tonne for premium brands is about ?5-10 higher per bag than the average (A cement bag weighs 50kg). Of course, with competition increasing in the arena, it remains to be seen how brand premiumization in the cement industry will pan out. UltraTech Cement scores well among peers here.
However, there are road bumps ahead for the cement sector and for UltraTech. Falling gross domestic product growth, fiscal slippages and lower budgetary allocation to infrastructure sector are making industry houses jittery on growth. Although UltraTech’s management is confident that cement demand is looking up, sustainability and pricing power remains a worry for the near term.